A Comprehensive Guide to Buying or Renting a Compact Excavator in 2023
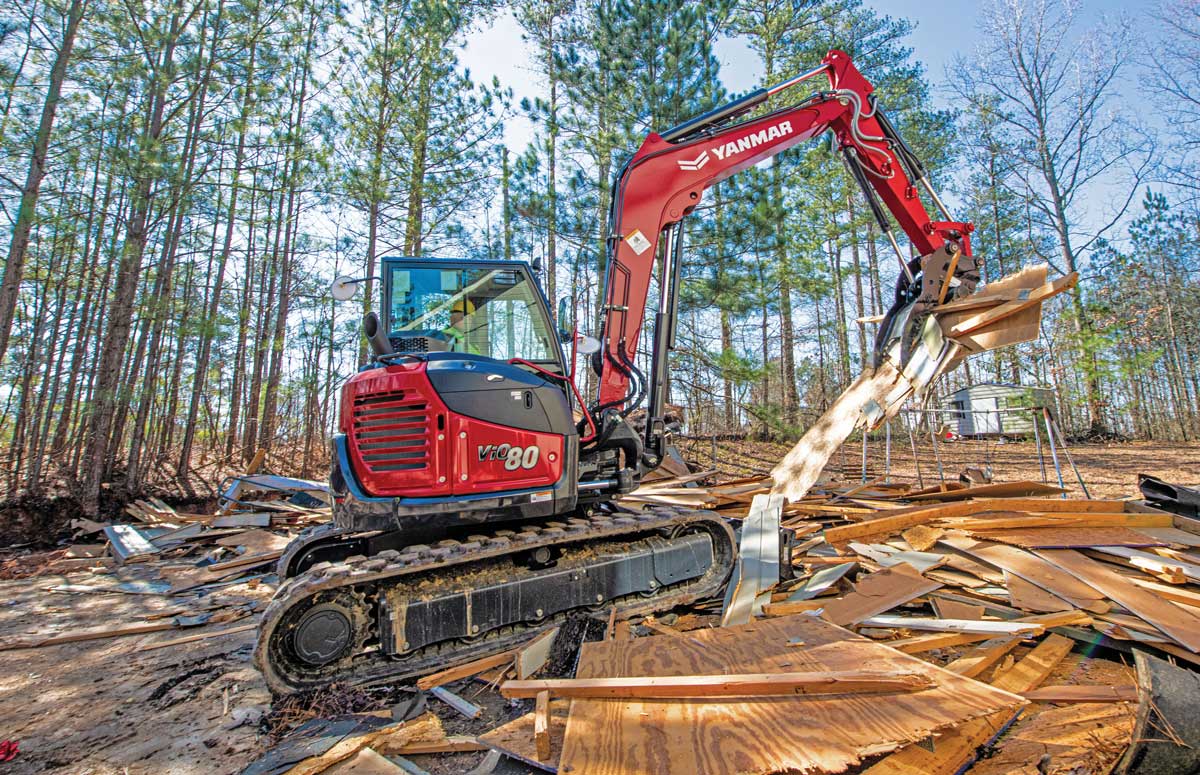
The compact excavator market is busy. Today there are probably 20 brands of mini diggers being sold in the U.S. marketplace, and just one of these (let’s pick Kubota as an example) might offer 13 units with 20+ variants. The sheer amount of brands and models on dealer lots is an impressive indicator of the demand for this category of equipment.
“The compact excavator industry closed off 2022 with 76,189 units, which is 2 percent market growth from 2021, and we expect to have 3 percent growth in 2023 as inventory levels replenish,” says Thomas Lee, director of product management at Develon (formerly Doosan Infracore construction equipment, which just rebranded after its acquisition from Hyundai). “Agriculture, ground maintenance and utilities activity are also showing growth along with inventory growth. We’re expecting growth in the 6- to 10-metric-ton segment whereas the smaller 3- to 5-metric-ton segment will likely decline due to high interest rates which will persist through 2023 and into 2024.”
Mini excavators continue to sell into a variety of channels. “Landscaping and residential building are growing markets,” notes Kei Matsumoto, product manager of compact excavators at Hitachi Construction Machinery Americas. Approximately 30 percent of compact excavators in North America end up in rental fleets. “We believe rental will be up considerably given the catch-up needed to replace aging fleets,” says Wesley Foy, Yanmar Compact Equipment product manager for mini excavators.
Both basic and high-tech units are required in these markets. Compact excavators ending up on rental lots are usually simple, no-frills units built for longevity and ROI. At the same time, contractors are demanding more comfort and sophistication, so manufacturers and aftermarket OEMs are now outfitting mini excavators for higher dimensions of operation — machine control, electric propulsion, tiltrotators, telematics, luxury cabs, wheels and beyond.
Contractors might have choices in tracks, tail swings, cabs/ROPS, attachments, extended booms, expandable undercarriages, coupler systems, hydraulic power and flow, display screens, angle blades, warranties and onward. Then each brand might offer unique technologies, engineering characteristics or standard features. Examples would include Develon compact excavators all come standard with an enclosed cab with heating and air conditioning and Caterpillar offers its unique Stick Steer system.
“It’s an exclusive feature for new Next Generation models,” says Greg Worley, global market professional for 1- to 10-metric-ton excavators at Caterpillar. “Stick Steer allows the operator to switch, with the touch of a button, from conventional lever/foot-pedal steering controls to low-effort joystick control. Automatic two-speed travel is also standard, as is a cruise control system that further simplifies machine travel.”
