Optimize Your Mini Skid Steer Performance with Daily, Weekly and Monthly Track Inspections and Maintenance
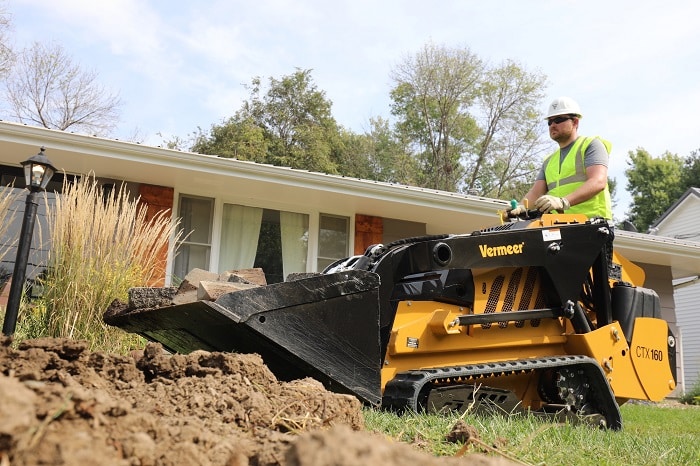
On machines like mini skid steers, operators have found that sustaining traction, minimizing ground pressure and compaction and providing high levels of steering precision are beneficial for any jobsite. But, in order to check all those boxes, mini skid steer tracks have to be adequately maintained with regular inspections, jobsite preparedness and both short- and long-term planning.
Different components call for inspection at varying intervals to help optimize the machine’s performance. Many major components — like tracks — require attention based on specific hours of operation. Typically, new tracks can see the most wear during the first 20 hours of operation, so an early inspection is a good idea, according to Vermeer Landscape Market Manager Brett Newendorp. From that point forward, he recommends the same detailed inspection every 50 hours of operation.
“For most operators, that means being prepared to make adjustments about once a month,” he said.
Why the Right Track Tension Matters
Track tension is the top priority to help sustain mini skid steer performance and longevity on most jobsites. Spring mechanical tensioners help maintain track tension over time, meaning adjustments are typically not necessary more than once a month. But, it’s important to spend daily inspection time making sure you’re operating within the right range of tension specified in the machine’s operator’s manual. Failing to do so can have costly long-term effects.
“If your tracks are too tight or loose, it can allow tracks to come off the frame, rollers or idlers,” Newendorp said. “It’s efficient to get them back on if you have the right tools in the field, but rollers, idlers and sprockets on the ground drive will see a shorter life if they’re not operated at the right tension.”
Mini skid steer tracks naturally loosen during normal operation over time, and an experienced operator can usually feel differences in machine vibration and sound during operation, indicating adjustment or more serious maintenance is required. Operators should follow the manufacturer’s guidelines found in the manual when performing routine daily track inspections prior to operating. And when adjustment is required, be sure not to overtighten, as that can also cause tracks to slip off rotors and result in premature failure.
“Our tracks have steel cords and bars running through them inside a rubber outer layer. Our goal is that our system is efficient for operators to adjust and maintain,” Newendorp said. “Rollers and idlers will see shorter life if they’re too loose or tight. If you’re overtightening them, you’re putting excessive pressure on the shaft of the ground drive motor, and that can lead to a hydraulic issue.”
Daily Inspection for Debris and Obstructions
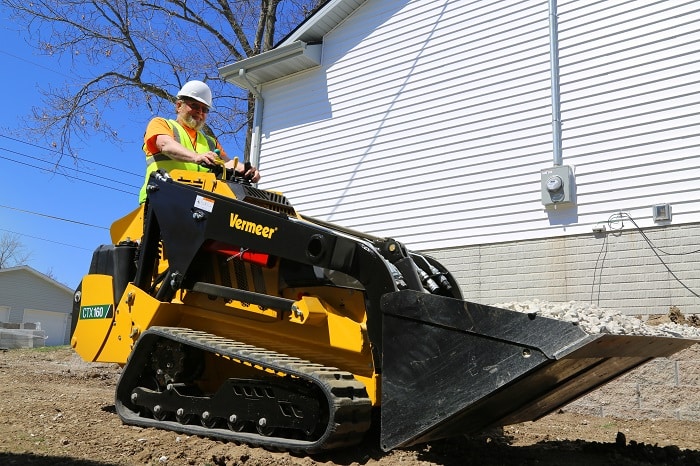
Where and how you operate your mini skid steer will contribute a lot to the lifespan and performance of your tracks over time. The type of terrain on which most mini skid steers are operated affect track longevity and maintenance. Though driving over hard, smooth surfaces more frequently helps keep tracks clean and free of debris, surfaces like concrete and asphalt can shorten the lifespan of the tracks’ outer rubber surface more quickly than operating in softer terrain, like soil. But that softer terrain is typically more likely to contain debris, like branches and rocks, that can inflict damage to track components.
Regardless of the primary terrain, Newendorp recommends checking overall track condition and cleanliness during daily inspections, concentrating on the condition of the tracks’ exterior and any debris that may have worked its way inside the track system during regular operation.
“You want your daily check to include the cleanliness of the tracks. Clear them of large pieces of debris and give them a good washout,” Newendorp said. “Operating on concrete and asphalt can be like sandpaper to the outside of the tracks. Once you get abrasive debris inside them, internal components may experience premature wear, especially when it gets between the roller and track itself.”
The likelihood of damage from debris is also affected by how well tracks are tensioned during routine inspection; if too loose, tracks are more likely to be infiltrated by debris, Newendorp added.
Weekly and Monthly Adjustments
Beyond a daily inspection performed prior to each day’s operation, Newendorp recommends a weekly check of more specific track system components to make sure the system is running smoothly.
“Every week, check on the rollers and idlers, listening for squeaks, looking for flat spots and making sure rollers and idlers are running smoothly,” he said.
And though it’s important to inspect tracks for the right range of operating tension on a daily basis, major tension adjustments typically are necessary on a monthly basis. With the combination of a gauge in the operator’s manual and a straightforward combination of tools and onboard adjustment bolts, the operator can take on the adjustment process during routine monthly maintenance.
“We’ve made it efficient with a spring mechanical tensioner and slots in the side where the machine indicates whether your tracks are properly tensioned or not,” Newendorp said. “If required, adjusting the spring is a matter of tightening or loosening a set bolt and one other bolt.”
Optimal performance and longevity of your Vermeer mini skid steer depends on inspection and the right routine maintenance in a variety of time frames during normal operation. An experienced team can help the process run smoothly. Contact your nearest Vermeer dealer and learn more about routine track maintenance for your mini skid steer here.