A Complete Guide to Renting or Buying a Skid Steer or Track Loader in 2024
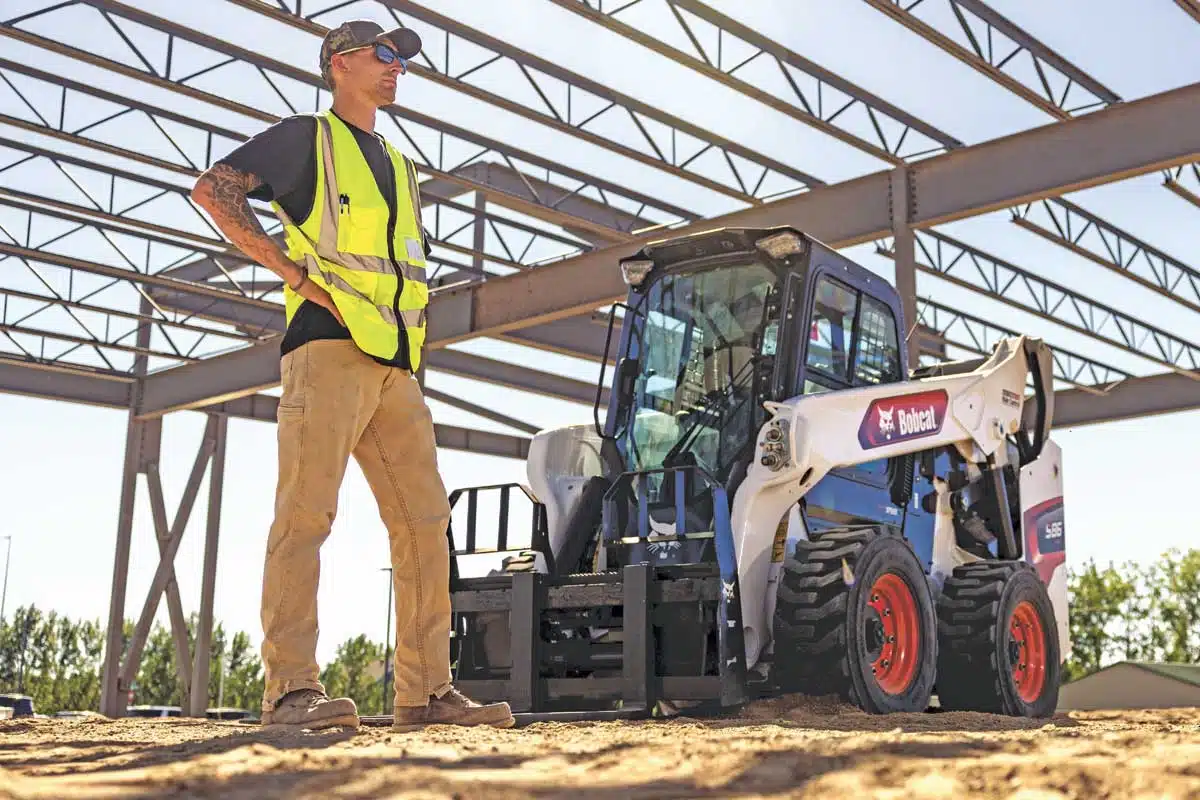
Americans love skid steers and compact track loaders. Last year, the combination of the two categories of off-highway machinery accounted for something like 120,000 units sold in 2023. Compact track loaders specifically are the hottest selling piece of construction machinery on dealer and rental lots these days. There are more than 15 brands selling skid steers and track loaders in America today, including ASV, Bobcat, Case Construction Equipment, Caterpillar, First Green Industries, Gehl, Hyundai, JCB, John Deere, Kioti, Kubota, Liugong, Manitou, New Holland, Takeuchi, Wacker Neuson and Yanmar. New players like Develon are also teasing entry in the market in 2024.
The sheer amount of product is intimidating. The Bobcat brand alone offers 11 different skid steers and 11 different compact track loader models. Hundreds of different mechanical and hydraulic attachments can be fitted onto each model’s universal attachment plate — brooms, buckets, breakers, blades, backhoes and beyond. These units can be optioned out with tons of cool technology (grade control, high-flow hydraulics, telematics and automation from ride control to creep control) and loads of luxury items (cab, HVAC, digital display, heated seat, rearview camera, Bluetooth radio and beyond). When it comes to buying or renting a skid steer or track loader, the real problem is too many options.
What Should You Know?
“That’s why there’s no substitute for knowing your application and tailoring your machine to it,” says Jerry Corder, Kubota product manager, construction equipment. “Do you need a big machine? Will your lift capacity requirements allow you to get away with a smaller one? What attachments will you be using? Will you need high flow to operate them? If you are transporting from site to site, what are your truck, trailer and license limitations? What are the available financing/leasing programs from the manufacturer? What is the resale reputation of a given brand? Even down to what do you know about the dealer? We all know that not all manufacturers are the same, but likewise not all dealers are the same. Service, warranty and training support are at least as important and arguably more important than the initial sales experience.”
There’s a lot to consider, which is why we’ve created this ultimate skid steer/track loader market overview. With the help of 10 different manufacturers, we’ve compiled the most comprehensive overview of the skid steer and track loader markets for 2024. From attachments and engines to automation and maintenance, here’s everything you’ll need to know.
Skid Steers Are on Wheels
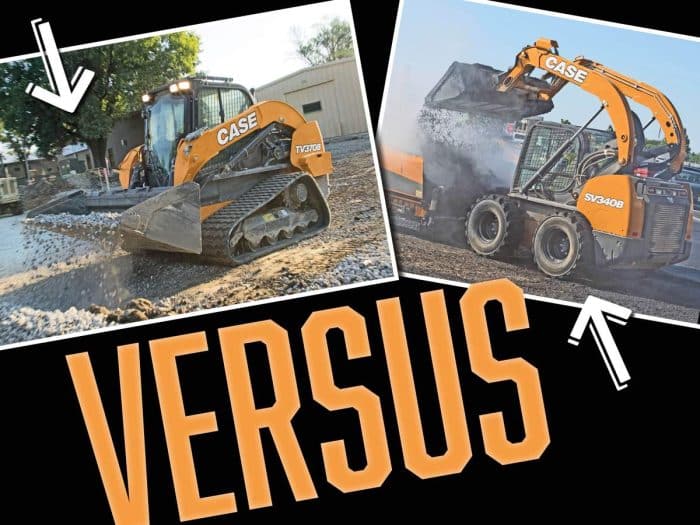
Let’s start off with an easy one. Do you want a skid steer (wheels) or a compact track loader (tracks)? Skid steers excel in applications that will involve traveling on hard surfaces like concrete, and they have higher ground speeds. A skid steer loader weighs less than a comparably sized track loader, allowing for more flexibility in transport. They are often preferred in applications because of their high cycle times and higher ground pressure.
“Skid steers are typically used more in paved and gravel areas for materials handling, demolition and snow removal,” says Lee Padgett, product manager, Takeuchi-US. “Skid steers can definitely move more quickly across larger worksites.”
Compact Track Loaders Are on Tracks
Compact track loaders look just like skid steers, using the exact same universal attachment system). But, they are engineered with a dedicated rubber track undercarriage. Steel tracks are available, but not many manufacturers offer the option. Compact track loaders or CTLs can navigate jobsites with more flotation and less ground pressure than wheels. That means CTLs work great in muddy and wet conditions and also leave a lighter footprint on delicate surfaces (as long as you’re operating correctly).
“Landscape and construction customers may gravitate toward compact track loaders for their ability for site prep, dirt work and material movement,” explains Julie Portillo, Bobcat marketing manager. “Compact track loaders can manage heavy loads with ease and help increase operator efficiency on the job. That’s thanks to the variety of attachments on the market and the dedicated undercarriage for added traction, which is great for grading work. These units also have a lighter footprint, resulting in less compaction of turf, soil, sand and gravel. They are better suited for slopes and slippery terrain. They are also great choices where large, heavy material handling is needed — like rocks or aggregate.”
Tracks vs. Skids when It Comes to Price
The pricing for a skid steer vs. track loader is becoming less of a factor in the decision-making process.
“There’s still a little more cost associated with the initial purchase of a track machine. I also think that gap is closing,” says Lee Tice, product specialist, material handing products, with JCB. “The price of tracks are definitely coming down as track machines become more popular. That was kind of the big thing years ago. Tracks were so expensive, and wheels were cheap to replace. Now that cost is coming closer together.”
