Dirty Diesel and Tier 4 Engines
Today’s contractors have access to some of the cleanest diesel engines ever built. These new power plants are nothing short of amazing. Buy a new skid steer, mini excavator or utility tractor and find the next generation of awesomely engineered, emissions-compliant diesel engines, designed over decades to not only burn cleaner, but maintain fuel efficiency, add power and decrease noise and vibration. But like most evolutions in equipment, there’s going to be a learning curve for owners and operators.
Since these new engines barely emit emissions, they require new and more demanding technologies than previous diesel engine ancestors. For starters, these new diesel engines rely on a whole host of new after-treatment and fuel injection systems. These new systems are very precise and complex, and in order for them to work properly, they absolutely need clean fuel.
“It’s my No. 1 concern,” says Eric Burkhammer, regional sales manager with the Manitou Group (owners of the Gehl and Mustang brands of compact equipment). “A customer must understand the vulnerability that comes with the delivery process of diesel fuel — just like you have to teach people to do their reburns or regeneration. This is one that you almost want the guy to sign off on. That you told him he needs to go home and check his fuel distribution system before he ever puts fuel in that piece of new equipment. I don’t feel anybody’s really taking an aggressive step to say, ‘Hey, look folks, clean diesel is one of your new biggest concerns.’”
Most of the media attention so far has gone to the sophisticated after-treatment systems on these new engines — technologies like cooled exhaust gas recirculation (EGR) and selective catalytic reduction (SCR). These relatively large, complicated and expensive systems clean the engine exhaust, yet before the fuel can even be burned and the subsequent exhaust treated properly, the fuel must first reach the combustion system safely and accurately.
To supply just the right amount of fuel, highly-advanced, electronic, common rail direct injection technologies have replaced the old mechanical indirection injection systems of yore. Tier 4 engines today use a high-pressure fuel rail that’s engineered with computer controlled electronic injectors, which completely atomize the fuel for an ideal, clean, powerful burn.
Those common rail fuel systems and those high-pressure injectors have an increased susceptibility to fuel contamination — water, dirt, rust, sludge and other impurities.
“Moisture and debris have always had the potential to cause damage to fuel system components,” says Charles Klose, fuel systems technical lead at John Deere Power Systems. “But with the high-pressure fuel systems featured on Interim Tier 4 engines, it is more important than ever to use high-quality fuel filters and employ adequate filtration on fuel storage and transportation tanks. The consequences of using improper or tainted fuel can vary dramatically depending on the type of fuel used.”
Since the Clean Air Act of 1990, both gas and diesel engine manufacturers of construction equipment have been designing new engines to comply with government-imposed emission regulations called Tiers, vastly reducing the amount of pollutants released into the atmosphere such as soot. The most intensive of these EPA Tier regulations arrived in 2012 (called Tier 4), aimed at cutting emission levels from construction, agricultural and industrial diesel-powered equipment by more than 90 percent. These new Tier 4 regulations are split into two standards called Interim and Final (that difference is explained on page 22). These standards will radically change the way construction machinery works, but only if we know how to use them correctly.
Maintaining Good Internal Fuel Distribution
It’s not like Tier 4 diesel engines are unprepared to tackle tainted fuel. They are engineered with water separators and fuel filters, which are essential parts of the internal fuel distribution system. On a skid steer for example, diesel fuel will often travel through seven systems, going from: 1) the fuel tank; 2) through the fuel filter; 3) into the electronic priming pump; 4) through the water separator; 5) into the common rail pump; 6) into the pressure rail; and 7) finally shooting through the injector. This advanced fuel delivery process gives the machine a cleaner burn, better fuel economy, increased performance and even quicker start-up times.
“Engine manufacturers require fuel instantly — from key on,” explains Paul Puleo, national sales manager for Motor Components LLC (a global leader in manufacturing electronic diesel priming pumps). “The fuel system must be pressurized and primed instantly when the operator turns the ignition key on. As the electronic priming pump is energized, the entire fuel system is operational. In the old days, the operator would allow the engine to crank until the mechanical fuel pump [which was mounted on the engine] eventually primed, sending fuel to the injectors. Now with the common rail systems and their high-pressure injectors, fuel is required before the engine cranks and the electronic priming pump is often required.”
