Electrifying Excavators: Some Mini Ex Manufacturers Are Turning to Electric. Should You?
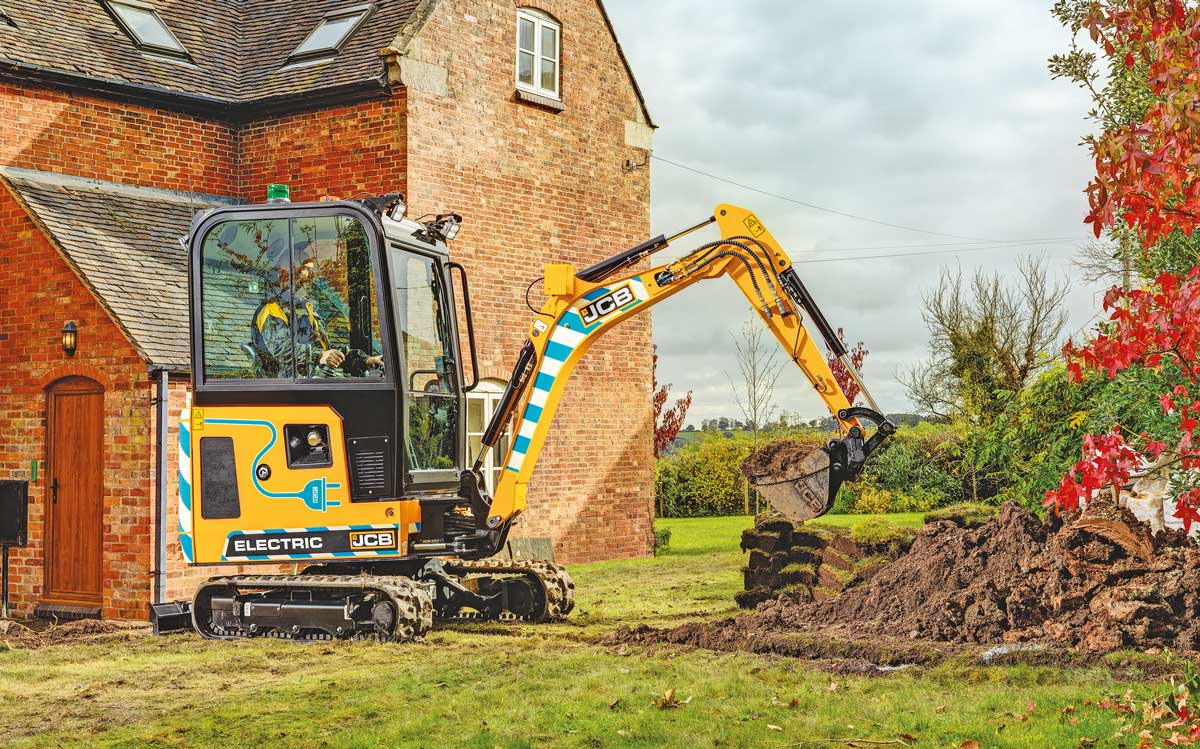
Mini excavators are all the rage right now, and it makes total sense. These small but mighty machines can access any jobsite (including hard-to-reach spots) and tackle everything from a patio renovation to installing a new water line. Their power and versatility make them popular. Couple that with their compact size and stationary production cycles, and you have the perfect candidate for electrification.
“Most manufacturers, including JCB, are currently focusing on machines weighing less than 5 tons for electrification, primarily because of the increased battery power required to operate larger machines,” says Chris Lucas, excavator product manager for JCB. “Excavators in the 1- to 2-ton range are most effective because you get the most capacity and run time for the size of battery pack required. Until technology advances further in this field, the opportunity cost of electrification of larger machines is too great.”
With mini excavators enjoying such fandom, there’s the thought: If it’s not broke, then why fix it? Why electrify? The obvious answer is reduced emissions. Lars Arnold, product manager of electromobility for Volvo Construction Equipment, says governments enacting clean air laws and project owners putting sustainability targets into their RFPs are prompting the demand for electric machines. With these requirements becoming more common, contractors will need the equipment to meet them.
However, the switch to electric is about more than just environmental sustainability.
“Fully electric machines are much quieter than diesel equipment, which could allow crews to work at night or in populated areas where there are noise regulations,” says Arnold. “Electric machine owners also might be able to expand their offering. Indoor jobs, food production facilities, high-dust environments and other applications where combustion engines and diesel fumes are a problem may now be open to them with electric machines.”
When buying an electric excavator, many of the same features you’d look for in a diesel model still apply — think operating weight, dig depth, bucket breakout/digging force, maximum reach and attachments. Add in motor style and battery life and quality.
“JCB uses a magnetic drive motor to engage the hydraulics, which consumes less energy and is the best choice for electric machines,” says Lucas. “Consider the energy efficiency of smaller components, such as LED lights, as well. The emphasis should be on optimizing battery usage wherever possible for the functions that matter most — like digging power. Another consideration is the battery manufacturer. Are they credible? What’s the warranty? What happens if I need to replace a battery?”
The options available for electric machines are also like their diesel equivalents. To name a few, operators can choose from standard or long arm, cab or canopy, auxiliary hydraulics for high- and low-pressure attachments, single- or double-acting cylinders, etc. Arnold adds that this level of versatility is what makes compact excavators so productive and in demand.
