The Big Benefits of Telematics for Compact Track Loaders (from Security to Maintenance)
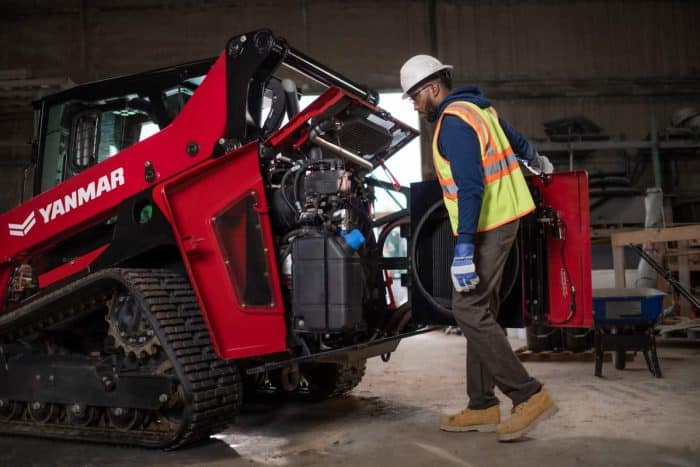
Running an equipment fleet is no picnic, though you could compare it to one. An enjoyable outing requires you to choose reasonably priced food that people will appreciate and make use of, the spread has to be easy to manage and cleanup should be straightforward. Fleets are a similar story. Equipment needs to fit the balance between reasonable acquisition cost and likely productivity and utilization. It should be easily tracked for purposes of operating hours and maintenance, and that maintenance must ultimately be straightforward to limit downtime.
Most construction, rental or utility fleets include a variety of compact equipment to tackle the meat of the majority of jobs. When adding units, fleet managers should consider features and qualities that ensure maximum performance for the price, fleet tracking capabilities such as telematics, and equipment that offers both reliability and ease of serviceability. Like in a picnic, the reward will be less hassle and a more filling experience. And unlike a picnic, it may mean savings of thousands of dollars in increased productivity.
High Technologies on Track Loaders
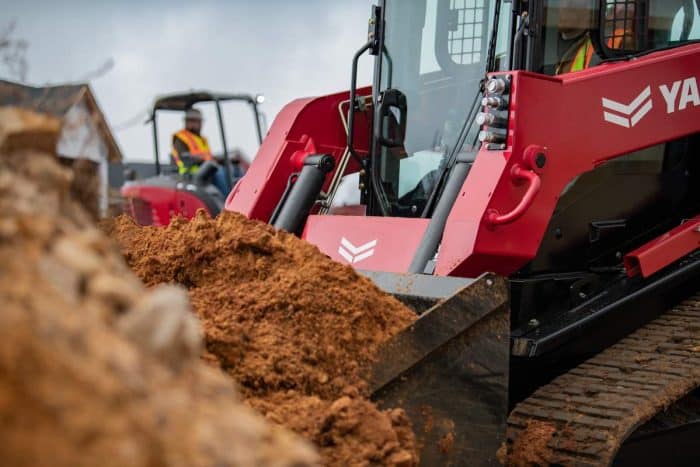
One of the first questions is whether the compact equipment’s acquisition cost can be paid off with high utilization. The most promising equipment is reasonably priced but still boasts the productivity, versatility and overall performance features needed to keep it in the field day in and day out.
Consider technology features. There are a number of technologies that can boost performance and efficiency. For example, some equipment features a load-sensing system that offers both improved efficiency and fuel savings that contribute to ROI. The system regulates the hydraulic pump, so it only produces what’s necessary to complete the work rather than using maximum flow all the time.
Other technology features speed up tasks or get new operators working on their own more quickly, keeping utilization high. While most only include one, some compact track loaders include a combination of return to position and work tool position features standard with the base machine. The work tool positioner allows operators to create a preset for the angle of the attachment based on the task at hand, allowing the tool to return to the set angle at the push of a button. Return-to-position technology complements the work tool positioner by allowing operators to set a designated height for the loader arms. The technologies can be paired together or used independently to adjust to jobsite needs. This expedites repetitive tasks such as truck loading or pallet unloading where the attachment needs to be at a certain height and angle. Additionally, it means repetitive tasks can be completed with similar levels of productivity regardless of whether the operator is experienced or new to the controls.
Speaking of controls, customizable operation patterns allow operators to match the machine to their preferences and application and likely increase productivity. For example, if they are used to ISO controls instead of H controls, a machine that allows them to choose will have a smaller learning curve. Operators can also change settings like response time speed to adjust to their working style. This means more efficiency out of machines that see more than one operator and the likelihood that operator skills will increase as they are working with familiar controls each time.
Compact track loaders are the most popular category of compact equipment in America. Learn why with loads of track loader features right here.