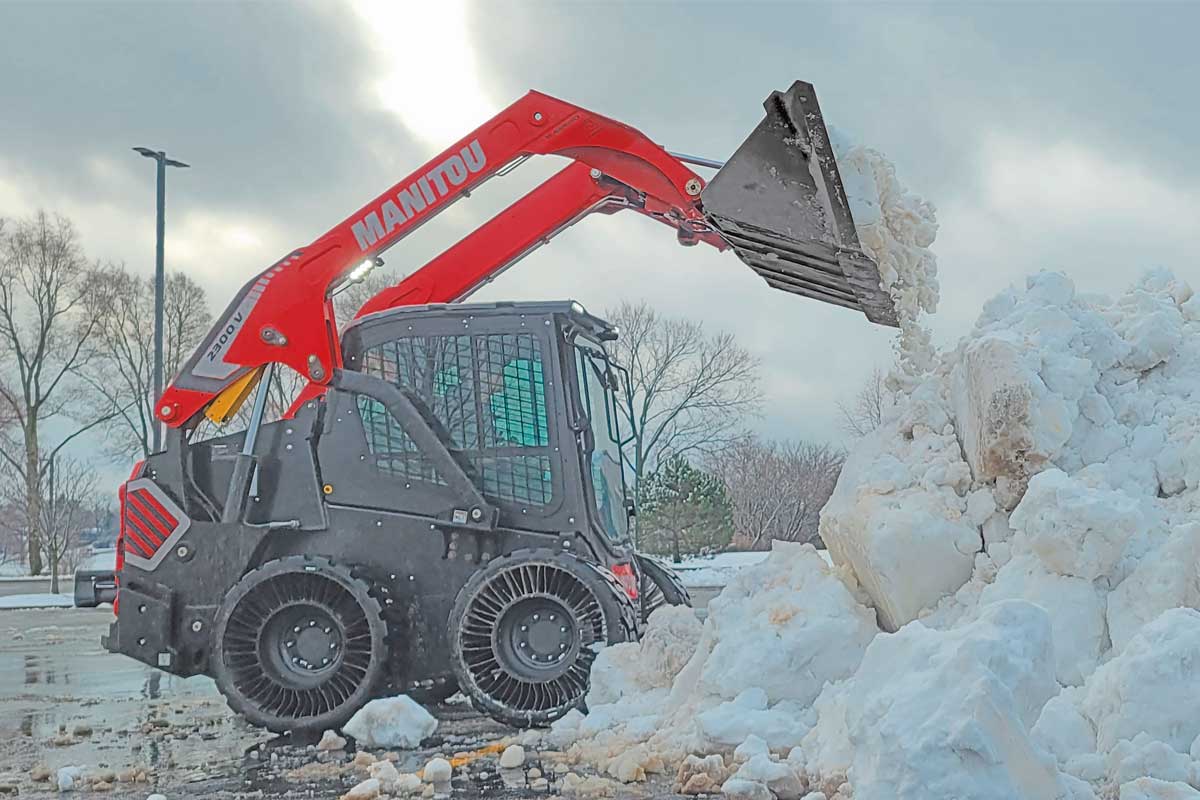
Maintenance on Skid Steers vs. Track Loaders
In terms of maintenance, a skid steer and compact track loaders require virtually the same commitment to upkeep. The only difference being tires vs. tracks. Skid steers will require checking the tire pressure and dealing with punctures. Track loaders will require checking the track tension, cleaning out the undercarriage and monitoring undercarriage components (from idlers to sprockets).
“Market use for skid steers and compact track loaders can be regionally dependent,” says Nathan Ryan, product line manager for skid steers and track loaders at Manitou and Gehl. “Here in North America, skid steers remain strong in agriculture and road work. Track loaders seem to be dominant in most other applications. I’ll note we are seeing an encroachment of compact track loaders into hard surface work.”
How Many Units Are Sold a Year?
The advantages of compact track loaders are growing on pros. Part of this trend comes from track loaders moving into markets a skid steer just can’t go. For instance, brush cutting and grade control are two emerging markets where wheels just don’t work as well. Because of all these factors, track loaders have greatly outpaced skid steers sales over the last year few years.
“Some sources state that approximately 93,000 compact track loaders were sold worldwide in 2022, compared with 30,000 skid steers,” says Padgett. “It’s hard to say how many will be sold in 2023 due to ongoing component shortages and shipping issues. Those challenges are diminishing. I would be surprised if we didn’t see a steady increase in track loader sales in 2024.”
Electric Skid Steers and Track Loaders
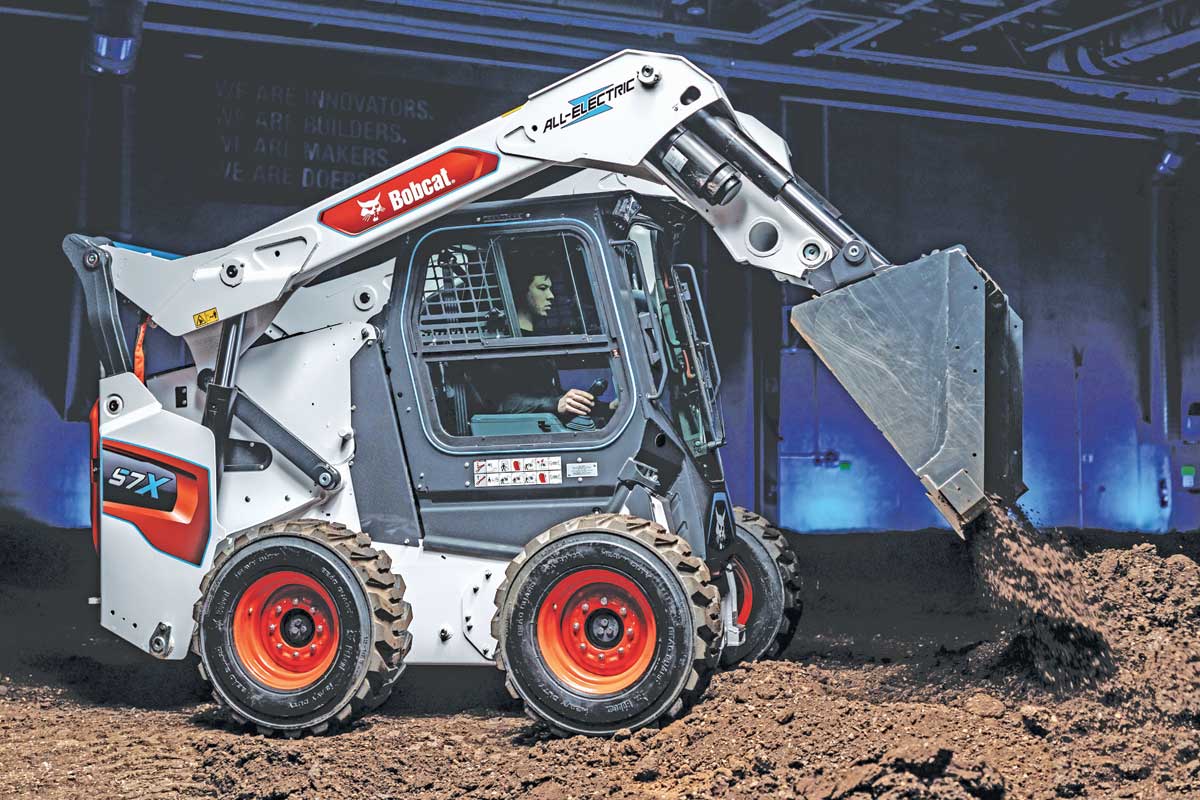
Bobcat launched the world’s-first, all-electric compact track loader at CES in 2022. It later introduced the all-electric S7X skid steer loader in March 2023. With the T7X and S7X all-electric loaders, operators can simultaneously power the drive, lift and tilt functions without the noticeable power lag that is common among diesel/hydraulic machines. Those who have experienced the machines report they can feel a distinct power increase over traditional loaders. There is also no performance trade-offs when operating multiple functions at once. The electric power system of the T7X and S7X takes Bobcat’s reputation for operator comfort to a new level. In addition, the all-electric compact loaders have familiar controls and instrumentation that are consistent with their diesel-powered counterparts. Learn more at bobcat.com.
Skid Steer and Track Loader Sizes and Specifications
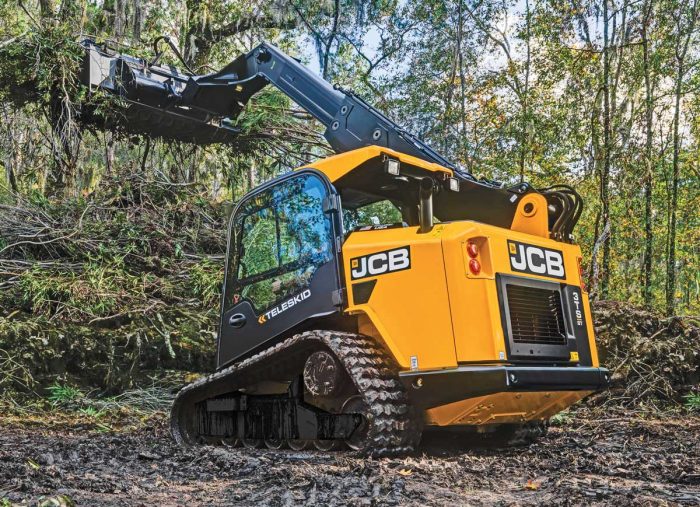
The size and power of skid steers and track loaders can be measured in many different ways. Popular specs on these units include operating weight, rated operating capacity (ROC), lift height, auxiliary hydraulic flow, speed, max reach, breakout force, tipping load and width, height and length. Units are categorized by rated operating capacity. That is the load that the equipment can pick up and operate without flipping or nose-diving.
“When you’re talking skid steers, the most popular size classes are going to be 2,700-lbs rated operating capacity,” says Tice. “Then you get into compact track loaders. You’re going to be looking at larger machines, which are more popular now. So that 3,000 lb and up ROC class.”
