Construction Equipment Tire Safety Dos and Don’ts
How Proper Tire Selection, Maintenance and Usage Improves Performance
Tires are crucial assets on the jobsite and are often the unsung heroes during a day’s work. Proper tire care contributes enormously to the overall safety of a construction fleet, and managers should take heed on what constitutes good tire safety practices — and what doesn’t. By eliminating possible tire safety concerns at the onset, business owners keep their jobsites productive and profitable and eliminate unnecessary risks to the operators and their equipment.
DON’T Under-Ply
When selecting a new set of bias tires, managers should match the ply rating to both the equipment and the application. The ply rating measures the strength and the load carrying capacity of bias tires — the higher the ply number, the higher the maximum allowable air pressure and load carrying capacity. If the chosen tire isn’t rated to carry the load, this could cause failure, leading to potential safety hazards. A general rule of thumb is to choose a tire that carries the load with the lowest inflation pressure. After choosing a set of tires, it’s crucial that operators don’t overload the equipment. Not only is this important to maintain tire safety, it prevents damage to the equipment and unstable working conditions.
DO Match Tread Pattern to Ground Conditions
While it might not result in an unsafe situation right away, not matching the appropriate tread pattern to the application could compromise machine stability and operation. Tire overheating, puncturing or tread separation could all occur as the result of an ill-chosen tread pattern for the ground condition and application. Owners should make careful note of the numbers that correspond to tread depth on a tire and what those numbers mean for specific applications:
1 — Denotes rib tread with standard depth for use in earthmoving applications, primarily on roads.
2 — Denotes traction tread with one-to-one lug-to-void ratio and a standard tread depth for use on soft surfaces.
3 — Denotes rock tread with two-to-one lug-to-void ratio and a standard tread depth for use on average hard-surface conditions.
4 — Denotes rock tread with a two-to-one lug-to-void ratio and tread that is appropriate for harsh, rocky conditions.
4S — Denotes smooth tread pattern with no lugs and a tread that is 1.5 times deeper than standard for use on hard surfaces where traction isn’t a concern.
5 — Denotes rock tread with a two-to-one lug-to-void ratio and tread that is 2.5 times deeper than standard for use in L applications in the most severe working conditions.
5S — Denotes smooth tread pattern with no lugs and a tread that is 2.5 times deeper than standard for use in severe working conditions that require wear-resistance over traction.
7 — Denotes rib pattern with a shallow tread that is 60 percent as deep as standard for use in settings where flotation and minimal ground disturbance is required.
DON’T Ignore the Wheels
A set of tires is only as good as the wheel assembly on which it’s safely mounted, and business owners should never be tempted to mix and match components or make a guess if something will fit correctly. Without the proper wheel and components, not only are the wheels and tires put at risk — so is the safety of the operator.
For all safety checks and mounting/dismounting procedures, owners should make sure to adhere to the tire data book provided by the specific tire manufacturer. This will clearly outline the manufacturer’s safety procedures for mounting/dismounting the tires, and how to service the tire and wheel correctly. Some good general guidelines include wearing proper safety gear, replacing any components that appear worn or cracked and never leaving a tire or wheel assembly unsecured.
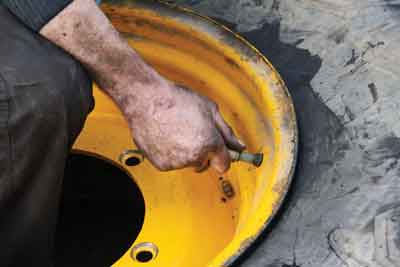
A set of tires is only as good as the wheel assembly on which it’s safely mounted, and business owners should never be tempted to mix and match components.
DO Inflate Your Tires Properly
Proper inflation pressure makes the biggest impact on tire performance and therefore machine performance. One of the biggest misconceptions regarding tire inflation pressure comes from treating all radial or bias tires equally, regardless of manufacturer. For example, Titan Tires are designed with nylon casing, which requires a higher inflation pressure than a comparable tire with a steel carcass. Owners may mistakenly inflate all their tires to the same pressure, and this can cause operability issues and eventually lead to safety concerns.
Owners should also keep in mind that inflation pressure is going to vary throughout the day, so checking inflation pressure in the morning before starting the machine will yield the most accurate measurement. A daily inflation check is ideal, but owners should be sure to check inflation pressure at least once a week, especially if the equipment is working on different jobsites or if ground conditions have changed.
DON’T Ignore Your Operator
There are a number of different operator tendencies that can negatively affect tire longevity, and Titan recommends that owners record everything from average haul distances, peak speeds and cycle times to number of shifts, days worked, cycles completed and type of materials being moved for each piece of equipment. Doing so helps to forecast expected lifespan under ideal conditions and thus identify problems.
Regardless of the tire or equipment, there are some general bad operator behaviors that must be avoided. Things like rapid stops and starts and sharp turns can put unnecessary stress on the casing, leading to premature wear. Excessive speed generates heat, which can degrade the tire. Additionally, it’s important to remember that the heavier the load, the more drastic the impact to the tires will be with all three of these operator tendencies.
For fleets including larger equipment, such as haul trucks, calculating the operators’ ton-mile-per-hour (TMPH) ratings is critical. This rating utilizes a formula to calculate the heat a tire will generate based on the way it is being operated. TMPH is calculated as the average weight of the vehicle multiplied by the average speed of the vehicle. Exceeding the TMPH rating will cause damage to the tire and ultimately pose a safety risk.
DO Implement a Tire Maintenance Program
Adhering to a daily tire maintenance and routine rotation program helps protect the entire machine throughout its life span and prevents safety issues before they happen. Ultimately, successful implementation of a tire management program takes buy-in from both the fleet manager and the operators. It’s important for the fleet manager to train the operators to use the equipment within its limits and to report any changes in inflation pressure or jobsite conditions that could lead to potential problems.
Also, owners should work closely with their tire dealer to solidify long-term success of the maintenance program. As an operation expands, haul distances, speeds, loads, site conditions, cycle times and equipment configurations can all change. Each of these factors necessitates a change to the tire management program, and as such, the fleet manager should work closely with his or her tire dealer for recommendations whenever major changes occur. Owners who adhere to the sound tire safety practices above can help ensure the jobsite stays productive and free of failure or injury, while also maintaining the integrity of their equipment.
Johni Francis is a global product manager for Titan International.