Compact Wheel Loader Dictionary: Let’s Learn About CWLs One Term at a Time
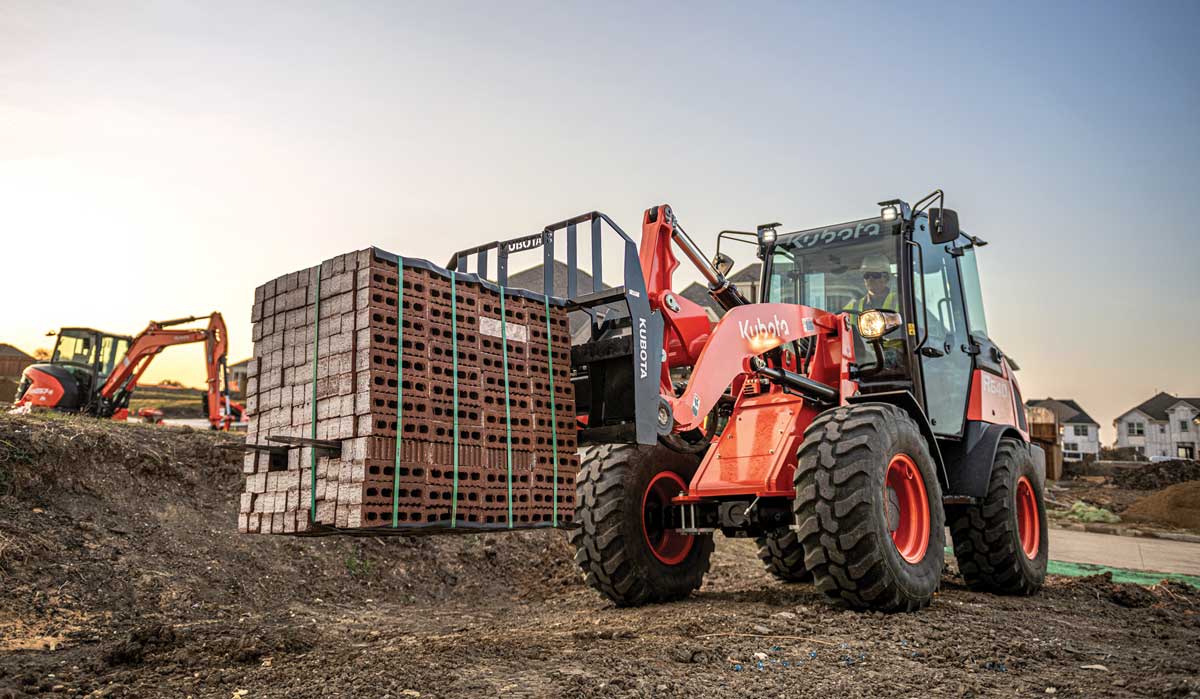
Wheel loaders are certainly not new to U.S. contractors, but compact wheel loaders are a category still gaining acceptance in America’s skid steer/track loader-dominated marketplace. They definitely offer some advantages over their skidding, zero-turn competitors. Most compact wheel loaders articulate or use all-wheel drive which is easier on tires, easier on turf and better on fuel. Other advantages include better visibility, faster ground speeds, serious ground clearance, longer wheelbases for better ride quality, greater lift capacities and higher lifting ability. These advantages are why small wheel loaders are gaining more work and acceptance in applications ranging from snow removal to landscape supply shops.
