How does a fuel pump work in a piece of compact construction equipment?
Motor Components Explains the Heart of the Fuel System
The most reliable diesel engine in the compact construction equipment industry isn’t going to start unless it has fuel. It just won’t happen. The engine component that, on demand, gives cylinders and injection systems the combustible liquid they need to explode into action is the fuel supply pump. To troubleshoot a pump, it helps to understand them.
The function of the priming pump is straight-forward, almost literally: It pumps the diesel forward from the engine’s fuel tank to the motor where another pump injects it into the combustion chambers. The process is summed up in the slogan of Motor Components LLC, a market leader in manufacture of fuel pumps: “We Move Fuel.”
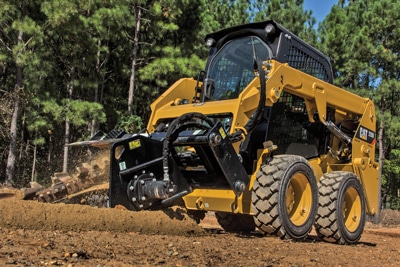
Fuel troubles? The first thing that must be checked is the fuel filter to see if it is clogged and needs replacement. If you put in a new filter and the engine is still hesitating, then obviously you need to change the fuel pump.
“There’s not much to explaining a fuel pump,” says Paul Puleo, national sales manager for Motor Components. “It is a pretty simple operation, moving fuel from point to point under a certain pressure.” Puleo good-naturedly adds that while a fuel pump is not especially sexy as machines go, “It’s glamorous for me. It gets me all over the world.”
Which is to say, Motor Components sells pumps worldwide. The company is one of a handful of manufacturers of fuel pumps in the United States and Europe, and its heritage goes back half a century to such manufacturing luminaries in the industry as Bendix, Fram and Purolator. Since 2001, the firm builds Facet/Purolator pumps as part of BAM Enterprises.
The original engine-mounted fuel pumps were mechanical. Running off a cam, directly or indirectly, they pulled in fuel and expelled it using a flexible diaphragm and two one-way valves. While they worked fine and dependably on engines with carburetors and mechanical injectors, mechanical pumps were found not to be a perfect match for electronic fuel-injected gas and diesel engines.
“There are still some mechanical fuel pumps out there, even in compact equipment, but most of the Tier 4 engines coming out require electric fuel pumps,” says Puleo. “Electric pumps give positive pressure in a fuel line as soon as you turn the key on. When the engine cranks, you get ignition.”
Motor Components doesn’t manufacture mechanical pumps. The company makes electromagnetic solenoid pumps compatible with gasoline, diesel and biodiesel engines, with very little distinction between them. Each pump has a piston that strokes back and forth, with valves admitting and emitting the fuel. Where the pumps differ is in the level of pressure they produce to move fuel into position. To determine which pump is best for a motor, the type of fuel injection on the engine must be considered as well as the distance fuel must be pumped.
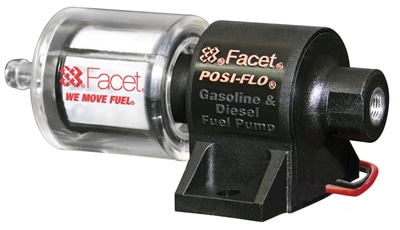
Maintenance personnel can take preventive measures to keep fuel pumps doing their job — typically for Facet/Purolator that is for 10,000 hours.
“There is a wide range of psi (pounds per square inch) and gph (gallons per hour) for fuel pumps. The requirements for a pump will change based on how far the pump has to push the fuel to the engine, how far it has to pull it from the tank, the micron rating of the fuel filter, if there is a pre-filter, and so on,” says Puleo. “All of these factors cause line (pressure) loss. For example, you may start with 6 psi and get to 3 psi when the fuel arrives at the injection pump.”
The total demands on a pump must be calculated to determine which pump in the Facet/Purolator lineup will best meet a specific engine’s requirements. In working with engine manufacturers, engineers may prescribe a certain pump during the testing stage but recommend another one in the end because another pump will produce the higher or lower psi stipulated for the engine.
By the time a shop maintenance person comes into the picture, it isn’t a question of which pump works best on an engine but, rather, why a pump is not doing a job. Usually it means the psi and gph have been degraded. Not enough pressure, not enough fuel.
“The first thing that must be checked is the fuel filter to see if it is clogged and needs replacement,” Puleo says. “If you put in a new filter and the engine is still hesitating, then obviously you need to change the fuel pump. That is the most common symptom and way to fix it.”
Generally, the problem of decreased pressure means that either valves have worn to where they are not sealing as they should or the piston itself is worn to a point that it has lost its effectiveness. On the other hand, when an engine simply refuses to work because of lack of fuel supply, the pump possibly has shorted out or is pumping bad fuel. Pumps in engines that sit for months at a time sometimes fail because they have become corroded to the point that a piston cannot freely move.
Whatever the problem, the solution is to replace the fuel pump with a new one. Rebuilding it is not an option. The units, in fact, are not engineered to be rebuilt, Puleo says. “As a company, we don’t sell component parts for rebuilding pumps. The pumps are relatively inexpensive to buy and are designed to be thrown away when they are worn out.”
Maintenance personnel can take preventive measures to keep fuel pumps doing their job — typically for Facet/Purolator that is for 10,000 hours. Fuel hose, piping and clamps can be checked to ensure they are in good condition. What happens when lines lose their integrity is that the efficient little pump sucks air into the system and that plays havoc with the efficiency of the injection system. Also, a technician can check electrical connections on the unit to ensure there is uninterrupted energy for the circuit boards powering the pump.
Fuel filters are part of the Facet/Purolator pump design. Cube and Posi-Flo model pumps have screw-on filters specifically designed for them, whereas filters for GoldFlo and Dura-Lift pumps are integrated into each unit. All the filters are replaceable, and a good maintenance protocol is to replace them on a regular schedule. The same is true of pre-filters, which are situated in fuel lines between tank and pump.
“Bad fuel will make a pump go bad if filters are not changed as needed,” Puleo says. “In the compact equipment world, .when a machine is used in an ag setting or at a construction site, the machine is not clean. There usually is mud all up around the tank and dirt around the fuel cap. If you don’t clear the dirt away from the cap, some will certainly fall in the tank and the pump will suck it right out of there and into the engine.”
A service technician can access a fuel pump easily — or maybe not so easily. It all depends on the design of a particular brand of equipment. Puleo says some manufacturers place the pump in an easily accessed area, and some don’t. “Sometimes a technician can see the pump, but sometimes he surely says, ‘Where in the world is it?’”
Manufacturers of compact equipment don’t ask Motor Components about convenient placement of their fuel pumps. If they did, Puleo presumably would respond, “Make it easy for service technicians.”
Nevertheless, the company does have a close working relationship with all major compact equipment manufacturers and diesel engine manufacturers. Some 80 percent of its business is OEM and that is a lot of pumps. In 2015, Motor Components produced between 800,000 and 900,000 units. If you are thinking you don’t commonly see the Facet or Purolator label on a fuel pump, it might be because the company also does private label work. That is, a Caterpillar, Perkins or Kohler fuel pump very well may be a Facet in disguise.
“We have the longest-lasting pumps on the market,” Puleo says, who for 17 years has been a company man for the Elmira Heights, NY, firm. “We are the standard, and we take great pride in our work.”
Giles Lambertson is a freelance writer for Compact Equipment.