How to Choose a Mini Skid Steer in 2024
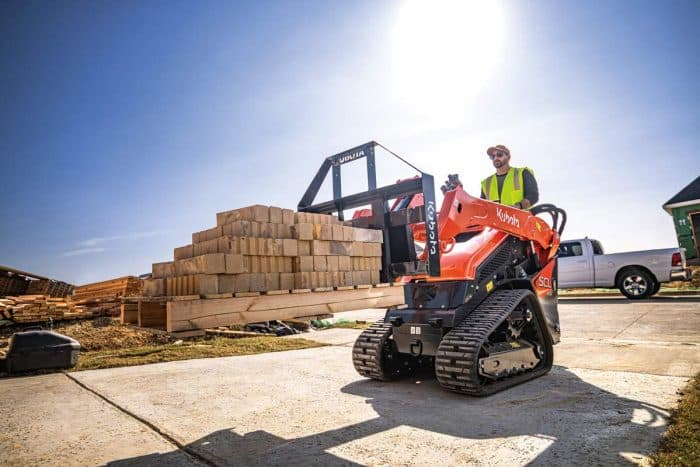
Mini skid steers may well be the most versatile single category of equipment in the construction market. True, their capacities are small compared to full-size excavators and wheel loaders and much less than even the capacities of full-sized skid steers and compact track loaders, but they can be configured to do most tasks that would otherwise be done by crews with hand tools and wheelbarrows and do them in a fraction of the time. Compact tool carriers (also called mini skid steers, mini track loaders, compact utility loaders and so on, depending on the manufacturer) provide pros with a powerful, hardworking machine that’s capable of navigating tight spaces.
Beyond applications that historically entailed hand labor, these machines also excel at loading, placement, backfilling, spreading, trenching and a host of other jobs that require mechanized equipment. Further expanding the utility of mini skids is the emergence of electric machines for indoor applications, such as demolition and flooring. The battery-powered eDingo 500 from Toro is one such machine, and Toro has developed a line of 30-in. attachments for use with the eDingo to maximize indoor maneuverability and access.
Stand-On or Walk-Behind Mini Skid Steers?
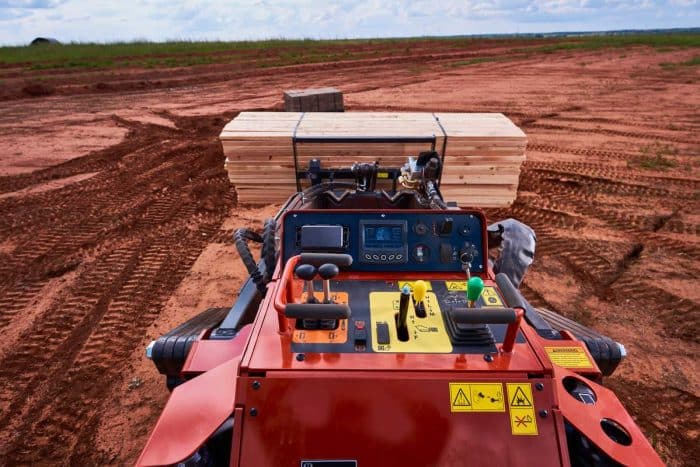
Early iterations of mini skid steers were typically walk-behinds or what the industry calls “pedestrian” machines. They were easier to design and build and in practice served as bridge technology between manual labor and the advanced mini skids of today. A few remain available. Their lower cost, lighter weight and smaller footprint all offer advantages. Yet, stand-on has become by far the more popular type and pedestrian models are fading.
The main advantage of stand-on models is that their ground speed is not restricted to the operator’s walking pace. Travel speed of the Ditch Witch SK3000, for example, is 6 mph, about double a normal walking pace. Some OEMs use slower speeds in reverse than in forward for safety and handling considerations. Ditch Witch uses the same speed forward and back with the idea that reverse speed is important for such applications as material handling and brush clearing. The overall design of the machine allows full-speed reversing with no adverse effect on controllability.
