Learn How to Upfit a Compact Track Loader for Abrasive Brush Cutting Applications
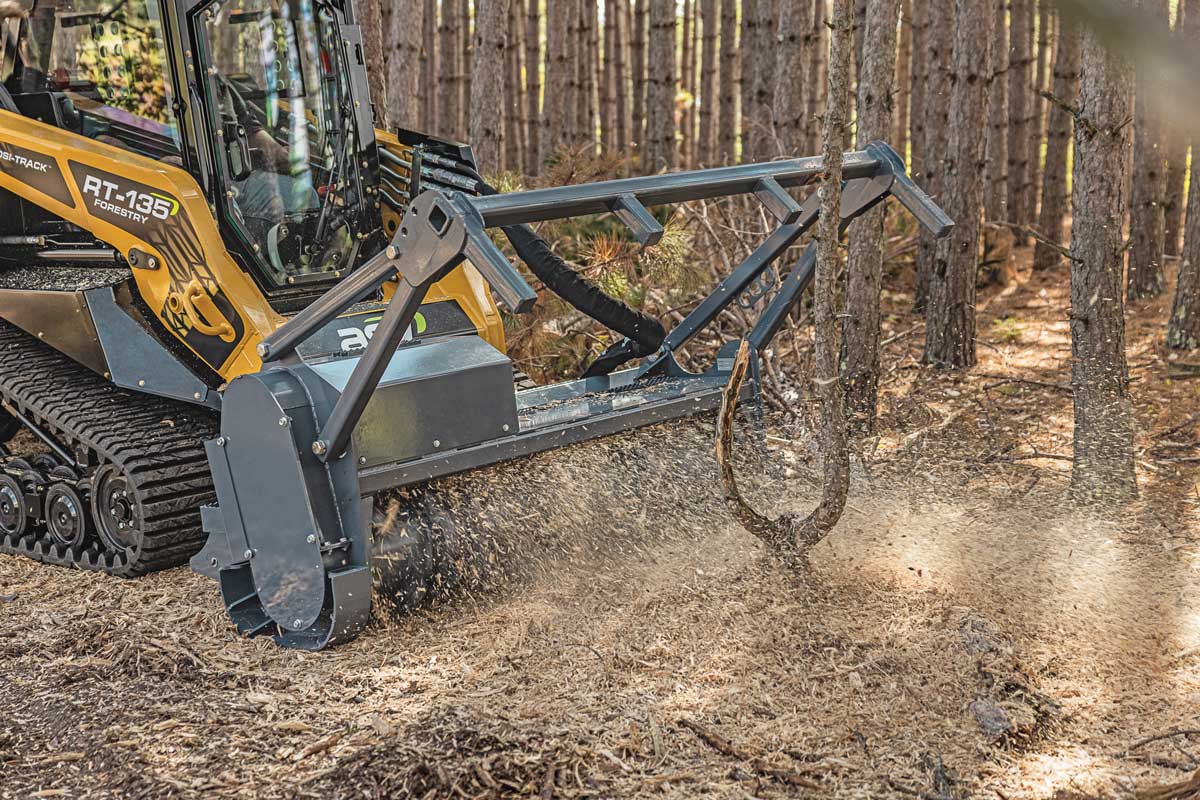
Track loaders are an American favorite. This versatile attachment taker boasts low ground pressure, easy transportability and a large power vs. small size ratio. A big part of the allure is a compact track loader’s adaptability. Like its wheeled skid steer cousin, CTLs can power hundreds of hydraulic and non-hydraulic attachments from brooms to buckets, working in industries as diverse as grading to tree farming. New markets continue to emerge. Brush cutting, for example, has become an important expansion application for compact track loaders. There have been big dedicated tracked brush cutting machines from brands like Rayco and Fecon for decades, but CTL makers finally got the idea that they could morph a small track loader to handle similarly tough brush hog work at a lower price point (like $100K vs. $300K).
“It’s the type of work and the size of the jobsite,” says Buck Storlie, product manager at ASV Holdings Inc., discussing CTLs vs. dedicated brush cutting tractors. “So CTLs hold the advantage in transportability, right? Easy to move from site to site. Faster ground speeds and a universal attachment coupler too. Dedicated mulchers hold the advantage in most available horsepower and flow — in power that you’re able to deliver to the ground. So, when you’re getting into large lot clearing sites, a dedicated mulcher is typically your best investment, but if you’re primarily doing underbrush clearing on smaller sites, moving from location to location, 5 acres or less, then a compact track loader is typically the better choice.”