Some Spec Examples
Manufacturers offer a wide range of sizes and models. Today, the Caterpillar brand offers eight models of skid steers. Cat’s smallest 226D3 skid steer has a 1,550-lb rated operating capacity, 5,849-lb operating weight, 67.1-hp (gross) diesel engine, 110.9-in. max lift height (measured at the bucket pin), travel speed of 7.6 or 11.1 mph (one- vs. two-speed option) and max auxiliary hydraulic flow ranging from 18 to 26 gpm (standard vs. high flow) at 3,336 psi. Note how auxiliary hydraulic horsepower to the attachment is rated at both gallons per minute (gpm) and pressure (psi).
On the other end of the spectrum, Cat’s big 272D3 XE skid steer loader boasts an 9,573-lb operating weight, 3,700-lb ROC, 110-hp (gross) diesel engine, 128.6-in. max lift height, max travel speeds from 7.2 to 10.3 mph (one- vs. two-speed option) and auxiliary hydraulic flow ranging from 23 gpm at 3,335 psi to 40 gpm at 4,061 (the latter being Cat’s XE hydraulic high-flow option). Why such a big diversity in size and power?
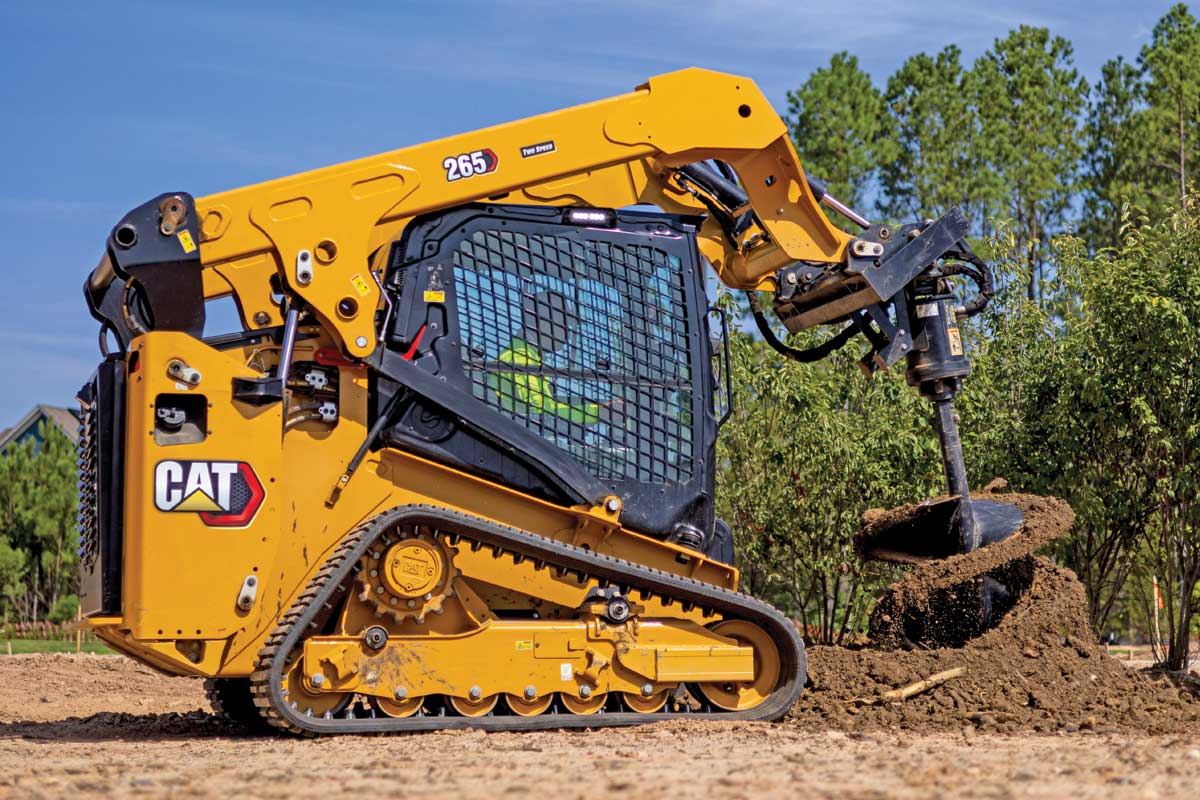
“It’s a matter of aligning a customer’s needs with the correct machine,” says Kevin Coleman, senior product application specialist at Cat.
For reprint and licensing requests for this article, please click here.
Radial Lift
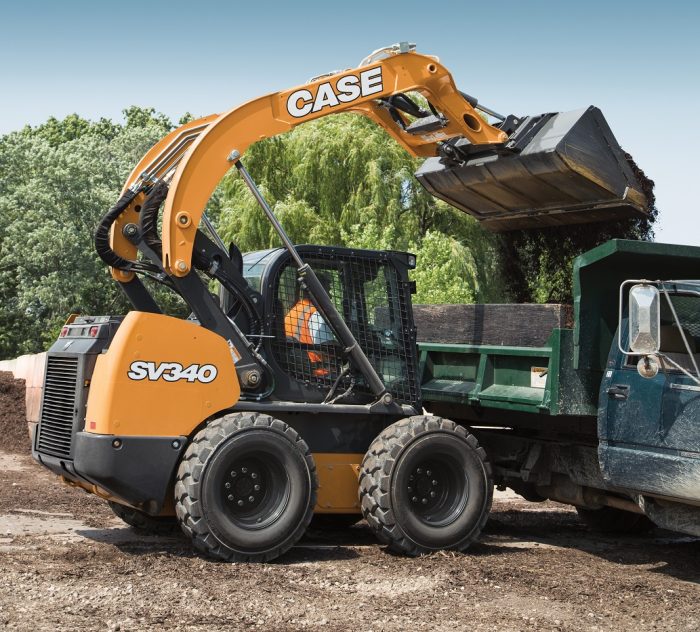
Skid steers and compact track loaders come in two different lift arm configurations. Radial-arm loaders are especially productive in excavating, grading and digging operations. The radial version is the simpler design. As the name implies it follows a curved path as it moves up. With fewer pivot points, the radial design tended to be more durable than the vertical design. Yet, its popularity is waning with manufacturers and customers.
“Radial still has some advantages, including the best reach at the midpoint of the lift range,” says Brad Stemper, North American Case product management. “There is also a lot less linkage to have to grease and maintain on a radial. Though the market trend for the past 10 years is the vertical-lift configuration, I don’t see the radial lift going away entirely. It has distinct advantages it offers in certain applications.”
Vertical Lift
Vertical-lift designs uses two extra links, which allow the boom arms to follow an S curve pattern as it rises. That curve is much closer to the center of gravity of the machine. All lift paths are slightly different between manufacturer. Vertical lift is usually used more to place the load up high on trucks or other targets. Also, pallet work is popular with vertical-lift machines.
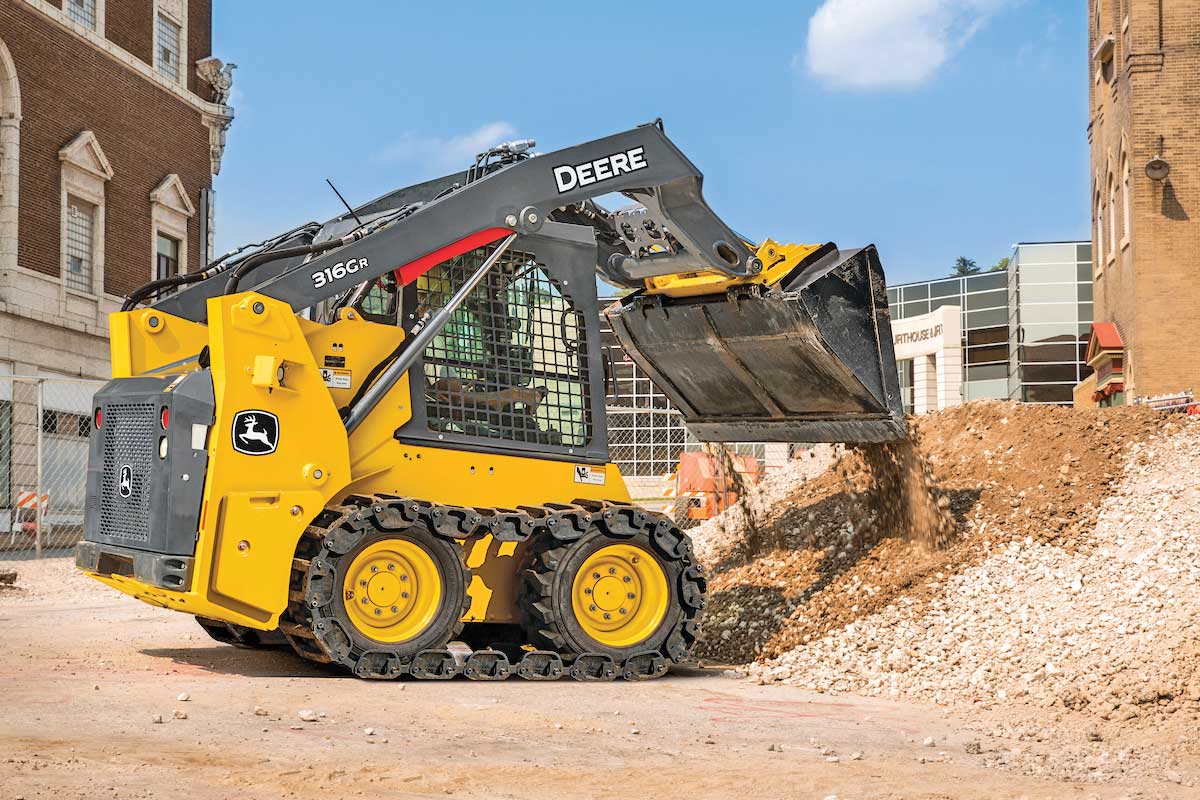
“The vertical-lifting pattern is the most popular. More and more manufacturers are leaning that way — though both vertical and radial have their benefits,” says Corder. “A machine with a vertical lift will have a greater rated lift capacity and a higher useful lift height. Since the loader arms stay close to the machine, rather than swinging out like they do in a radial machine, the center of gravity is always in tight to the unit. Since the bucket is always out in front rather than rotating over the cab of the machine, a vertical machine can make use of that maximum reach at height.”
