Bright Decisions: Should You Rent or Buy Those Light Towers
Overnight construction work has its perks. For one, it minimizes disruptions for local communities and businesses. And two, less traffic makes it safer for workers to perform their duties. As contractors turn their attention more to working through the night, light towers are becoming increasingly popular. For a product such as light towers — where more than one is often necessary — rental is a good option to consider. When it comes to renting versus purchasing, there are many considerations to take into account. There is a right answer for every size of contractor, but it is important to ask questions before ultimately renting or making the investment to purchase light towers.
Why Rental?
While it is a big consideration, price is not the only factor when weighing whether to invest in a light tower purchase or to rent. Rental is a wise decision when the contractor wants to avoid unexpected cost, such as repairs, insurance, depreciation and more. It is also a luxury to be using the latest models. However, low prices do not always guarantee the best deal. Depending on the complexity and/or critical nature of the job, the renter may also value knowledgeable and fast technical support during operation. For contractors with a small team, the ability to have technical support is crucial to reducing any downtime.
The Ins and Outs of Rental
When renting a light tower, the renter should ensure they understand the following:
• Light requirement of the application. This way, the rental company can assess what the best solution is for their needs
• A clear understanding of the rates
• What is and what is not included (such as transportation and maintenance)
• Response times if something goes wrong
• Policy for returns and anything affecting the availability of the equipment and the cost associated
For the rental house to best assist with selection, it is important the customer calculates the area they need lit. The best way to do this is to provide the overall area estimation, either from a map of the site or a rough estimation if the application does not require any strict luminosity levels. This is mostly a trial-and-error process for the customer, where the expertise of the rental company will guide them in the correct direction.
The Application
Receiving a good assessment for selecting the best light tower to pair with the application is another incentive for renting. As far as applications, it is important to understand the luminosity level required for each job. Even the same jobsite may require varying intensity levels in different spots. The luminosity level ultimately dictates the number of light towers to be used and their location. Other factors to consider are the risk of glaring and light quality, which may lead to selection of a specific light tower model.
The one-light-tower-size-fits-all approach is rarely the best solution. A couple examples of this:
• Say a contractor needs light in a warehouse under construction. They have power from the grid, so engine driven light towers are unnecessary. Instead, a better solution is electric light towers, which do not require fuel or engine service.
• A location for temporary parking, which is not equipped for power from the grid and where light will need to be spread out, is an application better suited for diesel engine light towers, rather than the contractor stringing long power cords across the parking lot.
• Engine-driven light towers will continue to lead the way in construction applications, but plug-in light towers are a good option, especially indoors. Currently, plug-in towers are more popular with customers looking for a party and event light solution, where the noise and exhaust from engine-driven light towers are not a welcomed guest.
Each application should be looked at individually. With the menu of options light tower manufacturers offer, a solution that fits the application is always possible.
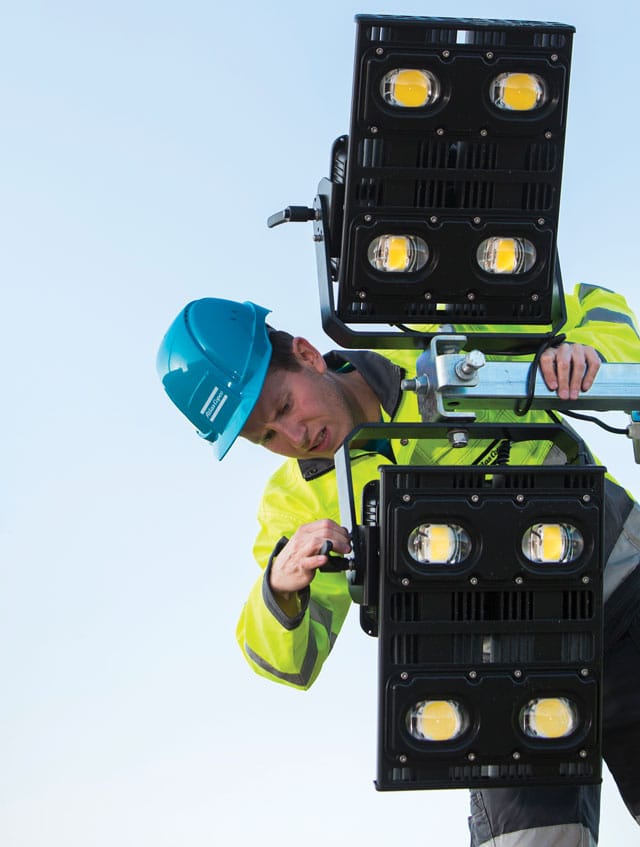
The eruption of LED technologies means a huge leap when it comes to fuel economy, durability and safety in light applications, but they are more expensive.
LEDs Versus Metal Halides
Currently metal halides are more popular in the rental market, mostly based on price. However, while metal halides certainly have a place on the jobsite, it is important to consider more than the up-front cost. Metal halides are ideal for companies infrequently working night jobs or shorter duration projects where contractors can rent a fleet of them on the cheap.
The eruption of LED technologies means a huge leap when it comes to fuel economy, durability and safety in light applications. The higher the running hours, the more appropriate LED lights are.
Fuel: When looking at fuel savings, metal halides are fuel-efficient units, but nowhere near the cost savings of LEDs. Some models are so efficient when compared to traditional towers that the user may save up to one dollar per running hour. Multiplying the total running hours by the total number of units on a project can equate to large savings.
Maintenance: LEDs hold a distinct advantage in this category. LED components last much longer. Additionally, the light can be switched on and off similarly to the lights in a house, immediately providing full luminosity. This is vastly different than metal halides, which take time to turn on and provide the ample cool down time the machine needs before shutting off. In the event the unit becomes too hot, it could take over 20 minutes to recover full brightness again. Because of this, it is much simpler and quicker to reposition an LED.
Lighting: Illumination is improved with LEDs for multiple reasons. For one, LED light is a brighter, cleaner light — similar to daylight. LED light also travels farther than traditional light. When it comes to staying power, there is nothing better than LED. Its traditional counterparts run hotter, leading to more frequent burnouts. True, LED bulbs are more expensive to replace than traditional bulbs, but they last much longer. Light bulbs are not overly costly to replenish, but over time all the replacements add up and can equate to lost time on a jobsite.
Top Tips
When renting a light tower, the renter should carefully inspect the machine either prior to hauling it away or when the rental center delivers it to the jobsite. They should inspect each unit is in good condition and correctly serviced. The operator should also have basic training on how to operate the equipment. During the rental process, the renter can potentially save even more by checking with the rental center about additional light tower features, which could help reduce operational costs. For example, a dusk-dawn photocell option will automatically start and stop the light tower every day according to the light conditions, without the operator’s assistance.
This, coupled with extended fuel autonomies above 150 hours, will strongly reduce the operating cost of the equipment. Additionally, it is important for the operator to see the light tower is properly installed by checking that the outriggers are deployed and the machine is well leveled before extending the mast. Strong winds may increase the risk of operation. Rental allows any contractor, construction firm or oil and gas company to access equipment in a cost-effective way, avoiding the risk of tying up capital. The fundamental function of light towers is simple. The decision process is anything but. When it comes to the bottom line, make sure to take the time to weigh the option of buying versus renting.
Find more enlightening information on light towers here.
Angel Nieto is the product manager of power and light at Atlas Copco.