Stand-on also gives better visibility, especially to the front of the machine and the bucket or other attachment, since the operator’s position is elevated and nearer the front of the machine. The third key advantage is the ability to design the platform to isolate the operator from vibration and bouncing, improving control and reducing fatigue.
Tracks or Tires?
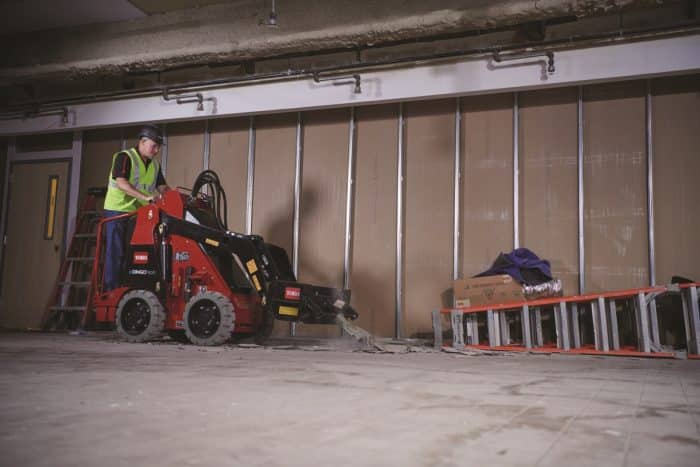
Mini skid steers are available with tracks and tires, and the feature sets are different. Tracks have lower ground pressure and are less likely to mar finished surfaces, whether a concrete patio or manicured turf. They also have greater tractive effort — that is, the ability to push. They also can produce far less surface disruption, but that depends largely on a skilled operator avoiding the use of counter-rotation steering. Tires are much less likely to be damaged by rocks, metal pieces and other debris.
Semi-pneumatic tires are nearly impervious to cuts and punctures. With tires, there is zero risk of de-tracking which results when tracks are improperly tensioned or subject to extremely rough terrain. De-tracking is the single biggest factor in downtime with tracked machines. Machine cost is higher with tracks. This is reflected in both the purchase price and rental rates and so affects customers whether they purchase or rent their mini skid steer.
Let’s take a look at six brands of mini skid steers or compact tool carriers.
Tool Tips
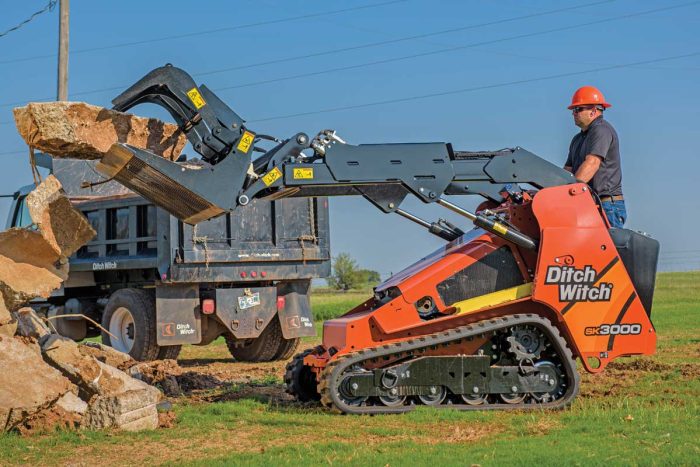
Buckets should be tipped slightly forward to keep material from spilling onto the loader. Buckets and forks should be carried low during travel. This lowers the center of gravity of the machine and improve stability. Some machines offer automatic self-leveling on the raise cycle and some on both raise and lower. For example, Ditch Witch’s SK3000 has bidirectional self-leveling. The feature can be toggled on and off by the operator and should always be off while digging.
Couplers vary. Some OEMs have proprietary couplers to pair with their proprietary attachments; using non-branded attachments requires an adapter. There are CII (common industry interface) couplers, and there are skid steer plate couplers. There are mini skid steer plate couplers. Unlike skid steer plates, which must conform to ISO standards, mini skid steer plates have no such standards but instead reflect an alliance among manufacturers.