Models with either design are good. “The type of lift arm really depends on the applications a user is looking to perform. Given the positive attributes and cost advantages I don’t see radials leaving the market anytime soon,” says Ryan.
Cab Environment
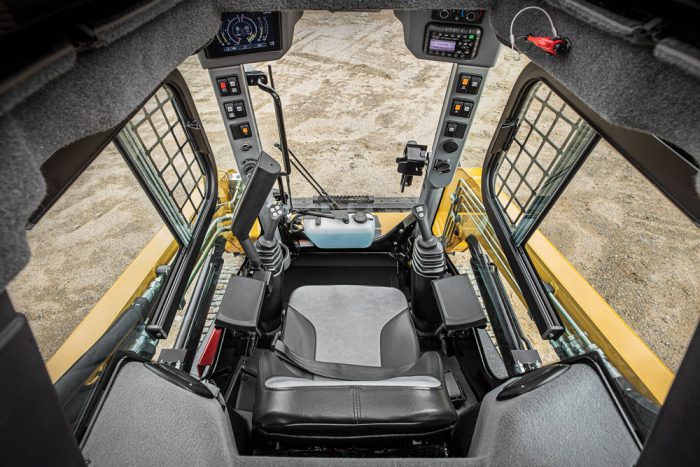
The operator station is the command center for controlling and operating your skid steer or compact track loader. It has become a real focus point for manufacturers over the last several years for a variety of different reasons. One being operators are harder to retain with the labor shortages. A loader can come with a simple, open-air rollover protection system called a ROPS. I can also come with an enclosed cab, noting not all cabs are created equally.
“A comfortable operator is always a more productive operator,” says Coleman. “For maximum comfort, an operator’s office should be somewhere he wants to be. It should also have a comfortable chair, a great view and an ergonomic desk layout. An enclosed cab with a one-piece, sealed and pressurized design is the first step in delivering a comfortable office. This means that the operator’s environment is sealed as a unit and does not rely on sealing by compressing gaskets and foam, as found on the two-piece cab designs offered by some other manufacturers.”
Get into the Cab
Cabs can come with a number of different entry systems, including swing-out doors, rollup doors or foldup doors. JCB even offers a one-armed boom design that allows for side cab entry. These cabs can be decked out with heat and air conditioning, Bluetooth speaker systems and a wide range of tech. LCD and touchscreen digital displays are now the control centers of the most high-tech skid steers and track loaders. Through these sophisticated control panels, operators can access maintenance vitals, automation features, security measures and a variety of languages. A backup camera can be integrated into these digital displays, with multi-camera systems just arriving on the market. Don’t forget about the seat. You could go cheap with a simple cloth sitter or maybe consider that heated air-ride option for those long, cold days in the cab.
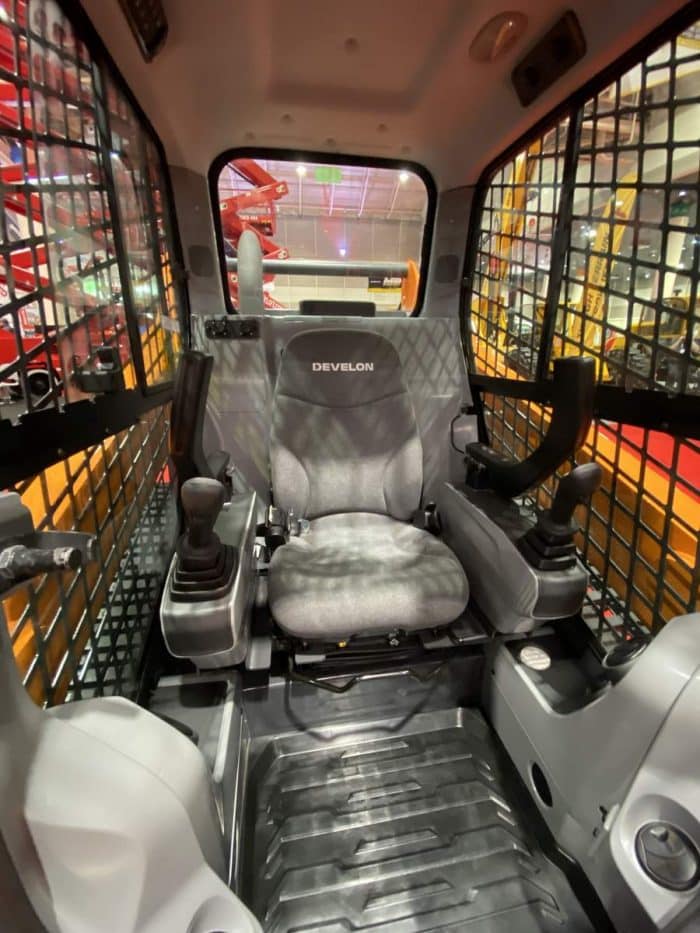
“Do you have room in the cab for yourself and your gear?” asks Corder. “Are you able to sit comfortably in the seat, operating over varying terrain for extended periods of time? Are there other features and options that not only make the experience in the machine more enjoyable — Bluetooth connectivity for example — but also a safer place to work — like a reversing or 360-degree camera or adequate external lighting?”
Lighting for Skid Steers and Track Loaders
Proper lighting increases the safety of your skid steer/track loader operations as well as others on your worksite. Specifically, lighting options that you should discuss include interior or cabin lights, rear work lights and front work lights. Interior lights are affixed inside your cab and provide illumination for the operator. Rear work lights increase the operator’s visibility when moving in reverse and are mounted to the back of your cab. Front work lights mount to the top of your cab and the boom to provide lighting for forward movement as well as for the job at hand.
Control Choices for Skid Steers and Track Loaders
There will also be choices in controls. On skid steers and CTLs, there are three primary types of controls: electrohydraulic and pilot-hydraulic — both of which are available in two operating patterns: H and ISO — and finally mechanical controls. Each manufacturer treats controls differently and calls them different things, but each generally provides some combination of the following: joystick controls and hand and foot controls.
Pilot and EH systems each offer attractive attributes. EH systems allow operators to adjust the response rates and switch patterns, while pilot controls deliver load feedback through the pilot lines and offer simpler problem diagnosis. Kioti just entered the skid steer/track loader market in late 2023, and the company has chosen pilot controls for its first two units (the SL750 and TL750).
“One thing is cost and serviceability,” explains Justin Moe, product manager, construction division, Kioti. “A lot of electrical issues can pop up with electric over hydraulic. You can get some neat features with it, sure, but at the end of today, the market we are playing into and the market we were satisfying with our current tractor customer want an easier servicing machine. Hydraulic pilot controls are really nice for that, but one of the other things too is performance wise you get a little lag with electric over hydraulic, which you don’t get in hydraulic pilot.”
The Pros of EH Controls
John Deere currently offers six skid steer loader models (the 316GR, 318G, 320G, 324G, 330G and 332G models) and four compact track loader models (the 317G, 325G, 331G and 333G machines).
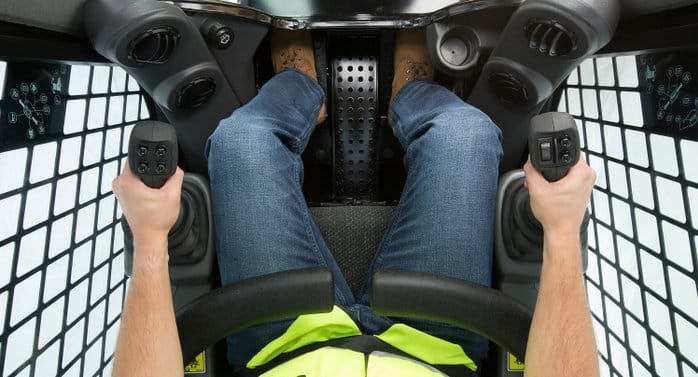
“The full fleet of John Deere compact track loaders and small frame skid steers offer the advantage of electrohydraulic controls, which offer increased functionality to allow operators to customize machine operations based on preference,” says Emily Pagura, solutions marketing manager at John Deere. “EH controls also require less operator effort and are not as fatiguing over longer periods of operation compared to manual linkages. With fewer physical components and maintenance requirements, EH control machines provide operators with increased productivity across a variety of job applications. Adding our EH joystick performance package adds maximum versatility in that it allows the operator to choose between four-way switchable controls [ISO, H-pattern, foot controls and ISO + foot controls].”
Still an option but fading in popularity, hand and foot controls operate much like the H pattern. The drive direction is controlled by pushing the handles forward, back, left and right, but boom lift and bucket functions are controlled with foot pedals.