Almost every manufacturer will offer similarly interesting brand differentiators — and those may indeed be major factors in your final decision — but choosing a compact excavator in general across the board is similar no matter the brand. I’ll show you in this article. It will be the most comprehensive overview of the U.S. mini excavator market in 2023: detailing size and tech trends; describing the manufacturers, popular machines and product differentiators; outlining options and attachments; and dispensing buying and renting advice from 10 experts in the industry (including myself). It should be a great refresher for old pros and the perfect primer for new buyers on the block. Let’s start with…
Specifications and Popular Size Classes
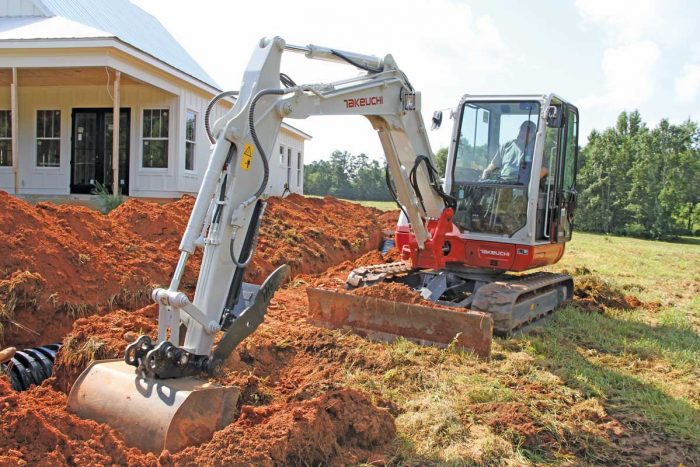
First off, compact excavators and mini excavators are the same thing, and I’ll use those terms interchangeably throughout this article. Compact excavators continue to increase in popularity for a variety of reasons that include size (nimble, easy to transport), versatility (attachments, angle blades) and excellent reach (some units even offer extended booms). Applications range from digging basements and trenching service lines to augering holes for trees and grappling big rocks for landscape projects. The competition is fierce with a metric ton of brands serving the market, including Bobcat, Case, Caterpillar, Develon, Hitachi, Hyundai, Kato, JCB, John Deere, Kobelco, Komatsu, Kubota, Liugong, New Holland, Sany, Takeuchi, Volvo, Wacker Neuson and Yanmar. Here’s just one of these lineups.
“We consider excavators under 10 tons to be compact, and we have 11 internal combustion engine models and three electric models that fit the description,” says Darren Ashton, product manager, compact equipment, with Volvo Construction Equipment. “Eight are short swing models. One is wheeled. They range from 16 to 63 hp in diesel and 16 to 20 kWh in electric.”
For some basic definers overall, compact excavators have dig depths between 5 and 20+ ft, cabs or ROPS operating stations, various tail swing configurations (conventional, reduced and zero), the ability to use attachments (from breakers to buckets) and diesel engines ranging from 13 to 70+ hp (with electric options also now on the market). Most capitalize on rubber track undercarriages that are great for navigating terrain with high flotation and a light footprint, fitting into cramped worksites to A) give precise and powerful dig performance, B) wield attachments like thumbs, grapples and brush cutters or C) offer great reach and dexterity in applications from digging foundations to brush cutting around bodies of water.
Questions to Ask When Considering a New Mini Excavator or Renting a Machine
- How deep do I need to dig?
- How far do I need to reach?
- What size limitations, if any, do I have for my jobsites?
- How much auxiliary hydraulic flow do I need for attachments?
- What does the mini excavator weigh, and will I need a bigger trailer if I want to transport it with attachments or another machine?
- What safety features are available?
“The smaller sized machines fit well into tight or confined applications where manual labor had been used in the past. Larger machines in the compact excavator class provide more digging and lifting performance when needed,” explains Mike Fitzgerald, marketing manager at Bobcat. “Those rental operations that focus on homeowner and short-term rentals tend to utilize smaller compact excavators. When working with construction contractors and long-term rentals, larger machines provide the best ROI.”
Specs and project figures are important data to narrow down a search. Most applications for compact excavators are project-based, so what are the dig depth, lift height and lift capacity parameters of the job? What are the installation specs of the product — drainage pipe, tree transplants, coffins? Also determine the amount of material you are going to be moving and the time frame you need to move it in. Then, match those measurements to a machine by determining the capability of the machine. Popular mini ex specs include operating weight, dig depth, bucket breakout/digging force, maximum reach and hydraulic flow and pressure.
“Each model has different key specifications to consider when it comes to operating weight, dig depth, lift capacity and attachments,” explains Justin Steger, solutions marketing manager-site development and underground with John Deere. “Operating weight is important for ease of transportation. Consider a model that’s operating weight is large enough to handle the work you typically do and is most easily transported between jobsites given the truck and trailer equipment in your fleet.”
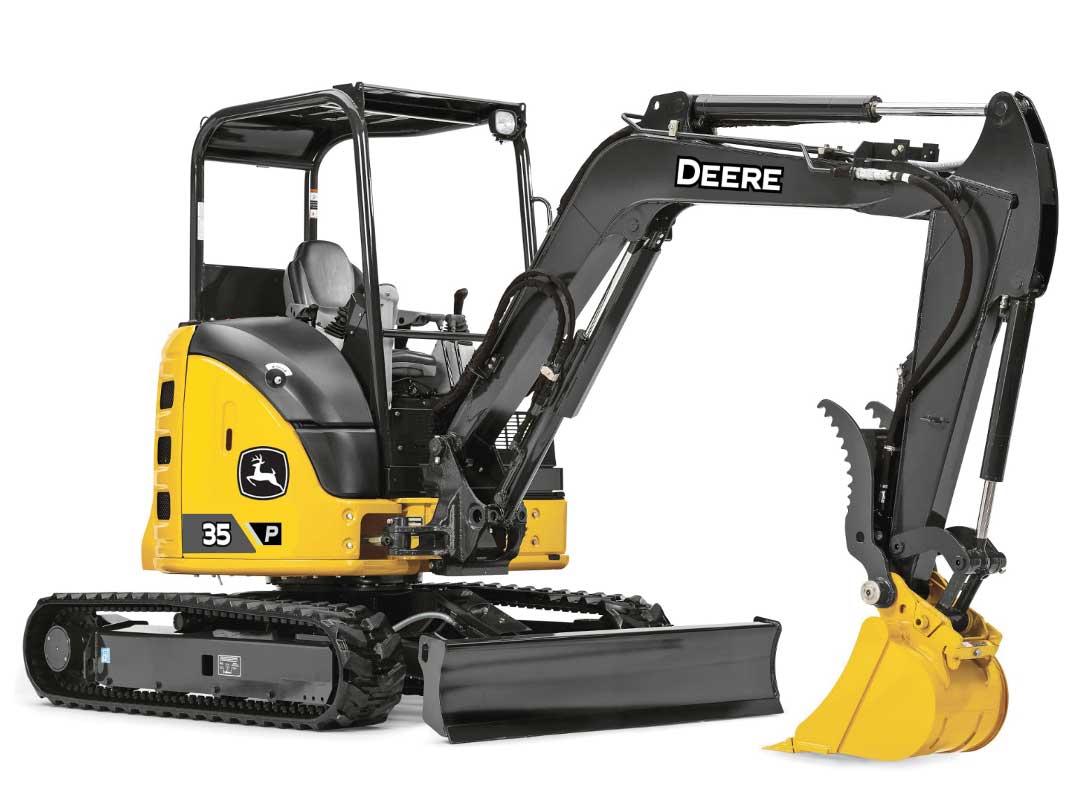
Let’s use John Deere as an example. Deere’s micro 17G offers a Yanmar 14.5-hp diesel engine, max dig depth of 7 ft, 2 in. and an operating weight of 1,790 lbs. The John Deere 60G boasts a 53-hp Yanmar diesel engine, max digging depth of 12 ft, 4 in. and an operating weight of 13,620 lbs. As you may have noticed, operating weights are also used to designate size class but instead of pounds (lbs) pros use metric tons. So, John Deere offers compact excavators from 1.7 to 6 metric tons overall.