A compact track loader’s tracks can also greatly affect its versatility and performance. The machine type is well known for having lower ground pressure than wheeled equipment, but not all tracks are created equal. Consider choosing a loader with premium bar tread tracks for increased flotation and traction on a variety of ground conditions. The benefit is the potential for year-round performance without needing to pay for a separate set of winter tracks.
Suspension systems can increase a compact track loader’s value to fleets. Not always included standard, suspension has the obvious benefit of increasing operator comfort and therefore boosting productivity on long days and potentially helping retain skilled operators in an ever-shrinking worker pool. Also, consider machines with comfortable cabs and extra visibility to make operating the equipment even more of an experience.
Suspension also contributes to increased efficiency and machine durability. A suspended system can limit material loss when traveling over bumpy terrain, especially when paired with self-leveling and ride-control features. Additionally, reduced vibrations throughout the machine can prolong component and overall machine life.
Fleet Management is a Gamechanger
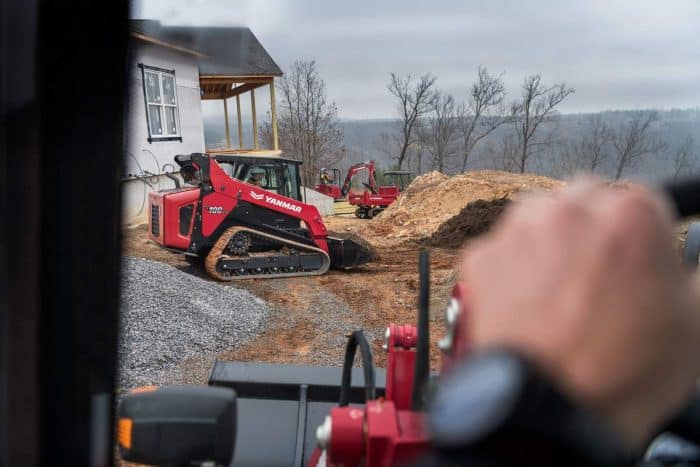
Telematics is a well-known gamechanger for compact equipment fleets that offer greater convenience, more control and easily identifiable ROI. A fleet outfitted with telematics can allow a manager to pull up operation and service data on all machines in a fraction of the time it might take them to either check on each piece of equipment manually or call individual operators. This provides several benefits, from confirming an operator completed the work they said they did, to providing the ability to schedule maintenance based on error codes logged by the system. The feature helps negate operator forgetfulness or inaccurate reporting. For example, a telematics system may alert a service manager to low oil pressure on a compact track loader. If this was left up to the operator and they forgot to report it and kept working, it could mean expensive engine failure and replacement.
Some telematics systems also come with integrated location tracking and geofencing, allowing for both management of equipment location and theft protection. The systems allow the fleet owner to set a range from a specific location and trigger an alert if that range is exceeded.
Telematics features can vary from manufacturer to manufacturer, so it comes down to which functions a fleet manager feels would be most beneficial and would provide the most value for the cost. Prices can vary, but some manufacturers offer telematics free for as many as five years on mini excavators with the purchase of a new machine.
Maintenance Matters
There’s no question that fleets benefit from the greatest ease of serviceability and reliability possible for equipment within their budget range. Time is money, so features that speed up the maintenance process pay for themselves. Ease of service features such as three-panel doors that open to the engine compartment can mean a faster turnaround before the equipment is out working again.
Compact track loader designs that include easy access to drain and fill plugs can reduce maintenance time compared to configurations that require track removal for motor oil changes. Also, consider fuel and hydraulic filter mounting and access. Some designs allow for faster changeouts and easier access. Rigid-mounted, spin-on fuel filters tend to be more convenient, compared to insert filters that are often hidden deep in the engine bay. Additionally, vertically mounted filters are less likely to make a mess than horizontally mounted versions. The difference between the designs could mean hundreds of dollars every year in labor costs, not to mention lost work time.
Whether the compact track loader has accessible grease points is another point to consider. Some feature Zerk fittings on the end of pins rather than the side to ensure quick and easy greasing. As an example, if an operator can save 10 minutes per day with more efficient greasing and works 200 days a year, they could save around 66 hours in just two years. That equates to about $3,000 in labor, not even counting the billable hours the machine was not working.
The equipment should also be able to stand up to the rigors of daily work and different operators and experience levels. This could mean cylinder guards on a mini excavator, or a construction-grade undercarriage on a compact track loader.
Lastly, fleets should consider choosing equipment from a manufacturer with a history of reliability. A reliable OEM will have a meticulous manufacturing process, executing regular checks and audits on the quality of their components. Look at their warranty options to see how they back their quality claims. Some mini excavator brands, for example, offer warranties double the standard length.
The Cherry on Top
Like the food you choose for a picnic, a fleet’s equipment choices can make or break the experience and the budget. Choosing carefully will maximize the speed of the return on investment, meaning more room in the budget for fleet expansion, personnel and other improvements that make the equipment purchase a sweet success.
Buck Storlie is aftermarket director for Yanmar Compact Equipment North America.