Trick-Down Tech: The Impressive Automation, Analytics and Operational Systems Migrating to Smaller Machines
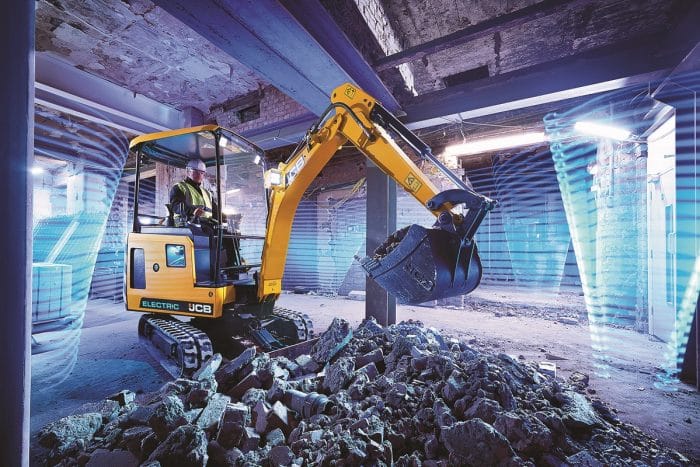
It takes money to develop technology, and those R&D costs are better applied to large equipment that costs more. Eventually the R&D investment is amortized and the cost of adding the feature drops significantly. It’s still not zero dollars because there are hardware and other costs, but it is significantly less.
One major benefit of this approach is that new technology often arrives with quirks and glitches that need to be addressed. That fine-tuning of features is completed before those features make their way to smaller machines; the technologies are mature by the time they appear on compact equipment. One example would be electrohydraulic joysticks. The early iterations lacked feedback; operators felt detached from the machine. Engineers hadn’t adequately addressed the science of haptics, which is the sensory feedback we get from devices, and had to improve that part of the operator experience.
The underlying technology of EH is different from pilot controls and radically different from mechanical controls and no amount of fiddling will get EH controls to feel exactly like either of those. But engineers improved the feel, operators adapted to the nature of EH and the technology is now embraced by most operators. In a simple world all tech would follow this path: Start on big machines, pay off the development costs, move down to smaller machines. But ours is not a simple world, and there are several confounding factors.
All Those Confounding Factors
A dozer in a quarry does two things: rips rock and pushes rock. Compact equipment commonly do many things. It’s true that some skid steer loaders only load, but it’s not hard to find owners with a machine shed full of attachments that enable that skid steer to do many things. Developing tech for a dozer that does just two things for its entire service life can be simpler than developing tech for a skid steer that may do three things in one day and three totally different things the next.
Some compact equipment is used mostly like its bigger equivalents. Wheel loaders, for example. But one key appeal of compact equipment is its versatility, and that trait is the very thing that complicates tech development for smaller machines. Machine control works well on large machines and on smaller machines. But those smaller machines don’t derive the same value because they do things where machine control isn’t helpful. Machine control on your compact track loader is great for grading but is of no real benefit when running a rotary mulch head.
Some of the smallest compact machines lack the architecture needed for technology. Electronic engines and a CANbus (controller-area network bus) system are needed for most tech because most tech has electronics at its core. Mechanical engines cannot support electronic features. Electrohydraulic joysticks can be added to a machine with a CANbus and possibly to one with a mechanical engine, although that would not be cost effective. Some of the smallest contractors don’t see value in technology. The ability to tailor response curves using EH joysticks and an interactive monitor may have little value to the owner-operator who is at one with his skid steer the way it is.
Economies of Scale and Scope
These are two distinct economic functions. Economy of scale is selling more of a certain technology, thereby lowering the cost-per-unit of each installation. If it costs $1M to develop a feature and it is applied to one machine, that is a per-unit cost of $1M. If it is applied to 10,000 machines, that is a per-unit cost of $100 ($1,000,000.00 ÷ 10,000 = $100.00). Economy of scope is applying that technology to a new type of machine. If it were initially developed for skid steers and later applied to compact track loaders, that would be an example of economy of scope. So, if that $1M R&D cost were distributed across 10,000 skid steers and 20,000 CTLs for 30,000 total applications, the per-unit cost would be $33.33 ($1,000,000.00 ÷ 30,000 = $33.33). Yes, this is an oversimplification, but it is an adequate explanation.