“The 3- to 4-metric-ton size class is the largest industry when it comes to compact excavators in North America,” says Steger. “John Deere offers two models in this size class — the 30 P and the 35 P [pictured above] — to make sure customers have a choice when choosing the right machine.”
One of biggest growth segments is the 5- to 6-metric-ton class, attractive because of their step up in volume and capability to run bigger and more varied attachments. “The 3.5-metric-ton and 5-metric-ton size classes are very popular,” confirms Matsumoto. “The Hitachi ZX35U-5N 3.5-metric-ton unit is our most popular machine. It’s good for rental because of its versatility. With an optional angle blade, the ZX35U-5N 5-metric-ton machine is a good fit for many kinds of applications, including trenching, landscaping and site development.”
Long Arms or Extendable Booms
Reach is ever important for compact excavators that also take attachments like grapples and thumbs to move and place objects. There are specific compact excavators that can come with a long arm option or extendable or telescoping boom option to give extra reach. Long or extendable arm excavators are ideal for contractors in applications where space constraints on site require a very compact machine footprint coupled with increased bucket reach and dig depth, commonly found on larger class machines. Utilizing a long arm reduces the operator’s need to reposition the undercarriage, minimizing disruption to established turf and landscape. Long and extendable arms often get matched with a heavier counterweight on the back.
Price, of course, will be a factor. Compact or mini excavators can range from micro machines costing $20,000 to large 8 tonners costing $90,000, with most models in that 3- to 4-metric-ton class costing between $30,000 to $40,000. The cost of renting a compact excavator will depend on the size of the unit and the length of the rental, but renters can expect $250 to $400 per day, $900 to $1,250 a week and between $2,000 and $2,500 a month. Just remember…
“There are so many factors that come to mind besides the price when it is time to consider purchasing an excavator,” says Bill Holton, Kubota product manager, construction equipment. “What is the application that the unit will be used in, will the machine in question have sufficient lift or dig capacity and reach, does the owner need to trailer the unit or will he be paying for trucking to and from the jobsites? Follow that with any warranty or insurance packages offered by the manufacturer.”
Buyers and renters should also understand the physical machine dimensions of the unit being considered. If you’re a contractor working in backyards with tight access points, height, width, reach and swing will need to be calculated and perhaps a zero tail swing model will be required (more on that later). If you’re planning on using attachments, oil flow should be another point of consideration. “After all, a versatile machine can save both time and money,” points out Foy.
Attachments and Hydraulic Power
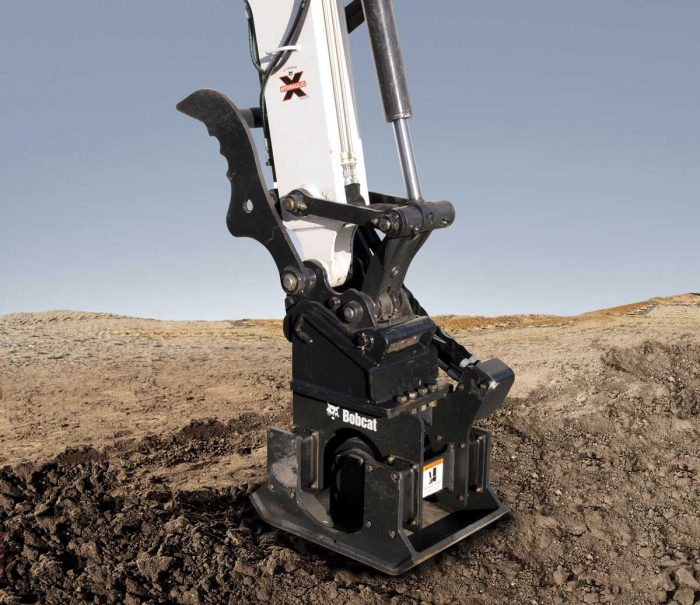
Compact excavators are powered via a complex circulatory system of hydraulic oil. Travel, boom, cab and attachment movements are all powered through the fluid mechanics of a mini ex’s hydraulic system. When discussing power to the attachment specifically, the term auxiliary hydraulic power is used, and it is measured in gallons per minute (gpm) and pressure (psi). For instance, Bobcat’s ultra-mini E10 excavator sports a max auxiliary standard flow of 5.3 gpm and max auxiliary pressure of 2,756 psi, while Bobcat’s big E88 offers a max aux standard flow of 25.1 gpm and max aux pressure of 3,045 psi. To match these…
“Bobcat currently manufactures more than 100 attachments for our excavator lineup,” says Fitzgerald. “We have seen in the market and heard from customers that attachment versatility has become incredibly popular. Along with buckets, our breakers, grapples and mowers are popular choices for a variety of specialized sitework for construction, land clearing and landscaping.”
Each attachment purchase or rental will require its own selection process, and I highly suggest you visit our archives at compactequip.com where we’ve done deep dives on almost every category. Let’s take hammer or breaker attachments, which work particularly well with compact excavators due to the machine’s long reach, ability to work with limited access and the ability to quickly switch from hammer to thumb and bucket when it’s time to remove the materials just demolished.
Mini excavators are making big waves on jobsites all over North America. Click here for the latest news on these machines and the companies that make them.
