Why Buy an Electric Loader? Let’s Talk About Battery-Powered Skid Steers, Track Loaders, Wheel Loaders and More
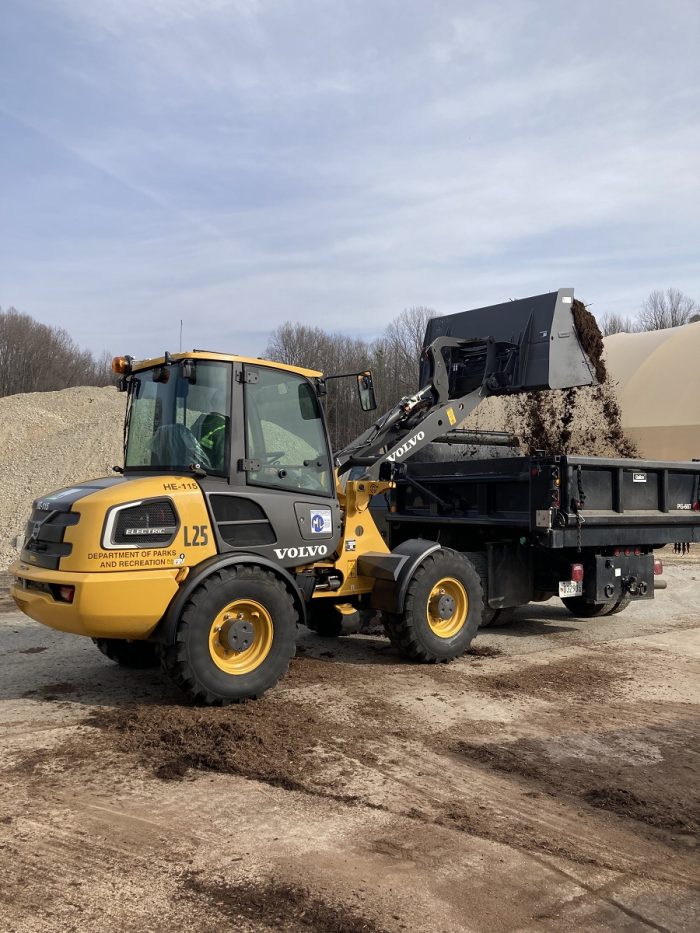
This article is part of a series on battery-powered compact loaders. In the coming weeks, we will be posting brand-specific stories summarizing the electric loader options from a variety of machine makers, including Volvo, Case, Toro, Cratos, Volteq and beyond. View those other stories right over here. Then enjoy the feature below.
Diesel has long ruled the equipment industry. Every earthmoving equipment category on the dealer lot is engineered with a diesel power plant — from skid steer loaders to wheel loaders. Boasting impressive torque, fuel efficiency, durability and longevity, today’s diesel engines are the superior choice for the long days and harsh duty cycles of commercial construction, landscaping and agricultural equipment. But let’s be honest; it’s really been the only choice.
More and more contractors have been discovering applications where internal combustion engines (ICE) are not ideal — like indoor demolition, zoo maintenance, night projects or perhaps construction around a hospital. These specific jobs require machinery that is emissions-free, quiet and free of smelly fumes. In 2024, finally, after years of prototypes and product previews, we can at long last entertain the choice of battery-powered construction equipment.
“We see electric vehicles as another tool in the toolbox for contractors,” says Brady Lewis, product manager for emerging products and technology at Case Construction Equipment, which will sell five electric machines by the end of 2024. “Our diesel lineup provides all of the power and capability that Case has built our reputation on for over 180 years, but electric vehicles are becoming a critical part of the landscape for some applications and regions.”
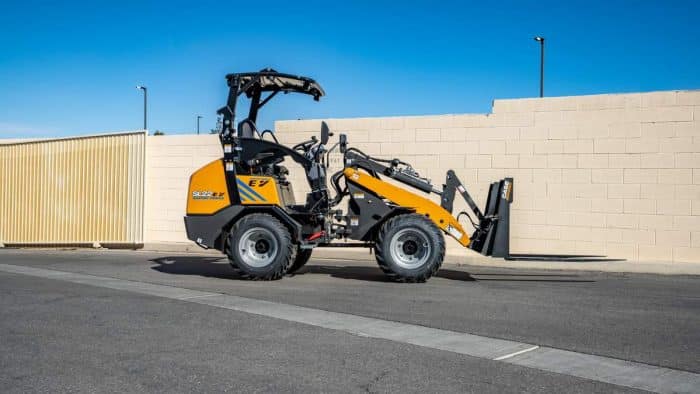
When it comes to loader categories specifically — wheel loaders, skid steer loaders, compact track loaders, backhoe loaders and stand-on and walk-behind loaders — there are a variety of interesting players and products arriving on the market. We have famous traditional brands like Volvo, JCB, Toro, Case and Bobcat offering battery-powered variants of popular loaders, and then there are lots of newcomers and niche players eager to serve the market — often focusing only on electric equipment — folks like Firstgreen, Volteq and Cratos.
