Hydraulic Maintenance: Ensure Your CTL’s System Stays in Good Condition for Better Productivity
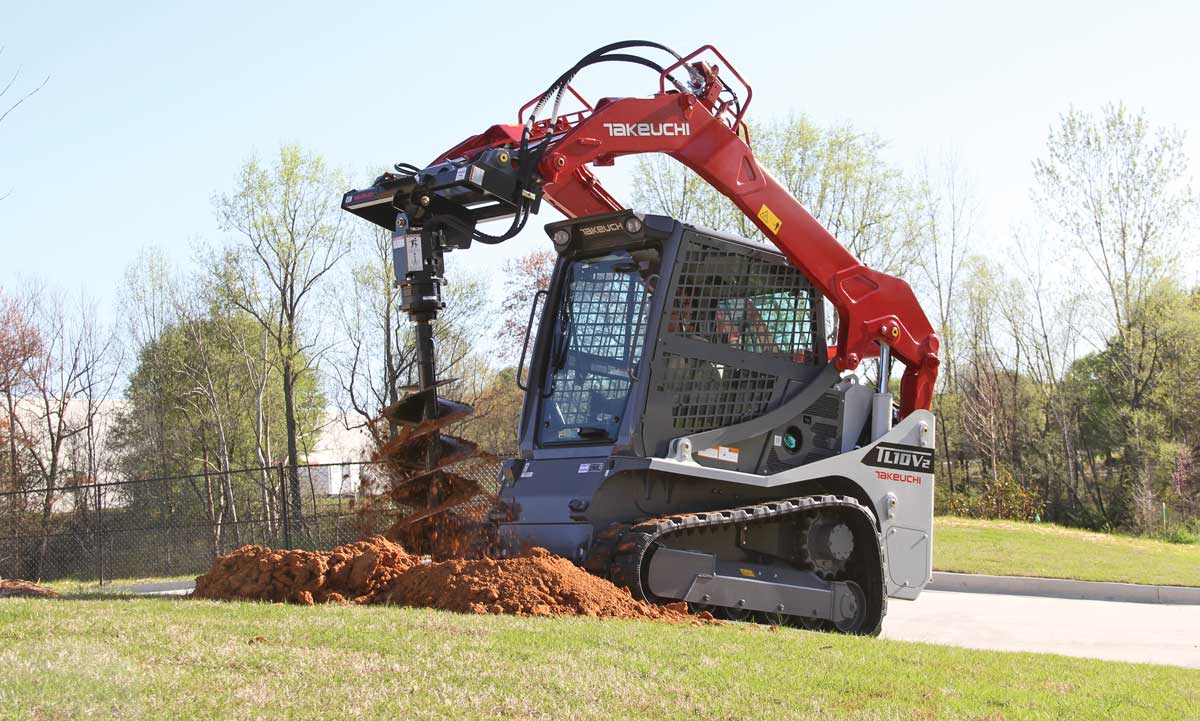
The compact equipment market continues to grow, and that growth can be attributed to many different factors, including increased spending on residential building and construction overall. Compact track loaders (CTLs) are now the most popular compact equipment category due to their high traction, low ground pressure and significant pushing power. However, perhaps the most significant reason why compact track loaders lead the compact equipment category is their versatility, and that versatility is due in no small part to the increasingly wide variety of attachments compact track loaders can use when outfitted with the proper hydraulic system.
Over the past few years, hydraulic systems have become increasingly sophisticated while also offering better lifting capacity and breakout forces thanks to larger pumps and higher pressures. In fact, these systems can help compact track loaders themselves perform tougher jobs without requiring more horsepower, which keeps costs and emissions down. But it’s the fact that improved hydraulic performance makes it possible to connect multiple attachments that truly sells these machines.
“Hydraulic systems make so many tasks possible today,” said Joseph Huling, national service and training manager for Takeuchi-US. “Before these systems became so advanced, you couldn’t use a compact track loader to clear land quickly and efficiently, remove snow, handle large quantities of materials and so on. Hydraulics are key to making these machines little powerhouses that can do so much more than lift and place. Potential buyers see how much compact track loaders can do, which leads to a greater return on their machine investment.”
Huling goes on to say that before these advanced hydraulic systems were available on compact track loaders, the machines could only use a limited number of attachments — and for shorter periods of time.
“Today’s more efficient hydraulic components and cooling systems mean you can operate hydraulic attachments longer without wearing out the carrier machine,” Huling said. “That makes these machines more productive in multiple ways.”
Keeping hydraulic systems in good working condition starts with ensuring they’re paired with the right attachments. Using attachments that exceed the carrier unit’s hydraulic flow and pressure specifications or require the carrier unit’s settings to be at maximum levels will result in increased wear to the carrier unit. Additionally, using attachments that are undersized relative to the minimum flow and pressures settings will overburden the system and potentially damage the attachment, seals, components and hoses. From there, it’s all about proactively maintaining these advanced systems properly to ensure they’ll keep performing their best for years to come.
