The Future of Parts: 3D Printing Offers Manufacturers the Opportunity to Strengthen Aftermarket Support, Develop New Products
Manufacturers are always looking for ways to improve their products and serve their customers better. It can include anything from adding new features to a product or rolling out a new aftermarket program. For companies such as Volvo Construction Equipment and Caterpillar, it includes adding 3D printing or additive manufacturing capabilities to stay innovative in product development and take care of clients after the sale.
“The advantages are huge,” says Daniel Kalfholm, project leader purchasing, aftermarket products for Volvo Construction Equipment. “Simply put, for the equipment manufacturer it’s faster and more cost effective to have a single line of production from idea to reality. But it is the customers who really benefit. From an aftermarket perspective, if a part has moved out of serial production or it’s too expensive to produce through conventional methods, additive manufacturing comes into its own.
“For example, production methods such as injection molding for plastics and casting for metals usually require a certain minimum order to be cost efficient — but 3D printing cuts all that out,” he continues. “And since this technology does not require production tools in the same way as regular manufacturing, the distribution possibilities are much greater. For Volvo CE, it means we can support our customers locally more efficiently, more economically and with far shorter lead times.”
Caterpillar shares similar sentiments on the aftermarket side, relying on these printed parts to keep older machines up and running. The company also uses this technology to create and test out new features.
“We have a strong aftermarket business and always work to make sure our customers stay productive and keep their machines running,” says Stacey DelVecchio, additive manufacturing product manager for Caterpillar. “There are older machines out there that we still support, and they need parts. Unfortunately, suppliers may go out of business or tooling has been scrapped and it’s going to cost quite a bit of money or downtime to order or find a suitable replacement. Financially it makes sense to print the parts versus having to purchase the minimum quantity of a part.
“Another use is in new product development,” DelVecchio adds. “We can take a part or feature from the very beginning of its life cycle and create it. Say it’s some sort of engineering feature that may help with fuel economy or prolong the lifespan of a product, we can design in a feature that really could only be printed. So, it may be a case where we had always wanted to do something with the product, but we could never manufacture it. 3D printing gives us an avenue to manufacture that component now that we couldn’t have done before.”
So, what parts are manufacturers printing? It varies by company. Currently Volvo prints only in plastic and sticks mostly with parts related to the cab. However, it’s looking into expanding its capabilities with steel printing and creating tools for its dealers.
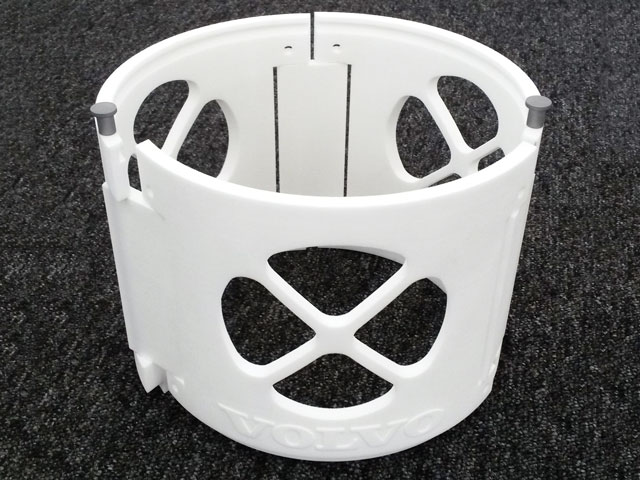
At Volvo, a workshop tool for mounting parts on an axle was made using 3D printing.
Caterpillar offers nearly 100 approved-for-use printed parts created with a mix of materials.
“We have a little bit of everything,” says DelVecchio. “One thing that makes Caterpillar unique is that we actually do have parts that are approved for use on our vehicles. We have about 100 parts that are approved — mostly aftermarket — and they’re a combination of plastic and metal parts. We also heavily use 3D printing for prototyping. The biggest change I’ve seen in the past two years is in the prototypes. They are functional prototypes, so we can actually turn on the vehicle and use the machine versus just a prototype as something to look at. When I look at what’s coming on the horizon, I think we’ll see more of the parts being approved because the printers are getting better and more robust. Not to mention, there are more materials for us to choose from. As those capabilities increase, the parts will become more cost competitive.”
