The Advantages of Drop Hammer Attachments for Efficient Demolition
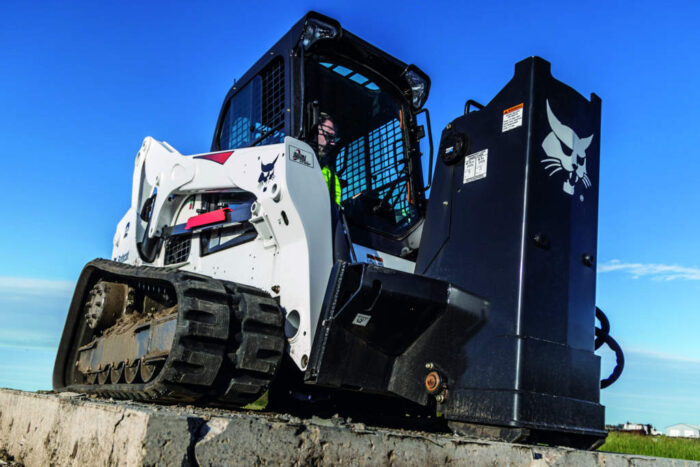
“The drop hammer is, in my opinion, very much underappreciated.” So says Travis Kidder, product manager, Bobcat attachments. It’s hard to argue the point. Drop hammers are simple to own and operate and are a cost-effective way to break up concrete slabs. Aside from greasing, they require minimal maintenance and if they sit in a corner of the shop for months between uses, they emerge ready to go to work.
“Almost no maintenance,” says Kidder, but here’s the little bit required. Greasing the hammer and oiling the drive chains should be done every eight hours. Zerks are provided for the drive motors and for the interface of the frame and hammer; the hammer distributes the grease as it operates. Lithium grease is recommended, but heat is not an issue so high-temperature grease is not necessary. Bobcat sells grease and chain oil for its drop hammers.
Bobcat has just one model, and it is simply called the Bobcat Drop Hammer Attachment. One model is sufficient as it fits most skid steers and other compact carriers. The drop hammer mounts right to the front of the machine with Bobcat’s convenient Bob-Tach mounting system. There is no reach, so most rated operating capacities are sufficient. Standard flow and pressure are also sufficient; Kidder says 13 or 22 gpm and pressures up to 3,500 psi are fine. There are no electrical connections and the drop hammer works with either hand-and-foot controls or joysticks.
Drop Hammer Operation
The drop hammer has dual hydraulic motors with chain drives. Catches lift the hammer to the top of the stroke and then release it to freefall to the surface. The hammer has a 38-in. stroke and weighs 1,165 lbs, delivering more than 3,600 lbs of impact force. That force is transmitted through the concrete for more complete breakage with much less surface chipping than with a hydraulic breaker, making debris removal with a bucket or grapple far easier. “At around $13,000, the cost is comparable to a mid-size hydraulic breaker, but you’re getting more impact per dollar,” says Kidder.
Cycle time is 20 strokes per minute, which allows three seconds for the operator to move the hammer to a new location between strokes. Kidder says the best pattern is to start at one corner of the slab and work backward in a straight line. At the end of the run, shut off the hydraulic flow. A bleed orifice allows the hammer to settle at the bottom of its stroke, much as the float feature allows loader arms to come to rest at the bottom of their stroke. With the hammer at the bottom, the operator uses the loader arms to lift the drop hammer and carry it to the start of a new row. Use continuous flow. You can do two or three cycles in one spot, if necessary. Cycling auxiliary flow on and off can slightly alter cycle times, but Kidder says Bobcat advises against that. If the operator requires slower cycle times, engine rpms can be reduced to meet the operator’s desired cadence.
Are you curious about how to size and buy a rotary tiller for your tractor? We have the answers!
Drop Hammer Attachment Safety Advice
The drop hammer must be on the same plane as the carrier. This means drop hammers are for use on slabs that are horizontal or nearly so. Never move the hammer when it’s in contact with the surface. Reposition the skid steer only after the hammer has lifted and make sure the skid steer is fully stopped before the next hammer drop. The objective is to avoid side loads on the tool. Kidder advises against using a drop hammer in confined spaces, near foundations or around other sensitive structures. The force of the drop hammer propagates out from the point of contact and will affect nearby materials. While a drop hammer is more efficient than a hydraulic breaker on larger slabs, a breaker is better for tight work. Optimal slab thickness for a drop hammer is 5 to 18 in.
The hammer emerges from the frame at the top of its stroke, so be mindful of overhead clearance. Use loader boom float to ensure there is no tension on the lift arms, either up or down. The drop hammer transmits far less shock load to the carrier than does a hydraulic breaker and keeping tension off the loader arms nearly eliminates any remaining shock transfer to the host machine. As with hydraulic breakers, avoid blank firing. Make sure the frame is in contact with the surface before raising and dropping the hammer.
Ensure the transport lock is engaged to hold the hammer at the bottom of the frame during transport. The drop hammer is designed to stay upright during storage and transport. Kidder summarizes the value of a drop hammer by saying it is an excellent supplement to owning a breaker and due to its high productivity and simple operation can be the preferred go-to tool for contractors wanting one attachment for doing slab demolition. And compared to hydraulic breakers, drop hammers have far fewer moving parts and no nitrogen accumulator to maintain.
Richard Ries is a freelance writer for Compact Equipment.