5 Cold Weather Maintenance Tips for Equipment (From Engine Coolant to Fuel Heaters)
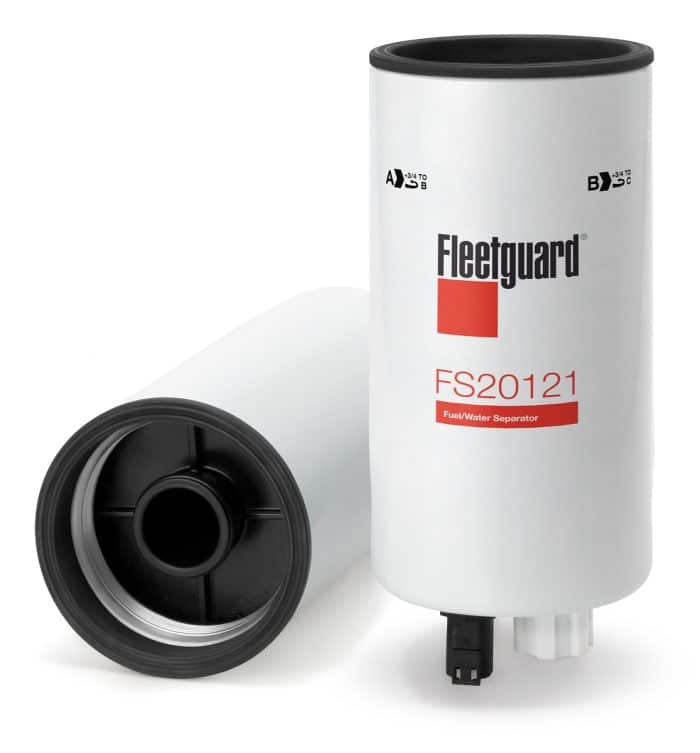
In ultra-low sulfur diesel fuel, water and paraffin cause major issues when temperatures drop. Imagine your fuel lines freeze due to water or your filter clogs because of paraffin crystals. These scenarios don’t just cause unplanned downtime; they produce hefty repair bills as well. So let’s talk cold weather maintenance.
Water in diesel fuel forms a cloudy mix that creates major injector issues and clogs filters. Add icy slush to it, and you’ll have even slower fuel flow. If that wasn’t concerning enough, paraffin wax, a naturally occurring substance in diesel fuel, can solidify in winter to form crystals. These will block the fuel filter, eventually starving the engine of fuel. The cloud point, where paraffin crystals begin to form, can happen anywhere from -45 to 35 ˚F, depending on fuel type. Fleetguard understands these challenges and — with the help of filtration science — aims to keep equipment running in the harshest conditions. Through advanced heating solutions and efficient filtration technologies, reliable engine performance is ensured, even in the brutal cold.
Filtration science experts recommend five ways to stay up and running.
Five Cold Weather Maintenance Tips to Keep You Running
1. Add a Fuel Water Separator to Your Vehicle
Fuel systems have extremely low tolerances for water and need additional water-separating filtration for adequate protection. Standard fuel filter elements become water-logged without a water separator, which makes them even more susceptible to plugging in cold temperatures. Some engines come equipped with an engine-mounted fuel water separator filter from the factory, but not all engines have one of these units. For instance, the latest generations of Cummins medium-duty engines utilize an engine-mounted, spin-on fuel water separator filter (part number FS20121 for 2021+ model years).
Older engines, however, may not always come equipped with such a filter from the original equipment manufacturer (OEM) and rely solely on a single engine-mounted fuel filter not designed to handle water in fuel. Placing filters with Fleetguard proprietary media types such as StrataPore, NanoNet or advanced water separation media upstream from the engine’s stage 2/primary filter can potentially triple the filtration service life of a stage 2 filter. Advanced filtration media captures and retains contaminants, increasing the primary filter’s lifespan and reducing frequent replacement. These media types can lower costs and downtime while continuously protecting your products and investing in your future.
