Diving Deeper into Machine Health: Regular Inspections, Fluid Sampling, Telematics and More
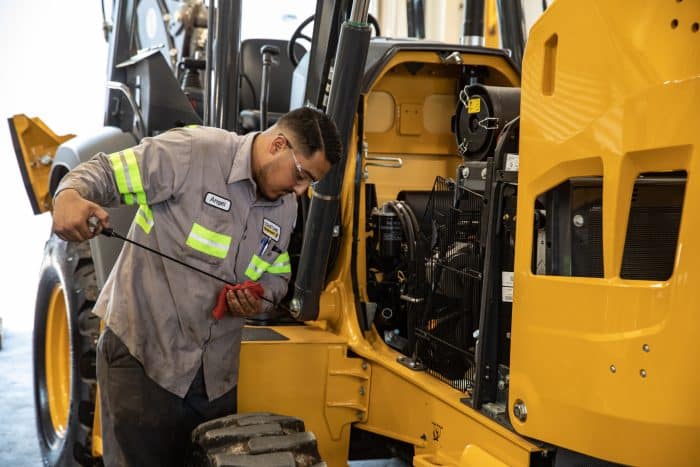
With new machine technology solutions entering the market every day, we are able to develop a deeper understanding of what to prioritize when it comes to machine maintenance and health. From common best practices, such as daily walkarounds and routine inspections, to innovations allowing our operators to work smarter, not harder, machine health and maintenance are at the core of a successful jobsite. Reduced operational costs, limited downtime and overall improved productivity are just some of the many advantages customers can experience by utilizing machine technology and prioritizing machine maintenance.
Performing Regular Inspections
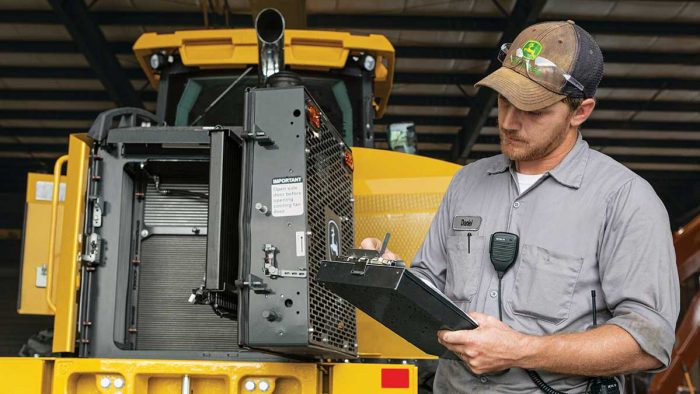
Performing regular inspections, such as daily walkarounds, are key to ensuring your machines meet their productivity potential helping to minimize downtime. When performing your walk around, visually inspect the machine’s appearance and look for damage and rub points, check fluid levels, look for leaks and take a close look at wear items that could prevent your machine from efficiently doing its job. Operators are the first line of defense in making sure their machine is in optimum operating condition to keep the jobsite productive.
Beyond performing daily walkarounds, operators should also prioritize routine full-machine inspections. While basic inspections such as daily walkarounds can be performed by operators themselves, it is important to note that full machine inspections are best performed by trained, certified individuals with expertise in the field. Machine inspections should be conducted with the intent of a purposeful maintenance strategy and should occur during the machine’s recommended service intervals to ensure the machine is operating in peak condition and to prolong machine life.
A machine inspection is a comprehensive process that begins with a well-defined checklist or task list, outlining the specific objectives and areas to be examined during the inspection. The process includes a meticulous visual assessment of the machine’s functionality and its components, ensuring everything operates smoothly. Safety checks, including failsafe functionalities, are conducted to guarantee the equipment meets necessary safety standards. Additionally, the inspection involves observing the machine in operation, and assessing any signs of wear or potential issues. Based on the findings, the inspection report includes recommendations for short-term, mid-term, and long-term maintenance steps to address identified needs. Immediate maintenance tasks are scheduled promptly to prevent any further complications.
Completing these routine inspections helps to spot potential problems early, which is beneficial on multiple fronts. Ultimately, it saves operators money by amending issues with individual parts and/or overall functionality, so that larger, more costly issues with performance and longevity are avoided.