“Regardless of whether you’re renting a hammer or purchasing one, it’s important to match it to your excavator and its capabilities,” says Lee Padgett, product manager for Takeuchi-US. “First, make sure that the hammer’s weight is within the machine’s working range. Second, you’ll need to have the proper hydraulic flow and pressure to fire the hammer. Finally, you need a hammer that’s the correct size for the material you need to demo.”
Along with weight and size, operators will need to match the max flow (gpm) and pressure (psi) of both the host machine and attachment. Takeuchi offers seven different hammer attachment options. Its compact TKB52-S has a working weight of 200 lbs, operating pressure of 1,500 to 1,900 psi and an oil flow range from 4 to 9 gpm. Takeuchi’s large TKB1702-S has a working weight of 2,380 lbs, operating pressure of 1,960 to 2,105 psi and oil flow range of 23.8 to 34.4 gpm. Then breakers will come with a variety of options: varying body styles (box-style and solid-body encasements); firing systems (nitrogen or oil); and hammer bits (conical, chisel, cross-cut or nail point). Then, buyers and renters should understand factors like impact power, dry firing and daily greasing maintenance.
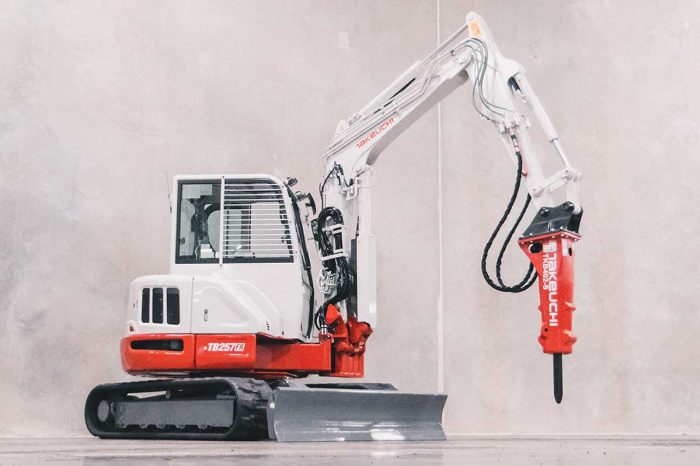
Like I said, each attachment will be its own research project, and there are a lot of implement options for compact excavators, including thumbs, augers, trenchers, grapples, rippers, plate compactors and mowers. The category of buckets alone will have loads of options from ditching and grading buckets to cemetery and skeleton buckets.
“Attachments have definitely been a driving factor in the mini excavator market as a way to maximize versatility on the jobsite,” says Foy. “We are seeing increasing demand for greater flow and pressure on hydraulic systems in mini excavators. When it comes to compact equipment like mini excavators, operators are looking for maximum power and efficiency in a small package.”
Mini excavators often have options when it comes to the coupler systems used for attaching. A standard attachment coupler system will require a person to manually secure and unsecure pins when exchanging attachments. A quick-coupler will enable fast, reliable and safe switch-overs between attachments without leaving the cab. A coupler with multi-pin centers and multi-pin diameters allows the coupler to pick up all attachments in the same weight class even though they might have different pin diameters. Tilt couplers allow the attachment to be tilted without moving the machine, so that slope work on trails, golf courses and other projects are more easily accomplished. Tiltrotator coupler systems allow an excavator’s attachment to twirl 360 degrees or tilt to odd angles for exacting excavation and implement work.
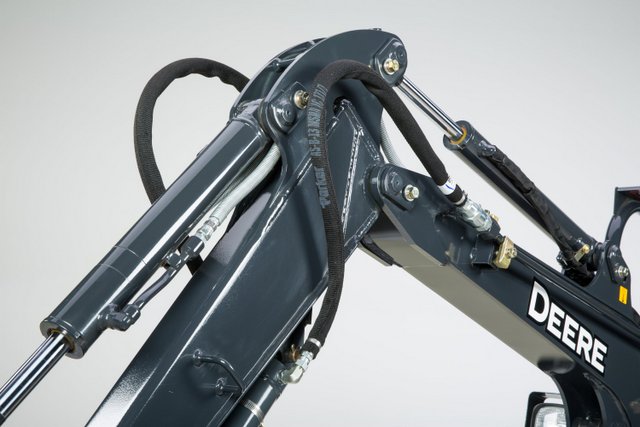
“Machines today have increased capabilities to handle and effectively multi-function with heavier and more productive tools,” says Worley. “Tilt Rotate System [TRS] models for Cat 302.7 through 310 Next Generation mini excavators allow attached work tools to rotate 360 degrees and tilt 40 degrees side to side. This enables the machine to reach more work areas from a single position, while maneuvering tools over, under and around obstructions when excavating, grading ditches, sorting recycled materials or placing pipe.”
Couplers and attachments will add to the utility of a compact excavator but also the weight. Counterweights may need to be added to allow safe operation of the equipment.
Two other cool attachment trends for compact excavators are grade control and diverter valves. Grade or machine control systems are usually installed through aftermarket OEMs like Trimble or Topcon, but two mini ex manufacturers (Cat’s Ease of Use system and Bobcat’s Depth Check system) offer very cool entry-level machine control options. Grade control systems help operators dig precisely, measuring the position of the bucket and boom and controlling certain parameters set by the operator (depth, slope and elevation control) or even using a 3D model to dig and sculpt. Applications such as trenching for footings, grading ditches or digging out basements might require a consistent grade, sustained slope or precise design.
“The cost of grade control systems is still a concern, but as this technology becomes more reasonably priced and common at jobsites, I expect to see the demand increase,” says Ashton.
Another popular trend over the last few years has been selector valves for auxiliary hydraulics. “John Deere offers these selector valves as standard equipment on the 26 to 60 models mounted to the arm of the machine,” says Steger. “This allows a machine with a hydraulic thumb to also use other auxiliary hydraulic powered attachments without the need to connect and disconnect auxiliary hydraulic hoses. The operator simply has to turn the valve to select where to route the hydraulic fluid, attachment or thumb, and that’s it.”
