New Welding Systems from Miller Deliver Next-Level Productivity, Cost Savings and Power
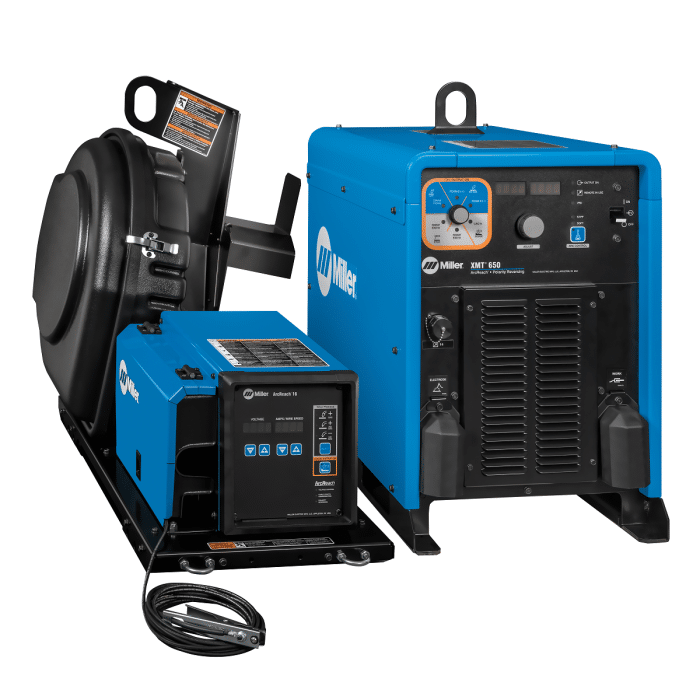
Miller Electric Mfg. LLC has announced the release of new welding power sources and a wire feeder designed to maximize productivity and cost savings and deliver the power needed for structural fabrication, steel erection and shipbuilding. XMT 650 ArcReach Systems let users weld and gouge with a single system and make process changes at the feeder without a control cable.
The system includes an XMT 650 ArcReach power source and an ArcReach 16 wire feeder. Configurations are available for field and shop applications, with remote polarity-reversing (PR) power source and non-polarity-reversing power source models — both compatible with the ArcReach 16 wire feeder. The remote polarity-reversing model lets operators switch polarity at the feeder, so they can quickly change between welding and gouging without having to walk back to the power source.
“These systems deliver the reliable point-of-use technology and quality results that make ironworkers more productive,” says Randy Decoster, product manager, Miller. “As a result, steel erectors can take their operations to the next level.”
PRODUCTIVITY: Walking to a power source wastes up to 250 hours per operator, per year, and also exposes operators to slip, trip and fall hazards. XMT 650 ArcReach Systems let operators change processes and polarity at the feeder. Operators get complete control, even hundreds of feet away from the power source, and they can switch between welding and gouging with the push of a button — without swapping leads or disconnecting them from the wire feeder. Operators can also remotely select electrode-positive or electrode-negative self-shielded wire.
COST SAVINGS: XMT 650 ArcReach Systems leverage the ability to weld and gouge with one machine so operations don’t have to rent a dedicated gouging power source — saving thousands of dollars over the life of each project. And since the point-of-use control at the wire feeder doesn’t need a control cable, it cuts expenses and maintenance, as these cables are easily damaged and require frequent repair. The systems also help operations avoid assembly downtime because they are available with a ready-to-use feeder cart or sled. In the field, the integrated sled’s robust metal rollers glide over pan decking, while a zero-turn radius makes it easy to maneuver. In the shop, the integrated cart’s handle can be easily moved to either end of the cart so users can push or pull it over floor obstructions like cords and cables.
POWER: XMT 650 ArcReach Systems remove more material per pass when gouging without sacrificing control; the power source is rated for 3/8-in. carbon. The ability to use large-diameter filler metal wires and large wire coils also helps operations improve project timelines and minimize downtime. In addition, Cable Length Compensation (CLC) technology automatically compensates for the voltage drop in long weld cables, so the voltage operators set is the voltage they get.
Durable XMT 650 ArcReach Systems can also withstand the elements — even rain, with an IP23 rating — and Wind Tunnel Technology and Fan-On-Demand technology help keep dirt out of the power source.
For more information on XMT 650 ArcReach Systems, visit www.MillerWelds.com.