Turn Debris into Profits: Learn to Size, Buy and Operate a Compact Crusher
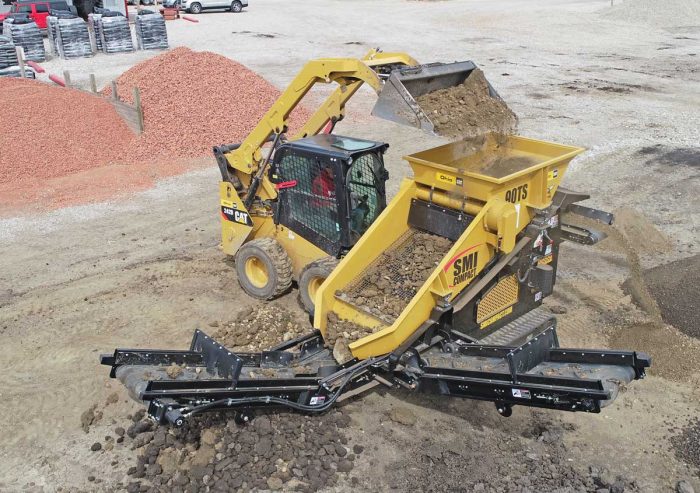
If you think the world of crushing and screening aggregates is reserved for big highway and demolition contractors, think again. In the last decade, manufacturers have taken this technology and packaged it into smaller machine sizes. These downsized crushers offer benefits almost any construction contractor — large or small — can enjoy.
“The core customer for our crusher lineup is the small- to mid-sized contractor, even the guy who is doing a few driveways a week or municipal curb and gutter work,” says Rob May, general manager at Senya Crushers.
Compact crushers can be set up in as little space as it takes to park a handful of cars, says May. Many of these machines can be towed by medium-duty pickup trucks, eliminating the need for haul trucks and permits. The majority of these machines are on tracks so they can be easily moved from pile to pile on a site.
“We brought our compact line onboard in 2017,” says David Stewart, director of marketing at SMI. “At that point compact crushing and screening was practically non-existent, and now it’s a pretty significant market. It’s just like compact skid steers and excavators. It lets the little guys do bigger jobs more easily.”
Making Money
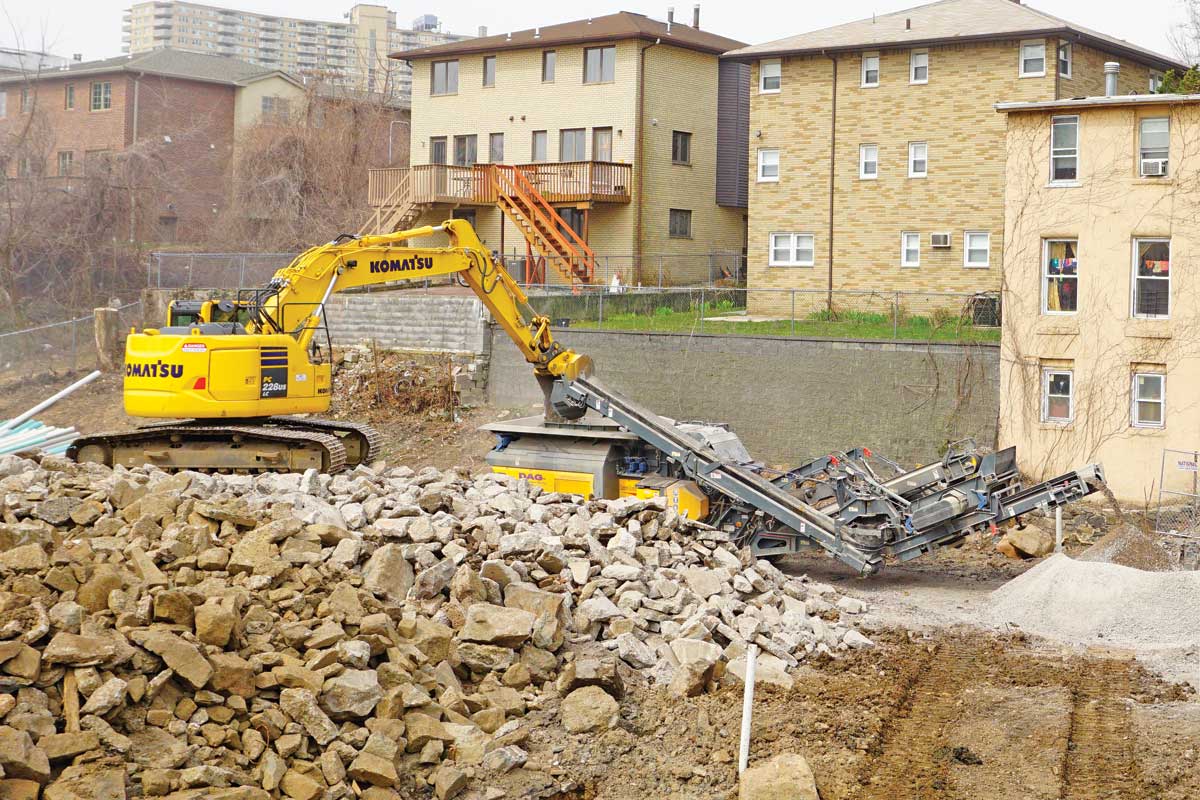
“The first thing that will happen after you buy a compact crusher is that you will start seeing money everywhere,” says René Wagner, marketing manager, Rubble Master Americas. “You’ll be driving down the highway and think, ‘Yeah, I could crush that.’ It’s a way to outmaneuver the competition by being in control of your material costs and producing your own quality aggregates. You can often make the payments on a crusher by running it as little as a couple of hundred hours a year.”
Transportation of materials is a big part of this equation. “Every time you touch the material it costs you money,” says Stewart. “The fewer times you have to handle it, the more profitable you’re going to be.”
