Exceptional Excavators: We Dig Around the Industry and Detail the Most Innovative Mini Exs on the Market
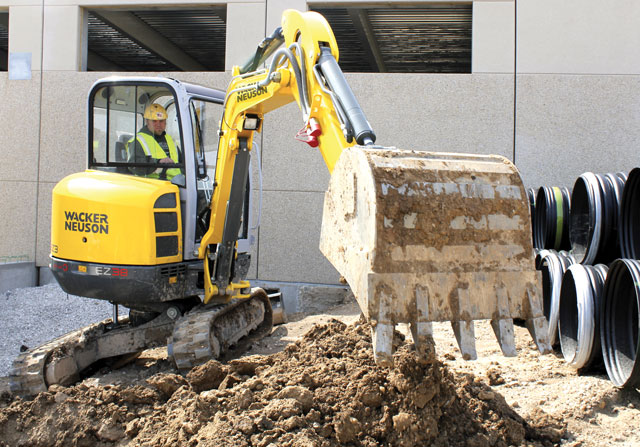
Wacker Neuson’s unique Vertical Digging System (VDS) lets an operator push a button and tilt the cab and boom up to 15 degrees, compensating for slopes up to 27 degrees. Pretty frickin’ cool, right?
Sometimes it feels like the only difference between one brand of compact machine and another is the nameplate and color. Features are common among them, and they are distinguished mostly by minor proprietary differences that constitute a unique “feel” for a brand. But not everyone follows the leader. Among compact excavators, for example, some manufacturers have taken a different approach to produce diggers with real differences. Wacker Neuson veered off the common path more than 25 years ago. In 1990, it introduced on a trial basis a leveling feature on its compact excavator called “Tiltmatic.” Customer reception was mild, possibly because of the name, which Wacker Neuson eventually replaced with the more explanatory “Vertical Digging System” or VDS.
In essence, VDS lets an operator push a button and tilt the cab and boom up to 15 degrees, compensating for slopes up to 27 degrees. The upshot is that the revolving superstructure of the excavator can be hydraulically leveled so that the boom with bucket or drill — and operator in his seat — can work on the true vertical.
“In traditional trench applications performed on a slope or hillside,” says Fred Paul, sales engineering manager at Wacker Neuson, “the boom tilts to the side. This means that more material needs to be removed to have the same width of trench at the bottom as there is at the top.” More material moved than necessary equates to less efficiency and more cost. Nearly as important, operators are less fatigued at the end of a work day because they have sat upright instead of constantly straining to offset the lean.
In addition, the extra time spent trenching runs up the hours on a small excavator. Consequently, when a VDS excavator and one without the system are owned the same amount of time, the VDS model will have fewer hours on it — and a higher resale value. The unique system is marketed on three Wacker Neuson zero-tail models — the EZ28, EZ38 and EZ53 units — with the 3.8-ton EZ38 being the most popular. Usual applications include civil engineering and landscape excavations as well as routine construction projects.
Caterpillar introduced a new idea in 2016 with the rollout of the four-ton 304.5E2 XTC excavator. The key letters in the mishmash name are “XTC.” The excavator is fitted with a skid steer attachment plate in place of the usual blade. Consequently, it can perform a variety of tasks on a jobsite formerly requiring another piece of machinery. The idea for the novel XTC came from the manufacturer. “As a product group,” says Cat senior project engineer Greg Worley, “we spend a great deal of time researching the different applications of our customers. We saw an opportunity to bring something different to the market.”
Caterpillar’s cool 4-ton 304.5E2 XTC excavator is actually fitted with a skid steer attachment plate in place of the usual blade, so it can run brooms like this.
He says giving a small excavator more versatility was the goal, “keeping it working for longer, in a wider variety of applications.” The most common attachments used so far by customers on their 304.5E2 XTC units are forks for material handling and a multi-purpose bucket for rock and soil handling as well as back-filling and fine grading.
The undercarriage was beefed up to accommodate the new applications, with the upgrades incorporated into the standard 4-ton Cat excavator. Engine and hydraulic systems are standard for the two units. “The XTC unit makes the excavator more versatile, but at the end of the day it is still a 4-ton excavator. You are not purchasing a dedicated niche machine. You are getting a machine with great versatility that can get more done for less.”
