Beat the Heat: Daily Maintenance for Off-Highway Diesel Engines Dealing with Hot Weather and Work
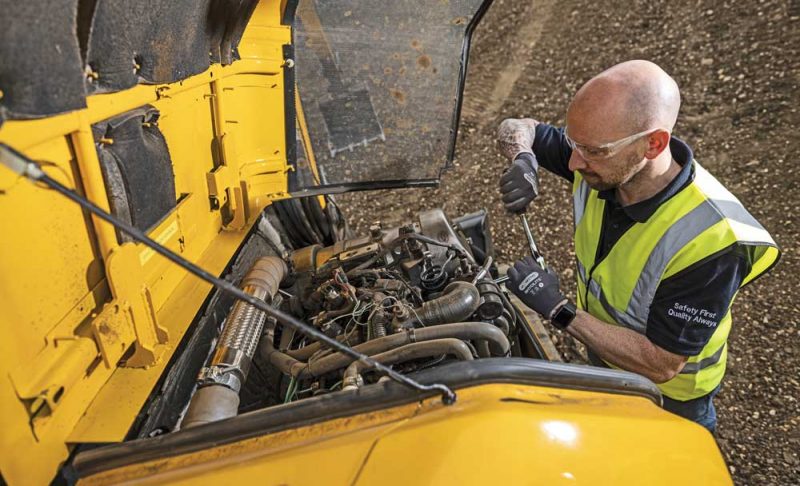
Summer work means hotter temperatures and tougher working conditions. Keeping crews safe from that intense worksite heat should be a top priority, so click this link to quickly read up on OSHA’s suggestions for employees working in the warmth. Luckily, machines handle the heat better — and can actually be a cozy place to retreat with an air-conditioned cab — but just like those boots on the ground, construction equipment also needs the ability to cool down to keep productive.
“Ambient temperatures are often elevated in engines just because the engine is usually in an enclosure or cabinet,” explains Julian Wood, product manager for aftermarket at Perkins (the global compact equipment diesel brand, a part of Caterpillar). “So poor circulation, especially when machines are static working, can cause a lot of heat. Think about a static machine that may be in a building or an enclosure. Ventilation is important for that machine. You see that sometimes with big gen sets running things like schools and hospitals. Sometimes people don’t think about the cooling slots when setting up the unit. So, to start off, think about airflow around the engine. It needs good space around it to stay cool. Just don’t operate machines with the cabinets open. That’s when you can get a lot more dust into the sensitive parts.”
It’s great advice, and there’s lots more. Diesels are already more tolerant of hot conditions than gas engines, but owners and operators still need to monitor excessive heat along with airflow, cooling, fuel and emissions systems during the hot months. Without being machine specific and with Wood’s expertise, we’ll quickly run down a set of best practices for keeping almost any off-highway diesel engine happily humming through the dog days of summer — whether for a compact excavator or a skid steer.
“As long as it’s an off-highway diesel engine, they all work the same way and they all have similar issues,” says Wood.
Daily Routine
Static or mobile, a piece of compact equipment will need an engine check as part of a daily inspection routine, along with more in-depth weekly, monthly and yearly inspections of that power plant. Daily, we recommend a complete visual and operational check. Generally, today’s engines will indicate when they have problems via a warning indicator in the cab or advanced signs such as excess smoke, loss of power, hard starting and overheating, so it’s important to first understand those repair indicators.
“Most engines have an engine temperature monitor, whether it’s coolant or a water temperature meter,” says Wood. “Take note of those sorts of warning lights on the machine. Then just make sure you’re doing the basic stuff. Make sure your tooling is up to spec. Use a hydrometer to check the strength of the coolant because we’ll see users top things off with water, weakening the coolant. The coolant doesn’t just keep the engine cool. The glycol will actually stop the engine from overheating. Coolant is there to protect from corrosion. Topping up with water weakens it.”
