How to Properly Maintain Your Skid Steer/Track Loader’s Hydraulic System
The diesel engine isn’t really the heart of a skid steer. When it comes to a heart (the machine’s pumps), a skid steer or track loader actually has three or four hydraulic hearts. These pumps power fluids — compressed oil — to move, spin, lift the boom, curl the bucket and run a zillion different attachments. This set of hydraulic pumps (gear, hydrostatic, tandem, back to back, variable displacement) come in many configurations, brands and power ranges. Over the last decade in particular, the science and technology behind these systems has made them smaller, more efficient and more sophisticated.
“Probably one of the biggest innovations in the last five to 10 years has been the advent of electronically controlled hydraulic systems. We call them EH systems,” explains Nathan Wood, hydraulics system engineer for John Deere Construction and Forestry. “You’re controlling the hydraulic system precisely with electronic signals. It leads to a lot more controllability and a lot more ability to do different types of automated controls and functionalities.”
“Originally the first skid steers were hydrostatic controlled by mechanical linkages,” says Kevin Scotese, product manager of sales support, compact equipment, at Volvo Construction Equipment. “The next step in the evolution was the implementation of pilot controls, and the last step has been in the improvements of electro hydraulic controls, which provide the possibility to customize the feel, speed and responsiveness. Another technology to maximize the power and reduce parasitic losses is the implementation of state-of-the-art closed center load-sensing systems in combination with the variable axial displacement piston pumps.”
Pretty high-tech stuff, eh? Today, fluid power is being used to control everything from the tracks to the attachments to the cooling fan to automated features such as creep mode, return to dig and settable attachment speeds — all built right into the joystick. But as you might expect, skid steer and track loader hydraulic systems have gotten quite complex, and just like any oil system in a machine, it will definitely require routine maintenance, testing and proper seasonal oil.
How Does It Work?
Well, that all depends on the size and configuration of each skid steer or track loader. Every brand is somewhat similar, but each unit is engineered uniquely. Let’s break the system down into two parts: 1) the hydraulics powering the boom, bucket and auxiliary circuit and 2) the hydrostatics powering the wheels or tracks. The hydraulic system powering the boom, attachment, automation features and even cooling usually uses up to three pumps — a main hydraulic pump, a charge pump, which provides control pressure, cooling and fan power, and if you get the high-flow option, a third high-flow pump. Without that option, there are two.
“For the pumps powering the arm, bucket and auxiliary hydraulics, smaller machines run a gear pump, but on the larger models this is a load-sensing axial variable displacement pump limiting the parasitic losses and providing better power to the loader functions and auxiliary,” says Scotese. “For the auxiliary, high-flow option on the smaller models, an additional gear pump is utilized in tandem to provide the required flow. On larger models, a higher-capacity load sensing axial variable displacement pump is providing the higher flow. Charge pressure and flow for the transmission and hydraulic fan motor is usually provided by a smaller PTO-mounted gear pump.”
When it comes to powering the tracks or wheels, there is a bigger, double-pronged hydrostatic pump that powers the machine’s mobility. There is a hydrostatic pump that provides flow and pressure to one motor on the right-hand side and one motor on the left-hand side. On a skid steer or track loader, it’s usually one tandem pump or back to back, providing dual power to two motors for each set of wheels or tracks.
“We call it a tandem pump or a back to back, but it’s really two axial piston pumps that are reversible, tied together with a common manifold,” says Wood. “A tandem would be facing the same direction and a back to back would be facing the opposite direction. It’s really manufacturing and packaging that determines how they’re going to put that together. So it is one component, but there are two pumps in it, and we call it the hydrostatic pump. One pump in there provides the flow to one side of the machine, and the other pump provides it to the other side of the machine.”
Manufacturers use lots of different brands of pumps — Danfoss, Turolla, Rexroth, Concentric, Eaton and Parker Hannifin. These pumps combined with the overall hydraulic systems come with three main specifications — system pressure (psi), gallons per minute flow to the attachment (gpm) and overall hydraulic horsepower (which tops off about 100 hp). Each manufacturer will engineer and market those specs differently.
“Starting with the hydrostatic system, the transmission and drives system, pressures are pretty high, upward of 6,000 psi,” explains Woods. “These are heavy-duty components to get the speed and torque you want. When it comes to the hydraulic system, bucket, boom and aux, typically you’re running between 3,000 and 5,000 psi. We run right around the 3,500-psi range. We find that that allows us to use reasonably sized cylinders and boom geometry to get the breakouts we need, while still maintain the speed we require.”
Hydraulic flow to the auxiliary circuit and the attachment will be determined in gpm and as standard- and high-flow configurations. Bobcat’s tiny S70 skid steer uses 9.8 gpm for its standard flow system. The optional high-flow on the Takeuchi TLV12V2 (the biggest track loader on the market) is 40.4 gpm. The price difference between standard and high flow usually falls right around the $3,500 range (5 to 7 percent more), and the high-flow option is usually more common on the largest skid steers and track loaders.
“ASV builds the widest range of track loaders in the industry from the RT-30 with a flow of 10 gpm up to the RT-120 with a max flow of 45 gpm,” says Bill Wake, ASV director of product development. “The RT-120 also features variable flows and operator adjustable settings ranging from 0 to 45 gpm depending on the attachments needs.”
Properly Maintain the Hydraulics
Let’s start off with this ubiquitous warning: It’s very important to review your owner/operator’s manual before attempting to perform any maintenance to the hydraulic system, taking special care to review the safety procedures listed in the manual. With the variety of options available today such as high flow, bucket self-leveling, ride control and hydraulic quick-attach brackets, there may be up to five or six control valves as well as pumps. All of these components are designed with very tight tolerances, which may fall below 0.001 in. Because of this, keeping the hydraulic system clean is critical to the life of these components.