This priming process includes two major filtration points to clean fuel, including the appropriately named fuel filter. Because today’s fuel injectors have close-fitting parts, they become easily clogged by dirt and grit. Instead of creating a fine spray of fuel that burns completely, they start to produce a stream that doesn’t completely ignite. Changing the fuel filter keeps the injectors clean longer, which means more power and better fuel economy.
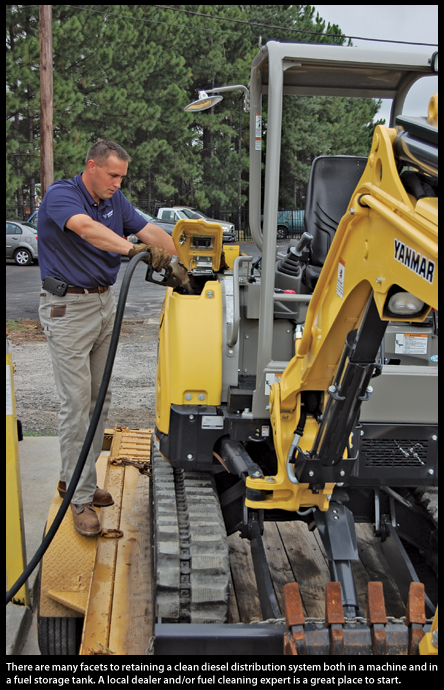
If fuel sits long enough in a storage tank, diesel can also become contaminated by water; diesel fuel absorbs water more than gasoline does. For this reason, most diesel equipment features a gadget called a water separator that collects water from the fuel. Although a few water separators are self-cleaning, most need to be manually drained. You just turn a little drain valve called a petcock and empty the water from the collection chamber of the separator. It’s a good idea to check the water separator weekly at first to see how fast it fills up under normal conditions when operating on fuel from your usual source.
“Water should be the primary focus when selecting additional filtration for a storage tank,” explains Klose. “Additional debris filters should be appropriately sized and target large particles — those with 30-, 50- or 100-micron ratings — with the primary benefit begin extended filter life on the equipment. Our Interim Tier 4 engines feature primary fuel filters with multi-layer media. This filter construction allows for greater ability to hold debris in the system and provides improved filter life with a higher degree of particle separation efficiency.”
But it’s not just the external containments in fuel that can create problems in a new Interim Tier 4 engine. Sometimes contaminants actually come from the internal fuel system. It’s a fact that both engine manufacturers and fuel system designers are slowly discovering as these new Interim Tier 4 engines start working on actual jobsites out in the field.
A good example is Bosch, one of the world’s biggest suppliers of automotive and off-highway equipment parts. Bosch recently released an announcement warning original equipment manufacturers of diesel fuel systems that all component surfaces in direct contact with diesel fuel must not contain copper, zinc or lead (as far as technically possible). Copper-containing materials in particular act to catalytically accelerate the aging process of diesel fuel. The resulting fuel aging, especially with admixtures of FAAE (fatty acid alkyl ester, a diesel blend component) can lead to deposit formation and corrosion inside the fuel injection equipment.
“In addition to dirty particle containments, there is also material containments that affect the injection system,” says Puleo. “They’re reasoning is that over time these materials can leech and cause the injection nozzles to clog. Motor Components has designed diesel priming pumps to comply with Bosch requirements due to the fact that Bosch injection systems are installed on many Tier 4 engines. So when a customer, whether it’s an engine manufacturer or an equipment manufacturer, request a priming pump and requires it to meet the suggested Bosch request, we have them ready for installation.”
Keeping Diesel Clean
Regardless of the type of diesel fuel storage onsite, fuel contamination is always a possibility and an eventual reality. It could be a below- or above-ground system, horizontal or vertical tank, single- or double-walled design, or a steel, concrete or fiberglass construction. It doesn’t matter. If diesel sits long enough, it will become contaminated. It starts with how diesel is refined and a process called carbon cracking.
“Carbon cracking came about after the fuel crunch in the ‘70s,” explains Dan Weeden, owner of Perfect Fuel Preservation (a diesel fuel polisher and cleaning expert working around Toronto, Canada). “Basically, it allows the refineries to take carbon molecules that would normally go to the use of asphalts and plastics and break them in half and break them in quarters. The purpose is to get more fuel from the available crude.”
Unfortunately, when you break a carbon molecule in half it begins to spin. If you put a carbon molecule in rotation, it’s going to get a positive or negative charge. Eventually, all of these little carbon molecules made from diesel cracking all go into a diesel storage tank and sit there. As positives and negatives start to become attached to each other, chains begin to form.