Of course, compact wheel loaders have tons of options and technologies, allowing owners and operators to outfit them for specific applications: various linkages; ROPS or deluxe cabs; high-lift or telescoping booms; assorted attachment couplers; loads of machine automation; and way beyond. A lot of these systems differ from a skid steer or track loader, so to help those both familiar and unfamiliar with the compact wheel loader category, we have compiled an easy-to-reference dictionary full of popular terms, explaining the wide range of systems, technologies and choices in the small wheel loader realm. We’d like to give a big old thanks to all the manufacturers — from Kubota to Cat — who helped pull this word party together. Let’s begin with…
Articulating Joint
Compact wheel loaders offer a unique solution for customers who need a machine with superior material-handling capabilities and high maneuverability. One of the key points of differentiation between these machines and others in the marketplace is their unique articulating joint. A compact wheel loader is composed of two separate frame components joined by an articulation joint, which offers several benefits. The articulation joint makes the compact wheel loader highly maneuverable while minimizing ground disturbance on soils and reducing tire wear on asphalt/concrete surfaces. In addition, it enables the rear tires to match the path of the front tires when turning, helping this highly nimble machine to navigate around obstacles and perform well in confined work areas. — Mike Fitzgerald, Marketing Manager, Doosan Bobcat North America
Attachments
Operators looking for more versatility with their compact wheel loader can utilize different types of attachments beyond the standard buckets and pallet forks. Grapples and grapple buckets are popular options for land clearing and debris cleanup. For road applications, cold planers and vibratory compactors help get the job done. For further versatility, bale spears and grab attachments can be used in agriculture applications while landscape tillers and rakes, augers, trenchers and soil conditioners excel in the landscape industry. For each application, be sure the auxiliary hydraulics are matched with the attachment for maximum productivity. Snow clearing is another popular category, using attachments such as snow throwers, sweepers and snow pushers. Wheel loaders have excellent visibility, making them a perfect choice for the application. Operators planning to complete many different jobs with their compact wheel loader should consider a hydraulic skid-steer-style coupler for quick change-outs and auxiliary hydraulics to give the attachments extra power. — Frank Gangi, Product Manager, Compact Wheel Loaders, Yanmar Compact Equipment
Buckets
It’s no surprise that a bucket tops the list as the most popular attachment for compact wheel “loaders.” It’s right there in the name. Operators use them to dig, load, scrape and spread materials on all sorts of jobsites in ag, snow removal and construction. Most companies selling compact wheel loader buckets will offer general purpose, light material, snow, flat floor and multipurpose buckets. There are also grapples and grapple buckets. Bigger loaders in niche applications can employ all types of unique buckets for coal, sand, gravel and trash handling, and there are also some unique choices like a side discharge bucket that is designed to collect and transport loose materials such as sawdust, sand, mulch and topsoil and then discharge these materials via a belt-type conveyor from adjustable openings (doors) on either side of the bucket. Regardless of size or type, picking the right wheel loader often boils down to the right bucket, the right amount of material (measured in cubic yards) that needs to be moved per hour, the weight of the material and the area that the loader will operate in. Correct bucket choice is paramount for this category of equipment. — Pam Kleineke, Managing Editor, Compact Equipment
Cabs or ROPS
The operator’s cabin is a central command center for controlling and operating the compact wheel loader, housing the mechanical and technical controls of the model and providing the operator with comfort and safety throughout the work. Compact wheel loaders that were designed with the landscape, residential and commercial construction operator in mind should provide operators with a panoramic perspective of the environment with enlarged windows and 360-degree visibility around the machine. When spec’ing out a cab, consider one that minimizes noise and vibration, offers a comfortable seat, has an adjustable steering column and provides climate control. Having frequently used controls in easy-to-reach places is ideal to reduce operator fatigue. Work lights aid in a wheel loader’s already impressive visibility. Many small wheel loaders also come with an industry standard rollover protective structure (ROPS) to protect the operator in the event the machinery rolls over. — Patrick Baker, Kubota Product Manager, Construction Equipment
Controls
With the various demands and circumstances from jobsite to jobsite, a compact wheel loader requires multiple functions, and all of those functions are connected to a system of switches, levers and buttons that power them from inside the cabin. A well-organized control console allows for easy training and increased productivity for the operator. To run the loader, there may be the option of a steering wheel or levers. With a multi-function control lever, operators can control forward, neutral and reverse, the differential lock and the wheel loader auxiliary port switch, making operation quicker and easier with all major loader and operational functions being accomplished with one hand. — Patrick Baker, Kubota Product Manager, Construction Equipment
Couplers