And what has been its reception? As expected, Worley says. “Introducing something new and different is always going to be a challenge. Once we get a customer on the machine, we get the positive reaction we expect. The challenge is getting the customer to try it in the first place.”
JCB prides itself on innovation, which Tyler Peterson, a JCB product manager, calls “the life blood” of the organization. Its latest innovation is a wheeled excavator called the Hydradig 110W. It is a major redesign of the basic excavator machine, with engine, tanks and ancillary systems situated between the wheels and the operator platform and boom swiveling above them.
“JCB looked for the next big thing the construction industry needs,” says Peterson. “We sent engineers out to talk to customers and asked what the five most important aspects of the machine are. What are you trying to do? What is important to you? We designed the Hydradig around those customer needs.” Incidentally, there is no consideration being given to introducing the design to a tracked excavator or to smaller wheeled models.
The JCB Hydradig can travel on the road at 25 mph, is serviced at ground level and can crab-steer turn within a 13-ft radius.
All through the five years of development, JCB engineers kept five “abilities” in mind: visibility, stability, maneuverability, mobility and serviceability. The result is a machine that has all wheels visible from the operator seat, can travel on the road at 25 mph, is serviced at ground level and can crab-steer turn within a 13-ft radius. All the attachments that fit other JCB machines will attach to the Hydradig, so it is a versatile tool carrier. Introduced in Europe at the 2016 bauma exhibition, it was rolled out in the United States this year at CONEXPO-CON/AGG. Two principal markets are targeted for the unusual excavator — municipal and road/bridge contractors.
The market reception has been encouraging. “Last year was more successful than we anticipated,” Peterson says. “We had set a target for the year and ended up nearly doubling it. There was a lot more demand for the machine than we anticipated.”
Takeuchi offers a hybrid small excavator, a distinctly dual-powered machine. The TB216H comes with a 14.9-hp diesel engine and a plug-in, three-phase electric motor with a voltage range of 400 to 480 volts. It can be plugged into an electrical system or a generator. The system is not complicated. Flipping one switch turns on the electric motor at which time the diesel engine shuts down. Can’t get much simpler than that. “There is an industry need for machines that can excavate both indoors and outdoors. Takeuchi saw the need, stepped up and produced the TB216H,” says Michael Shebetka, product manager for Takeuchi US.
However, it is important for operators — many of them rental industry customers — to know their electric power source, he adds. “The main thing is for operators and support staff to know for certain that an electrical power source is compatible with the machine’s electrical requirements.” Takeuchi trains rental house personnel and direct customers on how to avoid mismatched power sources. Introduced last November, the compact model was selected for the new power system because the model is popular in the rental industry and is easily transported.
“The TB216H is ideal for utility contractors that need a zero emissions platform for indoor use. Plus, with its hydraulically retractable track frame, it can get through openings less than 40 in. wide,” Shebetka says.
Horsepower output for the compact excavator is nearly identical for diesel and electric power plants, according to Shebetka, so the unit responds equally well with either engine. “Each system has its own set of hydraulic pumps of equal displacement, so there is no drop in performance when switching from one power source to another.” Takeuchi has no plans to introduce dual-power to its other excavator models.
Giles Lambertson is a freelance writer for Compact Equipment.
Drone Data: Trimble and Propeller Aero Announce Platform/Partnership
Simple tools to measure surface geometry, track trends across time and perform visual inspections.
The high-tech construction innovators at Trimble recently announced a collaboration with Propeller Aero to distribute its Unmanned Aircraft System (UAS) analytics platform. Propeller, based in Sydney and Denver, is a leader in the advanced collection and analysis of data from UAS. Propeller’s simple automated ground control targets, cloud-based visualization and rapid analysis platform will also be integrated with Trimble Connected Site solutions to bring an end-to-end, cloud-based UAS solution to civil engineering and construction contractors.
Pairing Propeller’s web-based interface with Trimble Connected Site solutions allow users to unlock the full value of UAS information. It gives users access to simple tools to measure surface geometry, track trends across time and perform visual inspections. Both technical and non-technical professionals are now able to gather insights remotely and collaborate, driving significant improvements in safety, efficiency and reducing environmental impact across a construction worksite.