“Those chains get longer, and they start to form a dark fuel,” says Weeden. “As they agglomerate more, they settle at the bottom of the tank as sludge. So you have to take that fuel and send it through a very specifically designed magnate that takes those little molecules and breaks them up and pulls them apart again. That’s how you’re supposed to polish diesel fuel.”
Weeden’s company is one of many across the United States and Canada that specialize in polishing and cleaning diesel fuel storage tanks and educating contractors and fleet managers on the dangers of dirty diesel. These clean diesel professionals can set up automated fuel cleaning systems, do yearly fuel analysis, add biannual fuel conditioners or just come out and clean your old, rusty diesel deathtrap. The first step in evaluating if you need these services is to take a fuel sample.
“First, you just take a look at the fuel,” explains Weeden. “You don’t really need to do a whole analysis. If you take a sample off the bottom of the tank and have a look at it, generally it will look clear and bright. Our diesel in Ontario is generally red. The color varies from province to province and state to state. But if your diesel shows various degrees of darkness or cloudiness, you have water, micro-activity or contamination, and you need to treat it accordingly.”
Adding a conditioner every six months to the tank will usually keep it clean. To filter already dirty fuel, diesel experts will use innovative machines that often combine cleaning fuel with polishing it. Manufacturers like ALGAE-X International, Dieselcraft and FuelTurbo all build turnkey, mobile portable systems for diesel cleaning, diesel polishing, diesel tank cleaning and algae contamination removal. Systems draw the fuel out of the tank and into a machine that has separate stages of fuel purification, using spinning water separators, strong magnetic polishers and fuel filters (while adding catalysts and conditioners to help clean and lubricate the diesel). The tank is rarely emptied. Instead, fuel is siphoned and re-circulated.
“If you’re removing water, you remove water at a very slow rate,” says Weeden. “We put a little PVC tube down to the bottom of the tank with a little bevel cut in it. We turn the pump on and let it very slowly draw water that’s sitting at the bottom of the tank up the tube to a disposal container. If you suck the water up too fast, the fuel will collapse around the water, and you’ll start throwing fuel out of the tank.”
Just be careful not to over-clean the fuel. You can actually change the ASTM specs on the fuel with too fine a filter, losing its burning and lubrication properties. Consult a local diesel expert first. He or she will explain that nearly all the sulfur has been taken out of diesel today. That’s why it’s called ultra low sulfur diesel (ULSD). Sulfur acted as a lubricant, so it’s been replaced by waxes and additives to help lubrication and those can be filtered out.
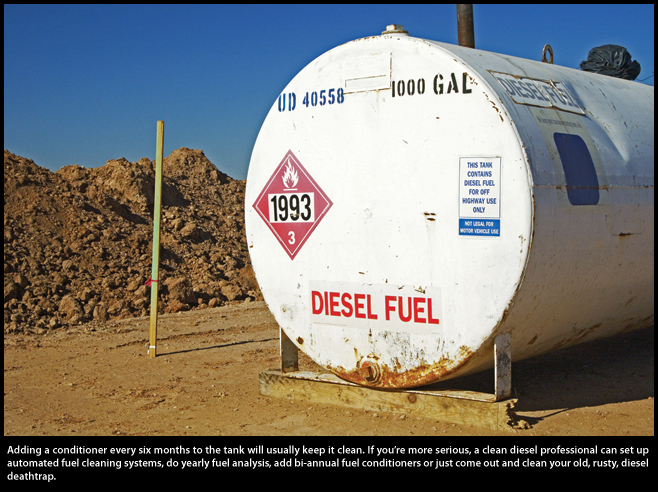
“The ultra low sulfur diesel fuel used today also has greater solvency than low sulfur diesel,” says Klose. “ULSD could initially require more frequent fuel filter changes as it cleans out debris present in older fuel tanks and storage and distribution systems.”
There are many facets to retaining a clean diesel distribution system both in a machine and in a storage tank. A local dealer and/or fuel cleaning expert is a great place to start. New Tier 4 diesel engines are more complex, but manufacturers have made extensive efforts to train dealers, educate customers and sell truly user-friendly engines. To keep those new diesels humming, owners, operators and fleet experts need to consider the quality of fuels more than ever before.
