Excavator Upkeep
When it comes to construction, excavators are often one of the first machines to hit the jobsite. While compact excavators are commonly thought of as “big shovels,” contractors can use them in countless ways during the site preparation and construction processes. Compact excavators can carve out trenches for irrigation, water, sewer and natural gas lines. They can demolish structures and clear vegetation at one stage of a project, then lift and place construction materials during another.
“Attachments make excavators even more versatile,” says Lee Rahn, heavy product line technical services expert at JCB’s North American headquarters in Savannah, Ga. “Outfitting an excavator with a hammer allows contractors to break up existing concrete during road, parking lot or building demolition. Grapples make it possible to grab long, heavy sections of sewer pipes and culverts, and plate compactors flatten and stabilize the earth before foundations or roadway surfaces are poured.”
There’s virtually no limit to the work excavators can do; however, like any machine, they must be well-maintained for optimum performance. These machines are expected to perform difficult tasks under near-constant exposure to the elements. “A properly maintained excavator leads to less downtime and more productivity,” Rahn says. “That’s why any equipment owner should understand basic maintenance and its importance over the long run.”
Getting Down and Dirty
Operating conditions have a significant effect on compact excavator maintenance. Dust levels, outdoor temperatures and soil conditions all affect the machine’s performance, as well as the types and frequency of the maintenance required to keep it in top working condition.
According to Rahn, if the worksite is extremely dusty — a particularly common occurrence during demolition applications — the machine’s air filters will need to be serviced more frequently. If these filters are clogged, the restricted air flow can increase fuel consumption and cause excessive internal engine wear, potentially reducing the engine’s life. It’s also imperative to service cab and HVAC filters in dusty conditions or operators will be subjected to poor air quality and diminished heater and air conditioner performance.
While temperatures inside the cab certainly impact operator comfort, extremely hot and cold temps outside can take a serious toll on excavator engines. “It’s very important to refer to your machine’s owner’s manual to verify that you’re using the correct viscosity of oil for the ambient temperature,” Rahn explains. “Hot conditions require a higher viscosity while colder temps require a lower viscosity. When you use the wrong oil, it cannot keep components properly cooled and lubricated.”
Another concern in very cold conditions — defined by Rahn as temperatures lower than 20 F — is the formation of wax crystals in No. 2 diesel fuel. These crystals can restrict oil flow in the lines and filters, adversely affecting engine performance. Rahn says that’s why it’s important to use the proper fuel and additives to reduce the risk of wax crystal formation when using your excavator under cold conditions.
The type of soil present at a worksite can create another maintenance issue. Soils with a stickier consistency, like clay, can pack into the excavator’s undercarriage and tighten the tracks. When tracks are too tight, they can stall, increasing wear on the undercarriage’s components. While a simple power-washing can remove the built-up soil, that’s not necessarily practical while on the jobsite. Rahn says that in this situation, operators can use the excavator to lift one track off the ground at a time.
“Operate the track that is off the ground both in the forward and reverse direction,” Rahn explains. “This will help clear the packed soil. When one track is cleared, do the same thing on the other. The amount of time you manipulate the track depends on how packed it is and the type of soil present on the site.”
Staying on Schedule
While operating conditions can create the need for special maintenance, it’s important for contractors to stay on top of regularly scheduled maintenance, like checking engine oil, hydraulic oil and coolant levels every day. They should also walk around their machine before each use to inspect for damage or leaks that may have occurred since it was last used.
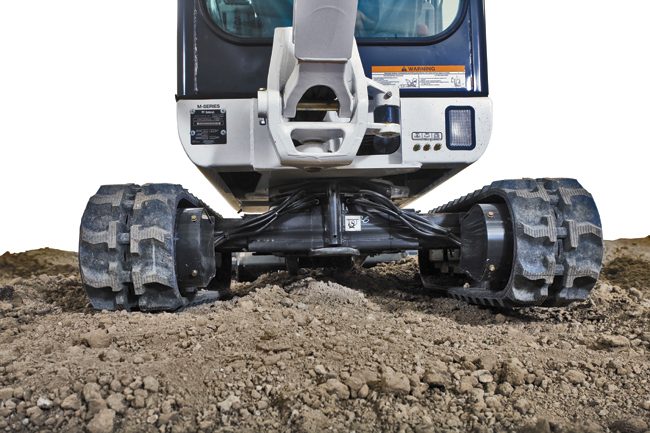
“Daily checks ensure that problems are discovered quickly, before they become major issues,” Rahn says. “However, other regularly scheduled maintenance is also important — activities like changing the engine oil and filter and checking belt tension as often as your excavator’s manufacturer recommends. At JCB, we tell contractors to base their level of maintenance on the total number of hours the excavator has on it and the amount of time since its last service.”
While it may seem like a no-brainer, some contractors don’t follow the service schedule outlined in their owner’s manuals — and that’s a recipe for trouble. In some cases, they may simply be unaware that it’s time for certain maintenance. Or they may perceive the costs of parts and labor required to perform the maintenance as outweighing the eventual benefit. And, of course, there’s that one priceless item we all wish we had more of — time.
“Contractors often get so busy or understaffed that they skip daily checks or other maintenance thinking they’ll do it the next day,” Rahn explains. “Then, a day turns into a week and a week turns into a month. We see this scenario a lot when it comes to greasing an excavator’s pivot points. Eventually, the contractor ends up with a large repair bill to replace all the worn components.”
Calling in the Experts
While many contractors are able to perform much of the maintenance on their excavators, JCB’s Rahn says that there are some processes that require specific training, like adjusting engine valves. That’s when it’s time to go to the experts. “Dealer technicians are trained to work on this equipment, and they may notice problems that operators and owners do not,” he says. “Recognizing a necessary repair and getting it fixed in the right way can save contractors a lot of money over the long run.”