Most manufacturers offer two styles of compact wheel loader couplers: ISO or hook style and skid steer style. Depending on the definition of a compact wheel loader, manufacturers may also offer IT, fusion or pin-on couplers. The ISO-style coupler provides the highest bucket breakout force and operating capacity because the ISO-style coupler design positions the bucket close to the end of the boom, similar to a pin-on bucket. With the skid steer-style coupler, the bucket is positioned out a few extra inches, however the skid steer-style coupler is widely popular for the numerous attachment possibilities that can be shared with skid steer and compact track loaders. Regardless of the coupler style, the type and density of the materials that will be handled should be considered to determine the appropriate bucket or attachment. — Keith Gribbins, Publisher, Compact Equipment
Engine
The engine of the compact wheel loader is the main system providing all of the muscle (i.e. mechanical force and motion) needed for all of the applications that the loader is capable of performing. These are diesel engines ranging from 40 to 80 hp and above (depending on how you define compact or small). These clean and quiet diesels adhere to EPA-mandated Tier 4 engine regulations, engineered with aftertreatment technologies that sport names like exhaust gas recirculation (EGR), selective catalytic reduction (SCR), diesel particulate filters (DPFs) and diesel exhaust fluid (DEF). Each manufacturer applies these and other aftertreatment technologies to various power bandwidths, depending on the emissions regulations of each country. — Patrick Baker, Kubota Product Manager, Construction Equipment
High-Lift
High-lift compact wheel loaders offer additional inches of reach compared to standard models, enabling operators to maximize productivity with the ability to move faster while reaching new heights. The extended lift capacity of high-lift compact wheel loader machines provides operators with increased hinge pin height and dump clearance. When equipped with a quick coupler and bucket, operators can confidently lift heavy masses overhead, while comfortably reaching even higher heights on the jobsite. High-lift models not only offer operators increased height but also enable further reach for dumping or stacking, ag material handling, general construction or landscaping and snow removal tasks and easily dump to the center of tandem-axle trucks for quick loading cycles. — Luke Gribble, Solutions Marketing Manager, John Deere
Hydrostatic Transmission (HST)
This type of transmission uses hydraulic pump motors instead of mechanical gears to adjust the loader’s speed while maintaining engine horsepower and rpm output. The system’s variable displacement pump motor constantly adjusts hydraulic flow and power. When the system senses an increased load, the pump motor makes adjustments to maintain hydraulic horsepower without lugging the engine and without additional input from the operator. HST equipped wheel loaders allow for continuously adjustable speed using an acceleration pedal. Starting, acceleration and stopping are performed automatically. The advantages associated with an HST include ease-of-use, optimal controllability at extremely low speeds and on slopes, smooth automated speed control, as well as excellent traction at all speed ranges. — Hitachi Construction Machinery Americas Inc.
I hate to be the bearer of bad news, but sometimes you can’t have it all… unless you rent. From finding the right dealer to scoring the perfect rental machine, we have you covered!
Linkages
For compact wheel loader owners and operators, it’s super important to ensure the lift height and lift capacity will work with the material type and amount you intend to move. It’s important to consider the kinematics or linkage of the compact wheel loader. A parallel linkage would be the best option for pallet forks and grapples, whereas a Z-bar linkage is best suited for bucket work. Each configuration has pros. The Z-bar linkage is the traditional option, and it enhances breakout force. It is also easier to maintain, having the least number of pins, links and levers. But, Z-bar configs may have visibility concerns when using attachments, which is a big selling point for parallel-lift linkages. Parallel linkage gives a clear view through the lift arms, which is imperative when handling pallets, pipes or timber. Parallel linkage will also have parallel lift, keeping the attachment and load from tipping while lifting. — Keith Gribbins, Publisher, Compact Equipment
Pallet Forks
An ideal solution for rental, ag material handling, landscape and construction customers, pallet forks are a durable and powerful attachment option that help transport heavy loads on the jobsite. Knowing that pallet forks are staple attachments for customers, they are often designed with more-durable frames for years of wear and tear. Pallet forks come in a variety of widths such as 42-, 48-, 60-, 72-in. wide and onward. They are often categorized as light, standard and heavy-duty. If an operator needs to move a lot of material, they should understand the maximum and minimum weights they are working with to ensure they are using a machine and pallet forks that are able to support the necessary weight. Forks may feature extras like a brick guard, which provides added strength and smooth surfaces to offer protection against load damage. — Luke Gribble, Solutions Marketing Manager, John Deere
Rear Oscillating Axle
Some manufacturers offer a rear oscillating axle on their compact wheel loader to enhance stability and traction when working on uneven terrain. Unlike a traditional fixed axle, a rear oscillating axle is connected to the rear frame with an oscillation hub and has separate shafts to each rear loader wheel. During operation, the oscillating axle absorbs jolts caused by undulation to deliver a smoother ride for the operator, maintain traction and provide stable load-carrying control. — Hitachi Construction Machinery Americas Inc.