Grade Control Track Loaders
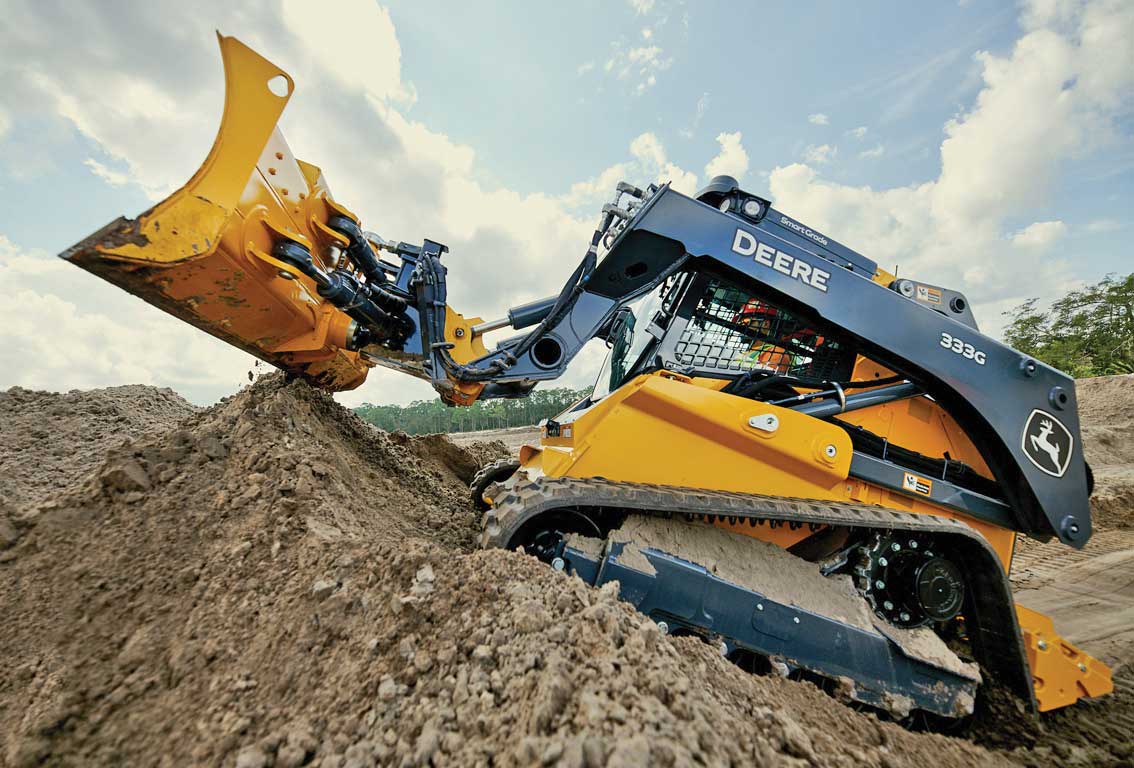
2D and 3D grade control have continued to see increased demand from customers that own and operate skid steers and compact track loaders. To address this, John Deere developed the 333G SmartGrade track loader, a fully integrated SmartGrade CTL that eliminates external masts and cables that enables grading tasks to be completed faster, in fewer passes, and with less rework compared to machines without grade-control technology. The 333G can be optioned out with fully-integrated grade control technology, sweet six-way dozer blade and the ability to spearhead precision dirt work quickly.
Customers that are not ready to take the full dive into full 3D grade control can look to other options like John Deere’s On Board Grade Indicate system the allows the operator to check the cross slope (roll) and mainfall slope (pitch) of the machine from the comfort of the cab. Other third-party options like box blades with laser control can also be effective in helping customers maintain proper grade on their jobsites and are compatible with a range of skid steers and CTLs.
Attachments and Hydraulic Options for Skid Steers and Track Loaders
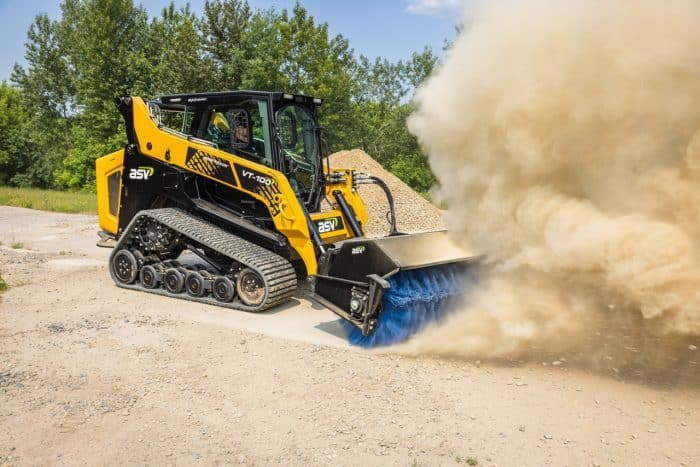
Skid steers and track loaders can utilize a variety of attachments — simple non-hydro mechanical implements like buckets or forks and high-flow tools like planers and brush cutters.
“John Deere offers over 100 attachments, each suited for a particular job,” explains Pagura. “When considering purchasing a new machine, customers should make sure they equip the machine to their existing attachments or for attachments they may choose to purchase in the future.”
Manufacturers of skid steers and compact track loaders have settled on the same attachment style, using a plate and two wedge pins that hold the attachments to the plate. These pins or pawls can be activated manually (operator must leave the seat) or powered (operator can perform the task from the seat).
“Here in North America, land management attachments like drum mulchers, disc mowers and flail mowers continue to gain popularity,” notes Ryan. “Another category of attachments that has benefited from technology improvements are snow removal attachments. Improved hydraulics and mechanical design changes allow for faster more efficient productivity clearing snow.”
Understanding Auxiliary Hydraulics
Each attachment is its own research project, but you can start off by matching a unit’s auxiliary hydraulics to the implement. When someone’s discussing a skid steer’s or track loader’s auxiliary hydraulic system, they are describing the pressurized hydraulic oil that is being used to power the attachment. The main specs are hydraulic pressure (psi) and flow rate (gpm), and units can come with standard- or high-flow auxiliary hydraulic options. Standard-flow skid steers and CTLs ranges between 11 and 30 gpm (3,000 to 3,500 psi), while high-flow units range between 30 and 50 gpm (4,000 to 5,000 psi). Some brands today even offer “super” or “enhanced” auxiliary hydraulics, although these are typically just powerful high-flow machines.
“Hydraulic demands for the new high production attachments are changing,” explains Stemper. “We need not only the power but also the cooling to ensure long component life. Some of our models feature load sensing because of the efficiencies that type of system offers. Case also offers hydraulics on demand so the operator can adjust the flow as the attachment is running to get maximum performance.”
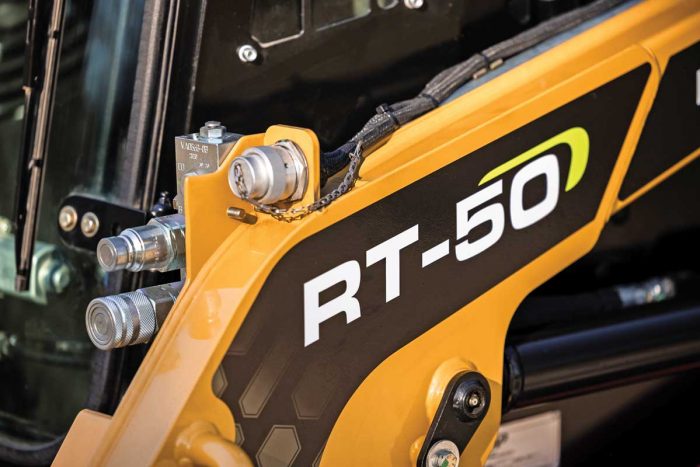
In 2024, John Deere will be launching its biggest skid steer and track loaders yet – the 334 and 335. Deere has noted that the real bulk of the engineering in the 334 and 335 went into the new, more sophisticated hydraulic system. The company’s older 332 and 333G models have open centered hydraulics which run as fast the engine rpms, but the new 334 and 335 feature a pressure compensating load sensing (PCLS) hydraulic system. The system can automatically detect how much load is needed depending on the attachment running. Not only does this provide better, more optimized attachment performance, it also allows the 334 and 335 to be more fuel efficient.
Hydraulics Trends
“Customers are consistently demanding more from their equipment, and skid steers and track loaders are no different,” says Pagura. “As these machines have become larger and more powerful, they are being used for tasks that used to require full-sized construction equipment. That trend drives growth in specialized areas such as high-debris applications that require extra guarding and protection, milling asphalt with a cold planer attachment and even bringing entire small jobsites like parking lots to grade with 2D or 3D grade control technology.”
The hydraulics on a skid steer and compact track loader are a complex, powerful, hardworking system. In fact, it’s so powerful and hardworking that the hydraulic oil (the lifeblood!) can get pretty hot, so hydraulic cooling has become an increasingly important consideration when buying or renting a loader tool carrier. Some brands and third-party manufacturers even offer external hydraulic coolers that can mount on top of a unit to aid in cooling during intense attachment operations like brush cutting and cold planing. Other brands are re-engineering units for aggressive hydraulic apps.
