Going with the Flow
When skid steers were first forged, they came with attachments. Back in 1957, when the forbearer of the modern skid steer was invented in Rothsay, Minn., by brothers Cyril and Louis Keller, the first units had only three wheels, a 6.6-hp Kohler engine and a rope starter, but they still took four attachments — a utility scoop, manure fork, snow blower and sweeper. From its creation, the skid steer was designed as a little loader and a big tool carrier. Today, it’s North America’s ultimate multifunctional machine. That’s because of its attachment system.
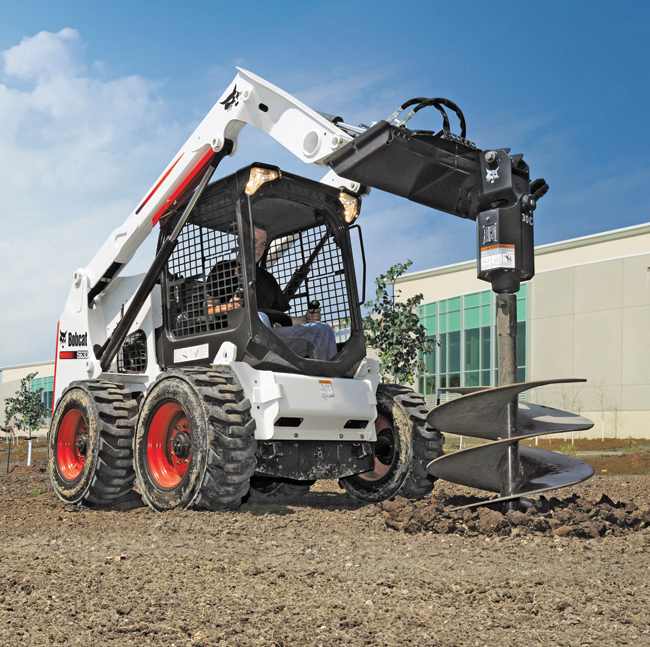
Of course the earliest skid steers could not even power those first attachments. They essentially had pin-on attachment systems with no auxiliary hydraulic technologies, and attachments were powered by the push and pull of the loader itself. It took a few decades to harness the high technologies of hydraulics. A whole new industry of skid steer engineers, attachment makers and hydraulic OEM experts emerged over the last three decades with the proliferation of skid steers using fluid power systems.
“The first widely available skid steer auxiliary hydraulics were used for powering cylinder-operated attachments such as grapple forks and hay buckets,” remembers Curtis Goettel, marketing manager at Case Construction Equipment (which has been building skid steers since 1969). “Powered attachments became common in the 1980s. By the mid-‘90s, nearly all skid steer manufacturers offered optional auxiliary hydraulics, but it wasn’t until about 10 years ago that auxiliary hydraulics became standard on skid steers.”
Over 50 years, the skid steer and its subsequent cousin the compact track loader have become some of the most recognized pieces of equipment on the construction site, landscape project, farm yard and rental lot. That has a lot to with its utilitarian nature. The rise of hydraulics has made skid steers and compact loaders kings of attachments. Whether it’s a massive cold planer to strip asphalt, a serious stump grinder to remove old trees or a large wood chipper to dispose of the debris, there are as many attachments as applications on the skid steer market.
“Over time, versatility has become a hallmark of the skid loader,” says Sean Bifani, product manager for skid loaders and compact track loaders at Mustang Mfg. (which makes 10 skid steers and two track loaders today). “Hydraulic systems have evolved to include standard- and high-flow auxiliary hydraulic configurations, mechanical and hydraulically-powered quick-attach options and pressure-relieving coupler systems. As technology has improved, skid loader hydraulic systems have become more efficient and more advanced. Though still operating on many of the same principles, pumps and valves are now being designed to operate at higher pressures for maximum efficiency. Equally important, they are requiring less horsepower in smaller physical packages.”
How Does It Work?
The steely heart of a skid steer is a diesel engine. That diesel power plant pumps energy to all of the machine’s many wheels, tracks, loader arms, attachments and other functions. In the belly of the beast, this diesel engine transmits its energy to a set of hydraulic pumps bolted directly to the output of the engine. A total of up to four hydraulic pumps hooked up to the engine power the loader arms, hydraulic drive motors, auxiliary hydraulic circuits and the unit’s attachments.
Most skid steers on the market utilize two hydraulic pumps to achieve the optimum balance between driving and lift arm and attachment functions. These are generally referred to as the main pump and the auxiliary pump. The main pump provides power to hydraulic drive motors, which in turn provides power to the axles and wheels. The auxiliary pump provides direct oil flow to the lift arm and hydraulic attachment operation.
“The powertrain in a skid steer is a diesel engine, and the drivetrain comprises hydrostatic pumps and motors,” explains Mike Fitzgerald, loader product specialist with Bobcat Co., which introduced the first model of skid steer (the M-60 Self-Propelled Loader) in 1959. “In the drive system, it is common to use two drive pumps and two drive motors — one of each, for each side. For attachment operation and lift arm functioning, there is typically one hydraulic pump. Although some machines can utilize two or three, depending on the ultimate hydraulic needs of the attachments or machine.”
In most types of pumps, the flow rate is determined by the pump’s speed (which is equal to the speed of the engine) and its displacement (the volume of the cylinders in the pump). The faster a given pump spins, the higher the flow rate. The pressure is determined by the tasks the operator is performing, the attachment he or she is using and the flow system of the skid steer or track loader.
