An All-in-One Solution: Jobsites Are Busy Places, and You Need One Tool to Handle More than Just Welding
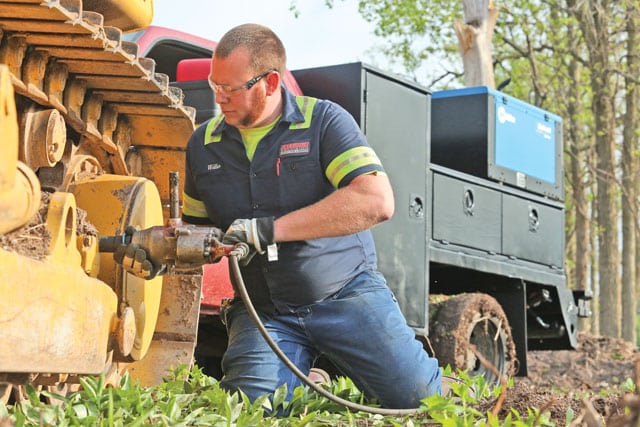
Contractors don’t want to bring the entire shop to the jobsite, so it’s a matter of having the right tools on hand that provide versatility to get a wide range of jobs done.
Contractors and service truck operators know that jobsite needs can vary from day to day, so it’s important to have a wide variety of handheld tools available to get jobs done quickly. In a single day, you may use an impact wrench, a drill, fluid pump and saw. Versatility is the name of the game. For many operators, there may be other pressing priorities, as well. These might include completing jobs faster to meet demanding timelines, reducing maintenance costs or lowering the wear and tear on your service truck.
So how can an engine-driven power source help you efficiently use the necessary tools, while also saving you time and money? An all-in-one, engine-driven solution delivers the versatility to power many tools to tackle whatever tasks you encounter. These machines also help save space, in addition to reducing overall costs and maintenance needs. Adding an all-in-one, engine-driven machine to your fleet delivers many benefits that help you stay competitive.
Meeting Many Challenges
Your goal is to complete jobs as quickly and efficiently as possible. Contractors and work truck operators don’t want to bring the entire shop to the jobsite, so it’s a matter of having the right tools on hand that provide versatility to get a wide range of jobs done. Because tools are powered in various ways — electricity, air power or batteries — you need the ability to use each option. And on some sites, a generator may be the only way to power tools if electricity is not available.
Having a separate generator and air compressor on a service truck to meet these needs means double the maintenance requirements — not to mention the additional space and weight on the truck. Using an all-in-one solution saves space, weight and costs. Engine-driven options can meet a wide range of needs, offering an air compressor, generator power, battery charging/crank assist and stick welding — all in one compact machine. The Bobcat 200 Air Pak from Miller Electric Mfg. Co. is an all-in-one, payload-saving machine, delivering 28 cfm of compressed air — enough to power virtually any air tool used on a jobsite — and a 5,500-watt generator. It also provides up to 100 amps of DC power for 12/24-volt battery charging and up to 300 amps for crank assist, along with a 210-amp stick welder.
Space and Weight Savings
On service trucks, space and weight savings matter. Having one versatile machine that combines the capabilities of numerous other pieces of equipment results in a smaller footprint and frees up payload space — so work crews can bring more tools or service parts to the jobsite. Replacing a PTO-powered air compressor and a separate engine-driven welder/generator can reduce a work truck’s weight by up to 550 lbs. Replacing an engine-driven air compressor and an engine-driven welder/generator with an all-in-one solution can reduce a truck’s weight by up to 400 lbs while increasing available payload by up to 24 cu ft.
Significant Fuel Savings
Another benefit for work trucks is the fuel savings offered by an all-in-one solution since these machines can provide compressed air, electrical power and welding capabilities with the truck’s engine turned off. You’re still completing jobs while the fuel savings add up quickly. The ability to complete work with the truck’s engine turned off greatly reduces engine idle time. For diesel-powered work trucks that are compliant with the Environmental Protection Agency’s Tier 4 emissions standards, a significant reduction in idling time can yield big benefits. Tier 4 engines are not designed to constantly idle, so it’s an issue that can cause extensive maintenance and added costs. The reduction in fuel costs, coupled with the reduction in wear/depreciation and engine repairs/maintenance, can total more than $50,000 over the average life of a truck. Reducing idle time can also extend truck life by several years.
Increased Capabilities
Some jobsites may have an air compressor only or perhaps a welder/generator but no compressor. Investing in an engine-driven solution that provides all these capabilities means you can do more than you are currently capable of. This helps you be more competitive and complete more jobs. These machines can be used on a truck or moved around the worksite on a trailer, which offers great portability in applications that range from construction to farm and ranch.
Additional Key Features
When choosing an all-in-one, engine-driven machine, there are some key features to consider that can help improve ease of use, efficiency and jobsite comfort.
- • Look for a machine that uses a rotary screw air compressor. This option is much quieter and more efficient than a reciprocating or piston compressor. A rotary-screw compressor also provides air faster, so you don’t have to wait for the air reservoir to charge up.
- • Some all-in-one machines utilize technology to ensure reliable engine starts in any weather for greater reliability and ease of use.
- • Some welder/generators also offer technology that lets them power tools with up to 2,400 watts of power at idle. This results in quieter operation and fuel savings when using tools.
One Versatile Solution
Jobsites are busy places. You need tools that offer versatility and reliability to complete a wide variety of jobs. Whether your key challenges are saving money, improving productivity or making smarter equipment purchasing decisions, an all-in-one, engine-driven solution can deliver results. These machines provide space savings and the power to run tools with the truck engine turned off. They also help reduce the time and money spent on maintenance. With the right equipment on your truck, you can meet your goals and be more competitive — for a positive impact on the bottom line.
Travis Purgett is the product manager at Miller Electric Mfg. Co.