Taking the Wheel: Proactive Compact Wheel Loader Maintenance Tips
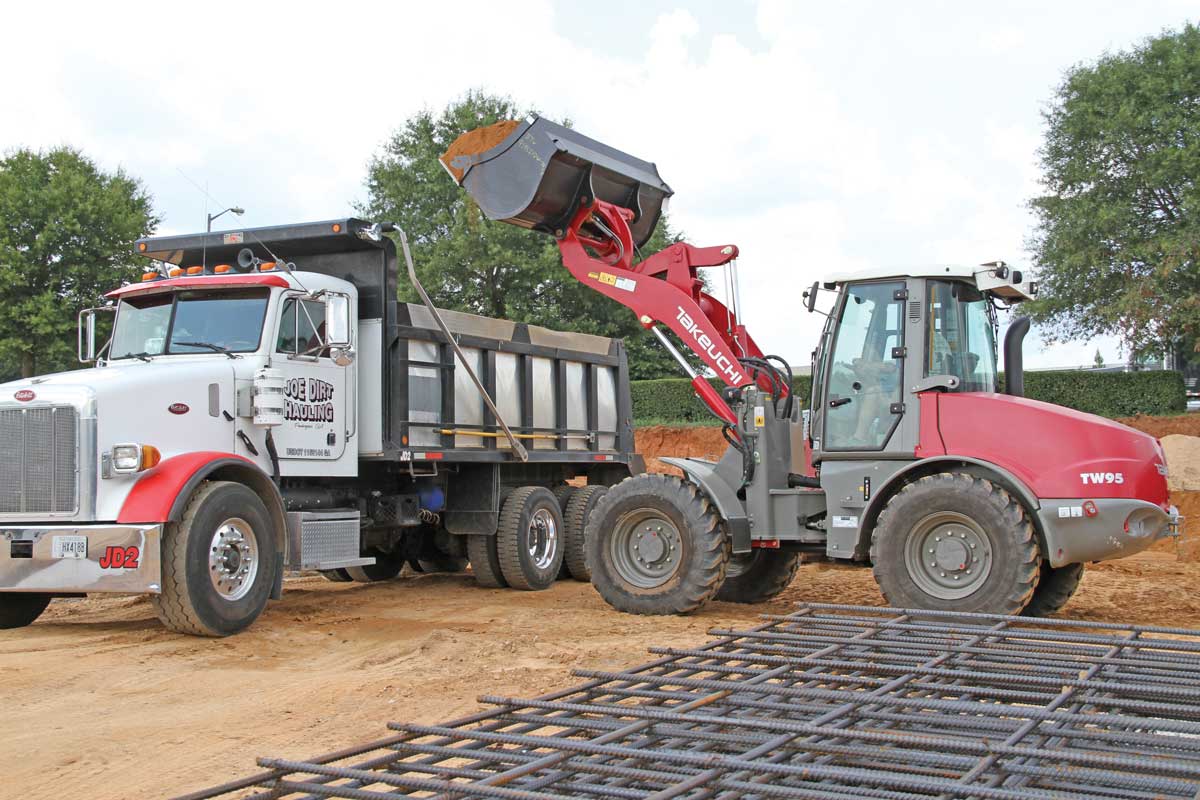
Not long ago, some people thought compact wheel loaders were only useful for one thing — moving materials around a jobsite. Now, because compact wheel loaders are often equipped with higher hydraulic flow and universal skid steer couplers, they can be outfitted with all kinds of attachments, making these little powerhouses more versatile than ever before.
“Thanks to manufacturer updates and advanced technology, compact wheel loaders continue to prove themselves incredibly beneficial for all kinds of jobsite applications,” says Lee Padgett, product manager for Takeuchi-US. “While they still excel at material handling, when combined with the right attachments, they can remove snow, sweep driveways, create trenches and much more.”
Padgett says another benefit of the compact wheel loader is that it is a relatively simple machine to maintain. However, as with all heavy equipment, it’s important to perform proactive maintenance to ensure uptime and productivity.
“Caring for your compact wheel loader should start from the minute you take possession of it, whether it’s brand new or used,” Padgett says. “It’s always best to review your operator’s manual and follow all recommended maintenance, from daily checks to weekly and annual maintenance. Otherwise, you’re taking a risk that your machine won’t be available when you need it.”
Padgett recommended these steps for appropriate and timely compact wheel loader maintenance, along with a few mistakes to avoid for optimum machine life and performance.