“In simple terms, an attachment that uses hydraulic power requires a fluid medium that is charged by a hydraulic pump,” says Bifani. “The pump pressurizes hydraulic fluid using power from the engine. The fluid is directed toward an attachment through a control valve. Energy that is created in the system is used to the fullest extent of the capabilities of the attachment, with remaining fluid returning to the hydraulic tank. As a generalization, flow and pressure are equally important. Flow creates speed, while pressure creates work.”
Walk onto a dealer lot today and you’ll see that hydraulic systems come in two configurations — standard flow and high flow. Standard-flow auxiliary hydraulics generally range from 10 gallons per minute (gpm) on smaller skid steers to 32 gpm on larger models. High-flow auxiliary hydraulics typically range from 31 to 41 gpm, providing more flow to get work done with bigger, more complex implements. Customers pay approximately $1,600 to $1,800 extra to equip a skid steer with high-flow hydraulics, but customers are demanding it more and more. Flow rates overall are a growing trend.
“Standard flow rates — gpm of oil flow — have increased over time as have hydraulic pressures,” says Perry Girard, marketing manager of parts and service at Case Construction Equipment. “An attachment’s requirement is measured in hydraulic horsepower. This is a number that is a result of both pressure and flow. Increasing one or the other or both will deliver more power for the attachments. The hydraulic pressures in early machines were 1,500 to 2,000 psi systems. Now 3,000 psi is common across the industry, and enhanced high-flow systems can reach 4,000 psi. Flow rates have also gone from 15 gpm to as much as 40 plus gpm on high-flow machines.”
Evolving Options in Hydraulic Power and Efficiency
Skid steers and track loaders continue to find high sales numbers and new markets. Depending on the year, sales for new skid steers can range dramatically — from 20,000 to 70,000 units in North America alone. New compact track loader sales can range from 5,000 to 20,000 units. Both rely heavily on the homebuilding markets, but that’s changing. Because of the diversity of hard working, high-flow attachments, skid steers and track loaders are migrating into lot clearing, road construction, design/build landscaping, disaster relief work and loads of other industries.
Easy-to-use attachments are a big part of the category’s growing popularity. Quick-attach systems have been standard on skid steers for decades now, but most manufacturers also offer quick-coupler systems with hydraulic pressure release technologies. If you’ve ever changed an attachment, you know trapped line pressure can make hydraulic attachment changes time-consuming and frustrating. Simplify the process with a coupler that has a hydraulic pressure release, allowing the user to swiftly switch from bucket to broom easily. As you push the coupler, hydraulic oil releases through a return line back into the machine. The system provides easy, clean attachment changes.
If it’s a non-hydraulic attachment, you can even swap attachments without leaving your seat. Optional power mounting systems allow the locking wedges (which secure the attachment) to hinge and unhinge from the cab seat. Push a button and an operator can lock and unlock the levers, dropping the attachment and securing the next one. For hydraulic attachments, operators still must shut off the loader and exit the cab to complete the changeover of hydraulic lines.
Operating attachments has become as easy as taking them on and off. Big, demanding and complex implements like tree spades, cold planers and grading machines can now be operated with the help of a digital interface, which can control the speed and flow of the attachment or the speed of the actual skid steer or track loader. Matching travel speed or attachment speed with the job requirements allows you to maximize attachment performance, decrease the chances of stalling the machine, reduce fuel consumption and reach top productivity.
“Advances in hydraulic technology provide an enhanced operator interface with the skid loader and attached implements,” says Bifani. “This facilitates better productivity and often more professional results. This is achieved by more precisely managing hydraulic flow and power to the attachment and the carrier drive motors. On modern designs when equipped, different settings can be managed by the operator, or functions can often be monitored and controlled through programming. While many operators embrace this level of control, many others prefer more simplistic and traditional systems.”
New school operators usually use joysticks with fingertip hydraulic controls, making attachment operation more precise and comfortable, even allowing attachment adjustments as you drive. Detent features allow continuous attachment flow without having to hold the switch. Flow goes both ways too, so lock the flow in the opposite direction for sweepers, soil conditioners, tillers and other attachments that operate in both directions. Variable and max flow options provide full control of cylinder adjustments, so you can slowly adjust grapples and combination buckets with the variable, featherable flow, and then engage the maximum flow rate to shake dirt from your trencher teeth.
“The compact equipment industry is continually looking at how contractors utilize their skid steers and track loaders,” explains Fitzgerald. “Today, Bobcat provides communication between specific attachments and the machine to help operators understand — like our new laser grader system available on M-Series loaders and our deluxe instrumentation panel. These aren’t really auto-pilot features, but we’re moving in that direction.”
Today, companies like Bobcat offer more than 80 attachments for its compact loader lines, many of which are unique to the company. Augers, backhoes, blades, brooms, breakers, cement mixers, log splitters, mowing decks, planers, silt fence installers, snow blowers, stump grinders, tree shears, trenchers, vibrator rollers, wheel saws and wood chippers are only a handful of the attachments available to skid steer and track loader owners and operators today. Finding the most unique and hard-working attachments is another story altogether, but to match your skid steer or track loader to the size and flow of your new attachments, make sure you check with your dealer and operator’s manual.
“You need to match the attachment to the overall machine size, as well as the flow and pressure capabilities to the machine’s hydraulic system,” says Fitzgerald. “For example: It doesn’t matter what type of attachment you’re using, if you put on a low-flow attachment and turn on the high-flow, something will go wrong. Understand how your loader’s hydraulic system works, and you’ll understand how to get the most out of your attachments.”
Keith Gribbins is managing editor of Compact Equipment, based in Peninsula, Ohio.