Service meter hours always provide a great way to structure checks and inspections, but engine upkeep is a daily matter too. If the engine works in a dusty environment — say a compact track loader doing brush cutting work — daily maintenance checks are even more imperative, including things like reviewing the filters and oil more regularly to ensure that the inside of your engine remains clean and cool. Here are a few checks to get you started:
- Cooling system coolant level
- Air pre-cleaner, empty if necessary
- Engine oil level check
- Fuel system primary filter check
- Drain water from the water separator
- Driven equipment, belts and electrical system check
- Walk-around inspection, especially guards and drive system
- Every 50 service hours or weekly checks include checking the fuel tank and draining water and sediment, if necessary
Clean Air/Fuel & Effective Emissions Systems
“Dust is a big engine killer,” explains Wood. “Machines like loaders and dumpers can lift dust into the air, which can get sucked into air intakes — all sorts of fine particles like silica, cement dust and rock dust. They can cause massive issues with things like turbochargers. It gets into the vanes, the impellers and, even worse, it gets into the bearings. If it gets around the combustion chamber, it’s going to start wearing the valves, rings and cylinder liners, which can be extremely expensive. You’ll see that in terms of reduced power and increased fuel consumption.”
Check the air filter often, but do not try to clean a dirty air filter to make it last longer. By removing blockages, a mechanic can actually create bigger holes, making the filter less effective.
Modern diesels also have emissions systems that bring their own cooling maintenance concerns. Cooled exhaust gas recirculation or EGR systems lower an engine’s peak combustion temperature to lower NOx, one of the emissions regulated by the EPA. EGR recirculates exhaust gas by mixing it with incoming fresh air. This process reduces oxygen content, lowering combustion temperatures and reducing NOx. Cooled EGR includes the cooling of the exhaust gas by passing it through a heat exchanger.
“EGR is actually pushing a portion of the exhaust back into the air intake, so you obviously need to cool that down,” says Wood. “There’s very often a cooler on the EGR system, and it’s actually running at a much higher temperature than the radiator, so you need to make sure that your coolant quality is good. The glycol is not just there for antifreeze. It also gives good heat protection.”
Diesel exhaust fluid and DEF components also need to be properly maintained especially in the hot, dry summer months. Selective catalytic reduction (SCR) systems utilize DEF to reduce NOx. DEF is made up of 32.5 percent urea and 67.5 percent de-ionized water. The ammonia in the urea mixes with engine exhaust gases in the SCR catalyst to convert NOx to nitrogen and water vapor. DEF is used at about 2 to 3 percent of diesel fuel consumption, engineered into engines over 75 hp (like a big skid steer).
“We have seen some issues with engines running DEF fluid,” continues Wood. “DEF systems require very clean fluid to function properly. As the summer months bring dry, dusty conditions, it’s extremely important to ensure the DEF filling process does not introduce contaminants. Basic steps such as cleaning the filler cap before removal and ensuring fill containers are clean before introducing DEF will have a big impact.”
It’s also important to check and maintain the diesel exhaust fluid filter. Urea crystals that come from degrading fluid and ordinary dirt can damage the DEF injectors if the filter doesn’t remove them. DEF also needs to be stored out of direct sunlight and in a dry temperature-controlled area below 86 degrees Fahrenheit. It has a shelf life of six months to a year, depending on storage. As far as application: “Best practices are really just to top off your DEF every time you top off your fuel,” says Wood. “That way you can make sure you’ve got good quality fluid in the system.”
Heat and cooling cycles also impact moisture and water buildup in fuel tanks or fuel storage tanks. All fuels contain some water in suspension, but significant levels of water can cause problems, like corroding the fuel systems and excessive injector wear, plugging of filters, reduced energy, lower power and the freezing of fuel systems in the winter. A little time spent every day draining water from the water separator on the fuel filter can save replacing damaged injectors.
“Diesel fuel acts as a lubricant within the fuel injectors,” explains Wood. “It prevents metal-to-metal contact. Water can start compromising that film strength.”
Shutting Down
Finally, the day is done and work is complete. It’s time to shut down the machine, go home and grab some dinner. But wait…
“The customer should be thinking about shutdown procedures,” notes Wood. “Quite often, workers just switch the engine off, but especially hot weather can damage things like DEF injectors and turbochargers. Switching off quickly and halting the oil flow could cause the turbocharger to overheat. DEF injectors also need cooled down due to their placement in the exhaust system to protect internal electronic components. So, leaving an engine idle at the end of a shift for five or 10 minutes is a good practice so that you can prevent risk of overheating.”
After that, definitely go get some grub. You’ve earned it.