What’s Here Now
EH controls have become commonplace, as have the menu of other features enabled by the same electronics that underlie EH. Responsiveness of key systems can be adjusted to meet operator preferences and applications. We have operator assist features such as return-to-dig. We have creep mode that limits travel speed while allowing full power from the engine and auxiliary hydraulics for such high-demand applications as cold planing and running a rock saw.
Telematics are arriving but haven’t come with the rush seen with electronics. Telematics help with diagnostics and PM planning. Some provide curfews and geofencing to limit unauthorized use of equipment. Although telematics can offer value to customers with smaller fleets, they’re of the most value to customers with fleets of many machines.
Advanced couplers are moving into the compact space, allowing the changing of attachments from the cab. Better lighting, reduced noise, better visibility from multiple cameras, heated and ventilated suspension seating, high-efficiency climate control and lower sound levels inside and outside the cab all found their footing in bigger machines before coming to compact equipment. Some features from the automotive world are showing up on compact equipment. Examples include rear object detection, courtesy lights that stay on for a period after shutdown so the operator can more safely exit the machine and leave the area and rotary knobs with push-to-select, often called haptic controllers, for improved menu navigation on the monitor.
Next to Arrive
AI service and diagnostic tools are coming soon. AI compares information specific to the customer’s machine to a large pool of data and uses that for diagnostics and to recommend repair procedures. The operator or service technician can query the AI tool with a text prompt, but the core of the process will be specific data such as fault codes. Machine control will continue to increase in the compact machine space. Attachments will become better integrated with their host machines. Many will have electronic communication with the host machine, and operating parameters such as hydraulic flow will be automatically set to match the needs of the attachment. Operator assist features will expand. Enhanced connectivity will provide real-time two-way communication for improved diagnostics and remote updates of software.
Impact on Business Operations
Operators and service technicians need to be trained on the new features. PM intervals may be longer, and diagnostics may be enhanced. Certain features will come to be expected in machines entering the secondary market, and machines lacking those expected features will have lower residual value. The overall impact will be noticeable but not disruptive. Here are some brand-specific insights from the experts who provided information for this article.
Case CE
Brady Lewis, product manager, emerging products and technology, Case CE, says Case SiteWatch telematics are included on every new machine. The dealer can be included on the network if the customer desires. He notes that “machine control” is a broad category. Laser and 2D systems are the least expensive with 3D machine control much more expensive. “Customers should look objectively at these features to decide whether they would add value to their operations.”
Develon
Jake Sherman, compact track loader and dozer product manager, Develon, says the company’s new DTL35 compact track loader is full of features, many of which came from other machines. Bucket shake came from blade shake on dozers. Ride control and hydraulic quick-couplers are standard. Return-to-dig and lift arm float are standard. A rearview (backup) camera is standard. The optional around view monitor (AVM) camera system with ultrasonic proximity sensors displays a 270° view of the machine’s surroundings.
Where’s the Tipping Point?
At what point does it make sense for contractors to fill their fleets with technologically advanced compact equipment? That’s hard to say because there are too many variables. Some are doing it iteratively, replacing one machine at a time. Some are doing it wholesale, often at the start of the snow season for contractors that offer snow removal services. Some are waiting for specific features to become available on the size and brand of machine they want. Do your homework. Run some numbers. Decide on the tipping point that works best for you.
Hitachi
Drew Norton, product specialist, excavators, says ConSite Air provides remote diagnostics to troubleshoot fault or error codes from the service shop, simplifying service and shortening downtime. Their 270° Aerial Angle system offers five viewing positions for increased safety.
JCB
Sam Wagstaff, general manager of product, JCB, notes that JCB LiveLink telematics are standard on new JCB machines. The thinking that led to the single-arm boom design on their skid steer and compact track loaders was first applied to larger machines. Extended-life pins and graphite bushings increase service life. He cites three areas that should be included when considering new equipment — productivity, maintenance and repair costs and operator experience.
New Holland Construction
Dan Kakareka, product portfolio manager, New Holland, says parent company CNH recently launched CNH AI Tech Assistant. It is available at more than 300 authorized agriculture and construction dealer groups around the world. “This tool enables dealer technicians to save time on repairs by providing fast and accurate answers to technical questions.” In the third quarter of 2025, New Holland FleetForce telematics will become My New Holland Construction. This app will allow customers to manage all their New Holland Construction equipment from the palm of their hand using a smartphone.
Richard Ries is a freelance writer for Compact Equipment.
Come learn the dos and don’ts of trailering compact excavators.