Staying on Track
A compact track loader is one of the most versatile and useful tools within a contractor’s equipment fleet, providing improved capability over soft terrain and increased capacity compared to skid steer loaders. However, the very items that make them unique and so useful also require some special care to ensure reliable service and uptime.
As with most modern motorized equipment today, if you want a product to be reliable you must maintain it properly. No matter if the unit is purpose built from the ground-up or is an adaptation of a skid steer or crawler chassis — every machine has an operator’s compartment, engine, loader, auxiliary circuit, drive system for the tracks and (of course) a track undercarriage system.
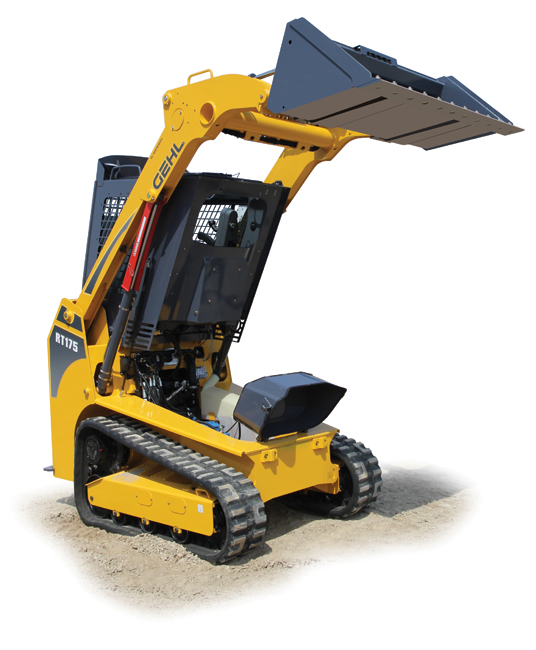
Maintaining the operators area is not that much different than on other pieces of equipment except that when track loaders are operated on hard surfaces, vibration of the cab and components is more intense. New track loader designs have taken steps to provide a smoother ride. Over time, intense vibration can lead to more maintenance depending on specific applications and operating conditions (like operation in soft soils vs. operation with a cold planner on concrete). With this in mind, an operator should pay special attention to hardware to ensure that all components stay securely in place. Cab mounts, seals and hardware should be checked on a regular basis. Loose components and hardware should be tightened, and damaged components should be replaced.
Track loaders are generally operated in dirty or soft ground conditions. Operators entering the cab tend to bring in a lot of soil and mud on their boots. As with most other products, the operator’s area needs to be cleaned on a regular basis. If the floor pod does not tip forward for easy clean-out, a shop vacuum should be used to ensure debris is removed. This is particularly important if the unit is equipped with an enclosed cab and air conditioning or heat. If the cab is equipped with a re-circulating air filter and a cab fresh air filter, they should be serviced on a regular basis. Keeping the air conditioner clean will ensure its long-term reliability.
The operator’s manual supplied with the product provides critical safety information and instructions on normal engine and hydraulic system oil and filter change intervals. Track loaders operate in fairly difficult conditions; spending a few extra dollars for regular oil sample testing will maximize your change intervals and help to ensure you are changing your oil and filters adequately. Oil sampling will also provide short- and long-term indicators of unusual wear or failures that are in progress to help eliminate downtime during critical periods.
Operators should also be very mindful of the diesel fuel systems. Water and fuel separators should be drained when needed. The new Gehl RT Series track loaders have a visual float indicator on the water fuel separator assisting personnel in keeping fuel clean and free of water. Change fuel filters on a regular basis. Also be sure to use good quality fuel from a secure, safe source that is of the proper grade for the ambient temperatures being operated in. If a fuel additive is used, make sure it is approved for the engine and emissions level of your engine.
Most engine intake systems today have an air restriction indicator on the air cleaner. These may be electric with an indicator light in the cab or manual when located at the air cleaner. Be sure to check your air restriction indicator before operating the loader each day. Manufacturers recommend air filters not be removed until the indicator shows they are in need of service. This reduces service work and eliminates the likelihood dirt will bypass the filters when inspected or replaced unnecessarily. The air filter elements should be replaced instead of cleaned. Taping air filters on a surface and cleaning them with an air compressor risks damaging the elements which can lead to dusted engines and very expensive engine repair bills, not to mention downtime. Inspecting air intake hose condition and connections and correcting any issues may eliminate costly engine damage.
