Six Ways to Improve Equipment Safety
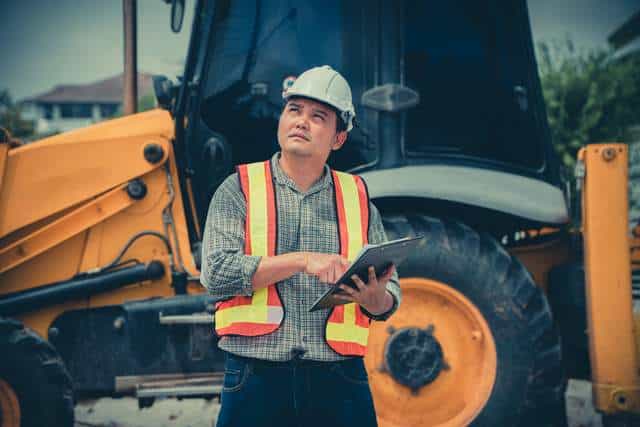
When working with large equipment, workers face some significant risks — like electrocution and “struck-by” incidents. Poor visibility, the size and weight of even the most compact equipment and construction site noise can all make maintaining equipment safety even more difficult for workers and site supervisors.
Fortunately, any construction company can significantly improve the safety of their working environment with the right adjustments to safety practices used around construction equipment. With these six strategies, any construction company that values safety can ensure their machinery avoids creating any unnecessary risks:
1. Have a Strong Maintenance Plan in Place
Mechanical failure can cause massive safety issues and is undesirable for other reasons — like putting equipment out of service and delaying work. A regular maintenance schedule is essential to keeping heavy equipment in good condition. Typically, daily checks before operating the machinery are necessary to catch any issues with the equipment undercarriage, hydraulics, oil levels, lights and other components.
Maintenance checks and repairs should always be carried out by trained technicians. Even a simple maintenance inspection presents the opportunity for internal systems to sustain damage. Intake valves may pull in dirt when tested, and electronics can be short-circuited by dust. Repairs by untrained workers present even more opportunities for mistakes and errors that can lead to mechanical failure down the line. Supervisors should also ensure technicians use proper lockout/tagout safety measures when performing maintenance on a piece of equipment. Doing this will ensure the machine in question isn’t in use while upkeep occurs.
2. Consider Advanced Maintenance Tech
For companies willing to adopt some advanced tech, they may consider predictive maintenance, which can be more cost-effective and efficient than preventative maintenance. With predictive maintenance, construction companies use wireless telematics systems that track operational data, like vibration, heat, lubrication and speed.
The company then uses that data to decide when maintenance checks and repairs need to happen, rather than wholly relying on a predetermined schedule. Predictive maintenance scheduling can help technicians avoid checking equipment that doesn’t need a checkup or missing issues that may arise in between pre-scheduled maintenance checks. Predictive maintenance can also help construction companies avoid some of the damage that can be caused by overzealous preventive maintenance scheduling.
3. Implement Robust Equipment Safety Training
Training is the best way to ensure workers know the potential risks and dangers of heavy equipment. Even something as straightforward and necessary as requiring workers to have training in any relevant Occupational Safety and Health Administration (OSHA) regulations will ensure both safe operation of tools and safe practices around compact equipment.
Both equipment operators and spotters should always have the necessary training and an understanding of how they’ll communicate on site before work begins. They should also know about any quirks or special requirements of the equipment they’re working with — like blind spots, maximum loads and proper techniques for mounting or dismounting the machines. Where necessary, operators and spotters should also have relevant certifications. Workers other than spotters and operators should also know best practices for staying safe around construction equipment. In general, they should be able to describe to supervisors the risks they’ll face on site.
4. Make Communication a Top Priority
Machine operators and spotters should constantly communicate, both with each other and the workers around them. This is the best way to ensure all employees in the area are aware of a machine’s movement, the operator’s plans and potential safety risks. A two-way radio is one of the best ways for spotters and machine operators to talk. In a pinch, hand signals and other communication methods that won’t be hampered by equipment or site noise can also be effective. Both spotters, operators and nearby workers should avoid using other communication devices, like smartphones, while a machine is operating.
5. Establish Pre-Planning Methods That Cover Site Risks
Before a construction company uses any equipment, it should make sure it has considered all possible site risks. Power lines, uneven grading and water can make the safe operation of heavy equipment much more difficult. If a machine operator needs to work on a site with these conditions, their supervisors should communicate the potential risks and ensure they know what standards to follow or safety practices to establish before they begin work.
Construction companies should also be aware of any equipment-related OSHA regulations they need to follow. For example, the employer is responsible for making sure the ground is both level and firm enough to support heavy equipment and vehicles. Employers will also need to ensure any compact equipment doesn’t operate in reverse gear if its rear view is obstructed — unless the machine has a reverse alarm or there is a worker to signal when the equipment is moving backward.
6. Adopt Advanced Safety Technology
In some cases, advanced safety tech may help construction companies manage some of the risks of using compact equipment. GPS tracking software can give site supervisors an instant picture of where workers and equipment are on site. This tech can help managers coordinate more effective responses in case of machine failure or accident. Because they know exactly where the machinery is located, they won’t need to spend time searching for the workers who need assistance.
Other types of tech, like a radio frequency identification (RFID)-based alert system, can alert the operator when an on-board safety system detects a worker behind or in front of the equipment they’re operating. This kind of system, combined with reverse alarms and a spotter, can ensure workers and operators have multiple lines of defense against a potential accident.
Making Equipment as Safe as Possible
Compact equipment comes with an inherent level of risk. Without the proper safety precautions, the operation of construction equipment can be extremely dangerous. This means that good safety practices will be essential for businesses that want to reduce the risk of incidents. Communication, pre-planning and robust safety training are some of the best ways to ensure equipment safety. The adoption of effective mechanical practices — like predictive maintenance or advanced safety tech — can also make these machines safer during use.