“Some of the key design criteria we’re chasing are things like larger line sizes and larger coolers,” explains Buck Storlie, aftermarket director at ASV and Yanmar. “If you think about 50 gpm of flow, we want to slow it down before we get into that cooler so it can go through there nice and slow and give the fan and the airflow time to exchange that heat. And then of course, large fans to speed up the airflow through that cooling system and hydraulic driven fans.”
Caterpillar Offers Smart Attachments
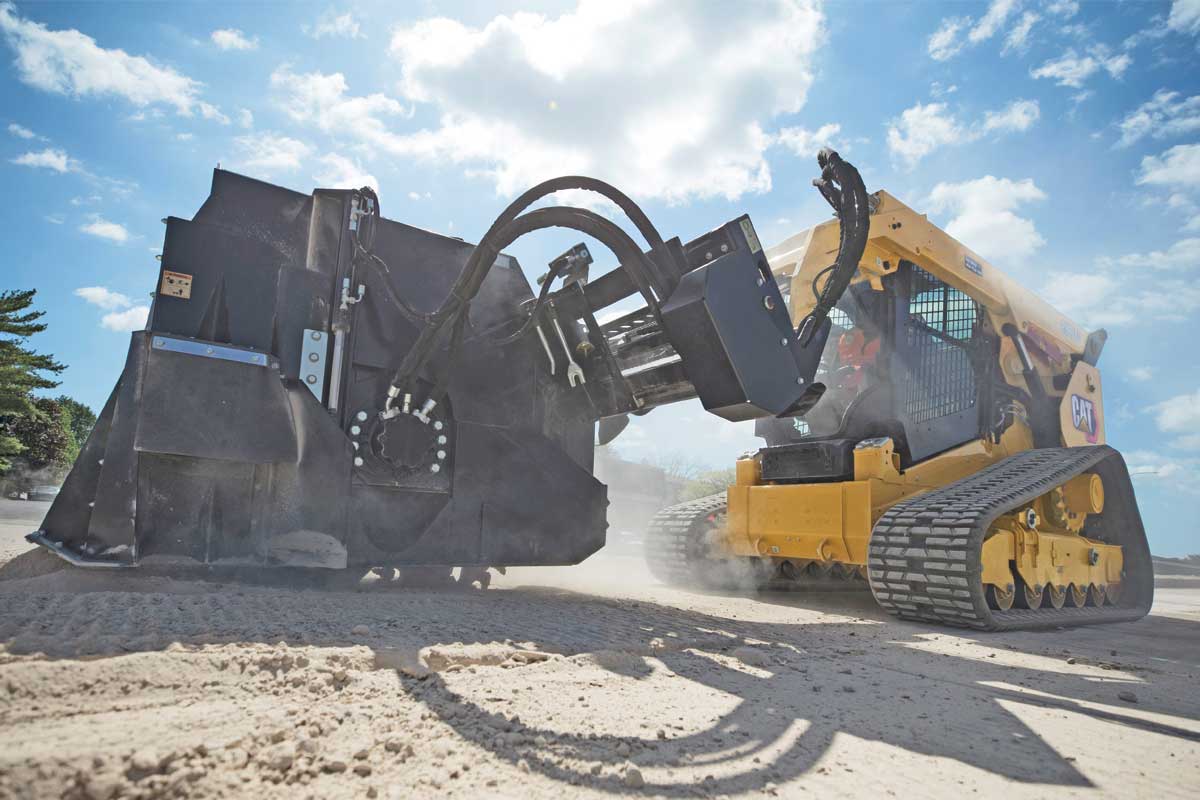
Cat skid steers and compact track loader models support a line of Smart Attachments. This advanced machine technology allows the machine to recognize when one of the Smart Attachments is connected and tailor the controls and operator information to match the recognized attachment and the task at hand. All current Cat models come standard with Smart Technology which delivers the high-level integration between the machine and the Smart Attachments. This integration allows for better machine utilization and a better finished product by delivering easy, intuitive operation of the grading and excavating Smart Attachments. Cat currently offers a Smart Backhoe, Smart Grader with Assist and a Smart Dozer with Assist. The Smart technology also provides additional control and/or information for the operator via special display screens on the in-cab advanced display monitor. For more info, visit cat.com.
Skid Steer and Track Loader Technology
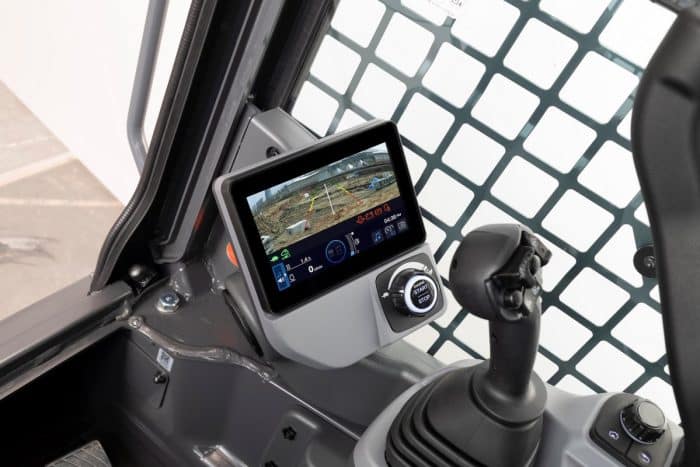
Both skid steers and track loaders have loads of cool tech options — sophisticated digital control panels that allow for attachment and machine automation — routine tasks such as boom settings, attachment speeds, hydraulic flows, wheel speeds, ride control and return-to-dig functions. Telematics systems can be installed to track and log all machine functions, spearhead maintenance schedules and perform security measures like geofencing. Grade control can be utilized on CTLs to perform precision dirt work.
“Kubota has added a new 7-in. touchscreen inside the cab [pictured above] with keyless start,” says Corder. “The monitor relays all machine vitals and serves as the display for the new, wide angle 176-degree backup camera. We have borrowed the advanced multifunction valve from the SVL65-2, which allows for enhanced, simultaneous machine and attachment operation. The auto-downshift feature from Kubota compact excavators has been incorporated as well. This function automatically shifts from high to low range when executing a turn for a smoother ride and maximum available torque when exiting the turn. Another new feature of the SVL75-3 touchscreen is the ability to select one of three track response settings to tailor the ride to the preferences of the operator or to the needs of the site or terrain.”
Common Tech Options
Manufacturers will offer unique technologies (like Kubota’s track response modes) and then common technologies options for customers (ranging from ride control to return to dig). Here’s quick summaries of the more common tech:
A dual self-leveling system can help ensure optimum material retention and control whether loading material into a truck or handling palletized products. A dual self-leveling system uses electronic sensors to monitor the attachment position and automatically adjust the attachment position to remain level whether the operator is lifting or lowering the loader arms.
The creep control function was introduced to systematically operate the skid steer or track loader at a pace matched to the production requirements of the attachment. Whether traveling in reverse to dig a trench or forward to operate a cold planer or road saw, skid steer and track loader operators must often move at slow, controlled speeds to perform the task at hand.
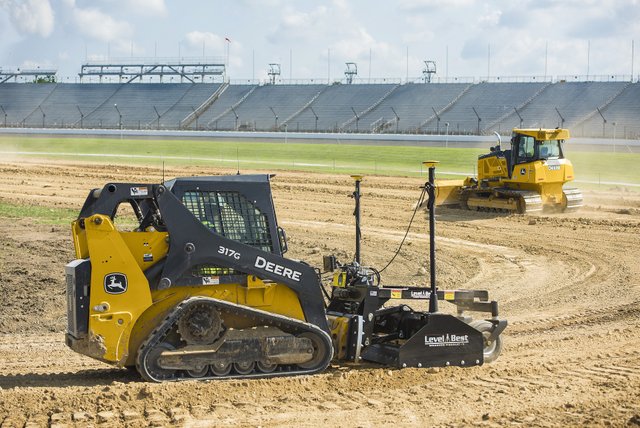
Grade Control, Ride Control and Return to Dig
The terms grade control and machine control are interchangeable. Both terms mean an earthmoving machine is being controlled by technology to produce a desired grade more quickly and accurately than an operator can do. Grade control technologies vary. They may include rotating lasers, sonic tech, satellite GPS or a robotic total station. On the machine, the set up may require masts off the attachment or maybe a new monitor outside the cab. Grade control is divided into two groupings: 2D (two-dimensional) and 3D (three-dimensional). 2D grading is essentially a flat surface that can be perfectly level or tipped in either one or two of its side axis to create a slope. 3D grading builds on the basics of 2D grade elevation, then adds cross-slope calculations to achieve the third dimension.
Ride control is exactly that. The operator gets to set control functions for the ride. It is an on/off function, and there can be a variety of them. One of them is automatic ride control, where if the arm senses pressure, ride control comes on so there is a smoother ride and the volume of spilled materials is reduced. Or, it will allow a faster travel speed and increased productivity.
The return-to-dig feature uses electronics to allow an operator to automate the returning of the loader arms to the lowered position and also return the attachment (bucket) to an operator selected angle for applications such as loading material into a truck. This allows operators to focus on other aspects of the work cycle instead of managing loader functions.
