Electric! An Overview of the Battery-Powered Stand-On and Walk-Behind Tool Carrier Market
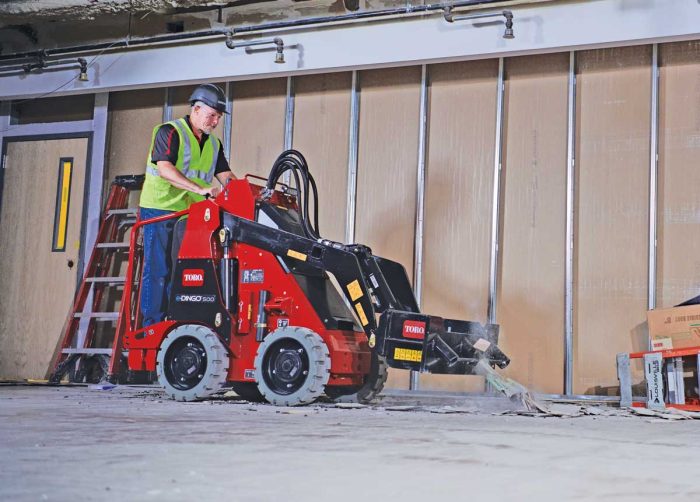
As one of the smallest categories of attachment-takers in the construction equipment industry, compact tool carriers make perfect candidates for electrification. These stand-on or walk-behind machines are small and ideal for battery packs. Compact tool carriers (sometimes called mini skid steers, compact utility loaders or stand-on track loaders depending on the manufacturer) often work in urban areas and even indoors, where emissions and noise regulations might not allow diesel-driven machinery. Operating in cities and neighborhoods, CTCs will have better access to power charging. Also, the natural start/stop, jump on/jump off work cycles of compact tool carriers lend themselves to lower operational hours, as electric units do not idle and waste fuel.
“It is really interesting to see who is gravitating toward electric equipment,” says Mike Slattery, VP of business development of Volteq Equipment, a new brand dedicated to electric with its battery-powered Sky mini skid steer lineup. “People working indoors are first in line because there are no exhaust emissions, and battery-powered machines operate with far lower decibel outputs. Landscaping construction is a strong second, heavily based on the initial idea that quiet operation can mean working earlier or later in the day, thus more billable hours. Public entities and governmental customers are embracing battery power as a step toward environmental and sustainability goals [ESG]. It is also worth mentioning the rental channel because as a customer, rental outlets serve a vast array of industries and applications that can benefit from battery-powered CTCs.”
The market for electric CTCs is a little different than the diesel-powered sector, which includes manufacturers like Toro, Bobcat, Ditch Witch, Kubota, Ramrod, Vermeer, Wacker Neuson and just recently Case Construction Equipment. Out of all those major brands only Toro offers an electric variant in America — its eDingo 500. The other manufacturers in the U.S. electric sector are smaller companies like Volteq, Firstgreen Industries and Cratos Equipment, but they are not without their bona fides. Cratos Equipment was one of the first brands in America to offer battery-powered construction equipment. It opened for business in 2013, and over the last 10 years has expanded its portfolio to include excavators, wheelbarrows and high tip dumpers, but it started with CTCs, which it simply calls “skid-steers.”
With electric machines finally gaining interest from American contractors, Cratos is positioned perfectly and is already expanding its business with a new facility in Pompano Beach, Florida, to improve storage capabilities and inventory management.
“Our existing facilities simply could not continue to service the demands of our growing customer base,” says Cratos founder and CEO Alex Berg. “We know the importance of having inventory readily available when our customers need equipment for a project start date.”
Demand is growing for battery-powered equipment in America, and now both classic and up-and-coming brands are starting to supply the U.S. market with electric iterations of compact tool carriers. What units are available? How do you pick one? Why should you spend extra money on a battery-powered machine? All good questions I’ll try to answer.