The use of electric power in construction machines is not new. Electric-powered equipment has long been used in the mining and demolition markets. Certain machine sectors like industrial forklifts and mobile elevating work platforms (MEWPs) have used batteries for years. Now, the loader tool-carrier categories of compact equipment are getting electrified, which is an exciting proposition for progressive contractors. Where does electric off-highway construction equipment fit in a fleet’s toolbox, and how can it be used to make a company more efficient and profitable? Let’s find out.
The Pros of Electric Loaders
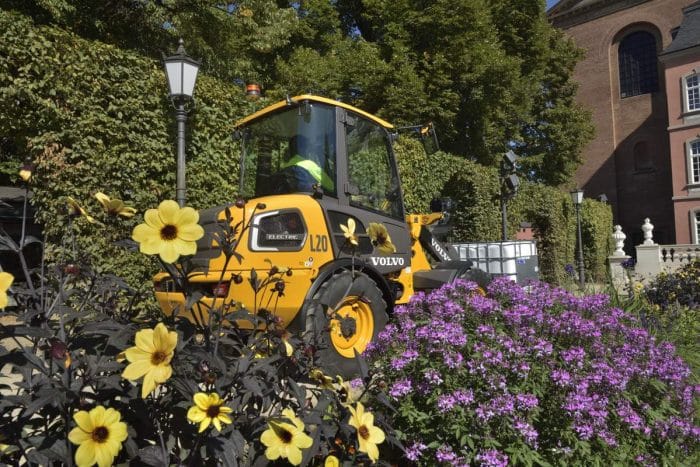
Electric loaders produce less pollution. First off, battery-powered loaders create zero tailpipe emissions, significantly reducing the release of harmful pollutants such as carbon dioxide (CO2), nitrogen oxides (NOx) and particulate matter. There’s also less noise pollution; electric motors are inherently quieter than their diesel counterparts. The reduction in noise pollution is particularly beneficial for construction projects in urban areas, minimizing disturbances to local communities and improving the working environment for operators.
“Electric drivetrains inherently produce less noise and vibration compared to internal combustion engines,” explains Marcus Suess, chief operating officer of Firstgreen Industries (makers of electric skid steers). “This not only makes the loaders suitable for use in noise-sensitive environments such as residential areas and indoor facilities, but also improves operator comfort.”
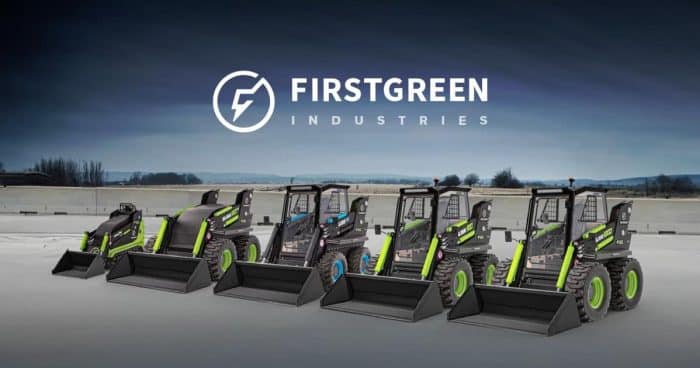
Electric loaders have fewer moving parts than traditional internal combustion engines, which translates to lower maintenance requirements and costs. The simplicity of electric motors reduces the likelihood of mechanical failures. This reliability is crucial in construction, where equipment downtime can cause significant project delays and increased costs. Additionally, the cost of electricity is generally lower and more stable compared to diesel fuel, leading to substantial savings over the equipment’s life cycle.
“I think the one thing operators need to get their heads around is that there’s no idle time on an electric machine,” says Joel Honeyman, vice president of global innovation at Bobcat, which launched the industry’s first electric track loader (the T7X). “With a diesel machine, there’s all this idle time. We know it from our own telematics. A third of all equipment on the jobsite is at idle. We’ve found this is a wow factor for our early customers. They’ll say, ‘I couldn’t believe it. We used it all day, and it had 60 percent charge left.’ Well, you didn’t really move the vehicle all day. You might’ve used it throughout a workday, but when the operator was waiting, got up for lunch or got off the machine to do something, it wasn’t consuming energy.”