“These engines and new products have changed the face of the equipment market dramatically,” says Burkhammer. “These new engines are so much cleaner and more efficient. Engine manufacturers have done an amazing job. Now we need to do our job and keep those engines running properly, which means using clean diesel. Cleaning your diesel storage tank is a great start, but the next question is: When’s the last time you cleaned the fuel cell on your service truck?”
Keith Gribbins is managing editor of Compact Equipment, based in Peninsula, Ohio.
Ultra Low Sulfur Diesel
Alan Parker, Engineering Manager with Yanmar America Corp., Answers Our Diesel Questions
Why is ULSD required for Interim Tier 4 engines?
Ultra low sulfur diesel fuel [less than 15-ppm sulfur] was introduced into the market between 2006 and 2010. ULSD allows the engine manufacturer to develop advanced emission control systems in order to meet EPA and CARB [California Air Resources Board] emission regulations. Sulfur acts as a poison to after-treatment catalysts. Exposure of catalysts to higher sulfur content can quickly and significantly reduce the efficiency of these devices, resulting in increased emissions.
Does ULSD offer better performance?
Cetane number is an indicator of the diesel fuel’s efficiency or how fast the fuel will create pressure after it is injected into the combustion chamber of the engine. Experience from commercially available fuels is that the introduction of ULSD has not affected cetane number. But while the introduction of lower sulfur fuels may not reduce performance directly, complying with new emission regulations may affect performance in certain parts of the engine’s power curve. However, advanced engine controls may provide the engine manufacturer the ability to fine tune fuel injection, power and fuel efficiency.
What insights can you offer contractors about keeping ULSD clean?
High pressure fuel injection systems using fuel injectors with small orifice sizes may require tighter control of fuel quality. These engines may use a fuel filter and water separator that remove fine dust particles more efficiently. Always follow the requirements for fuel and oil established by the engine manufacturer. These requirements are established to ensure compliance with emission regulations and a long and useful life of the engine.
EGR vs. SCR
Explaining the Two Big Technologies in Tier 4 After-Treatment Devices
For Tier 4 there are two primary technology paths engine manufacturers will use to reduce nitrogen oxides (NOx) and particulate matter (PM). The first is with cooled exhaust gas recirculation (EGR) and an exhaust filter. EGR lowers NOx and the exhaust filter reduces PM. The second way to reduce emissions is with selective catalytic reduction (SCR) and a diesel oxidation catalyst (DOC). The SCR system lowers NOx while the DOC reduces PM.
Cooled EGR is essentially the opposite of SCR. Cooled EGR cools and mixes measured amounts of exhaust gas with incoming fresh air to lower the engine’s peak combustion temperature, thereby reducing NOx to an acceptable level. Because of the lower combustion temperatures used to reduce NOx with the cooled EGR approach, there is an increase in PM. To reduce PM to acceptable levels, exhaust gases are routed through an exhaust filter, located downstream of the engine, containing a DOC and diesel particulate filter (DPF). PM is trapped in the filter and — through a process called passive regeneration which utilizes normal engine exhaust temperatures — the PM is oxidized into nitrogen gas and carbon dioxide, then expelled through the exhaust pipe.
With the SCR approach, the technology increases the peak combustion temperature in the engine and the result is less particulate matter but NOx levels are increased. If mandated PM levels cannot be achieved, any further reduction in PM is accomplished by a chemical reaction in a DOC. To reduce the higher levels of NOx, a diesel exhaust fluid (DEF) is injected into the exhaust downstream of the engine. When the exhaust gases combine with the DEF in the SCR catalyst, NOx is broken down into nitrogen gas and water vapor and expelled through the exhaust pipe.
Interim vs. Final Tier 4
By Charles Klose, Fuel Systems Technical Lead at John Deere Power Systems
We’ve seen some confusion in the marketplace amongst end-users regarding Tier 4. It might be advantageous for readers to distinguish between Interim Tier 4 (IT4) and Final Tier 4 (FT4), their respective emissions requirements and implementation dates. Final Tier 4 for engine power ratings between 25-74 hp goes into effect in either 2012 or 2013, depending upon the option engine manufacturers elected to take under the EPA regulations. Option 1 mandated reduced particulate matter (PM) levels in 2008, but allowed delay of FT4 until 2013. Option 2 did not mandate a reduction in PM levels in 2008 for that power range, but required that manufacturer’s meet FT4 in 2012. For all engines 75 hp and above, the FT4 regulation doesn’t take effect until 2014 or 2015, depending upon power range.