Diesel vs. Electric
With buying criteria covered, let’s further compare diesel and electric machines with three more considerations: performance, price and maintenance.
“In terms of power and performance, we’ve been happy to hear operators who have used Volvo electric mini excavators say that they operate basically the same if not better,” says Arnold. “The differences so far have been positive as well. Operators report that the electric machines feel stronger and smoother, and the lower noise level means jobsite communication is much easier.”
As for price, buyers can expect to pay twice what you would pay for a diesel-powered model of the same variant. However, Lucas says that as technology advances and more electric machines enter the market, these prices will change.
“We always encourage operators to look at the return on investment [ROI] on electric mini excavators,” he says. “Thanks to limited service costs, minimal related maintenance, elimination of exhaust extraction requirements and increased after hours/noise-restricted work opportunities, a JCB 19c-1E can provide enough ROI to cover the up-front cost in approximately five years depending on machine use.”
When looking at maintenance tasks, engine upkeep is replaced with battery charging. Operators are still required to conduct visual inspections on hydraulic lines and grease machine components.
“With electric, there’s no engine-related maintenance,” says Arnold. “Essentially, the only supplies required for a technician working on Volvo electric excavators are grease and hydraulic oil. The lifetime of the battery-electric components should be equal to or better than that of the diesel engine on a conventional machine.”
Mini excavators are making big waves on jobsites all over North America. Click here for the latest news on these machines and the companies that make them.
Current Choices…
With electric machines being more common in Europe, Volvo and JCB are two manufacturers that have been ahead of the game in electrifying their machines — with the plan to bring them to North America. For example, Volvo has sold hundreds of its ECR25 Electric compact excavators in Europe and has had several customer pilots in North America. The ECR25 Electric offers comparable performance to its diesel counterpart with a digging depth of 9 ft, 1 in., a max reach of 15 ft, 1 in. and a breakout force of 5,020 lbf. Arnold adds that with the recommended 240-volt setup, the ECR25 Electric can be fully charged in six hours. Its off-board fast charger allows the machine to reach 80 percent capacity in less than an hour.
“The ECR25 Electric takes the proven credentials of the industry’s foremost cab — accessibility, visibility and class-leading ergonomics — and adds a substantial reduction in noise, vibration and heat, ensuring long-lasting comfort and productivity,” he says. “The lack of emissions is also noticeable, removing the associated fumes and minimizing dust.”
When talking with JCB’s Lucas, he says watching (and listening to) the electric JCB 19c-1E mini excavator perform indoors, underground and in noise-restricted areas is the coolest thing.
“You’ll notice that it’s completely quiet — except for the sound of the bucket cutting through the earth — and it is extremely efficient in these environments that previously required exhaust extraction, limited work hours and the like,” he says. “Because the machine produces no sound, we have included a blue LED light inside the cab to notify the operator that the machine is live. We have also made the orange safety beacon on the cab roof standard to alert bystanders.”
Lucas adds that the 19c-1E offers five hours of continuous runtime with multiple charging options, including a fast charge option at two and half hours from 0 to 100 percent charge.
Also of note, Bobcat currently has a partnership with the Green Machine brand to produce electric models. Read more about those at compactequip.com.
…and a Few More to Come
In November 2021, Yanmar Compact Equipment announced its first electric mini excavator prototype: the new SV17e. According to the company, the SV17e is aimed at customers in the European market and fits in the 1.5- to 2-metric-ton segment. The new mini excavator is a quiet, zero-emissions machine powered by 48-volt batteries.
“Our prototype is significant because it demonstrates our capability to bring the quality and reliability of our highly respected conventional engine technology into the arena of electrification,” explained director of product management, EMEA, Cedric Durand, in the company’s press release. “But we have gone further. As always, the operator is at the heart of this machine, and we have challenged ourselves to deliver the comfort, power, control and precision which we believe will surpass the expectations of professional operators.”
Yanmar says the SV17e is currently undergoing its vigorous product testing regimen in preparation for sales to start at bauma 2022 (that big German tradeshow).
Customer requests spurred Doosan’s entry into the electric mini ex market with the DX17Z-5. The company is currently developing the 1.7-metric-ton zero tail swing machine for customers who work in applications where exhaust gases are prohibitive, such as indoor demolition projects. According to Doosan, the size of the DX17Z-5 was selected because of customer requests for a narrow mini excavator that could work in confined spaces and may be available in North America sometime in 2023.
Volvo is keeping busy in the electric market and plans to introduce two additional models — the ECR18 Electric and EC18 Electric — later this year. Arnold says both machines are 1.8-ton units and feature the same emissions, noise and maintenance benefits of the ECR25 Electric. The ECR18 will boast an ultra-short tail radius, giving it additional advantages in tight spaces.
“We’ll also have our Electric Machine Management Application [EMMA] available,” says Arnold. “This is an app that provides real-time insight into a single electric machine or an entire fleet, including battery status and geographic location. Fleet managers can simply use the application from any internet-connected device to access valuable information, helping to manage the charging process more efficiently and maximize machine uptime.”
Pam Kleineke is managing editor of Compact Equipment.