As valuable as vegetation is, it usually needs to be managed in some fashion — trees, saplings, bushes and fields for new construction. Other times we need to manicure overgrown right-of-ways or remove forest storm damage. In many of these cases, a compact track loader with a vegetation management attachment is an excellent solution.
“There are many different ways to upfit your compact track loader to further accommodate brush cutting applications,” explains Ethan Clowes, JCB product manager of skid steers, compact track loaders and backhoe loaders. “First of all, you need to ensure your cab has a polycarbonate windshield installed for operator safety as well as roof, front and side guards and a rear bumper bar to protect the operator. Our vegetation management portfolio features attachments like brush cutters, disc mulchers, drum mulchers and grapples. But the one thing we cannot stress enough: It is extremely important to select a mulcher size that is well-suited to your machine.”
Let’s start with …
The Host Machine
Compact track loaders look just like skid steers — even using the exact same universal attachment system — but are engineered with a dedicated rubber track undercarriage. Steel tracks are available but only from one or two select brands. Compact track loaders or CTLs can spearhead operations and navigate jobsites with more flotation and less ground pressure than wheels. That means CTLs work great in muddy and wet conditions and also leave a lighter footprint on surfaces. These units also have great traction and pushing power. All of this makes them ideal for forest and brush work, navigating both boggy and hilly terrain safely.
There are many factors in buying a compact track loader for your operations — size, price, automation, comfort, transportability, attachments and onward — and I’d encourage you to look around this site to delve deeper into buying a complete host unit. If you’re keen on brush cutting apps, a major consideration will be the compact track loader’s lifting capacity vs. the weight and width of the attachment. For instance, consider how flotation may be an issue with a heavy mulching head on soft ground. The weight and balance of the unit makes stability an important consideration when operations are often in or on rough terrain, steep hills and wooded valleys.
A track loader’s auxiliary hydraulic power to the attachment will also be very important, measured in gallons per minute (gpm) and pressure (psi). CTL manufacturers offer standard- and high-flow aux power options. The latter is more popular for aggressive brush hogging jobs, but standard-flow brush cutters are available on the market.
Compact track loaders are the most popular category of compact equipment in America. Learn why with loads of track loader features right here.
“Our standard models use between 16 and 25 gpm of hydraulic fluid per minute, whereas high-flow models use between 26 and 42 gallons per minute,” says Jason Simmons, program manager of attachments at John Deere. “High-flow machines offer the operator enhanced versatility and productivity. An additional advantage of operating high-flow machines compared to standard-flow equipment is that they have the ability to recover faster and can continue their rotation even while making other adjustments to the boom or bucket height. This offers less downtime on the job, getting the operator back to work sooner.”
Brush cutting pros tend to gravitate toward the biggest compact track loaders for brush work — that 3,000-plus-lb rated operating capacity segment — like John Deere’s 333G unit with an MH60D mulching head. “We hear the term ‘rig’ often used by our customers in this application,” says Simmons. Using such high-powered attachments can cause a lot of heat in the hydraulic oil (and everywhere else), so hydraulic cooling kits can be mounted to the roof, available from some machine manufacturers and via aftermarket specialists. Some brands also see diesel engine aftertreatment becoming a factor in heat generation and thus unit selection.
“Many customers have downsized to 74-hp compact track loaders due to DEF [diesel exhaust fluid] requirements and the fact that machines with greater horsepower run hotter with the aftertreatment system, creating a potential fire hazard when producing such fine mulch,” says Clowes.
On the topic of cooling, a reversing fan is a must for dusty, dirty vegetation management.
“From a machine standpoint, first and foremost you gotta make sure you got the proper cooling specifications,” emphasizes Storlie. “Larger cooling packages are typically required due to the high load, the high heat and then the high dust and debris applications. A reversing fan is a must. It reduces your cleaning interval times, and it keeps your system operating cleaner. Cleaner means cooler, and cooler means more product longevity.”
Last year, ASV launched its RT-135 and RT-135F forestry variant. Both machines boast an industry-leading 132-hp Cummins diesel engine that’s combined with a head-turning 50-gpm maximum auxiliary flow — the industry’s highest — and an oversized auxiliary pump capable of 66 gpm, allowing the RT-135F to power gnarly high-flow implements like brush cutters. That also directly translates to more productivity from the 50-gpm Loftness mulching head that is sold with the RT-135F. This is a radial-lift unit, since ground-engaging work is the focus (not lifting high). Most track loaders going into forestry work utilize a radial- vs. a vertical-lift orientation.