Speaking of cost, curious minds (and potential buyers) want to know: How much do printed parts cost vs. traditionally manufactured ones? Well, the answer isn’t that simple.
“It’s hard to give a definitive answer as it changes on a case-by-case basis,” says Fredrik Andersson, development engineer for Volvo. “The state of the production tools or the particular specifications for the parts all factor into the total cost, but in general it’s likely to be the same or lower.”
Caterpillar weighs in with its perspective.
“When you try and compare a traditionally manufactured part to a printed part, it’s frequently not an apples-to-apples comparison,” explains DelVecchio. “In order to really take advantage of the technology, you should be changing something in the process. For example, if a traditionally manufactured part has a big chunk of metal in it from the casting process, you wouldn’t print it that way. If you did, you’re not taking the full advantage of 3D printing.”
From a durability perspective, manufacturers are finding success with 3D printed parts and their ability to mimic the strength of conventional pieces. Plus, the technology and options are only getting better and allowing even stronger parts to be produced.
“All the 3D parts we offer are made to be the same as conventionally manufactured ones — there are no major differences in the way they function,” says Andersson. “Some parts require specific materials, shapes or production methods to perform at the required level, while other parts can sometimes perform even better with alternative materials and production methods. It really comes down to making sure the part does the job it is intended to do in the best possible way. For a simple job, you might have the choice of several different methods.”
DelVecchio adds, “It is material dependent as far as how they compare from a strength perspective. At Caterpillar, we do an analysis of the material properties and write a specification for it, which is fairly standard type of work. We’ll only use it if those properties are similar to mechanical properties we can get from another manufacturing method. I have never worked on something where there is so much innovation and advancement happening month after month. The materials are always changing and only getting better.”
From the ability to offer aftermarket parts to designing future machines, manufacturers are finding and reaping the advantages of 3D printing. As more companies adopt this technology into their manufacturing processes, the industry will only continue to benefit.
“The fact that you can come up with an idea one day and then quickly and inexpensively provide a working prototype to bring to the boardroom the next day is a huge advantage,” says Kalfholm. “But to make the best use of additive manufacturing, it has to become a part of the production method from the very birth of the machine and its parts. When the part design is final, there is only so much freedom when trying to manufacture in this way, but when 3D printing becomes part of the initial design process we will soon start to see new and more liberating designs. It’s a learning curve, and we need to be constantly on our toes when coming up with new ways to work.”
The World’s First 3D-Printed Excavator Unveiled at CONEXPO-CON/AGG
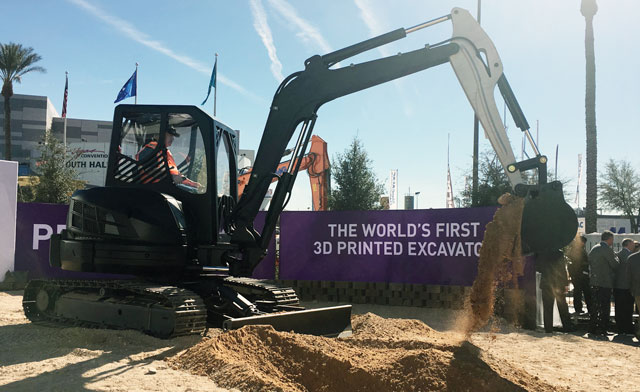
Project AME made its debut at CONEXPO-CON/AGG and IFPE 2017 in Las Vegas.
Attendees who visited CONEXPO-CON/AGG and IFPE 2017 in Las Vegas had the opportunity to see the world’s first 3D-printed excavator at the event’s inaugural Tech Experience. The Association of Equipment Manufacturers (AEM) was part of the team effort that developed that 3D-printed excavator. Known as Project AME (Additive Manufactured Excavator), the excavator was 3D printed using a variety of machines to create and assemble three components: a cab, a boom and a heat exchanger. The excavator’s boom was fabricated using a cutting-edge free-form additive manufacturing technique to print large-scale metal components.
Read more about Volvo CE and Caterpillar.