“Keeping the system clean and cool is the No. 1 objective,” explains Wake. “ASV has the largest cooling packages and hydraulic tank capacities in their respective classes. That combined with double and triple filtering assures the oil is kept both clean and cool. Owners can help by following the maintenance guidelines in the machine’s owner’s manual, as well as making sure to clean around the hydraulic cap before removing. Be sure any hose fitting is cleaned before removal, and wipe off quick-coupler ends before hooking attachments to the machine.”
Contamination can enter the system in a variety of ways. Before removing the hydraulic oil reservoir cap, clean the area around it to prevent dirt from entering the tank. If using a bucket, make sure that there is no loose dirt on the lip. While all machines will have at least one hydraulic filter to remove debris from the system, this filter might be in the return side of the hydraulic system. There is a screen inside the tank to prevent large material from getting into the pumps, but it won’t catch small particles. Make sure you look for features from brands that make using and cleaning the hydraulic system easier.
“A very important feature which is standard on Volvo skid steers is the case drain on the auxiliary block and the pressure relieving by simply pushing in the quick-connect couplers on the manifold which simply vents pressurized oil in the main lines to the tank. This is a very well-liked feature to ease the hookup of hydraulic lines,” says Scotese.
In order to further prevent contamination, make sure to follow the OEM’s service interval for hydraulic filter replacement. This may fall anywhere between 500 to 1,000 hours depending on manufacturer and operating conditions. A plugged up hydraulic filter may cause a variety of issues such as loss of speed or power, overheating of the hydraulic oil and damage of components. What type of hydraulic oil should be used in your loader?
“The oils that we recommend for our machines are proprietary John Deere products,” says Wood. “We control the specs, and they are available worldwide. We have two different versions — one is an all-season oil, and one is cold weather oil.”
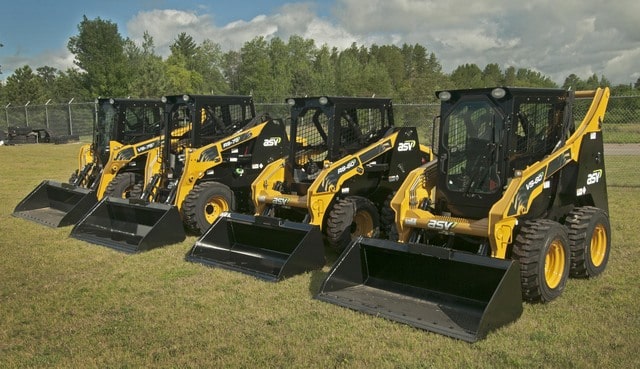
Keeping the system clean and cool is the No. 1 objective.
Just as important as the type of hydraulic oil used is the amount in the tank. The operator’s manual will show where the level should be within the sight glass and where the boom and bucket should be located while checking the hydraulic oil level. Most machines should be checked on a level surface while having the boom all the way down and the bucket flat on the ground. Hydraulic oil should be checked daily, if not before every time the machine is operated. If the level is low, look around carefully for leaks. Given the dusty and dirty conditions that skid steer loaders and compact track loaders operate in, it is not uncommon for debris to damage the hydraulics and thus affect things like “feeding speed.”
“Brushcutting and cold planing are a couple examples of demanding applications on a hydraulic system,” says Wake. “Both can use 100 percent power at nearly 100 percent of the time. In demanding applications like this, the key to maximum production is feeding speed. Feeding the attachment at a rate to use 100 percent of the power — but not exceeding it to the point the engine bogs, the attachment slows greatly or the attachment stops — will give the most production with the least demand on the machine and operator. A feed pace with the engine pulling a few hundred rpm off peak, tends to be the sweet spot.”
The accumulation of debris from an application like brush cutting can harm the hydraulic cooler. The oil cooler might use engine coolant or outside air to cool the oil. It is vital that the oil remain within the acceptable operating temperature range. Make sure the oil cooler is free of debris and the cooling fins are fairly straight. “John Deere has an electronically controlled hydraulic fan that can vary the speed based on the required cooling,” says Wood. “It’ll also automatically reverse at a set interval to expel the debris built up on the coolers to help limit the number of times you actually have to physically clean out the cooling package.”
Another common way for contamination to enter the hydraulic system is by using hydraulically powered attachments. Before connecting any of the auxiliary hoses, be sure to wipe off the connectors to get rid of any water, dust or other debris. If an attachment was used on a loader that had a hydraulic failure and spread contamination into the attachment, that contamination may enter the next machine it’s connected to.
“That’s probably one of the more concerning things,” says Gregg Zupancic, product marketing manager of skid steers and compact track loaders with John Deere Construction and Forestry. “When you rent attachments, the question is: Who rented that machine last, and what types of materials are in their hydraulic systems and sitting in that attachment unused for a long period of time? That’s why you do things like hydraulic fluid sampling.”
Keep It Cool
Check Out Loftness’ Innovative Hydraulic Oil Cooler Attachment
The Cool Flow hydraulic oil cooler from Loftness Specialized Equipment greatly reduces the risk of overheating in skid steers and hydraulically powered attachments when operating in demanding applications and hot work environments. The automatic thermostat-controlled fan provides adequate cooling to the system whenever needed to boost machine efficiency, even when an attachment is not being used. Unlike most other hydraulic coolers that are mounted near the attachment, the Cool Flow attaches to the roof of a skid steer cab where it is less susceptible to vibration, back pressure, debris and potential impact damage. It is specially engineered to allow full hydraulic flow to the attachment in either direction without risk of damage to the cooler. The Cool Flow has up to 40-gpm flow capacity and is compatible with all brands of skid steers.
For more info, visit loftness.com.