Tiltrotator Advice via Takeuchi
It’s a good idea to demo a machine outfitted with a tiltrotator before purchasing one, just to make sure you feel comfortable with the idea of operating it. Once you’re ready to buy, ensure that your excavator model has the correct hydraulic flow to match a tiltrotator’s requirements. Tiltrotators can be controlled in several different ways, so make sure you have the appropriate number of circuits for the model you choose. While it’s important to get the unit that fits your budget without overextending yourself financially, purchasing or renting a more feature-rich model with options like a hydraulic coupler, hydraulic gripper and attachment quick-change system can drastically reduce the number of workers required on site to complete the same task. It can also increase the number of attachments you’re able to use, opening you up to more job possibilities. More sophisticated tiltrotators with grading capabilities built in are a great choice when operators will need to complete jobs with extreme precision. For all these reasons, even a more expensive tiltrotator can often pay for itself in a relatively short period of time. — Lee Padgett, product manager, Takeuchi-US
Mini Excavator Cabs and Telematics
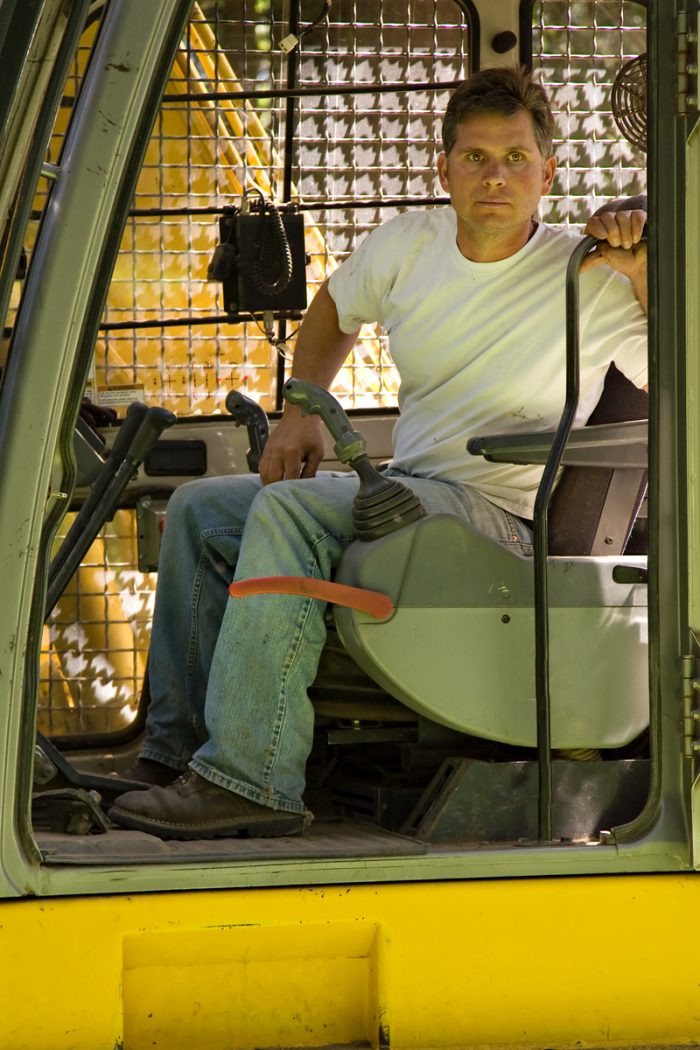
The operator station of a compact excavator has come a long way, and today they are especially customizable — for long days, short rents and specific applications. Do you want an enclosed cab with heat and air conditioning or is an open-air roll over protection system (ROPS) just fine?
“Develon -7 Series mini excavators come standard with enclosed cabs with heating and air conditioning for enhanced operator comfort,” says Lee. “Adjustable armrests in the mini excavator cabs move precisely to where operators are most comfortable. The seat features extra layers of insulation, minimizing heat transfer and vibration from the engine to provide enhanced comfort.”
First, that seat. A vinyl or cloth suspension seat with lumbar support and limitless adaptability will immediately enhance comfort and probably production. You can get that seat heated too. The overall size of the cab is important, including the door opening, shoulder room and foot and floor space. Check for ample storage. Work the ergonomic controls, adjustable wrist rests, adjustable windows, windshields and automotive-style climate controls. Ensure that switching from pilot controls to traditional backhoe configurations (ISO to SAE) is simple. This writer is old and prefers backhoe pattern. Also, a radio with Bluetooth technology can enhance an operator’s groove.
From the cab, explore how the machine sounds and travels. Does the unit have a solid construction that absorbs vibration? How loud is it? Does it have an auto idle or eco mode feature to automatically rev down, lower noise and save fuel costs? How does it travel? Mini excavators can move pretty slowly, so some manufacturers offer innovative travel tech. Ask about them.
LCD touchscreen digital displays are now the command centers for the most high-tech excavators. Through these sophisticated control panels, operators and mechanics can access machine maintenance vitals, service manuals and security and language protocols. Operators can access the pattern changer or hydraulic quick-coupler with the push of a digital button. Attachment automation features are also available, often via these digital displays. Adjustable auxiliary attachment flow or continuous flow can be dialed in precisely from these command centers.
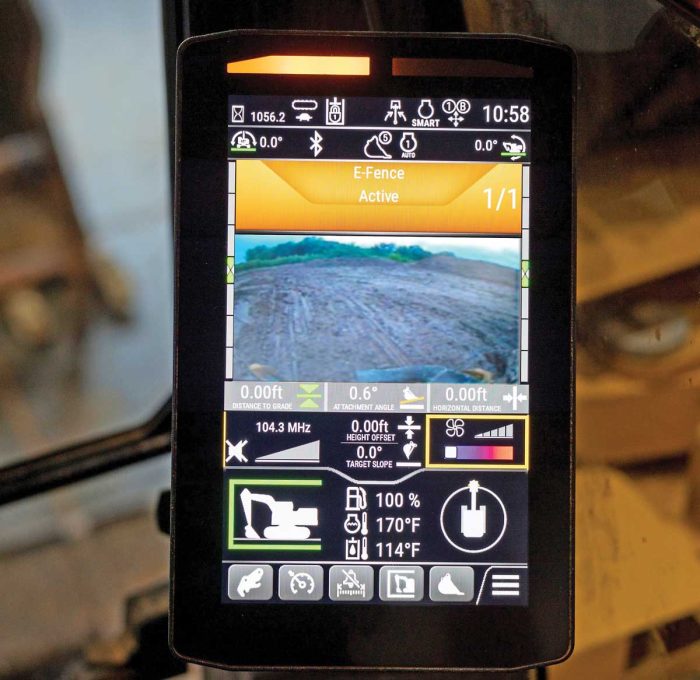
“The 7-in. LCD screen comes standard in Kubota’s -5 Series and provides the operator a clear full-color display with easy access to the biometrics of the machine at a glance,” says Holton. “It features an operator friendly jog dial to scroll through the features and adjustments and a 60/40 display screen split if equipped with the optional rearview camera.”