If you rip up a sidewalk or driveway, throw the slabs in a dump truck, haul it off to be crushed at a remote site and then haul it back to be used as base material, you’ve just paid double for that material. And even if you just dump the material at a construction landfill, the fees alone can run into hundreds of dollars. Onsite crushing eliminates not only these labor and transportation costs, but the costs you pay for new aggregate.
“Many of our customers generate tremendous income recycling or processing byproducts of their demolition such as concrete, block and brick, glass and granite countertops,” says May. “We even have ranchers graveling their own roads from the rock on their land. The decorative gravel business can be huge as well with some material fetching as much as $200 to $300 per ton.”
Applications Unlimited
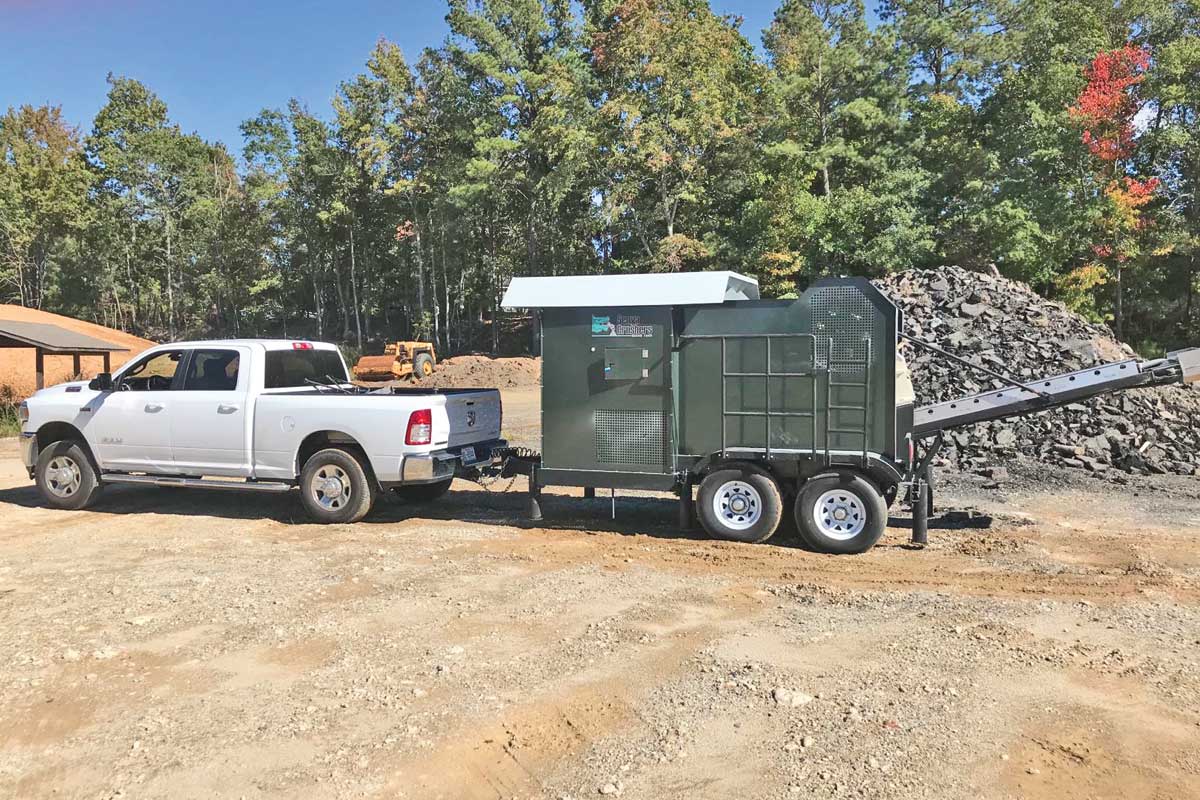
The number of applications for a compact crusher is broad and touches on dozens of different construction practices, says Cody Price, operations manager at Komplet. Some of these include:
- Urban construction sites where streets and buildings restrict transportation access.
Demolition sites where room to maneuver a crusher, conveyors and screens or the loading machine is limited. - Landscaping and earthmoving. Whether its old concrete or brick structures or boulders and environments with large rocks, compact crushers can eliminate the problem and if needed provide aggregates for the next phase of construction.
- Recycling centers. Municipal dumps and construction landfills can take advantage of on-site recycling and generate new revenue streams by selling the finished material.
Interior demolition. The smaller sizes of compact crushers can work inside buildings such as warehouses and industrial facilities. - Large aggregate operations that need convenient, short-term crushing work. “We have one customer who has set up half a dozen concrete recycling drop sites as close as 10 to 15 miles from their main crusher, but the savings in transportation costs make it worthwhile,” says May.