Volteq Sky Mini Electric Skid Steers
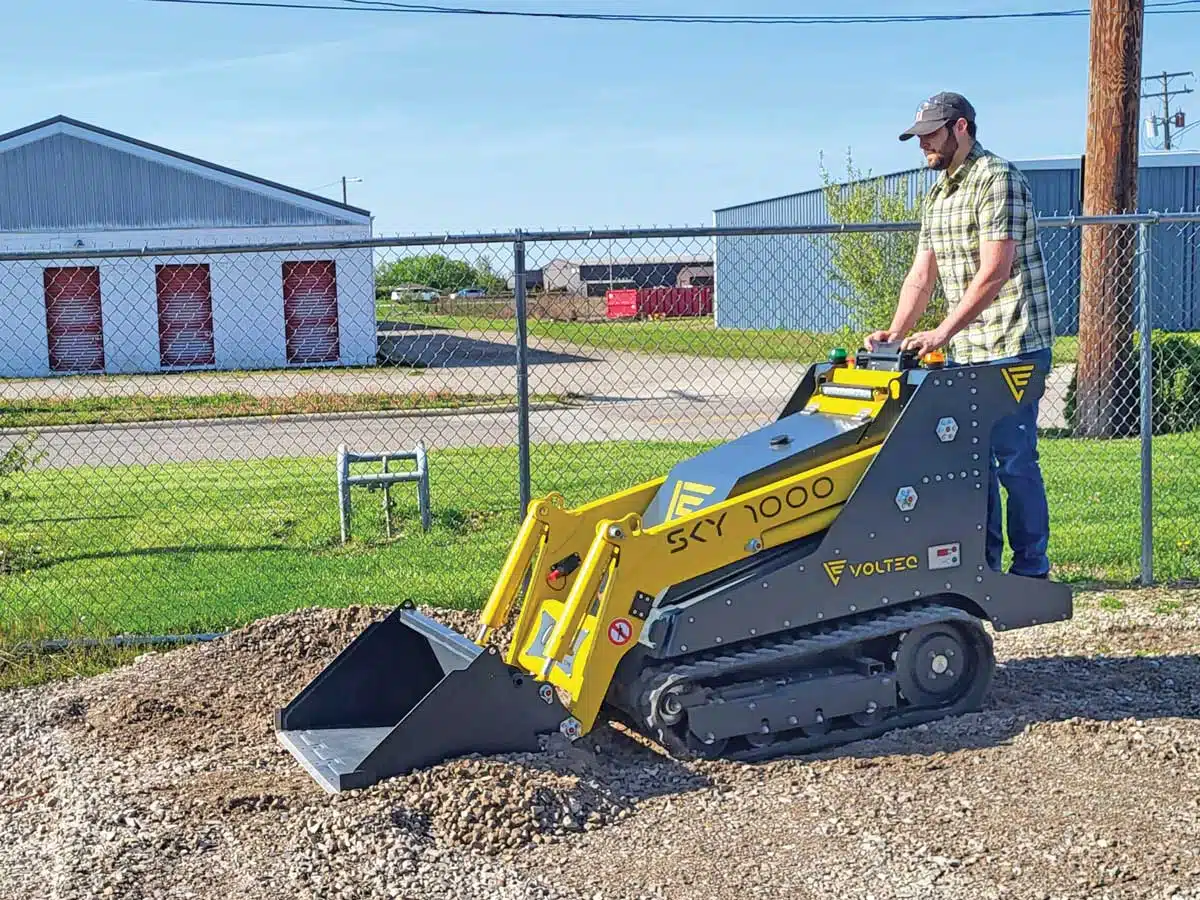
Volteq Equipment Inc. offers battery-powered mini skid steers with up to an eight-hour run time, built-in chargers, radio remote control, GPS, telematics and a universal mount system compatible with countless attachments. While only 34-in. wide, the Sky 1000 offers a 1,000-lb lift capacity and a 20.48-kWh lithium-iron battery. The Sky 2000 is in development for late 2024 and offers up to 50-kW lithium-iron battery and a 2,000-lb lift capacity. Speed up charging is likely to be more compelling as more powerful CTCs enter the market. Volteq’s Sky 2000, scheduled for Q4 of 2024, offers a lift capacity of 2,000 lbs, twice that of the Sky 1000. To minimize charging time of the larger up to 50-kW battery, it is likely customers without 220V power will make a small investment to upgrade their service and shorten charge times. These electric Sky mini skid steers also offer features like self-leveling and float functions. For more info, visit voltequip.com.
The Pros of Electric CTCs

Compact tool carriers have been evolving for 20+ years, so the emergence of electric models is just another stage. CTCs started off as wheeled, medium-power supplemental equipment and have morphed into track-driven, spec-heavy jobsite project leaders. Some units are nearly the size of a skid steer (just check out the Toro TXL 2000), noting electric models are usually pretty small. The size, power and versatility of compact tool carriers have significantly increased the sales of this category over the decades.