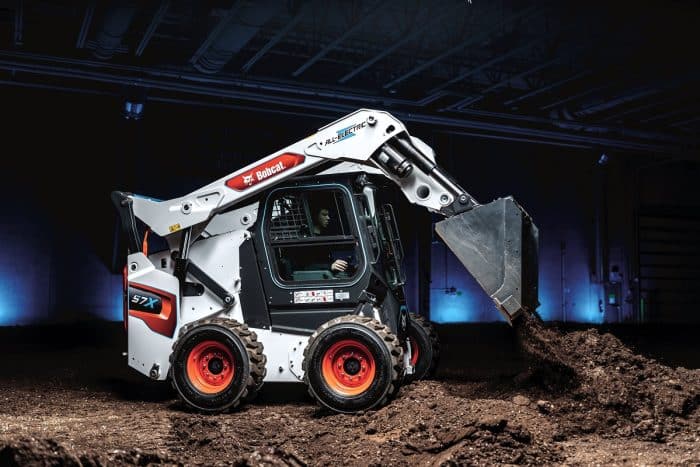
There are clear operational advantages as well. Electric motors provide instant torque, resulting in smoother and more responsive operation. This enhances the precision of tasks such as digging, lifting and grading, leading to increased productivity and reduced job completion times. Quieter loaders with less vibration and instant responsiveness make for happier operators.
“Everyone I’ve seen use one of our electric machines on a job or even just a test drive is pleasantly surprised at how powerful they feel — some even say they feel more powerful,” says Darren Ashton, product manager of compact equipment at Volvo Construction Equipment, which offers electric wheel loaders, excavators and rollers.
Going electric also offers plenty of interesting technological upgrades. The integration of automation, autonomy, software upgrades and telemetry are easier on e-loaders. “For instance, on our current diesel hydraulic loaders, you have auto bucket positioning, right?” says Honeyman. “Well, that’s all done hydraulically, but there’s hoses and valves to do that. On our all-electric loader, it’s software. We just programmed it.”
Battery-powered machines have several advantages over traditional internal combustion engines, particularly when it comes to considerations such as incorporating advanced programming and smart functions.
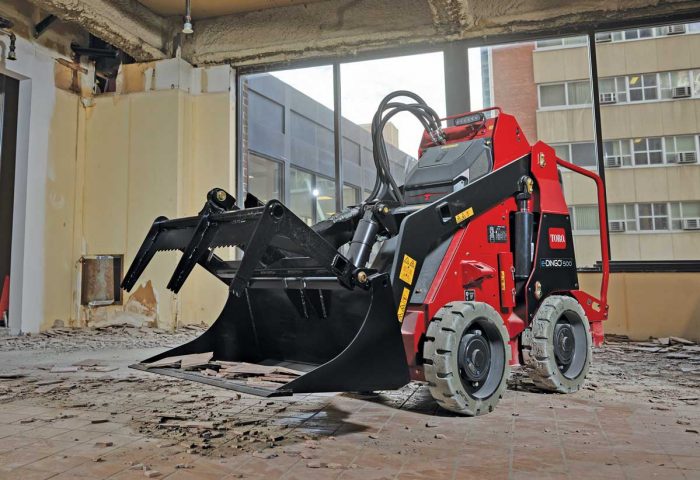
“Battery-powered compact utility loaders can be easily integrated with advanced control systems, allowing for sophisticated programming and customization. This enables enhanced automation, precision and efficiency,” explains Sam Dando, senior product marketing manager at Toro, which builds electric stand-on loaders, mowers and power buggies. “With the ability to add sensors and connectivity, battery-powered machines can support various smart functions more easily. These include real-time monitoring, predictive maintenance, remote diagnostics and over-the-air software updates. Smart functions improve reliability, reduce downtime and extend the lifespan of the equipment.”
Utilizing electric equipment is also a great opportunity to market a company as being environmentally conscious and less invasive. Both homeowners and commercial businesses appreciate eco-focused construction — especially when it means less noise and less fumes. Soon, projects may require them. Organizations like the California Air Resources Board are already setting rules for a zero-emissions automotive market. Off-highway equipment will likely be next. Employing electric equipment now allows companies and their customers to be good stewards of the environment and practice sustainability. That green halo is something contractors can also upsell to customers.
Keith Gribbins is publisher of Compact Equipment.