Since track loaders are uniquely qualified to operate in harsh soil conditions, it is also important to check the chassis. Be sure all covers, doors, belly pans and shields are in place, in good condition and securely fastened. Manufacturers recommend the chassis be kept clear of debris and in most cases cleaned daily. This is required to prevent catastrophic failures due to accumulation of foreign material or overheating due to plugged radiators. The heart and soul of a compact track loader is its undercarriage and track system. Proper operation and maintenance will either lead to greater productivity or downtime and high operating expense. Proper operation and maintenance is not difficult, but does require following recommendations in your operator’s manual.
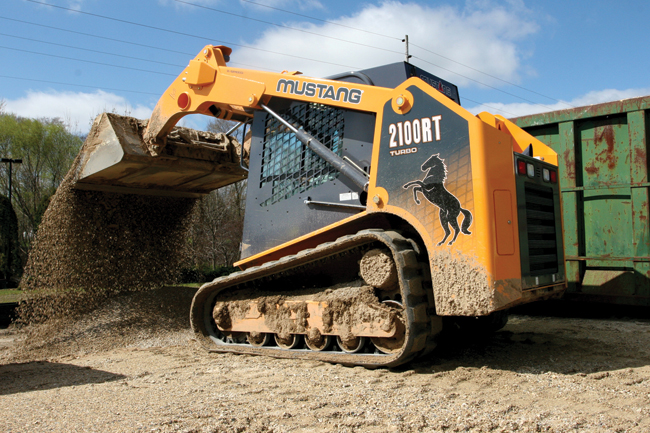
Track tension is very important to extend the life of tracks and the rolling elements of the undercarriage. In fact improper track maintenance may be the single largest contributor of premature wear and failure of tracks and components, especially if tracks are over-tightened to delay normal adjustments. Over-tightening the tracks also robs horsepower and increases likelihood of damage to tracks during machine operation. Normally this maintenance is so frequent and labor intensive that Gehl RT Series track loaders feature the industry-exclusive HydraTrac Automatic Track Tensioning system. This system uses hydraulic pilot pressure to optimize tension on the track during machine use. This system assures efficient transmission of horsepower to the tracks and optimized life of tracks and rolling elements.
The system also releases track tension when the machine is shut down, taking stress off tracks and providing visual confirmation the system is working. Other track tensioning systems generally maintain track tension through a series of large springs and a grease-filled cylinder. This is effective, but requires daily checking and manual adjusting of the track tension. The procedure to check and adjust the track is detailed in the operator’s manual. Taking a few minutes each day to check the track tension will extend the life of the track.
The tracks ride on a set of steel or plastic rollers. Regardless of the material, the roller must be free to turn. As discussed earlier, a track loader is uniquely qualified to operate in soft, muddy conditions. However, this mud builds up and can eventually dry and lock up rollers. If the rollers are not free to turn, flat spots will wear on them. This will not only damage the roller and make them ride rough, but it will also eventually destroy the track. Debris and mud should be washed out of the track on a daily basis to ensure the rollers are free to do what they are designed to do — roll and carry the loader on the tracks.
In addition, watch the rollers for excessive grease or oil leakage. If oil or grease is present on the roller, it indicates a seal or bearing failure is in progress. Correcting it early can save the component and possibly even a track. The track system is driven by a sprocket engaging in the track. The condition of the sprocket can greatly affect the life and adjustment of the track. Sprocket teeth should be inspected on a regular basis for wear. Hooks or pockets on teeth will have a tendency to hook the mandrels that are molded into the track. Worn sprockets will pull the mandrels loose in the track destroying the track assembly. When loaders are operated in abrasive soils or sand, a sprocket can wear much quicker than the track mandrel itself. Replacing a sprocket when worn will increase the life of the track.
Don’t forget to inspect the track on a regular basis. Rubber tracks offer many advantages but can also be damaged by rocks or other objects in the soil. If a rubber track is cut or damaged down to the reinforcement cables, moisture will rust the steel cables that provide the strength to the track. This will lead to broken cables within the track and eventual track failure. To avoid damaging the tracks, keep them properly tensioned at all times and free of debris as much as possible.
Overall, track loaders offer many operating advantages over wheeled loaders depending on soil conditions and allowing improved productivity. In fact, track loaders remain productive when select soil conditions make wheeled machines useless. But as with any machine, they must be maintained properly. A little extra time spent on them each day before they are operated will increase their productivity and ensure they are operating when they should be.
Mike Jerred is a Gehl technical services manager, based in West Bend, Wis.