Think of CTCs as skid steers or track loaders without a cab. They use a similar universal quick-attachment plate (some can even wield a skid steer quick-attach plate), they come on wheels and tracks and they have a zero turning radius that’s ideal for tight quarters. Buyers have a bevy of options: stand-on and walk-behind units; hydraulic flow rates from 8 to 22 gpm; gas, diesel and electric power; wheels or dedicated track undercarriages; and a zillion different attachments (buckets, breakers, brooms, blades, backhoes and box scrapers, and that’s just the Bs). Electric models aren’t much different from popular diesel units.
“The eDingo is built to be an intuitive tool on the jobsite, and contractors familiar with operating gas or diesel-powered [CTCs] will find the experience much the same on the eDingo,” explains Sam Dando, product marketing manager at Toro. “The patented one-handed traction controls are user-friendly and allow for smooth and precise movements at any skill level. The eDingo features instantaneous torque that electric motors are known for. Contractors generally find that battery-powered equipment will typically meet or exceed the power and performance of similar gas or diesel machines.”
Instant response is just one of the many advantages of embracing electric equipment. With the absence of a diesel engine, maintenance on a battery-powered machine will be a lot less messy. Everything from checking engine oil to replacing fuel filters will no longer be needed. That time and money adds up over the years. Because electric equipment doesn’t create emissions, there will be no need for emissions aftertreatment systems like diesel particulate filters or extra products like diesel exhaust fluid or DEF. Electric motors are more reliable and durable than diesel motors, which could mean fewer overhauls. Pretty much the only maintenance supplies required on a battery-powered machine are grease and hydraulic oil.
“The absence of a diesel engine also eliminates a tremendous amount of vibration and noise stemming from combustion, exhaust and cooling fans,” says Slattery. “This is physically better and less stressful for those operating the equipment.”
Of course, there will be some new maintenance checks and training. Depending on your unit, the battery, charging plug, inverter, battery management system and power converter may need inspections. Service activities may require a trained high voltage technician, which would require a specialized class to enhance their knowledge on how to safely interact with wiring on battery-powered equipment and how to properly secure a machine before performing service. Those techs will need to wrap their minds around some new components. For example…
“When evaluating battery-powered equipment, ask sales reps about the ratings of the electric motors,” suggests Slattery. “Are they properly rated for nominal and peak power for the intended duty cycle of their respective function? You don’t need to understand all that goes into this but know that a motor can be viewed as undersized if it is operating at peak capacity in a continuous duty cycle. Track drives are a good example to explain this further. A motor that operates at nominal capacity under a continuous duty cycle will have the ability to intermittently deliver peak power for short spikes in demand, such as counter-rotating or climbing a steep hill, without over-taxing the motor. But if a motor is undersized and working at peak capacity under continuous loads, it may underperform in more demanding work and lead to excessive heat or shorter component life.”
Maybe the biggest benefits of electric construction equipment come from a trio of pollution factors — no emissions, no smell and low noise. Reduced noise, smell and emissions create a safer work environment for the operator and coworkers and keep jobsite neighbors happy. This non-pollutive trio allows pros to find new work. Indoor demolition, jobs near a hospital, nighttime projects or work inside a zoo might be new opportunities for a contractor.
“We designed the eDingo specifically with indoor construction and demolition work in mind,” says Dando. “In the past, contractors would need to spend extra time and money making sure indoor jobsites were properly ventilated if they wanted to use compact utility loaders [Toro’s brand name for CTCs], many of which don’t fit inside anyway. The battery-powered eDingo eliminates engine emissions, allowing it to come inside and make quick work of jobs that were historically accomplished manually.”
Compact tool carriers, compact utility loaders, mini skid steers. Whatever you call them, we can all agree these machines pack a lot of productivity in a small package. Learn more about them here!
Price and Charging Infrastructure
Brace yourself: Electric construction equipment can cost twice or three times as much as its diesel counterpart. Luckily, because of their size, electric CTCs can be somewhat economical. “The price of our Sky 1000 is only approximately 30 percent higher than its diesel counterparts,” says Slattery.
There are ways to lower that price. Federal and state grant programs and various tax incentives are available. Feel free to visit the U.S. Department of Energy’s website for a list of incentives, laws and regulations for electric vehicles at both a federal and state level (https://afdc.energy.gov/laws). It is essential that the buyer works with the dealer to understand grant and rebate opportunities that can help ease the pain of the purchase price.