Daily Wheel Loader Maintenance
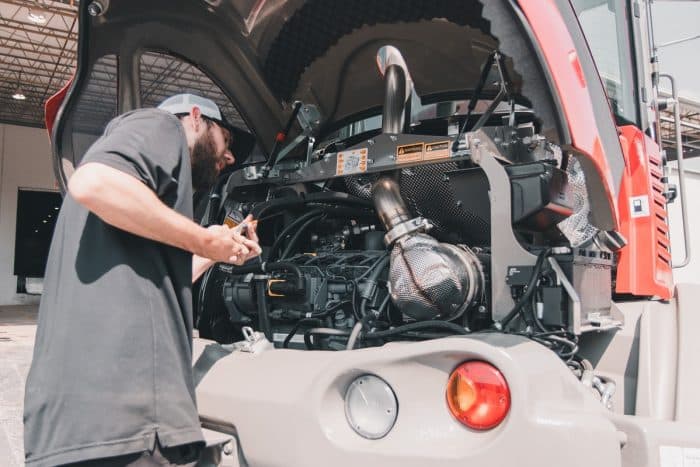
Visual checks. Look over the compact wheel loader and take these precautions before starting it up:
- Ensure the machine is free from debris in vital areas like the radiator, AC condenser and exhaust. If debris has accumulated in any of these areas, use compressed air or high-pressure water to remove the debris before operating the wheel loader.
- Look for oil leaks.
- Drain the fuel and water separator if applicable.
- Examine tire pressure and condition. Replace any tires with punctures or gouges, visible metal or inadequate tread depth as soon as possible.
- Check engine oil, engine coolant, hydraulic oil, fuel and windshield washer fluid and replenish if necessary.
- Ensure all driving and warning lights function properly.
“While some compact wheel loaders will warn you about low-fluid levels, others do not, so it’s best to get in the habit of conducting a daily visual check,” Padgett says. “Then, if the fluid levels check out okay, you can start greasing all pivot points, either prior to starting or ending the shift, whichever you prefer.”
Greasing. Speaking of greasing pivot points — don’t forget the compact wheel loader’s articulation point, a step Padgett says is commonly forgotten. Clean the grease fitting prior to greasing the joint to avoid pushing any accumulated dirt on the fitting into the pin boss. That mistake can end up contaminating the grease, with the debris acting like sandpaper inside the pin boss between the bushing and pin, resulting in premature wear.
“Wheel loaders have many pivoting and articulating components,” Padgett says. “That’s why greasing the machine is imperative for extending its useful life. Because the articulation joint is constantly moving, it’s under a lot of stress. By giving it plenty of grease, you can avoid prematurely wearing out the pins and bushings. It’s also a good idea to grease the wheel loader’s steering cylinders and loader pivot points every day.”
Operator safety. Check all areas related to operator safety before climbing into the cab. Clean mirrors and windows as needed, especially if you used pressured air or water to clean debris in a previous step. After you’re in the operator’s seat, ensure the brakes are functional and the backup alarm is working properly.
“After performing these daily checks, you can get to work with greater peace of mind,” Padgett says. “You can be far more productive when you know your machine is in excellent condition, because you can focus more on the task at hand.”
I hate to be the bearer of bad news, but sometimes you can’t have it all… unless you rent. From finding the right dealer to scoring the perfect rental machine, we have you covered!
Weekly Wheel Loader Maintenance
Weekly, or approximately every 100 hours, thoroughly grease the machine’s pivot points, bushings and bearings. Beyond this additional greasing, weekly maintenance tasks are a bit more complex than daily checks.
- Check the electrical connections, cables and plugs to determine if they have any issues.
- Clean and securely attach the battery contacts.
- Look for blown fuses or loose connections in the fuse panel.
- Clean a dirty radiator and oil cooler from the inside out with compressed air or high-pressure water. Be careful to avoid damaging any other components in the process.
- If necessary, clean and replace the engine air filter. Dirty air filters are especially common when working in dusty applications like site prep or demolition. Do not use high-pressure compressed air to clean the air filter or hit it against anything to free it from dirt as this can damage the filter.
- Check the lug nuts on each tire and tighten them to the appropriate torque.