Not exactly in the cab, but telematics is another feature that excavator owners are adding for a monthly fee or often getting for free for the first couple of years of ownership. Telematics is an umbrella term for a variety of technologies and services that monitor a unit, collecting and sharing digital data on everything from systems analysis (think maintenance) to location (think theft). A telematics monitoring device would be installed on the unit or multiple units, and vested parties would be able to monitor those machines via smart devices like a computer, phone or tablet.
“Technology such as telematics and automation are starting to migrate from the larger excavators into compacts,” says Steger. “While telematics provides benefits such as location and utilization, automation can make a machine more efficient. It’s important to consider customer value for this size class machine.”
Tail Swing, Backfill Blades and Tracks and Tires
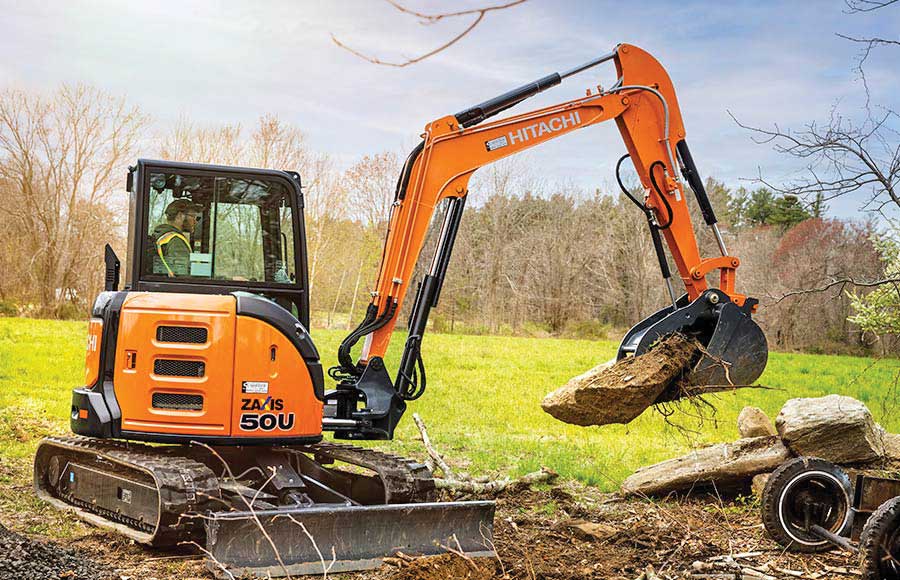
Compact excavators are designed to work in tight quarters — next to a house or busy lane of traffic. With this in mind, manufacturers offer three main tail swing configurations. On conventional tail swing machines, the rear of the machine extends over the track width. Minimal tail swing usually means, under the same condition, the counterweight might extend a few inches outside the width of the lower track pads. Lastly, there are zero tail swing machines, “which means the rear of the machine never protrudes past the tracks of the machine at any point,” says Foy. “This function allows an operator to get close to a structure or in tight areas that a conventional tail swing would not allow.”
Attached to the undercarriage frame, a backfill blade is an important part of the compact excavator’s arsenal. The blade is used to backfill spoils into a trench, grade material, add stability while digging and help prop up a unit for undercarriage work. There are some unique backfill blade options out there. Blades can come in simple push configurations or angle versions. Blades on the smallest micro units will have the ability to fold in with a retractable undercarriage. There are also four-way and six-way angle backfill blades on higher-end units.
“The Kubota KX040-4 is a top selling 4-metric-ton machine, and when equipped with the optional six-way dozer blade function, this machine is tough to beat,” says Holton. “Weighing in at just over 10,000 lbs, the KX040-4 is a competitor in the dirt with its dozer blade options and operator friendly controls.”
Those blades attach to the compact excavator’s undercarriage, which can be broken down into many components and systems. A sprocket is a profiled wheel with teeth that meshes with the compact excavator’s tracks. Idler wheels are at the front of the track frame that guides the rubber track. Rollers are metal wheels that are mounted to the top and bottom of the track frame, which support and guide the rubber track between the sprocket and the front idler. There is also a variety of tracks. Owners and operators can choose between aftermarket tracks or OEM tracks, the latter coming from the mini excavator manufacturer. There is usually a budget-friendly alternative aimed at less abrasive applications, and there are always higher-grade options.
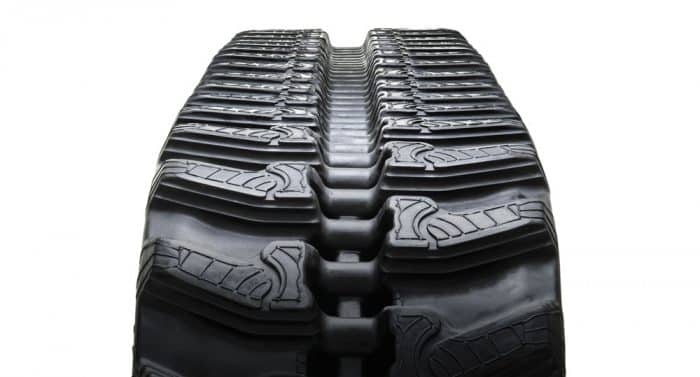
Discussion points might include rubber quality, resistance to punctures, cable corrosion, detracking, tread life, vibration, correct sizing and the “carcass.” There are also pattern choices, which vary by name and design, but popular patterns include: turf (light footprint); slick surface (traction on snow/wet surfaces); zig-zag (mud); all-terrain (from rocks to mud to lawns); and the C-pattern (a standard OEM tread). There will also be straight rubber tracks (most popular), steel tracks (for bigger diggers in aggressive applications) and hybrids which are a mix of steel and rubber usually with detachable pads.
Instead of tracks, wheeled models are also becoming available in America, but they are usually on the larger end of the compact realm, aimed at applications that require roading.