Specs
Like any equipment, compact wheel loaders have lots of specs — engine horsepower, operating weight, breakout force, bucket capacity, travel speed, turning radius, width, height and beyond. Boasting big ranges of operating weights between 4,000 to 20,000 lbs and lifting capacities from 4,000 to 12,000 lbs, compact wheel loaders are obviously big for the compact arena. Compact wheel loaders can wield hydraulic attachments in the 15- to 33-gpm range, with the ability to travel between different tasks at speeds over 12 to 20+ mph. Which specs are important? To simplify it, start out by focusing on loading (the major application). Selecting the right loader is often based on the amount of material (measured in cubic yards) that needs to be moved per hour, the weight of the material and the area that the loader will operate in. It’s important that you know how the loader will get the material, how quickly the material needs to be moved and where the material needs to go. Look for a brand that accommodates your bucket work. — Keith Gribbins, Publisher, Compact Equipment
Speed
Compact wheel loaders can motor. They are among the fastest construction machines, engineered to transport materials quickly and safely. Units can hit top speeds between 12 and 20+ mph. Machine speeds have increased to quickly transport material, and the introduction of ride control provides operators a shock-absorbing system that helps them to travel faster and maintain the bucket or attachment load. Before buying or renting, make sure you know both forward and reverse speeds, as they may differ. — Keith Gribbins, Publisher, Compact Equipment
Rimpull
The rimpull control feature on compact wheel loaders allows you to adjust the torque to match the underfoot conditions in order to minimize tire spin, ultimately helping you lower total owning and operating costs. Rimpull reduces the unnecessary wheel spinning and wear in poor or slick ground conditions. The result is less wear on the four tires and the driveline as well as less fuel spent. Performance is also enhanced. Rimpull gives better traction and better bank penetration, leading to decreased bucket loading time and improved fill factor. — Keith Gribbins, Publisher, Compact Equipment
Telematics
Telematics is a software designed to monitor a machine’s location and health remotely, tracking metrics such as hours, fuel level, location, temperatures, error codes and more. Telematics can help an owner more efficiently monitor their machine’s performance, a rental company monitor where a machine from their lot is at any given time and generally provide more peace of mind and added protection for your investment. This has become a must-have feature, and many manufacturers have made telematics standard on all compact wheel loader and construction equipment models. Telematics provide operators with the right information, when and where they need it all in one place, which is typically in an app available on an operator’s smartphone. — Patrick Baker, Kubota Product Manager, Construction Equipment
Telescopic Boom
With multiple sections that extend and retract, a telescopic boom on a compact wheel loader increases reach in jobsite applications while maintaining a relatively small operating footprint for tighter turning circles and improved access under space constraints. It is a highly versatile machine, pairing a wheel loader’s maneuverability with the reach of a telehandler, that delivers optimal productivity and value. In fact, many customers forgo buying either aforementioned machine with more specialized functions because of the telescopic boom’s versatility, achieving significant savings on initial purchase costs, maintenance and insurance over its lifespan. — Ethan Clowes, JCB Product Manager for Skid Steers, Compact Track Loaders and Backhoe Loaders
Warranties
Warranties are important for protecting your investment. Buyers should look for a warranty program that covers all the most common parts compact wheel loader operators may encounter issues with. Manufacturer warranties typically range between one to three years (2,000 to 3,000 hours). Depending on the type of work a contractor may be doing, they may also want to consider investing in an extended warranty. These types of warranties can vary greatly and include everything from extending the time and hours associated with a standard warranty to covering the costs of some preventive maintenance expenses. Many contractors choose to add an extended warranty package when financing to help reduce potential out-of-pocket maintenance expenses in the future. — Pam Kleineke, Managing Editor, Compact Equipment
Return to Dig, Parallel Lift and Programmable Kick-Outs
By Kade Lusk, Cat Product Application Specialist
One thing that is always brought up when discussing return to dig, parallel lift and programmable kick-outs is whether they are strictly creature comforts or a value add to the machine and, by extension, the application. Built-in technology-sensing linkage position allows for precise set point targets to give the operator total control on the go. This technology also dampens linkage movement when approaching cylinder stops and set point targets. The integrated technology is working for the operator behind the scenes to make work more efficient and with less fatigue on the machine and operator. A quick definition of each will demonstrate how their value will help you work smart and move more.
Return to Dig — By positioning the bucket with the desired angle of attack, the operator pushes a button to set and recall the desired position with certain joystick commands for precise settings in repetitive cycles like truck loading. This reduces cutting edge and bucket wear and allows the operator to focus on the next cycle.
Parallel Lift — Bucket, and more so, fork applications require precision throughout the lift cycle to manage the load and reduce material spillage. With linkage-sensing technology, the forks can remain parallel throughout the lift range without any extra input from the operator. This helps preserve damage to costly material that might fall from the forks or excessive site cleanup from spilled material in bucket applications, again saving time, money and excessive machine wear.
Programmable Kick-Outs — This is the same logic as return to dig but also adds lift and lower set points to be easily set by the operator with the push of a button to minimize excessive bucket wear when going into the pile (lower set point) and repeatably target a linkage height when dumping into a truck or when overhead height is a restriction (upper kick-outs). The bucket or forks can also be given a desired angle set point for repetitive work cycles. This technology dramatically reduces excessive bucket wear and helps with site safety. When all three are put together, the excessive wear on the bucket and machine are reduced as is operator fatigue, which leads to more money in your pocket at the end of the day and a more focused operator who is efficient and aware of site safety.
For reprint and licensing requests for this article, please click here.