Because engine and hydraulic fluids are so vital to an excavator’s overall health, some manufacturers offer special programs designed to analyze these fluids as a way to track a machine’s level of internal wear. JCB offers a Fluid Analysis Program specifically for this purpose. “Obviously, a visual inspection is not always a practical way to evaluate internal components,” Rahn says. “That’s where our program comes in.”
As a machine’s internal components break down, residue from those components mixes with the hydraulic and engine fluids. Owners take a small sample of those fluids and send them to a pre-designated laboratory for analysis. The lab then generates a report that indicates the amount of component residue found within the fluids and indicates whether those amounts are within specified guidelines. The report also shows the overall condition of the fluids.
“Owners who have their engine and hydraulic fluids analyzed on a regular basis are able to see a trend,” Rahn says. “When a report comes back with an unexpected increase in the level of component wear materials present within the fluids, the owner can use that information to help plan repairs instead of having a machine go down in the middle of a job.”
The Bottom Line
An excavator that’s been poorly maintained or neglected generally often requires extensive repairs, or worse yet, meets an untimely demise. Perhaps even worse, contractors must then cope with unexpected downtime and lost productivity, both of which can cause projects to fall behind schedule.
“Making sure your equipment is regularly maintained — either by you or your dealer — is simply good common sense,” Rahn says. “When you add up the possible costs of machine repair, downtime and lost productivity, skipping or skimping on maintenance can be a costly mistake that can impact a contractor’s reputation for years to come.”
Lynette Von Minden is a public relations writer with Swanson Russell, based in Lincoln, Neb.
Staying on Track
Tracking Wear on a Compact Excavator’s Dedicated Track Undercarriage
By Christina Schave
Compact excavators are often workhorses on jobsites, spending the day digging trenches or picking and placing materials. In these applications, or even in more demanding work, such as demolition, the excavator has the advantage of sitting in one place, letting the swing of the machine’s house and movement of the boom and arm do the work. But even though the excavator is not moving back and forth across the jobsite like a skid steer or compact track loader, tracking the wear on the undercarriage is still a critical part of any maintenance plan.
“Compact excavator undercarriages don’t see the same duty cycle as that of a compact track loader,” says Tom Connor, Bobcat excavator product specialist. “However, tracking wear is still important, as an improperly tensioned track or worn sprocket could cause additional problems and additional costs for a contractor.”
Tracking Tracks
A good plan to track the wear on a machine’s undercarriage starts with a daily visual inspection of the tracks. Connor says depending on the applications the machine is used in, tracks may need to be replaced due to old age before other reasons. However, damage to tracks can still happen and a daily inspection will help prevent failure of a track. The operator of the machine should do a walk-around of the machine each day before starting work. When examining the track, the operator should look for cuts or tears on the track or any place where the steel imbeds are showing. Any of these could lead to moisture or contamination getting in the track, which in turn accelerates the chance for a failure and downtime on the jobsite.
Another important item to check is track tensioning. Connor says the tracks should be tensioned correctly, not too tight and not too loose. Referring to the operation and maintenance manual will help keep the tracks in the right tension range. “Running too tight can suck up power on the machine,” Connor says, “while running too loose could lead to a track being thrown when the machine twists and turns in loose materials such as pea rock. That is hard on the track as it puts an enormous force on it that it is not necessarily designed for.”
Undercarriage Components
While other undercarriage components may not need a daily inspection like tracks, regular monitoring of the components can help identify potential problems early. Idlers, rollers and sprockets are all components that should be checked. Connor says that it can be hard to see normal wear on the idlers and rollers, which may need to be measured. However, since the idlers and rollers are permanently sealed and lubricated, a sure sign to look for is fluid or moisture leaking around the seal, indicating a failure. In this case, the preventative maintenance for the machine is to replace the damaged roller or idler, as they are not serviceable at that point.
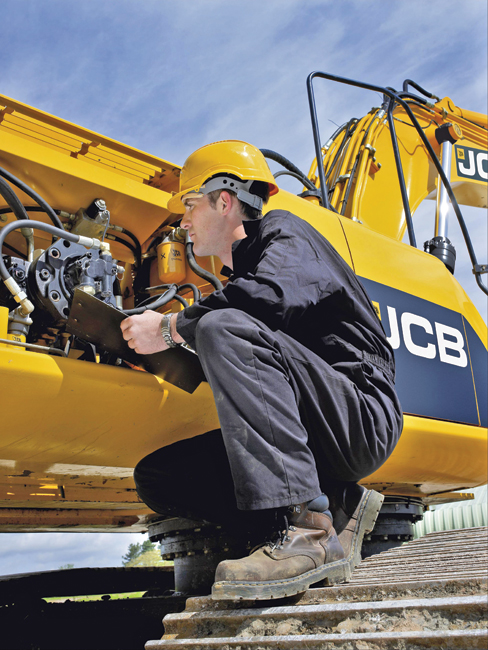
While accelerated wear on the sprocket is not common, it should still be checked periodically. To check the wear on a sprocket, look at the teeth. A good sprocket tooth has a rounded end, while a worn tooth is more pointed. This is especially important to check when putting a new set of tracks on the machines. “You don’t want to put a new track on a bad sprocket because it will accelerate the wear of the steel imbeds in the new track,” Connor says.
Whether it’s being used as a trenching and excavating application, or to demolish and move concrete, a compact excavator has the same risks of any tracked machine. However, a routine inspection schedule can help identify issues early and prevent extra downtime or damage to the machine.
Christina Schave is a technical writer with Two Rivers Marketing, based in Des Moines, Iowa.