Compact track loaders are the most popular category of compact equipment in America. Learn why with loads of track loader features right here.
Machine Design
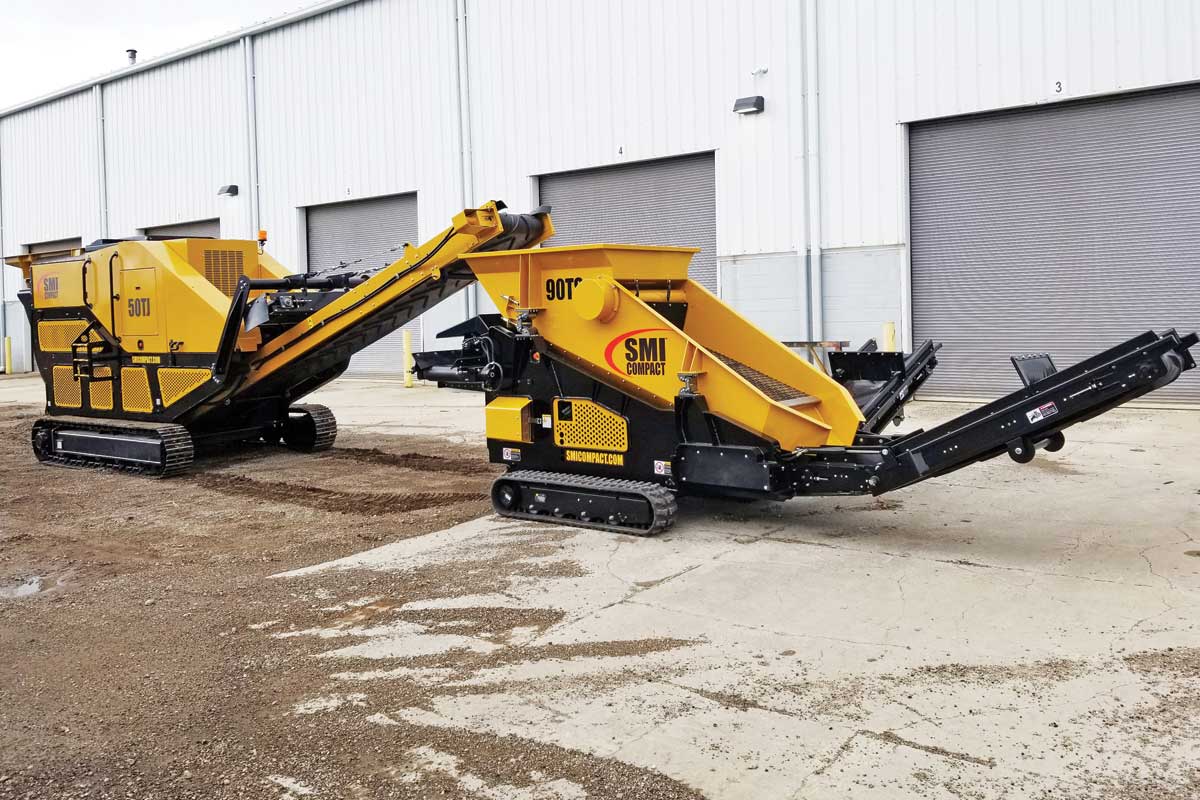
Choosing the right type of crusher depends on factors such as the type of material, the desired product size, and the production capacity requirements, says Price.
Jaw crushers use compressive force to break down materials. The crushing chamber has a fixed jaw and a moving jaw, says Price. The moving jaw is attached to a pitman that moves back and forth creating a swinging motion. Jaw crushers are generally more affordable and best suited for hard rock and an initial reduction in size. Jaw crushers produce a coarse non-spec material. Jaw crushers have a simple structure, and maintenance is generally easy.
Impact crushers use impact force to break down materials. The material is picked up by a fast-moving rotor and slammed against the impact plates or other materials, says Price. They are well suited for soft- to medium-hard materials, concrete and asphalt. They also create a more uniform size of finished product for applications requiring aggregates that must meet DOT or engineering specs. Impact crushers have more maintenance, needing to change consumables more often because the machine works harder and reduces the material further.
Cone crushers use a rotating piece of steel against a stationary piece of steel to reduce material by compression. The material is crushed by squeezing it between the mantle and a concave surface. They are well-suited for hard and abrasive materials but are not typically found in compact crushers.
Operational Tips
A skid steer or compact loader is sufficient to feed the smallest compact crushing machines. These loaders also have the advantage of being able to sweep the site clean of debris and move stockpiles when not feeding the crusher.
