Mini Ex Engine Maintenance
When digging duties are needed on the job, an excavator reigns supreme with its ability to tear up the earth and expose what lies beneath. At the heart of this machine is its engine — pumping power through its veins to keep you productive and meeting deadlines. In order to stay on the job and avoid costly downtime, it’s essential to be diligent about engine maintenance so the excavator can chug along rather than sit on the sidelines.
“As with all construction equipment, the efficiency of an excavator is highly dependent on the efficiency of the engine,” says Joe Mastanduno, product marketing manager, Engine/Drivetrain, for the John Deere Construction and Forestry Division. “Improper care of the excavator engine can result in increased fuel costs along with reduced machine productivity.”
Keeping up to date on engine maintenance is vital to keeping your excavator productive on the jobsite. While workdays may get busy, it’s always important to take the time to perform routine engine upkeep. To assist an operator in his or her maintenance tasks, most excavators come equipped with a periodic maintenance chart on them, as well as a detailed operator’s manual for further maintenance points.
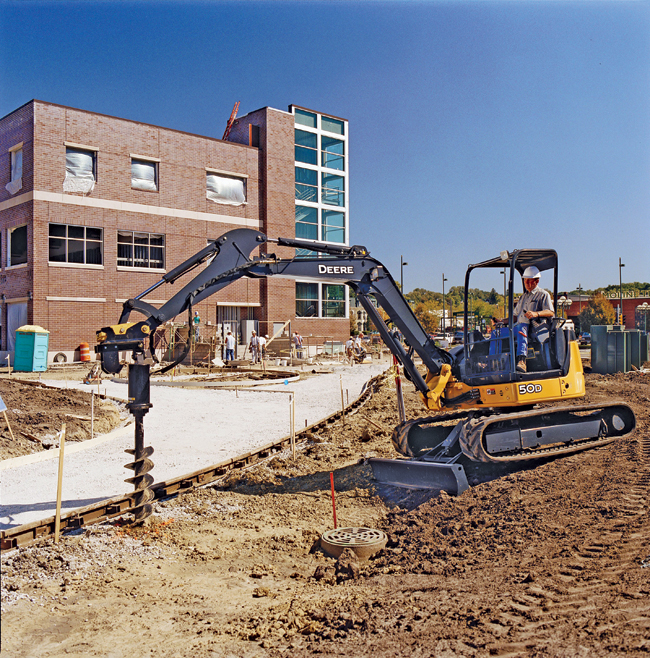
“It’s vitally important to follow the maintenance timetables of the excavator,” explains Mark Wall, product marketing manager for Hitachi. “At Hitachi, we think in terms of greasing intervals, fluid change intervals and filter change intervals.”
Understanding what to check and when will ensure that the engine is taken care of properly during the lifetime of the machine. A diligent maintenance plan helps to increase fuel efficiency, productivity and the excavator’s life.
Relying on Your Senses
Both Wall and Mastanduno recommend performing a daily walk around on each machine before starting it. This maintenance task includes taking a look under the hood, along with basic fluid checks. While these daily checks are important, operators should also rely on three of their five senses to get a full understanding of what’s going on inside the engine. Before and during use, operators should take the time to “look, listen and smell” their excavators.
Look — When an operator walks up to the machine, he or she should observe track tension and look for loose bolts. When moving the machine, the operator should look for wet spots on the ground or on the machine.
Listen — As he or she is operating the machine, the operator should listen for different sounds, such as a pump squeal, a different hydraulic sound, a pin squawk that needs greasing, a track pop that is too tight or too loose or something missing from the engine.
Smell — Also during use, an operator should smell for fluids that may be leaking. An operator should be able to smell the difference in hydraulic oil and diesel fuel or engine oil and antifreeze.
If the workday gets hectic and an operator is unable to do this evaluation of the excavator, the machine’s fluid levels should at least be checked before operation to prevent any issues down the road. Thanks to telematics technology, such as John Deere’s JDLink and Hitachi’s ZXLink, daily checks can be enhanced with a quick look at the on-line machine status. These systems can be a great benefit since a quick check of any codes that have been set and any pending software downloads can all contribute to enhanced machine efficiency and productivity of the excavator.
Daily Duties
To aid in understanding daily engine checks, both John Deere and Hitachi offer advice on four components that should be observed and tended to on a daily basis — the fuel system, engine oil, the cooling system and the air filtration system. By paying close attention to these important parts of the engine, an operator can expect increased productivity and longevity out of his or her machine.
Fuel System — On a daily basis, it’s critical that the operator bleed off water from the fuel/water separator. It’s also recommended that the operator drain the fuel tank sump water. “The decal on the machine is 50 hours,” explains Wall. “But from an operator’s point of view, I would check daily and measure water until I knew what the check frequency should be.”
Engine Oil — The oil level should be checked on a daily basis and filled as needed.
Cooling System — The coolant level should be checked on a daily basis and filled as needed.
Air Filtration System — According to Mastanduno and Wall, John Deere and Hitachi excavators have an air filter indicator on them. This device allows operators to determine if there is a blockage in the air filtration system before it becomes a serious concern. “This indicator allows for a quick indication of the filter being plugged,” explains Mastanduno. “There is a pressure switch on the air filter that is connected to the engine computer. As a result, JDLink will also alert an owner/operator to the pending need to replace an air filter.”
Smoke Signals
Another way to determine when maintenance may be needed is checking out the exhaust smoke that’s coming from the excavator. The color of excessive exhaust smoke — such as black, blue and white — can expose specific maintenance needs and signal when an operator should take a closer look.
“Black smoke indicates that there is a restriction in the air circuit, either in the intake/exhaust or as a result of excessive fuel,” says Wall. “If the air cleaner is not being properly maintained, there is likely to be excessive black smoke.”
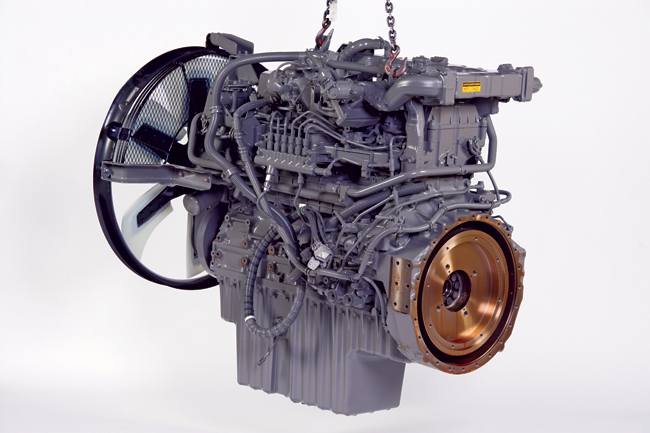
Mastanduno points out that blue smoke is almost always a by-product of excessive oil consumption, while white exhaust smoke is usually only seen in cold-weather operation — and then only briefly unless poor cetane fuel and/or poor compression are present, resulting in a misfire. White smoke could also be from a loose connection or clamp to the turbo. Keeping up with an engine’s maintenance regimen is important to stay on the job and remain on task. By following some basic guidelines and intervals, an operator can ensure the heart of his or her excavator is working properly and will continue to pump out the power needed to stay productive.
Pam Kleineke is a contributing editor to Compact Equipment, based in
Peninsula, Ohio.
Comments are closed here.