Air Compressor Safety — Tips for the Top 5 Air Tools
When it comes time to choose the right tools for the job, there are a number of reasons why pneumatic tools — air tools — are preferred over their electrical counterparts. Air tools deliver more productivity through higher torque and can be used in challenging work environments, such as flammable or wet conditions.
All the standard safety measures apply when operating pneumatic tools, such as wearing protective gear, and performing regular maintenance and visual inspections. But it’s also important to take into consideration the safety guidelines specific to each tool and the manufacturer recommendations for properly operating the air compressor that powers it.
1. Breaker/Chipper
Whether using a 60-lb breaker or a 30-lb chipper, it’s important to use an air compressor that delivers the proper pressure. Using incorrect pressure can damage equipment — both the air tool and the air compressor. And although an incorrect airflow setting may not damage an air tool, it will prevent the tool from operating correctly.
Breakers and chippers are common on construction sites where multiple tools may be connected to the same air compressor. It’s important to properly size the air compressor to the needs of the tools being powered. A 185-cfm air compressor can typically operate two pneumatic tools, such as a breaker and clay spade, but larger air tools may require a higher volume of air or greater pressure to perform correctly.
Rating information typically corresponds to the weight of a piece of equipment. For example, a 90-lb breaker requires 90 cfm, and a 60-lb breaker needs approximately 60 cfm.
A dual pressure air compressor such as the Doosan Portable Power P250/HP185 delivers the pressure and flow typically supplied by two units. The variable pressure and flow settings are controlled with a simple push-button keypad, so it’s essential to ensure the proper pressure has been selected on the control panel before operation.
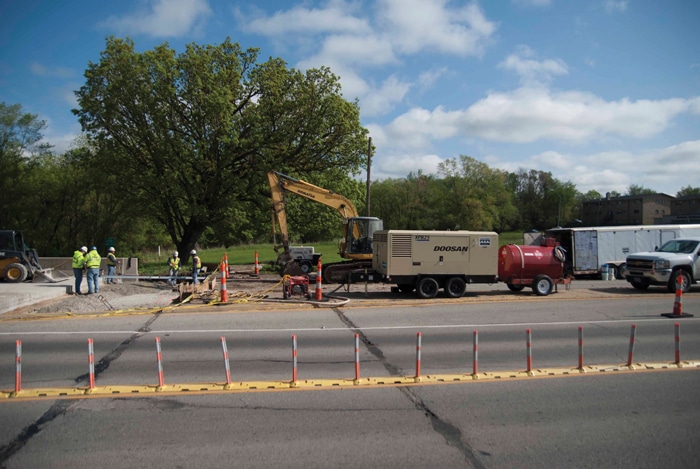
It is important to take into consideration the safety guidelines specific to each pneumatic tool and the manufacturer recommendations for properly operating the air compressor that powers it.
2. Paint System
While painting systems come in a variety of styles and sizes, one thing they have in common is the need for quality air. When moisture, oil and dirt accumulate in the lines of an air compressor, these contaminants can lead to a poor quality finish and spoiled paint surfaces — not to mention decrease the lifespan of air tools.
Using an air compressor with specialized features that eliminate contaminants is an important consideration for painting applications. For example, Doosan Portable Power air compressors include a patented IQ System for cleaner air.
Models with the optional IQ System feature: an onboard aftercooler with 20 degree F approach; coalescing dual filtration system; and an exclusive, zero-discharge condensate removal system — all of which work together to remove oil vapor and other common contaminants to improve the quality of the paint job. The result is a fine surface finish, whether painting a water tower, bridge or a large ship.
3. Abrasive Blasters
Abrasive blasting is a highly regulated industry that includes a multitude of hazards and safety procedures. The value chain of abrasive blasting includes high-pressure hoses, metal blast nozzles and hose couplings. Additional safety precautions can help prevent injury from malfunction or improper use of these applications.
Many air compressor manufacturers such as Doosan Portable Power recommend the use of whip checks on all pressurized hose applications. The steel cable fits over hoses or couplings with spring-loaded loops, providing an additional layer of protection. The cable prevents hose whip in the event of accidental separation of the hose connection during air compressor operation. Whip checks are also required by the Occupational Safety and Health Administration (OSHA) to meet hose restraint compliance.
4. Directional Boring Tool
Underground utility contractors and landscaping companies are familiar with directional boring tools, commonly used as a trenchless method of installing water lines, sewer lines, fiber optics and underground pipes.
Because directional boring tools are frequently used in heavily traveled areas, using an air compressor model with curbside controls and service valves that keep operators from entering the roadway will significantly increase safety.
Air compressors should always be parked on a level surface and operated with closed doors and chocked wheels. Not only does this reduce the chance of the machine tipping or rolling into traffic areas, but many models will not operate properly if positioned on an incline.
5. Air Drill
Air hammer drilling, sometimes referred to as wellbore or down hole drilling, consists of a pneumatic hammer positioned at the end of a drill stem. Compressed air operates a piston that repeatedly strikes the top of the bit at a rapid rate.
Safe air drilling operations can be achieved only with extensive operator and safety training. This training needs to include environmental regulations regarding air compressor operation, such as 110 percent fluid containment requirements. Air compressors used for air drilling operations should be capable of delivering optimal performance despite harsh jobsite conditions — preventing disruptions and distractions that increase safety risks and lower productivity.
Rus Warner is manager of global air products at Doosan Portable Power.