Remote Control
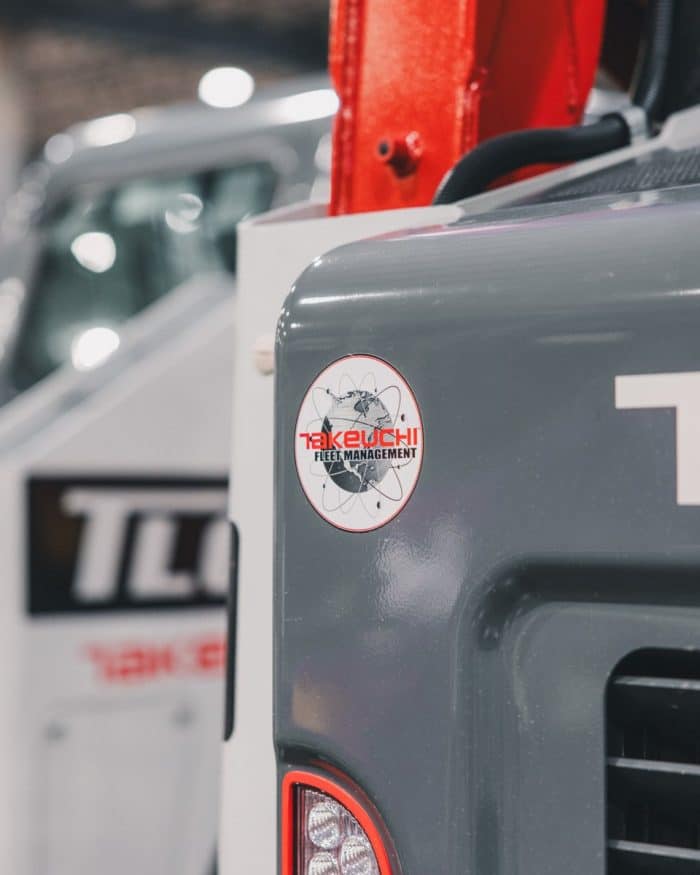
Operator safety and comfort are the primary reasons for the use of remote-control technology on skid steers and track loaders. Think of an application like stevedoring — the loading and unloading of cargo ships — which lends itself to skid steer remote control operations. There are not a lot of these systems on the market today, noting Bobcat and Cat offer them.
Telematics
In broad terms, telematics is the communication of data about your machine. A telematics system receives data transmissions from your loader and makes the information available to you in digestible, meaningful reports. Metrics provided to you through telematics include location, operating hours, machine maintenance history and instant alerts.
The work tool positioner feature is great for any application where a repetitive attachment tilt angle is desired. Think fork operation, trenching, wheel saw cutting/trenching, etc. Using electronic sensors, the operator can select and set the desired working angle of any attachment. The attachment can then be returned to the pre-selected angle with the touch of a button.
Maintenance for Skid Steers and Track Loaders
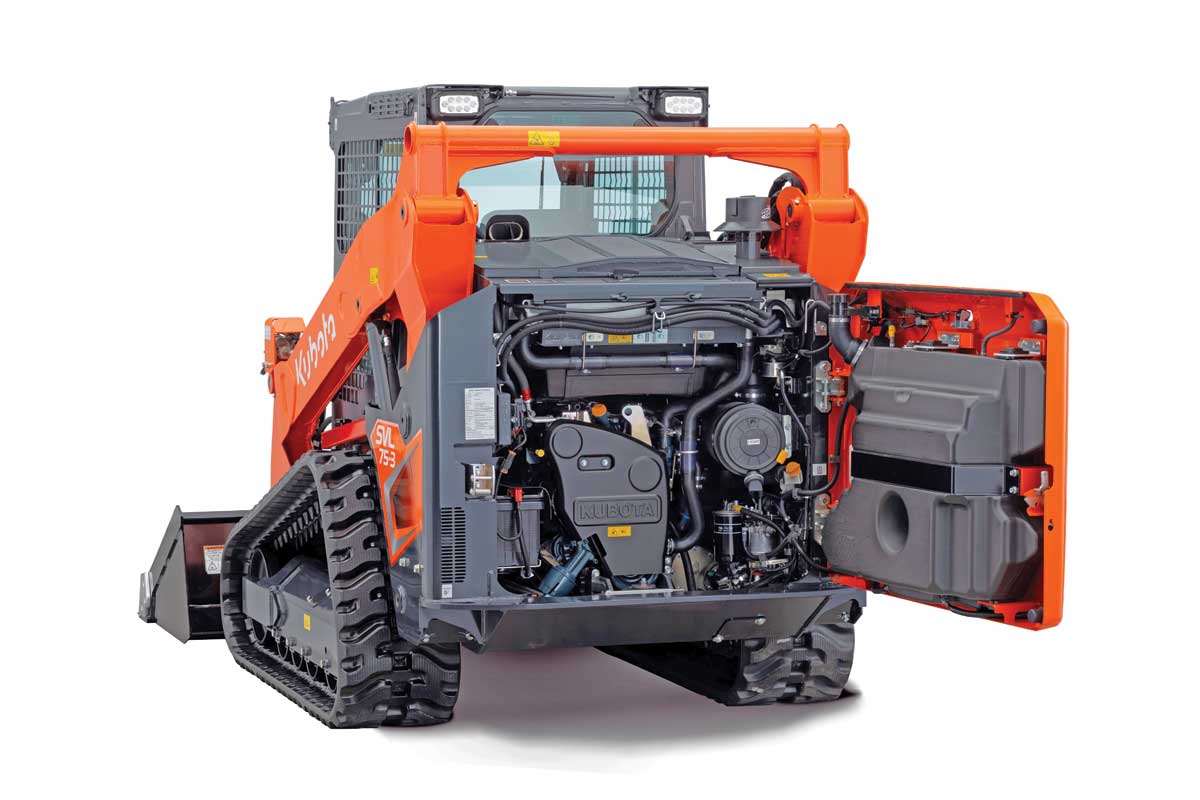
Consider access for daily service and routine maintenance items when buying or renting a skid steer or track loader. Check the operator’s manual for the location of these items and the frequency at which they are to be serviced. Then simulate servicing those items. Daily checks and fill items, such as engine oil, should be easy to accomplish without having to reach into areas where components may be hot. Routine maintenance items, like cleaning and replacing the engine air filter or servicing the fuel filter, should be quick and simple without requiring bolts or panels to be removed.
“I think it’s important to research a machine’s dependability and uptime before making a purchase,” says Padgett. “Contractors use skid steers and track loaders in the pursuit of their livelihoods. They need machines that they can trust to be there when they need them. How difficult or simple is it to perform regular maintenance? If it’s a challenge, you’re less likely to do that maintenance at the recommended intervals.”
Flip-up or tilt-up cabs are becoming more and more popular. This allows owners, operators and mechanics to simply flip up the operator station to easily access all types of drivetrain, electrical and hydraulic componentry.
Engines and Fans
Moving to the engine compartment, diesel engines are the heart of skid steers and compact track loaders. Diesels power the hydraulic system, which is what controls a unit’s force, movement and attachment usage. These are diesel engines ranging from 20 to 130+ hp and above. New machines are now sold with clean and quiet diesels that adhere to EPA-mandated Tier 4 Final engine regulations. They are engineered with aftertreatment technologies that sport names like exhaust gas recirculation (EGR), selective catalytic reduction (SCR), diesel particulate filters (DPFs) and diesel exhaust fluid (DEF). Each manufacturer applies these and other aftertreatment technologies to various power bandwidths, depending on the emissions regulations of each country.
Machines under 75 hp do not typically require the use of DEF. Diesels under 25 hp will not need aftertreatment at all. Today these are electronically-controlled engines, taking skid steers and CTLs to new levels of power, efficiency, automation and connection to the cloud.
To keep things cool, hydraulic reversing fans are made available either as optional or standard equipment. They serve two important rolls: minimizing the amount of material and debris that gathers in and around the engine compartment and ultimately reducing engine compartment temperatures by removing blockages and encouraging greater air flow. When the ambient air temperature is low and cooling requirements are at a minimum, the fan will call for less hydraulic flow to drive it. This in turn saves fuel compared to a fixed drive mechanical fan.
Track Loader Undercarriages
Just remember, the undercarriage on a compact track loader will require extra love. Operators should regularly clean a compact track loader’s undercarriage since its cleanliness directly impacts the wear rate. Contractors should also closely inspect rubber track undercarriages regularly. The average rubber track life is about 2,000 hours but can be as high as 5,000 if maintained well. To get the longest track life, check track tension and condition daily. Then conduct visual checks for damage and lubricate grease points. Then there’s inspecting lugs, sprocket rollers, drive wheels and other extras needed when maintaining a compact track loader.
That’s a Lot, But There’s a Lot More
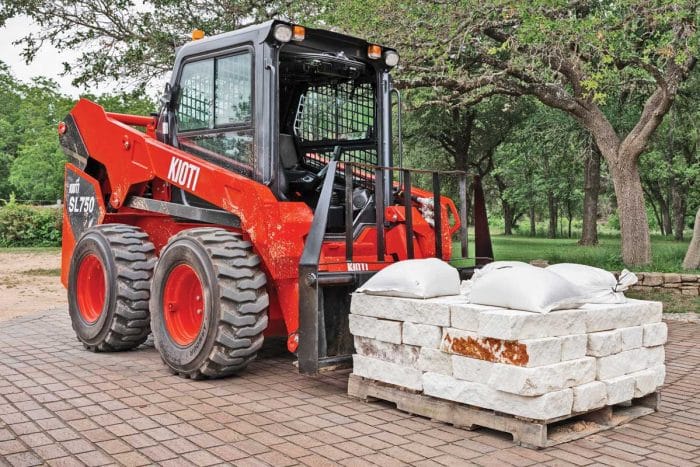
Skid steers and compact track loaders have become sophisticated and powerful machines. This category of construction equipment is engineered as a chameleon. These units have the ability to quickly switch attachments and applications with its advanced hydraulic system and zero-turn maneuverability. More and more technology continues to be integrated into these compact loader tool carriers — attachment automation, remote control, battery power, telematics, backup cameras and ever onward. Even in this 6,000-word article, we’ve been unable to capture everything we’d like to tell you about skids and CTLs. Please visit compactequip.com to enjoy daily coverage of these two categories and all of their attachments.