Guarding and machine armor will be equally important for the host machine. Brush cutter attachments are designed with deflecting chains, front shields and push bars that deflect debris toward the ground and away from the operator, but if the occasional piece of debris gets caught and ejected from the back of the unit, your operator will appreciate that shatterproof cab door.
Maintenance Musts
It is essential for operators to learn how to use the equipment properly to safeguard the machine and guarantee it will perform at its best. All operators and managers are encouraged to read the equipment manuals and follow proper maintenance cycles to ensure ideal performance. Daily checks ensure that a proper visual inspection of components has been completed prior to operating with the attachment. On the mulching head, these checks involve taking a look at things like belts and hardware, checking for damage or dull teeth and making sure the attachment is lubricated as needed. On rotary cutter blades, routine maintenance is important for performance. Daily checks of the blade for dullness or damage should be completed. The most common wear part on rotary cutters is the blade. Owner operators might sharpen dull blades themselves several times prior to replacing. Some rotary cutter models also offer blades that can be flipped once a side is worn. Owners should always consult the operator’s manual for proper maintenance. — Jason Simmons, program manager, attachments, John Deere
“Land management and forestry customers upfit their Kubota SVL machines with lots of forestry guards,” says Patrick Baker, Kubota product manager of construction equipment. “We offer lots of kits for ample machine and operator protection for our SVL97-2 in a forestry application — an auxiliary coupler guard, DEF guard, rear guard, light guard with brackets, FOPS Level II guard and a polycarbonate door. Kubota offers very durable and supportive tracks in all applications, and the track offering holds up very well in a forestry setting.”
When it comes to tracks, operators often prefer bar-style rubber tracks for vegetation management operations. Moving into the cab, automation and digital technologies on the host machine may also benefit operators working in the woods. Telematics is an umbrella term for a variety of technologies and services that monitor a unit, collecting and sharing digital data on everything from systems analysis (think maintenance) to location (think theft). Telematics on a forestry CTL can help track a machine in a remote environment while also giving important maintenance analysis for rugged work cycles. Machine control systems may also be key.
“Using your CTL’s creep speed control feature to maintain even hydraulic flow to the attachment while adjusting ground operation speed is extremely valuable,” notes Clowes. “It’s also important to know when the drum or disc speed is too low so you can back off to allow the rotary attachment to recover before reengaging.”
The Attachments
When it comes to picking a vegetation management attachment, many different types of categories, styles and heads are available on the market today. Buying decisions need to be based on applications (project sizes, brush types, etc.), operating costs (fuel and consumable knife or blade costs) and maintenance requirements (time and replacement parts). There are two main types of brush- and tree-tackling attachments for CTLs.
“Wacker Neuson offers both the drum-style mulching heads as well as rotary cutters,” explains John Dotto, product application and training specialist at Wacker Neuson. “The rotary cutter should be considered a very interesting option for contractors who are looking to get into land clearing work but not necessarily mulching. Rotary cutters are very capable of tackling many vegetation management jobs and deal with gnarly species like mesquite and buckthorn quite well, and they do it at a much lower cost to acquire. A high-end rotary cutter should price out at roughly half the cost of a mulching head, with more economical solutions also available. They don’t produce a fine mulch but do a heck of a fine job clearing stringy brush and small trees.”
Wacker Neuson’s most popular model for mulching and brush cutting is its largest and most powerful machine, the ST50. As the name suggests, rotary cutters use a rotary, deck-type mower with usually two large swinging blades to tackle overgrown green space (from 4 to 8 in thick). There are some extreme rotary cutters on the market with four spinning blades. Rotary cutters tend to be less effective in heavier material, but they are ideal for light brush and maintenance mowing. Features might include front and rear chains, pusher bar, stump jumper, side discharge chute and options like a case drain, pressure gauge or various motors. Popular sizes for rotary cutters are 60, 72 and 78 in.
Drum-style mulching head attachments are designed for heavy-duty brush shredding applications such as land clearing for fire breaks, real estate development and right-of-ways maintenance. In this arena, horizontal drum rotors with fixed cutters have emerged as the most popular type of head. Units often come in common sizes such as 60, 66, 72, 76 and 90 in. and can utilize 33 to 60+ gpm of aux flow at up to 6,000 psi. Important considerations when selecting a drum-style mulching head are the cutting teeth and rotor options. Most mulching heads can be used with either carbide teeth or sharpened knives.
“Carbide teeth are a durable, low-maintenance option for inexperienced operators, and they are usually recommended for rocky conditions,” explains Bill Schafer, product development supervisor with Loftness. “Lately, however, more operators have been gravitating toward sharpened knives. Although knives are not as durable and require regular sharpening, they are much more aggressive, making them capable of cutting finer and working faster than carbide teeth.”