Diesel Engines and Electric Variants
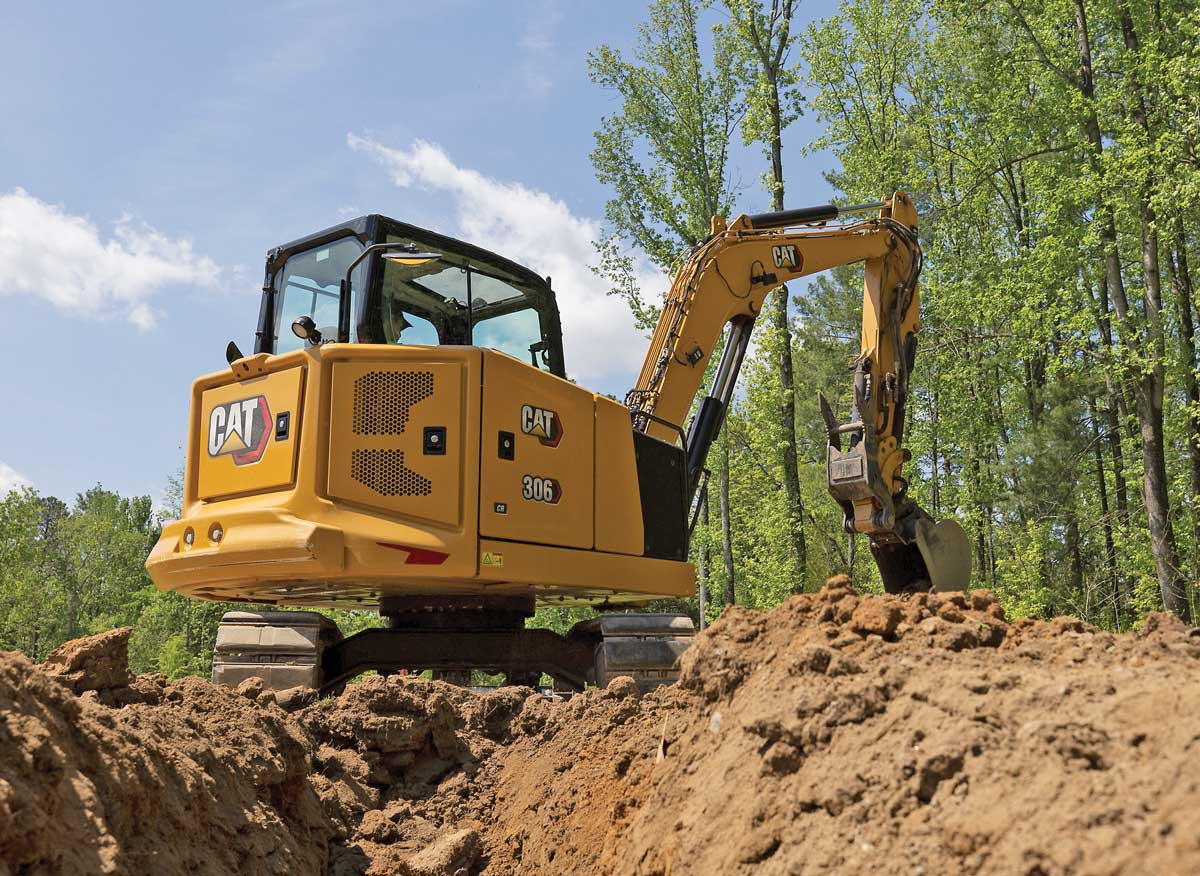
For the most part, off-highway diesel engines power compact excavators, ranging from around 13 to 70+ hp. All newly sold excavator engines will meet EPA’s newest standards for off-highway diesel engines known as Tier 4 Final. These diesel power plants are smarter, more complex and cleaner burning and may include new technologies, maintenance and fluids (but also more advanced features, better fuel efficiency and greater eco-friendliness).
Many small excavator units rely on emissions-reducing exhaust filters in aftertreatment systems, also known as diesel particulate filters or DPFs, which require periodic cleaning called regeneration. Bigger units require SCR technology, which stands for selective catalytic reduction. It’s a Tier 4 Final system aimed at cleaning up emissions too, and it requires the use of an extra liquid (diesel exhaust fluid or DEF) at about 2 percent the ratio of fuel. NOTE: Most compact excavators won’t require DEF. In fact, most manufacturers have a mission to stay below a 25-hp threshold on popular units like those 3 to 4 tonners, which allows them to bypass EPA regulations. It’s all about downsizing.
Electric-powered variants are starting to creep into the American market as well, boasting big upfront price tags but also low fuel costs and zero emissions.
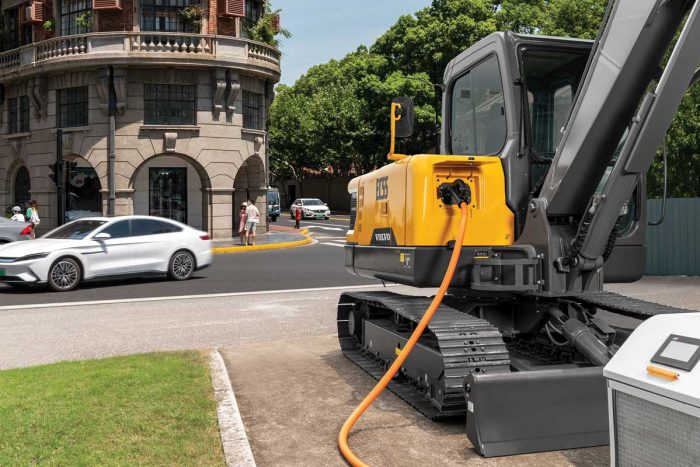
“Electric is definitely a hot topic in compact equipment right now,” says Ashton. “[Volvo] currently has three electric compact excavator models on the market. They are expanding people’s ideas about what these machines can do because zero emissions and significantly lower noise levels allow them to work in spaces where diesel machines aren’t usually welcome. These early models are also providing insight into the design of larger electric models and what could or should be done differently and what is working well.”
According to a report from Calstart, a global non-profit focused on clean energy and transportation, sales of battery electric mini excavators accounted for 5 percent of the total U.S. market in 2021 and are projected to account for 15 percent of the market by 2029. Volvo Construction Equipment has produced electric mini excavators for a couple of years now. JCB just announced its electric-powered 19C-1E reached a milestone of 1,000 units sold. Many other brands are beginning to market units in America. Wacker Neuson showcased a 1.7-metric-ton battery-powered excavator, the EZ17e, in its booth in March at CONEXPO-CON/AGG (that big tradeshow in Vegas that only happens every three years). Hyundai showcased its prototype 2-metric-ton R19E electric-powered compact excavator at the same show.