“When looking at the return on investment for electric compact utility loaders, the easiest comparison is that you are purchasing the machine and most of its fuel needs for its lifetime — upfront,” says Dando. “The amount of money a contractor could potentially save on fuel costs by switching to electric equipment depends on several factors, such as the type of equipment, the size of the fleet and the cost of electricity in their area. Contractors can typically expect to save a significant amount of money by switching to electric equipment and often even recoup the investment over the life of the machinery. Additionally, battery-powered machines require little to no maintenance which increases their productivity on the jobsite.”
Slattery breaks down ROI into a few numbers.
“The short answer is that daily estimated savings of approximately $21.79 can be achieved by operating a lithium-battery-powered CTC vs. a 25-hp diesel-powered model,” he says. “If used for just 120 days of the year, that is an annual estimated savings of $337.45 before considering lower maintenance costs. These estimates are based on six hours of use per day and the national average U.S. energy costs for diesel [$4.10 per gal] and electricity [$.23 per kW] in the second quarter of 2023. Note that diesel-powered CTCs continue burning fuel when idling between tasks such as changing attachments or when talking with coworkers. In the same six hours of use, an electric CTC stops consuming battery power when no functions are active.”
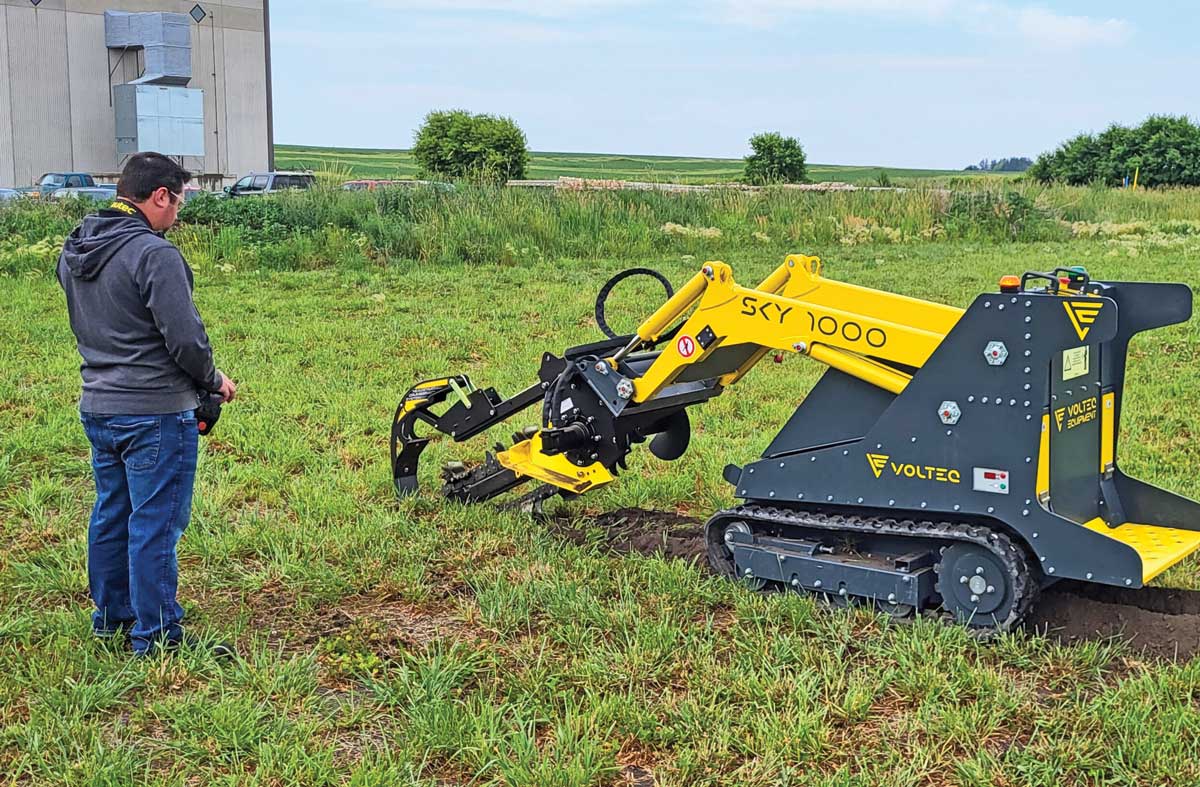
As it gets here realize there are charging options but not many fast charge options in the CTC sector. In the overall electric machine industry, there are on-board and off-board charging, stationary and mobile fast-charging and off-grid battery packs and solar powered charging stations. Almost all battery-powered earthmoving equipment will have an on-board charging option. An on-board charging system might plug into a standard single-phase, 110/120V wall outlet or a 240V level 2 AC outlet system, which will determine how fast the battery will charge. Using off-board, three-phase chargers can dramatically increase charge times, but most CTC makers don’t offer three-phase charging. Most homes in North America are wired for 110 to 240V single-phase power and most commercial and industrial buildings in North America use 277 to 480V three-phase power.