Two Lifting Patterns for Mini Skid Steers
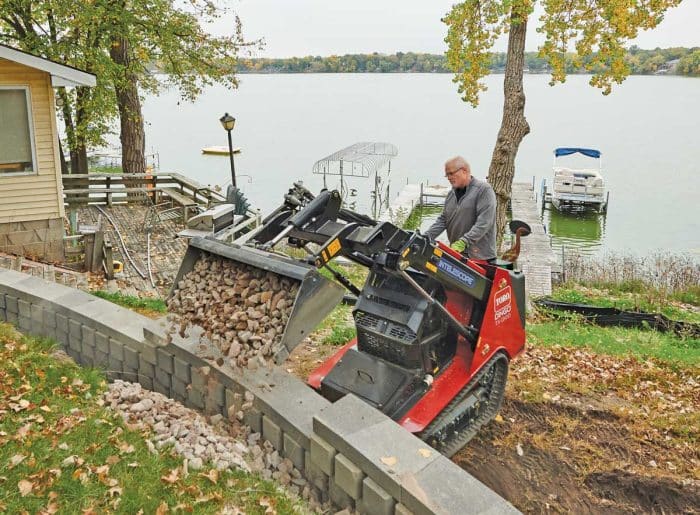
There are two lift patterns, vertical and radial, and the key distinction is where they place the bucket or attachment relative to a plumb line dropped at the front of the loader. Vertical lift keeps the attachment the same distance in front of the machine and provides greater reach at the upper and lower extremes of the lift cycle. This is helpful for loading, whether with forks or a bucket. Radial puts the attachment through an arc during the lift cycle so that it is nearer that plumb line at the top and bottom of the lift and farthest forward in the midpoint of the lift. This provides greater breakout force.
Mini skid steers will commonly have auxiliary hydraulics to run attachments. There can be one or more auxiliary circuits, and these can be one- or two-way flow. There can also be electrical connections for attachments requiring them. Make sure all couplers are clean, secure and leak-free when changing or mounting attachments.
So many variables. How can a customer possibly know them all? You don’t have to be an expert in mini skid steers and their attachments. You just have to be knowledgeable about your objectives. What are you trying to accomplish? What materials are you working with? Indoors or out? Underfoot conditions? Terrain? Required lift height? Required volume? Share this information with the rental house or dealer and let them select the right attachments and pair those attachments with the right compact tool carrier.
Operational Tips for Mini Skid Steers
Avoid travel on steep slopes. When traveling on slight slopes, reduce your speed. Travel up and down the face of the slope. Do not travel cross-slope. Keep the heavy end of the machine facing uphill. Never operate on slopes in ice, snow or rain. Use the same guidelines when getting the mini skid steer on or off a trailer where the maximum angle of the loading ramp should be no greater than 15 degrees.
As for the controls themselves, they vary widely. Why? Although mini skid steers are not expensive machines by construction equipment standards, there is a broad range of price within the category. The most advanced models can easily be two or three times as expensive as the simplest machines.
Control systems vary accordingly because of their cost: mechanical, pilot, and electric over hydraulic; joysticks, thumb wheels and levers. Control patterns also vary and some machines use a combination of patterns. This allow the patterns to be configured to match operator preference. Despite the non-standardized controller landscape, OEMs do their best to make controls that are understandable and easy to learn. For example, Kubota’s one model of mini skid steer, the SCL1000, has a standard ISO joystick to control the hydraulics and loader arm of the machine. Then there’s a T handle to control travel direction and speed. Spend time with the dealer or rental house to go over the controls. Then practice on site until the controls become at least somewhat familiar and intuitive.
Our thanks to the following for their support with this article: Brant Kukuk, product manager, Ditch Witch; Anna Kitzerow, product marketing specialist, construction equipment, Kubota; Sam Dando, senior product marketing manager, Toro.
Richard Ries is a freelance writer for Compact Equipment.