Hourly Interval Services for Compact Wheel Loaders
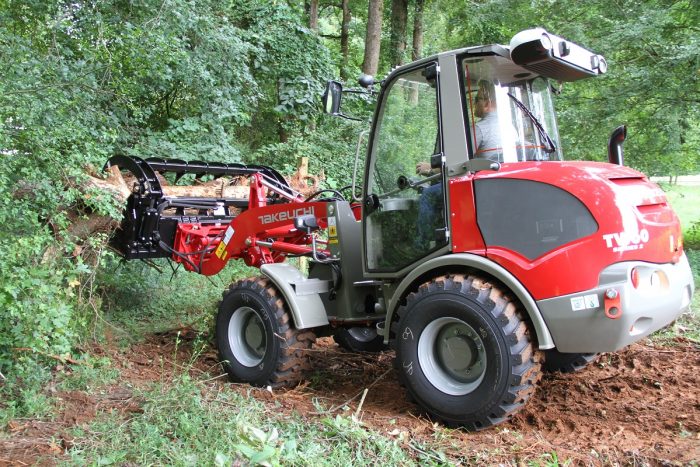
Keeping track of the hours on your compact wheel loader may not seem all that important — that is, until you need to conduct maintenance at the manufacturer’s hourly intervals.
“When machines reach 250 and 500 hours, Takeuchi recommends additional maintenance,” Padgett says. “So, it’s important to know when those milestones are approaching and plan ahead for a little downtime.”
250 Hours. Engine oil and fuel filters should typically be changed every 250 hours, depending on the manufacturer’s recommendation.
“Most engine manufacturers require an initial engine oil change after a pre-specified break-in period,” Padgett says. “From then on, oil change intervals are usually 250 to 500 hours.”
Check the oil level in the front and rear axles, power divider and all four planetary drives. Initial service for the wheel loader’s planetary assemblies after the first 250 hours is also recommended.
500 Hours. Change the oil in the front and rear axles, power divider and all four planetary drives within the initial 500 hours. Following the initial period, the oil in these components will only need to be replaced every 1,500 hours. Then, replace the axle breathers and check battery posts for corrosion and clean if necessary.
1,500 Hours. Replace the oil in the axles, power divider and planetary drives. Also, change the hydraulic oil and service the brake system. Check the wheel loader thoroughly for any damaged parts.
3,000 Hours. Replace the hydraulic oil, air filters and breathers. The 3,000-hour mark is also a good time to tighten all bolts and screws to the proper torque specifications. Look at hydraulic hoses for fatigue, cracking or leaks and replace them if any of these issues are present.
Engine Maintenance on Wheel Loaders
While manufacturers may have different specifications, most diesel engines will likely need maintenance at certain hourly intervals. Most of this maintenance will be fluid changes, valve-train adjustments and fuel and exhaust-system checks.
Wheel loaders with turbocharged engines must be warmed up before putting the machine under load and cooled down before shutting the engine off. It’s a common misconception that because a compact wheel loader’s engine is smaller, cold starts and hot shutdowns won’t hurt it — they will.
“Engine manufacturers will have their own guidelines for service and inspections,” Padgett says. “That’s why it’s important to review the engine service manual for specifics on the best way to maintain your engine over the course of its lifespan.”
Communication Is Key
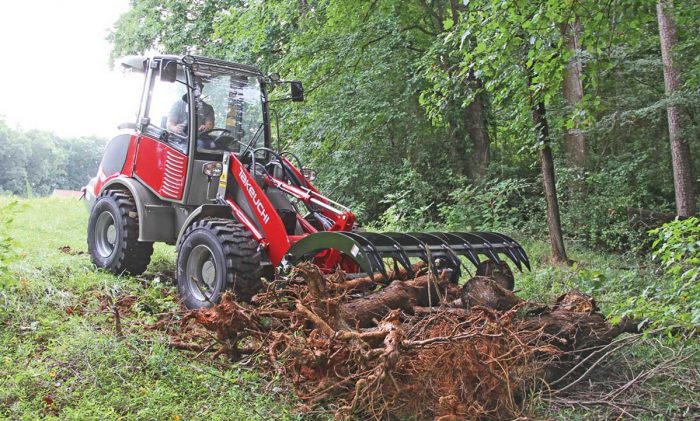
Compact wheel loaders are often left at jobsites to load and unload materials, which can lead to another common problem. When different operators use the same machine at different times, they may assume someone else is handling its maintenance. One operator may finish his shift and leave, expecting the next operator to grease it and check the oil. Perhaps that person thinks the operator before him already took care of it. Then, it turns out no one has done those important tasks for days on end.
“Reading your operators manual and following its recommendations closely is important,” Padgett says. “It’s also necessary for all operators to communicate with each other. When you have the right processes and procedures in place, your compact wheel loader should stay in good condition for many years to come.”
Lynette Von Minden is a public relations manager at Swanson Russell.