But excavators have advantages too. For example:
- Excavators typically don’t hold as much material in the bucket as loaders and are less likely to overload the crusher.
- With an excavator you can see what’s going into the bucket and avoid dumping large chunks of metal, tangled rebar or over-sized material in the hopper.
- Using the bucket, a good excavator operator can sort and segregate these unsuitable materials for handling later, says Wagner.
- An excavator with a thumb is better at grabbing material and, if need be, pull a too-large chunk of material out of the hopper.
- Depending on the job, a compact excavator with a hammer attachment may be useful in reducing concrete slabs to manageable sizes. This can also be done with an attachment on a skid steer, but excavators are better at it.
- Excavators will also give you flexibility in jobsite layout. Wheeled or tracked loading machines require a V-shaped path from the point where they load to the point where they dump, whereas an excavator can swing back and forth between the pile and the crusher without having to reposition itself.
Get to SPEC
If you are interested in crushing materials to a specific size and shape (DOT or construction spec) on a regular basis, a common setup is to use both a primary (jaw crusher) and a secondary (impact crusher) to create uniform aggregates that meet specific engineering standards. You’ll also need a conveyor to feed a mobile screening plant to segregate your aggregates that meet various engineering specs. Screening plants can also serve double duty and screen topsoil, mulch and other materials used in landscaping operations.
Operators Are Key
“An experienced loader operator is worth is worth his weight in gold,” says Stewart. “If the material jams up, somebody has to go up there with a pickaxe or wedge and start moving the blockage out. That can turn into a day-long affair and send your tons-per-hour number through the floor.”