Compact track loaders are the most popular category of compact equipment in America. Learn why with loads of track loader features right here.
“It’s important to be proactive and perform regular, routine maintenance to safeguard your compact track loader’s hydraulic system from even the smallest contaminants,” Huling said. “You can’t wait until there’s a problem to maintain these systems. Today’s hydraulic systems are more refined, making them extremely sensitive to contamination. If you don’t keep the system clean, you could drastically shorten its life or completely destroy its components.”
Huling says that Takeuchi recommends the following maintenance schedule for its hydraulic systems:
Daily:
- Check fluid levels.
- Drain any fuel/water separators.
- Look for damaged lines, cylinders and hydraulic leaks around the machine.
- Clean hydraulic attachment couplers before connecting to the machine.
- Pay attention to hydraulic oil temperatures, particularly when running high-flow attachments like mulching heads.
- Remove any flammable debris from the machine’s belly.
Weekly:
- Check the machine over for any loose fasteners, repair any damages and adjust the track tension.
Monthly:
- Clear any debris from the machine.
- Clean the radiator and cooling package fins to ensure sufficient airflow.
- Inspect and replace engine air filters.
Annually:
- Take fluid samples to ensure hydraulic oil and
- vital components are at acceptable particle levels.
- • Always replenish fluids according to the manufacturer’s recommendations.
- • Check and replace the fan belt if needed.
- • Inspect undercarriage.
At Other Intervals:
- Most manufacturers have a new machine “break-in” period, typically after the first 50 hours of operation and recommend checking hydraulic components at that time.
- Follow scheduled (hourly) maintenance when replacing hydraulic oil and filters.
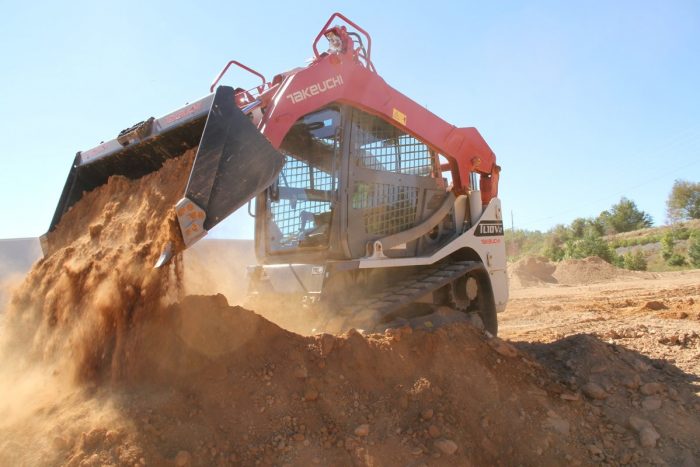
“With today’s common rail diesel engines, daily inspection and draining of the fuel/water separator is very critical, as is checking fluid levels on the machine,” Huling said. “This, combined with removing debris from the belly pan of the machine, loader arm towers and hydraulic cooler as needed, will ensure consistent performance and less downtime.”
While conducting routine maintenance is paramount for long hydraulic system life, so is cleanliness. When swapping out attachments on the jobsite, keep dirt and other contaminants from entering the hydraulic system by cleaning the attachment’s fittings, both on the machine and the attachment itself before connecting it. When removing a hydraulic attachment from the carrier, clean the automatic fittings and protect them from debris during storage and usage intervals. If the hydraulic fluid is low on the carrier unit, clean the refill cap and surrounding area before replenishing it.
“It’s also very important to connect only attachments that are new, inspected or known to be in good working condition,” Huling added. “If you don’t, you may introduce contaminated oil into your machine from a used attachment, or worse, connect a failing attachment to your machine, resulting in damage to the hydraulic components on the carrier unit. If purchasing a hydraulic attachment from an unfamiliar source, I’d recommend having an inspection performed by a reputable dealer or hydraulic specialist prior to connecting the attachment to the carrier machine.”
Operators themselves can also implement best practices when using their compact track loaders’ hydraulic systems to ensure they’re not generating unnecessary wear and tear. Those best practices include ensuring the attachment’s cutting teeth are sharp (when applicable), removing any buildup of material in the attachment housing and allowing attachments to do their job without requiring additional force from the machine itself. It’s also imperative to allow for adequate cooling intervals between operational cycles. Doing so ensures you’re not operating the machine outside of normal operating temperatures and putting additional strain on the hydraulic system.
“The bottom line is that if you take care of your loader’s hydraulic system, it will take care of you,” Huling said. “Machine owners simply need to follow their manufacturers’ maintenance recommendations and timing. That’s the most important step to keeping hydraulic systems running smoothly. No one wants a breakdown in the middle of an important job. While it may take time and effort to perform daily, weekly, monthly and annual services, it will pay off with greater machine productivity in the long run.”
Lynette Von Minden is a public relations manager at Swanson Russell.
For reprint and licensing requests for this article, please click here.