Tips to mini ex operation: How to lower maintenance costs through quality operation
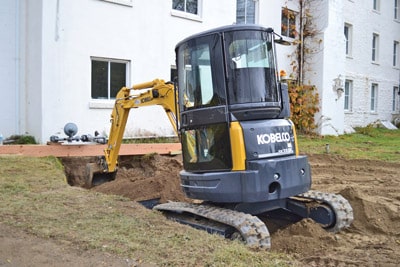
Specific to a bucket, the teeth should be monitored for any signs of damage.
Mini excavators are a significant investment that require the same maintenance as larger, full-size models to keep them up and running. Paying close attention to maintenance intervals and checking all service points daily will ensure your equipment stays in top condition. Here are some simple steps that can be taken to minimize costs and maximize the life of your compact excavator.
Start-Up Checks
Start-up checks are essential for safe and reliable operation. At the beginning of each day or each shift, operators should take the time to walk around the machine, reviewing each and every service point to see if there is any area that requires attention. Most of these points should be conveniently located, with easy access from ground level, so this task should be fairly simple. If an operator is performing a start-up check on a daily basis, he or she will know immediately when a problem arises before it causes severe or irreversible damage to critical machine components.
Attachments
Any attachment your compact excavator is using should be lowered to the ground and visually inspected before each use. Any dirt or debris on the attachment should be removed before inspection because it can mask problem areas. Important issues to look for include excessive wear, damage or cracks as well as any loose bolts or pins. Typically, minor cracks can be repaired fairly easily as long as they are caught early on. Specific to a bucket, the teeth should be monitored for any signs of damage. If any teeth are found with extensive wear or holes, they should be replaced as quickly as possible. Also on the bucket, as well as all other attachments, operators should check the cylinder and linkage for ample lubricant, leaks and/or damage.
Tracks
Operators should check track tension daily and make adjustments as needed based on current jobsite conditions. Your excavator’s track tension should not be too tight or too loose. Failure to make the proper adjustments can lead to serious track and undercarriage damage. Loose tracks, for example, are susceptible to de-tracking and excessive wear while overtightening can cause tracks to tear and will put more wear on other system components. Neither situation provides a favorable outcome. Every machine is different so be sure to refer to the operator’s manual for specific track adjustment instructions.
Fuel Filter
It is extremely important that the fuel filter is checked and changed frequently. A clean filter will do the job of screening any dust, dirt and debris from the fuel tank. If the filter is not changed regularly, it can become clogged and either limit or completely disrupt the flow of fuel to the engine, inhibiting machine performance. When the engine is not receiving a consistent supply of fuel, operators may experience rough idling, engine hesitation and difficult start-up. Using an OEM filter that is sized to fit your specific excavator model and changing it frequently is your best bet for better fuel filtration, optimum machine performance and lower maintenance costs.
George Lumpkins is a national service manager with Kobelco Construction Machinery USA.