Keith Gribbins is publisher of Compact Equipment.
Skid Steer/Track Loader Product Line Summaries
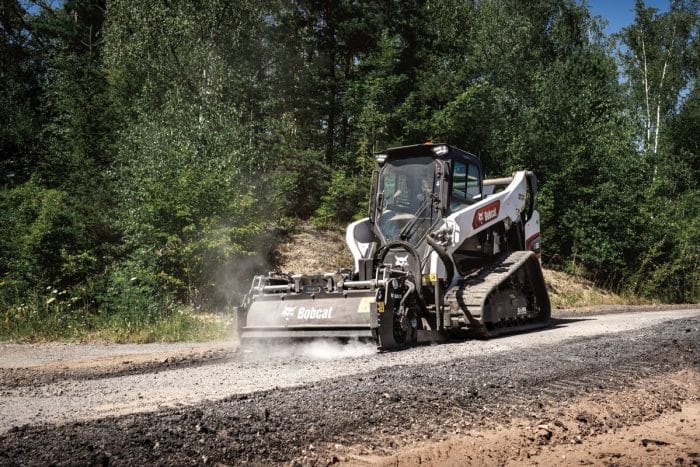
Bobcat
Bobcat actually invented the world’s first skid steer loader way back in 1960. It entered the compact track loader market in 1999. Today, Bobcat offers 11 skid steers and 11 compact track loaders. The latest additions are its most powerful — the S86 skid steer and T86 compact track loader. The latter delivers three hydraulic flow options (standard, high and super flow).
Caterpillar
Cat launched its first skid steers in 1999. After almost 25 years of loader production, Cat has eight models ranging in horsepower from 67 to 110 gross hp. The company just announced its Next Generation track loaders with the 255 and 265 models. These boast big increases in lift/tilt height, engine torque and ROC. Plus, Cat offers Smart Attachments!
Kubota
Kubota launched skid steers in 2015, and today its SSV Series includes the 64-hp SSV65 and the 74-hp SSV75. In 2010, Kubota entered the CTL market, and today offers the SLV Series (the SVL65-2, SVL75-3 and SVL97-2). The SVL75-3, launched in 2023, features big breakout force (6,191 lbs) and lift height (122.7 in.) plus three track modes (mild, normal and quick).
John Deere
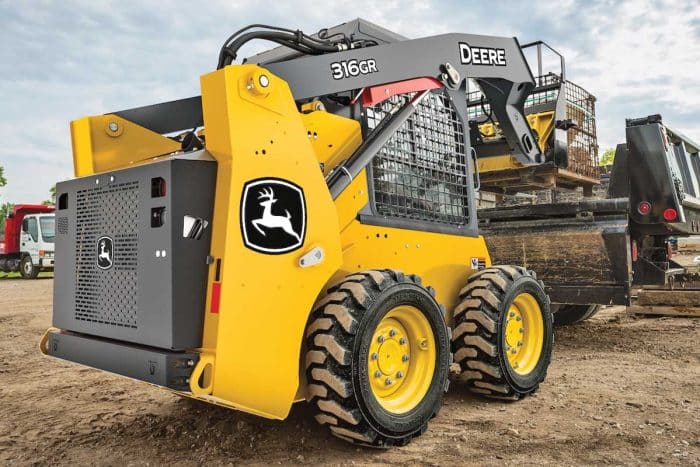
John Deere has been making skid steers for over 50 years. Today, the John Deere lineup consists of six skid steers (the 316GR, 318G, 320G, 324G, 330G and 332G) and four compact track loaders (the 317G, 325G, 331G and 333G). This year, the company will release its biggest, most powerful loaders yet — the 334 P-Tier skid steer and 335 P-Tier track loader.
Case
For more than 50 years, Case has brought practical innovation to the skid steer market. Today, the company also now has one of the strongest track loader lineups in the industry with the new TV620B. With eight skid steer models and six compact track loaders, Case has a solution for contractors in any industry segment.
Takeuchi
Takeuchi built its first compact track loader in the mid-1980s. Today, the company offers five compact track loader models, featuring a unique undercarriage design with model-specific components. Takeuchi track loaders feature spacious operator stations with deluxe, high-back suspension seats. New models include a standard 5.7-in. color monitor and rearview camera.
JCB
In 1993, JCB entered the skid steer market with the first mono-boom, side-entry skid steer. The company added CTLs in 2001. In 2017 JCB launched Teleskid compact track loaders with a telescopic boom, offering greater lift, reach and dig depth. Currently, JCB offers four skid steers and five compact track loaders (two CTLs and one skid steer are Teleskid models).
Kioti
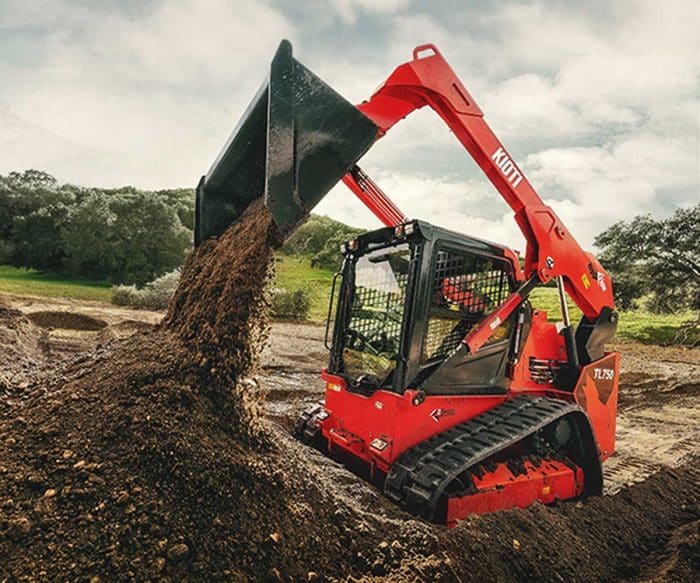
Kioti just entered the market in 2023 with its SL750 skid steer and TL750 compact track loader. Both are vertical-lift machines with a lift height 10.5 ft. Both machines utilize a 74-hp Kioti engine, proven in its RX-Series tractors. When it comes to auxiliary hydraulics, both units sport a standard flow up to 21.9 gpm with pressures up to 3,335 psi.
Yanmar
Yanmar introduced its modern line of compact track loaders to the North American market in 2023. The TL65RS, TL75VS, TL80VS and TL100VS are construction-grade machines featuring the company’s performance, efficiency, technology and reliability standards. Ranging from 67 to 103.5 hp, the new compact track loaders cover a wide range of customer needs.
ASV
ASV is known as the creator of America’s original compact track loader. The ASV brand offers compact track loaders and skid steers primarily for the landscaping, forestry and construction markets. Its product line consists of nine compact track loader models. They range from the smallest sit-in compact track loaders in the industry to the most powerful.
Gehl
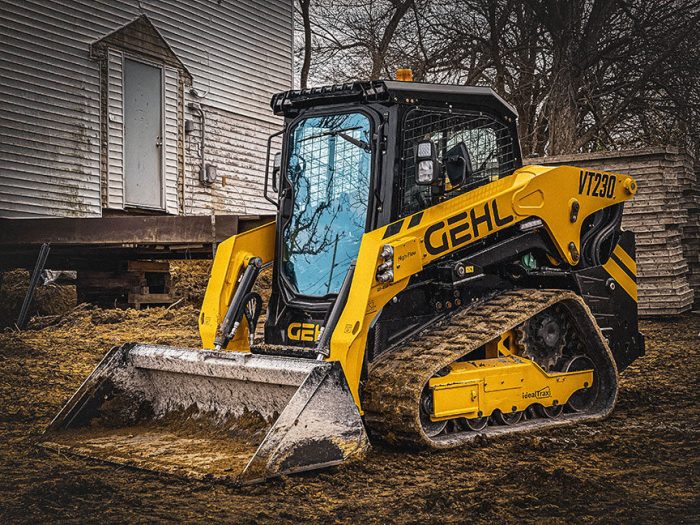
Three all-new Gehl skid steers and three all-new CTLs deliver significant improvements. These include bigger breakout force, run times (larger fuel tank) and an overall improved operator experience. The cabs feature 23 percent more cab volume. That means improved cab sealing, increased foot room and a heated seat option for cold weather environments. Each machine features low-effort, ergonomic controls and a keypad with push-button start.
Manitou
Three all-new Manitou skid steer loaders (the 2100 V, 2300 V and the 2750 V) and three new compact track loaders (the 2100 VT, 2300 VT and 2750 VT) deliver improvements in safety, comfort, productivity, simplicity and serviceability over previous Manitou skid steers and CTLs. All models are vertical lift and feature a new lift arm design meant to improve visibility. The operator experience has also been improved with Manitou’s patented folding door.