Utilizing Your Dealership
Utilizing dealership technicians for construction machine service offers a multitude of invaluable benefits. Firstly, these technicians undergo rigorous factory training, ensuring they possess an in-depth understanding of the machinery they service. This specialized education equips them with the expertise to diagnose and address a wide array of potential issues efficiently and accurately. Moreover, dealership technicians have access to a much broader pool of machines, granting them exposure to various models and configurations. This extensive experience translates to a deeper knowledge base, enabling them to troubleshoot even the most complex problems effectively.
Additionally, dealership workshops are equipped with the precise tools and equipment necessary for the job, guaranteeing that maintenance and repairs are carried out with utmost precision and efficiency. This combination of factory training, diverse experience, and specialized tools ultimately leads to enhanced reliability, longevity, and performance of construction machinery, making dealership technicians an invaluable asset to any project.
Fluid Sampling
Fluid sampling is all about preventative maintenance, helping keep your equipment running at its best. The fluids that help your machine run smoothly can also provide some tell-tale signs about potential health issues. Fluid sampling offers a crucial return on investment by providing a cost-effective approach to preventing costly failures. By comparing the expense of fluid sampling to the potential costs associated with a major component failure, it becomes evident that this proactive measure is a vital investment. Through regular fluid sampling, insights into the machine’s health are gained.
Fluid samples taken are sent to specialized labs where they undergo meticulous analysis, revealing key information about the machine’s performance. When a critical component begins to deteriorate, heightened levels of specific materials in the sample act as an early warning system, notifying customers of impending issues. This invaluable foresight allows for timely intervention, preventing costly breakdowns and downtime. Moreover, the integration of fluid monitoring into overall machine management forms a symbiotic relationship.
Machine Monitoring
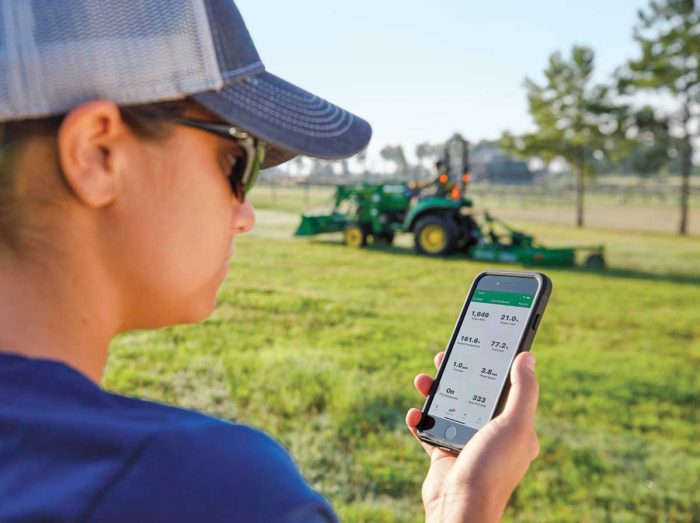
Machine monitoring is a pivotal component in modernizing construction operations, bolstering efficiency, and minimizing downtime. The utilization of advanced telematics systems empowers manufacturers and operators to seamlessly gather, analyze, and act upon crucial data from their machinery. This solution helps operators stay on top of machine monitoring which ultimately helps the machine run better and extend its lifespan. By aggregating real-time information on equipment performance, fuel consumption, maintenance schedules, and location, companies can proactively address issues before they escalate, ensuring that resources are allocated optimally and operational costs are kept in check.
One of the major benefits of machine telematics monitoring is machine health. This can be done in many ways including using asset allocation services. Machine telematics data, such as the data sourced through John Deere JDLink Connections, can provide valuable fleet insights and remotely monitor your machines, showcasing how often and for how long your machines are running. Access to this information can help operators determine if they are underusing or overusing certain machines, ensuring your machines are being used efficiently and machine life is being prioritized. Additionally, machine telematics can also grant you vital information on machine maintenance and repairs. This technology makes it easy to view a machine’s daily operation hours, helping contractors plan downtime for maintenance or repairs during off-hours to maximize uptime and productivity. Operators can also get immediate alerts for machine diagnostic trouble codes, preventing failures.
Machine monitoring systems also foster a culture of preventive maintenance and data-driven decision-making. This technology can also forecast potential malfunctions based on historical performance trends, enabling timely interventions to avert costly breakdowns. Additionally, remote diagnostics and programming solutions allow the operator’s dealer to access and reset diagnostic trouble codes and record performance readings without visiting the jobsite. Machine software can also be updated remotely. Remote diagnostics and programming can help increase uptime and decrease costs.
Mike Fulton is a service marketing manager with John Deere.