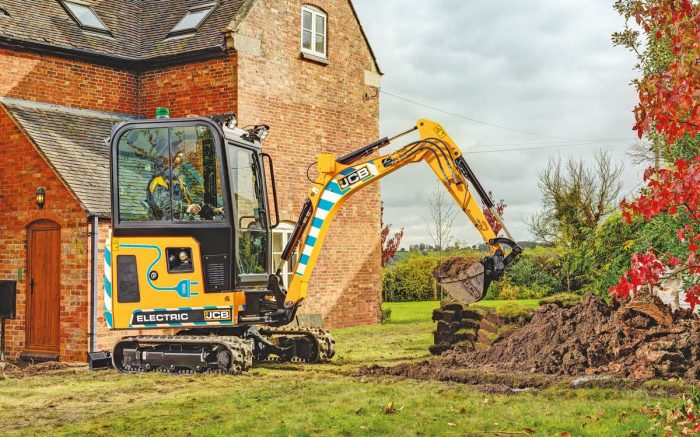
At the Consumer Electronics Show in January, John Deere showed off its mid-sized 145 X-Tier electric excavator prototype powered by Kreisel battery tech (a company Deere acquired and is expanding). At bauma (that big tradeshow in Germany that happens every three years), Hitachi unveiled four new zero-emissions excavators, all of which can be powered by lithium-ion batteries or a cable connection. Bobcat has a partnership with Green Machine (an equipment electrification expert) to make and sell its electric mini excavator variants.
“Compact excavators are prime candidates for operating on electric power,” says Fitzgerald. “They are frequently used indoors where there may be a desire to reduce engine emissions. Some jobsites have working hour noise restrictions, and an electrically powered machine provides additional jobsite utilization.”
Go Operate Some Units
To complement all of this great information, demos will be required. A great way to experience multiple units is to rent machines from local lots, but remember, rental units are usually bare bones and often do not have a lot of the high-end features mentioned in this article. Dealers are always happy to let potential buyers run a unit through its paces as well, so take the opportunity. Demo multiple brands and models.
“You have to visit your local dealer or the nearest independent rental company that have compact excavators and operate them,” confirms Matsumoto. “Get a feel for how smooth the hydraulics are and how easy the attachment operation is. This cannot be described in text. You need to experience the machine yourself.”
Keith Gribbins is publisher of Compact Equipment.
Brand Differentiators
Bobcat
The Bobcat mini excavator lineup has 17 models and two series (the R- and R2-Series). All Bobcat excavators are engineered to provide peak performance and compatibility to an array of attachments. Many of its models can be configured with industry-exclusive features, including the unique Pro Clamp system, Hydraulic X-Change coupler, extendable arm and Depth Check system. The recently launched R2-Series offers an impressive array of options, including a high-back, heated seat with headrest and a 7-in. touch display that’s one of the nicest in the industry.
Cat
Caterpillar offers an extensive line of mini hydraulic excavators from 1 to 10 metric tons. An exclusive feature for these Next Generation models is the standard Cat Stick Steer system, which allows the operator to switch from conventional lever/foot-pedal steering controls to low-effort joystick control. Automatic two-speed travel is standard, as is a cruise control system that further simplifies machine travel. Plus, Cat’s new E-Fence and Indicate technologies for Cat 6- to 9-ton mini hydraulic excavators are awesome entry-level grade control options.
Develon
One of the big differences between Develon mini excavators and other brands is Develon mini excavators come standard with an enclosed cab with heating and air conditioning. Another differentiator between Develon mini excavators and other brands is the standard telematics system available for all Develon models. The telematics system allows owners to remotely check their mini excavators from an app on a smartphone or on a computer. The data for the equipment is available in one easy-to-access interface from Develon.
Hitachi
Hitachi offers eight mini excavator models to the North American market. These include the ZX17U-5N, ZX26U-5N, ZX30U-5N, ZX35U-5N, ZX50U-5N, ZX60USB-5N, ZX75-5N and ZX85USB-5N. The company’s focus is to provide customers with a machine that delivers efficiency, reliability and safety. The Hitachi hydraulic system is especially great for efficient fuel consumption, and it delivers the speed and power the machine operator wants. The ZX35U-5N (3.5 metric tons) is the brand’s most popular machine, great for rental because of its versatility.
John Deere
John Deere offers six compact excavator models from 1 to 6 metric tons. Its new P-Tier models replace the durable and smooth operating G-Series machines and maintain the same levels of productivity operators expect in a small excavator. Just like the G-Series, all six of John Deere’s P-Tier models come standard with mechanical, wear compensating couplers that are also interchangeable with D- and G-Series buckets and attachments. Additionally, the P-Tier models will now offer optional JDLink telematics providing customers with valuable data.
Kubota
Kubota is often cited as the market leader in mini ex sales, selling the most units in the North American market. The Kubota compact excavator lineup provides support in segments from 1- to 8-metric-ton machines with a total of 13 in all. One of its coolest features is the 7-in. LCD screen that comes standard in the -5 Series and provides the operator a clear full-color display with easy access to the biometrics of the machine. It features an operator friendly jog dial to scroll through features and a 60/40 display screen split, if equipped with the optional rearview camera.
Volvo
Volvo Construction Equipment has 11 internal combustion engine models and three electric models. What makes these models unique? Not only do Volvo compact excavators have advanced telematics and 50-hour greasing intervals, but the company’s hydraulic system is flexible and customizable for the end-user. Operators can adjust flows, whether it is a single direction or dual direction, and save their preferred settings. Also, a standard patented hydraulic filter provides extra protection in the hydraulic system when using attachments.
Yanmar
Yanmar currently has nine different models ranging from 1- to 10-metric-ton size classes. The company offers six true zero tail swing machines, which means the rear of the machine never protrudes past the tracks of the machine at any point. Yanmar also has a standard hydraulic quick-coupler to change out attachments quickly and easily, which reduces downtime at a jobsite. With each of Yanmar’s mini excavators paired with a standard four-year, 4,000-hour standard warranty, operators know uptime and return on investment is a staple to the Yanmar line.