Breaking Down the Immersion Cooling Tech Behind Kreisel’s and John Deere’s Construction Equipment Battery Packs
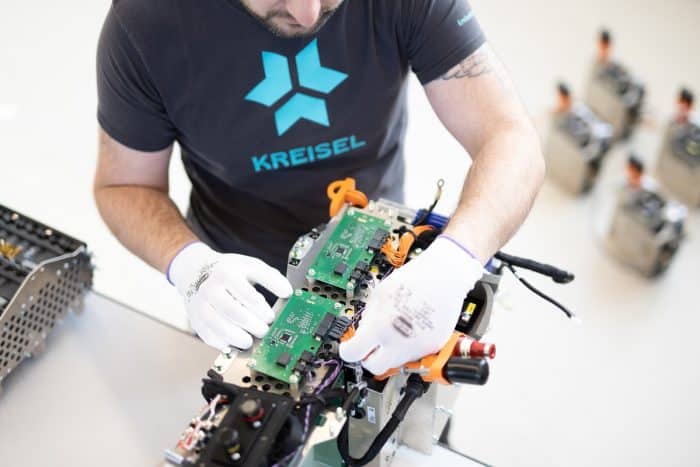
With so many different battery choices on the market today, it is important to understand the differences in technology making up the solutions that are powering the growing electrification industry. From cell types and packaging to cell chemistry and structure, there is a wide variety in overall battery design and technology to consider. The makeup of a battery plays a critical role in its performance, safety and reliability. With this in mind, Kreisel Electric (Kreisel) developed its battery packs with state-of-the-art technology that offers impressive lifetime and ultimate thermal management performance. This technology is the company’s patented immersion cooling technology. Together, John Deere and Kreisel are accelerating the development of this innovative battery technology and expanding the production capacity of Kreisel. (Note: John Deere acquired majority ownership of Kreisel in 2022)
Immersion Cooling
At the core of all Kreisel battery systems is a cutting-edge thermal management solution — the patented immersion cooling technology. Immersion cooling refers to a system design where a battery’s cells are immersed in a specific fluid. Kreisel’s solution features a non-conductive cooling fluid that is in direct contact with each individual cell, helping to achieve energy-efficient thermal management which provides excellent environmental conditions for every single cell.
The battery cells are immersed in a dielectric thermal management fluid that provides a unique low temperature spread of <1°C (1.8°F) throughout the battery module to ensure that all cells are within the same temperature range. As with all Lithium-ion batteries, consistent temperature control enables prolonged battery life and optimal performance.
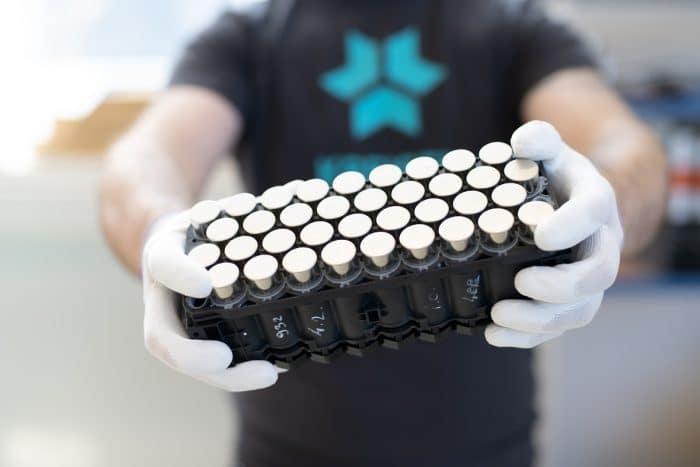
Performance features incorporated into each battery module provide fire propagation prevention, controlled degassing, and defective cell shutdown for efficient operation of the battery. Because each cell is individually fused, if an issue with a cell does occur, the cell can be isolated electrically, and the immersion cooling technology supports isolating the cell thermally to prevent propagation from spreading to the rest of the pack.
Efficient Performance
Battery efficiency is closely linked to the energy required to either heat up or cool down the battery to achieve its optimal operating temperature. With the Kreisel solution, thermal transfer efficiency is maximized due to the specialized non-conductive fluid that has strong thermal management properties. Fluid touches more of the surface of the battery cells than other solutions commonly used in the automotive industry, such as conventional base plate and side wall cooling. Also, the fluid is in direct contact with the cell surface so there are no thermal transfer barriers impacting efficiency.
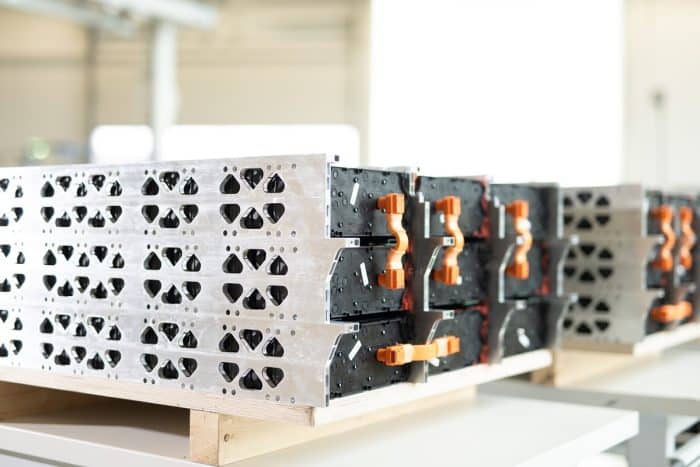
When battery cells are efficiently kept at optimal operating temperature, the benefits are optimized range, lifetime and excellent performance. The performance of many battery systems can be negatively impacted by extreme temperatures. Kreisel provides a technology that is capable of operation in -40°C (-40°F) up to +70°C (+158°F) ambient temperature, provided the vehicle thermal system is matched to these conditions.
A Growing Portfolio
As more of the off-highway industry looks to electrify their equipment, there will be a significant need to have scalable power and battery configurations that can meet unique energy and design needs across applications and equipment sizes.
To meet this growing need for diverse battery sizes, Kreisel has introduced three new concept batteries that build off the modular design of the 63-kWh KBP63 battery. The two concept batteries at 38-kWh 750 V max can be used in parallel to meet larger power needs. The 20-kWh 400 V max battery can be connected in series or in parallel for extraordinary packaging flexibility.
With up to 750 V from a single pack and flexible dimensions, these new models offer industrial and marine customers increased packaging flexibility and utilize Kreisel’s modular architecture and patented immersion cooling technology. With the addition of more diverse sizes, Kreisel can offer OEMs even more versatility for application packaging and enable smaller vehicles to take advantage of high-performance Kreisel batteries.
To learn more about Kreisel battery technology and the company’s growing battery portfolio, click here.
Preston Moore is a product planner for battery and charging solutions for John Deere Power Systems.
Developing Charging Infrastructure
An efficient, well-made battery is only as good as its charger. John Deere recognizes the important role and opportunity that charging infrastructure presents when it comes to the successful progression and adoption of battery power as an industry. The company is working to develop comprehensive charging solutions customers can rely on to run in rugged environments. Like batteries, charging requirements will differ by market segment and applications — conceivably needing both stationary and mobile options and versatile ranges and charge times. That’s why John Deere is building out a diversified battery portfolio and developing a charging ecosystem, starting with the Kreisel Chimero battery integrated charging station to meet operating conditions on a variety of jobsites.