“Volteq’s Sky 1000 is really simple and convenient to charge,” says Slattery. “The on-board smart charger is compatible with single phase 90V to 265V outlets, empowering customers to control where and when they charge the Sky 1000. It can literally plug into a 110V outlet next to your smart phone and fully charge in up to eight hours, depending on the discharge level and input power. Lithium-iron technology allows opportunistic or partial charging during the lunch breaks without downgrading or hurting the battery. Customers are not forced to use a special connector, find a compatible charging station, have a secondary power bank or do full charge on a single charge.”
Overall, charging requires a thinking reset for machine pros. Toro’s eDingo has an onboard charger plug that fits a standard 120V wall outlet and fully charges the machine overnight so it’s ready to work first thing the next morning. Toro’s Dando shared several steps pros can follow to build a proper charging system:
- First, assess your current electrical load and identify the peak draw month to understand your facility’s maximum power demand. Evaluate your existing electrical capacity, typically measured in kilovolt-amperes (kVA) or kilowatts (kW), which can be found on your electrical service panel or through consultation with an electrician.
- Next, calculate the charger load for each piece of equipment in your fleet. Check the power rating (in watts) or current draw (in amps) specified on the charger’s serial tag or spec sheet. Divide the power by the voltage to determine the current draw. Repeat this calculation for each charger.
- Consider other electrical loads present in your facility, such as lights, computers, microwaves, refrigerators, security systems and any other equipment. These loads should be factored in along with the charger’s electrical demands.
- Add up the current draw of all the chargers and the current draw from other electrical loads to calculate the total electrical load. Ensure that your electrical service capacity can handle this total load. If it exceeds the capacity, you may need to consider electrical upgrades or alternate solutions.
- Consult with a qualified electrician to accurately assess your electrical system, ensure compliance with regulations and determine any necessary upgrades or adjustments to support your battery-powered equipment fleet.
Keith Gribbins is publisher of Compact Equipment.
Toro eDingo 500
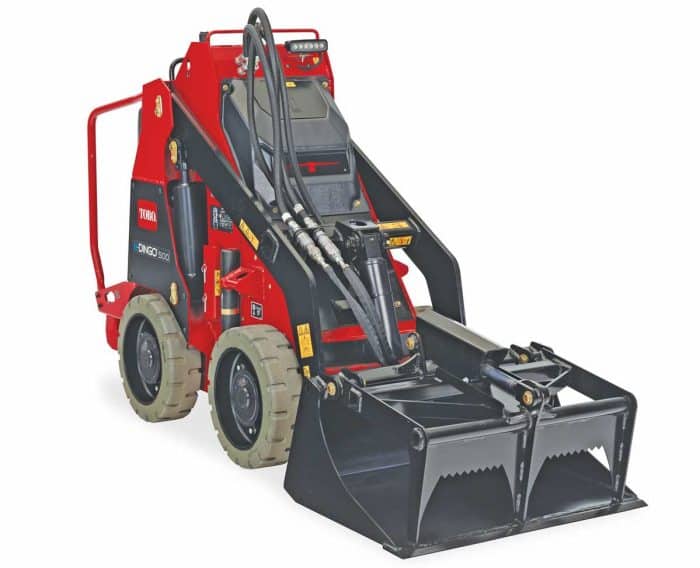
Toro engineers built the next generation of electric-powered eDingos to allow contractors and construction professionals to reap all the benefits and power of a standard compact utility loader with zero exhaust emissions and a significantly lower cost of operation. The eDingo is the ideal choice for indoor construction jobs that require heavy or continuous operation, fast completion times and reduced overall costs. The new design is now capable of fitting through even the tightest of doorways with a narrow width of 30 in., yet still boasts a rated operating capacity of 515 lbs and 6.5 gpm of hydraulic flow. It also boasts a hinge pin height of 81 in. The HyperCell Power System allows for all-day run times. New onboard charger and cord storage, patent-pending traction controls, a powerful 1,200-lumen work light for improved visibility and a comfort mat to fight operator fatigue round out the new eDingo features. For more info, visit toro.com.