Kick Ash: The Inside Scoop on a Revolutionary, DPF-Saving Oil from Chevron
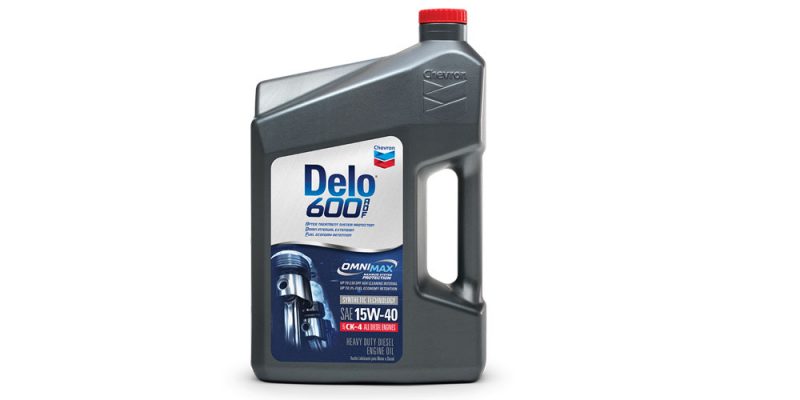
I don’t typically fly across the country for oil and lubricants news, but Chevron’s new Delo 600 ADF had me on a jet to its Technology Center in Richmond, Calif. This super low sulfated ash oil might very well be a game-changer in the off-highway diesel engine market, boasting way less maintenance for Tier 4 Final emissions-complaint power plants — specifically engines using diesel particulate filters or DPFs. The product is even more interesting for European Stage V-compliant engines, which require the use of a DPF. In fact, Delo 600’s engine and emissions protection abilities looked so impressive that OEMs and oil quality standards organizations refused to believe the results at first.
Why DPFs Clog
Diesel particulate filters are through-the-wall flow devices that trap and hold particulate matter (PM) in the exhaust. They are a big part of an off-highway diesel engine’s emissions aftertreatment system, and they are actually physically quite big. Emissions-reducing exhaust filters in DPFs require periodic cleaning. This cleaning, sometimes referred to as regeneration, eliminates soot that accumulates during normal operation. There are active and passive types of regeneration (look that tech up at your convenience).
A DPF collects up to 98 percent of particulate matter emissions in the form of ash and soot. That ash is incombustible material derived from metallic lubricant additives. Over time, after a zillion regenerations, the DPF will eventually clog up. That means units not working until the DPF is serviced. Heavy-duty engine oil produces about 1 percent sulfated ash (an API requirement). Chevron’s Delo 600 ADF with Omnimax, a Chevron patented technology, is formulated to 0.4 percent sulfated ash. This equates to a 60 percent reduction of ash in the DPF and translates to DPF service life 2.5 times longer than standard. Considering that even getting to a 0.9 percent ash level is a challenging task, achieving the 0.4 percent mark required rethinking everything about heavy-duty engine oil additives.
Why Not Give Me an Oil with No Ash?
The entire concept was sparked by a comment from a chief technology officer at a leading heavy-duty diesel engine OEM during a Chevron customer event way back in 2003. As Wim van Dam, product development manager for Chevron Lubricants, recalled: “He was talking about the developments on their side of the house, and about introducing DPFs, and they figured out in their own research that those filters were plugging with ash constituents from the oil being consumed in the normal process. So, he just threw it out there: ‘Why not give me an oil with no ash?’ We chuckled a little and said, ‘Yeah, you can’t do that.’ But we took the challenge home and started thinking about it and testing some things. It was a tough nut to crack.”
It’s fair to say Chevron is the only lubricant company capable of cracking said nut and achieving a step change of this magnitude. What stood out to me at the event was learning just how segmented the lubricant industry is. A company producing additives likely isn’t dealing with base oils and finished lubricants, for example, or getting involved in deep research of new experimental formulations. Chevron, however, is fully integrated and houses everything from strategic research to formulation to commercial development. This allows information and ideas to flow freely across silos. Strategic research breakthroughs can directly lead to OEM proposals. Questions from customers can head back to the R&D teams for noodling and so on.
“We are freer to explore crazy ideas,” said Teri Crosby, global automotive engine oil manager at Chevron Oronite, of the company’s strategic research division. “We have hypotheses that span base oils, additives and finished lubricants, and we come together as all three industries and decide which are of highest priority and what kind of funding we can get to work jointly on these.”
For this project, Chevron’s Strategic Research team went through a number of different iterations. They took out all of the metallic detergents. Then they took out the anti-wear compounds. Eventually they figured out they could replace a number of metallics with low or no ash additives.
Then it was Oronite’s turn. Oronite is a 100-year old additive company wholly owned by Chevron. It creates additive packages and sells those to customers that blend in refined base stocks to create lubricants. With Delo 600, the challenge was to take its historical formulation and replace the metallics with non-metallics or those that do not produce ash.
“It was a unique challenge,” Crosby said. “We had to start by understanding exactly how the metallics protect the engine, what substitution class of chemicals we could use that still provided the performance a heavy-duty engine oil needs to deliver.”
To achieve emissions system goals, a tradeoff in performance is expected, but a funny thing happened during the strategic research.
“In this case we saw we could not only still protect the engine but also increase performance in several areas — protection of aftertreatment system, extending drain intervals and then improved fuel economy,” Crosby said.
Field tests started in 2008, which means another 12 years passed before it was commercially ready. Why the hold up? Most oil improvement is spec driven. This means the outcomes are prescriptive with OEMs and providers all on the same page. Delo 600 was, in a way, too good. OEMs aren’t actually big fans of step changes like this, preferring incremental upgrades that align with their own product spec timelines. The typical process would be something like: The OEM has its 2023 engine specs in sight and works with lubricant suppliers to develop oils for them. For a change of this magnitude — even one that solves a problem everyone wants solved — an unreal amount of testing and tinkering needs to be done on the part of all stakeholders.
This again shows where Chevron’s full integration makes a difference. They started getting this in front of OEMs for discussion and testing as soon as they believed they had something. As OEMs became believers, they started investing their own money for further testing.
I’d Definitely Experiment with Delo 600
DPF clogging increases engine back pressure and regeneration cycles, resulting in a higher fuel consumption. Extending DPF life means saving on maintenance costs and lost productivity. Less ash also means fewer notifications to perform a regen, which means fewer times an operator skips it to keep working on a job. This also means way fewer DPF failures. If too much soot and ash build up, the large amount of heat produced upon regeneration can result in DPF damage, with replacements costing up to $7,000.
“Let’s not forget this is an engine oil, and we have seen remarkable performance in engine protection too, which will add to the value Delo 600 ADF will bring customers,” said James Booth, NA commercial sector manager at Chevron.
We’re talking a 3 percent fuel economy retention advantage over the life of the equipment, delivering significant savings to customers. OEMS will be able to extend service intervals even further. All of this ultimately contributes to reducing customer operating costs. Delo 600 ADF also has delivered excellent valve-train wear protection and piston deposit performance. Bottom line, if you have an engine with a DPF, and you like saving time and money, you might want to give Delo 600 ADF a look.
Potential costs of DPF failure:
- New DPF: $3,000-$7,000
- Remanufactured DPF: $1,500
- DPF Cleaning: $700
Chris Crowell is a contributing editor for Compact Equipment.