The crusher operator also has an important role to play. If he sees a piece of rebar that might get tangled up inside the crusher or tear a hole in the conveyor belt, he can prevent that from becoming a bigger disaster. “Don’t throw rebar spaghetti into the crusher,” says Wagner. It’s not a rebar crusher, and it’s not a dump truck. You want to make sure the rebar is encapsulated in the concrete before loading it.”
Homework Required
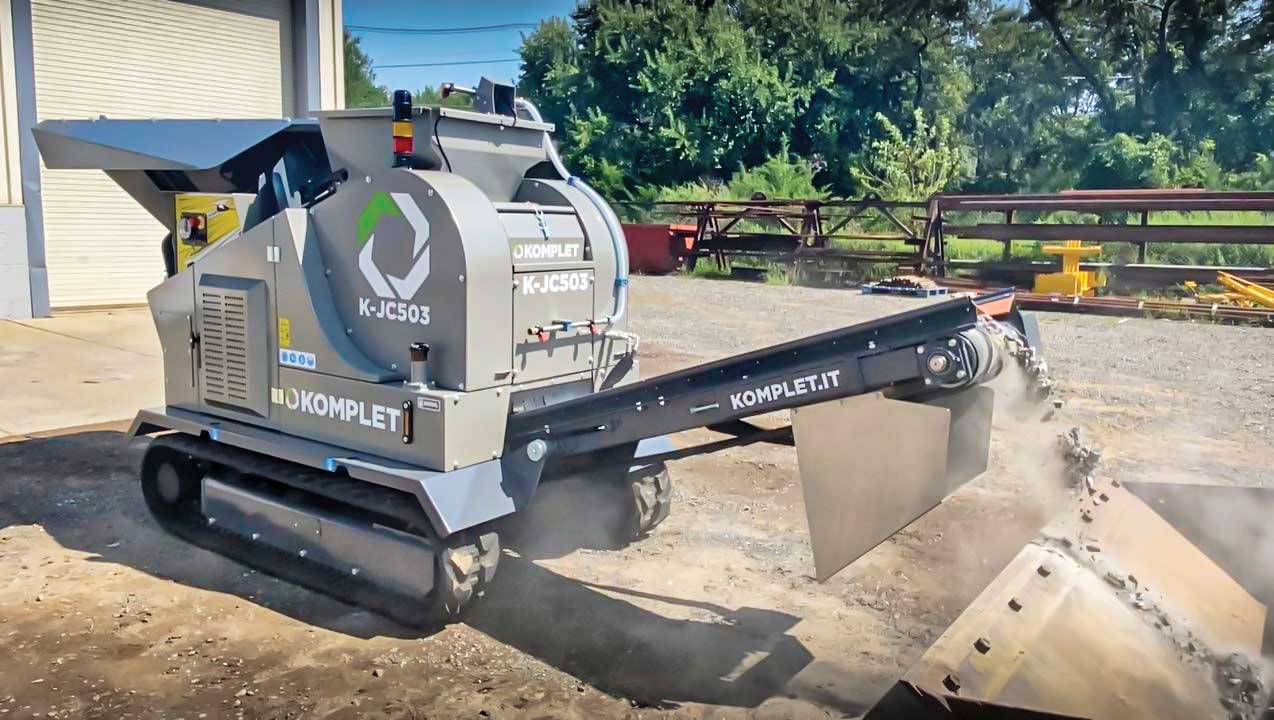
Some people buy crushers online or at auctions. Without any guidance they may run into problems or disappointing results down the line, says Wagner. Crushing may be a brutal process, but it takes a bit of science, knowledge and experience to do it efficiently.
Before you acquire a compact crusher, Wagner recommends that you get a materials expert to look at your jobsite and talk you through the economics of crushing. To maximize profits and tons-per-hour, you need to choose the right size of machine and the right type of crushing technology matched to your raw materials and jobsite conditions. A key point to remember, says Wagner, is that if you can’t reuse or sell your crushed material you have accomplished nothing.
Tom Jackson is a freelance writer for Compact Equipment.