Miller Electric Introduces a New ArcReach Heating System, Check It Out
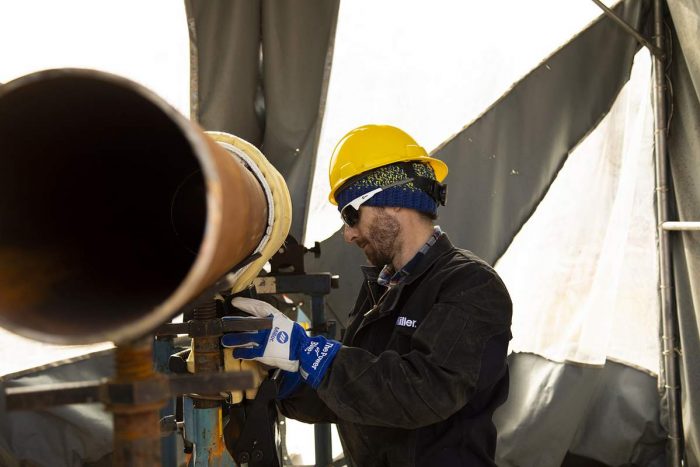
Miller Electric Mfg. LLC recently announced its newest induction heating solution. This new system is designed for jobsite weld preheating and bakeout in construction and pipe applications with temperature maximums of 600 degrees Fahrenheit and 315 degrees Celsius. ArcReach Heating Systems deliver weld joint preheating and bakeout that is easy to use and significantly faster, safer and less expensive than open-flame or resistance methods.
With ArcReach Heating Systems, contractors in refinery, petrochemical, power plant, shipyard, structural construction and oil and gas applications can insource weld joint preheating and bakeout in the field — improving productivity and profitability on the jobsite. ArcReach Heating Systems utilize ArcReach-enabled welding power sources, further enhancing convenience and lowering costs.
“This technology can save several hours and hundreds of dollars per weld joint,” says Linda Hintze, induction heating systems product manager, Miller. “Contractors using ArcReach Heating Systems can control their own heating timeline and see a return on their investment by the 11th joint they preheat, which is an extremely fast payback.”
Resistance heating, another option, requires installing and dedicating expensive primary electrical power that could be used for welders or other tools. It can also add hours in setup and tear down for resistance equipment. When contractors hire specialized heat-treat companies to perform weld preheating and bakeout work, it can cost up to $2,000 per weld joint. The third option is flame heating, which consumes up to $50 per hour in propane, requires paying fire-watch personnel and creates numerous safety hazards. In addition, the time it takes to reach required temperatures using flame heating can take hours.
By comparison, ArcReach Heating Systems allow contractors to insource preheating and bakeout using welding power sources already on site. Welding operators can perform the preheating and bakeout with easy-to-use equipment and tools and don’t have to rely on third-party contractors, providing complete control of the schedule. With induction heating, the system can typically bring a joint to temperature in 20 minutes or less — saving significant time and money. An ArcReach Heating System includes an ArcReach Heater that is used with air-cooled cables or air-cooled quick wraps as heating tools.
ArcReach Heaters are powered by select models of compatible ArcReach welding power sources, including all XMT 350 FieldPro power sources, any Miller engine-driven welder/generator with ArcReach technology and any Miller power source that can run a Smart Feeder. The DC power from the welding power source or engine drive is converted into AC current to power the ArcReach Heater. Standard weld cables connect the compatible power source to the system, with a maximum distance of 200 feet one way and 400 feet total loop.
Mini excavators are making big waves on jobsites all over North America. Click here for the latest news on these machines and the companies that make them.
Induction heating is faster, safer and more consistent compared to flame and resistance heating methods. ArcReach Heating Systems use electricity from heating tools placed on or around magnetic metal surfaces, such as iron or steel, to create currents in the metal. These currents pass through the workpiece and are converted to heat — so the workpiece itself is the source of the heat, not the heating tools.
These induction benefits also make it quick and easy to set up, use and tear down an ArcReach Heating System, since it can be quickly moved to the next joint with no need to wait for the tool to cool down. In addition, induction results in temperatures that are consistent and evenly controlled throughout the weld joint. The system uses thermocouple sensors to accurately report joint temperature, which is displayed on the interface. Temperature information is recorded automatically for quality control and reporting purposes.
ArcReach Heating Systems can be used for preheating and bakeout of flat surfaces and also provide uniform heating for pipes, irregular-shaped parts and those with non-uniform thicknesses.