As sharpened knives have become more popular, so have limiting rotors, says Schafer. Because knives have a natural tendency to bite into material more aggressively than what is ideal, a limiting rotor helps control the material in feed for more efficient performance. “The two main types of limiting rotors available today are ring-style and depth gauges,” he notes. “Ring-style rotors are generally known as having the most restriction. Depth gauges aren’t quite as restrictive, which allows operators to pick up material from the ground easily, especially when using less aggressive carbide teeth.”
Another important factor is cutting width. While it’s true that a wider head can cover an area more quickly, it may not accommodate the ground contour. For instance, in narrow ditches, a 5-ft-wide head will likely be able to cut lower to the ground than a 6-ft-wide head. Cutting width also ties back in with hydraulic horsepower. A person concerned about low-end hydraulic requirements may be wise to select a narrower model over a wider one.
As mentioned earlier, most drum-style mulching heads prefer high-flow hydraulics on a compact track loader, but attachment experts are creating standard-flow options. Fecon’s RK6015 mulching head and the Loftness Battle Ax L Series are prime examples (the latter is designed for standard-flow loaders with 16- to 30-gpm hydraulic flow ratings). There are also other attachments options — tree and brush pullers, root rakes and stump shredders are available to outfit an entire vegetation management arsenal.
“Our portfolio features four primary attachments: brush cutters, disc mulchers, drum mulchers and grapples,” explains Clowes. “The brush cutter is a great option for cutting grass and smaller brush. Both the disc mulcher and the drum mulcher excel at cutting down trees. The more cost-effective disc mulcher is used for larger applications but does not process a particularly fine mulch. Meanwhile the drum mulcher is a bigger investment but produces a nice, fine mulch when processing the downed material on the ground. A grapple can be used for removing debris from a worksite.”
Operation
Each vegetation management job and attachment will require a specific approach. For instance, when operating a drum-style brush mulcher, it’s recommended to operate 500 psi underneath the maximum hydraulic relief pressure (so if it’s 3,500 psi, then don’t exceed 3,000 psi). Most mulching heads have a pressure gauge on the top of the unit for easy reference. For a rotary cutter…
“Try to keep the cutter deck and blades clean — clear of grass, dirt and debris before and after use,” says Baker. “Inspect the area of work to make sure there are no hidden objects that could damage the cutter and the machine or harm the operator. Complete a machine and brush cutter daily check. Inspect the cutter’s nuts and bolts, clear debris and make sure the hydraulic connections are free and clear of any debris. Also, don’t push the cutter too hard or bog the cutter down by trying to handle material that is too large. This will damage or hurt the attachment and the machine.”
There are several techniques to using a drum-style mulching head, according to Schafer. “First, the head can be tilted back to expose the knives for felling standing trees,” he says. “Next, operators can shave off large material from a felled tree by lowering the rear of the unit to contact the trunk, which prevents logs from being ejected to the rear. Another application is forward mulching. When doing this, the rear of the cutter can be lowered close to the ground to help trap material in the cutting chamber for more thorough processing, if desired. Operators can also reverse mulch or back drag. Here, the head is tilted forward while the skid steer or track loader backs up. This is very effective for sizing material, since this action pulls the downed material against the cutter bar and into the chamber.”
Check with the host machine and attachment maker for technologies that help with productivity and safety.
“When it comes to operation, the Deere RS72, RX72, RX84 and MH60D attachments each incorporate a push bar that can be used to direct material and help push trees away from the carrier,” says Simmons. “Roll the head forward when back dragging to better engage the material on the ground. When operating a mulching head, don’t push the head into the ground in rocky conditions. This will help avoid tool breakage and excessive wear.”
Obviously, operators should consider the size and density of the brush or small trees on the project. Trying to cut down a tree larger than what is recommended by the manufacturer can increase safety risks. Work with your dealer or the manufacturer to ensure you are buying the appropriate attachment for your compact track loader. They will probably have some operational advice too, especially with local conditions in mind.
“It certainly is a full contact environment, so going slower is faster,” says Storlie. “Use caution. The other most common mistake I would say is probably over tilting with the brush cutter heads. And by that, I mean you’ve got a rotary drum or a turning blade that’s throwing a lot of material. If you rock that attachment too far forward, let’s say even on the ground, then the attachment itself can start throwing that material back towards the machine. It can be dangerous. That’s when an operator is happy they properly equipped their unit with a three-quarter inch polycarbonate door.”
Keith Gribbins is publisher of Compact Equipment.
For reprint and licensing requests for this article, please click here.