2. Install a Remote Mount/Fuel-Water Separator
Combination fuel filters/water separators, such as the Fleetguard Fuel Pro series and Diesel Pro produced in partnership with DAVCO, serve as upstream water separators that will significantly enhance the performance and prolong the life of downstream, engine-mounted fuel filters. These types of fuel processors are common in the heavy-duty truck segment and have proven to reduce issues caused by contaminated diesel fuel. Upgrading or complementing your on-engine filtration with a remote mount/fuel-water separator allows easier access to the filter and provides additional benefits such as diesel fuel heaters, water-in-fuel (WIF) sensors, finer filtration of unwanted contaminants, and/or longer service life. In order to upfit your vehicle with one of these fuel processor units, you must know the following information:
- Current on-engine filter requirements for filter efficiency (micron rating)
- Current on-engine filtration water separation requirements for both free and emulsified water in diesel fuel (fuel water separation efficiency)
- Maximum and minimum flow rates of the fuel system (usually in liters/gallons per minute)
- Maximum fuel system restriction guidelines
To determine this information, use the current on-engine filter as a baseline or consult with your OEM.
3. Add a Diesel Fuel Heater
Heating the diesel fuel in a vehicle or equipment application will help to alleviate the problems that can occur when temperatures drop during seasonal changes. In cold weather, diesel fuel can solidify as paraffin crystals form, coating the filter media and preventing diesel fuel from flowing to the injection system. Common methods used to heat diesel to continue running in cold weather include using electric pre-heaters, which come in either direct current (DC) or alternating current (AC) configurations, or coolant and/or fuel return lines. These electric pre-heaters and fluid return lines are typically built directly into the aforementioned remote mount/fuel-water separators.
Electric pre-heaters will ensure engines start in most cold weather conditions. For extreme cold weather operating environments or higher fuel flow systems, additional coolant or return fuel heaters could be necessary.
Higher-wattage DC pre-heaters are necessary for biodiesel fuel applications, as well as combining with coolant or return heat to ensure proper fuel viscosity.
4. Test the Engine’s Coolant
Coolant is often associated with the hot side of the engine temperature equation, but freeze protection is equally critical for protecting the system. It’s important to test coolant in cold temperatures to ensure that it can effectively protect your engine during below-freezing conditions and prevent unplanned downtime. A few of the ways to do this are with using a test strip, sending off a sample to be tested in a lab (using a coolant analysis kit), or with a refractometer, an instrument that provides information about the concentration of a substance.
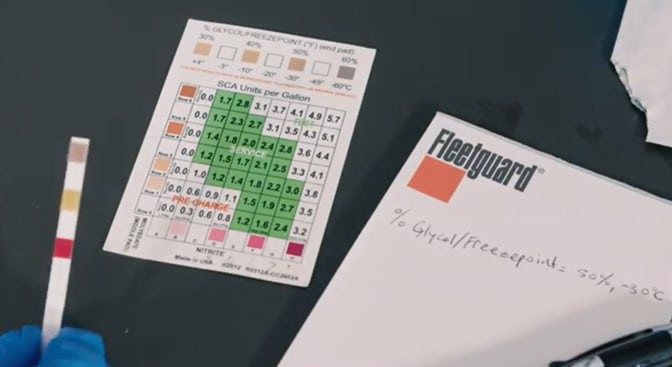
When testing, make sure the glycol percentage in your coolant is approximately 50%; however, if the temperature that system is exposed to exceeds -40 °F, a glycol percentage of 60% is recommended to increase freeze protection. If the percentage dips below these recommendations and the engine coolant is not in the appropriate concentration, you run the risk of the coolant freezing and damaging your equipment. The following Fleetguard products are some recommended ways to test the health of your coolant:
Test Strips
Coolant Testing
- Corrosion and metal movement testing: CC2700
- Dilution and system contamination: CC2717
Refractometers
5. Engage the Experts for Cold Weather Maintenance Tips
Online training from the filtration science experts can supply you with the latest maintenance information and troubleshooting tips. Free training such as Fleetschool or Fleetguard LIVE webinar sessions allows you to access valuable information in order to help you reduce downtime and save money.
With the help of filtration science, Fleetguard products keep equipment up and running in some of the most extreme conditions. Click here to learn more about its products.
Jay Stephenson is the North American training leader at Fleetguard, a brand of Atmus Filtration Technologies.