Mini Extras: Build the Ultimate Mini Excavator with the Right Attachments
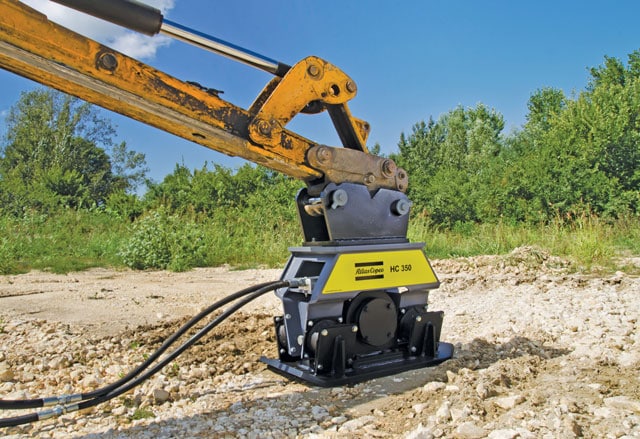
Whether it is water lines, gas lines, electric cables or sewage, a reliable compactor will be needed for restoration. Atlas Copco’s mini excavator compactor works perfectly.
On today’s utility jobsites, if you aren’t able to accomplish several different tasks with just one machine, you are missing out on big-time boosts to productivity. Consider all that can be accomplished with just a mini ex and the right arsenal of attachments.
Attachments of Removal
If you are doing road plate or concrete removal, a vacuum attachment can be the perfect implement. Vacuworx was the first manufacturer to introduce vacuum lifting systems for compact equipment and is currently working on “next generation” improvements. Its SL and CM Series Vacuum Lifting Systems are lightweight and versatile, allowing them to be easily attached to multiple host machines including skid steers, backhoes and excavators. They significantly reduce the amount of time it takes to get the job done by cutting down load cycle times and the number of workers needed to perform tasks.
“They are hydraulically driven, so they offer the perfect solution to common jobsite restrictions such as loud noise, emissions, debris and vibration,” says Lance Osterhout, area sales manager for Vacuworx. “In addition, when used for concrete demolition projects, material can be removed with minimal damage to the sub base and surrounding area.”
The CM 3 in particular can be used with single or the Vacuworx double pad assemblies, depending on the material being lifted. Both systems are designed with quick-connect hydraulic hoses and a factory pre-set flow control valve to ensure optimal performance on any host machine and can be shared easily among multiple host machines.
Attachments of Compaction
Whether it is water lines, gas lines, electric cables or sewage, a reliable compactor will be needed. In this realm, Atlas Copco recommends a hydraulically operated attachment with an overflow and pressure control valve to help ensure the proper operating parameters are met because all compactors will require a specific flow and pressure requirement to operate at maximum performance.
“These are typically installed on a carrier that operates multiple hydraulic attachments that may require different oil flow and pressure settings from the carrier’s auxiliary circuit,” says Rich Elliott, product manager for hydraulic attachments at Atlas Copco.
Use the safe and reliable power of this vacuum attachment on your excavator.
Also consider the multiple ways this attachment will be used in compaction and extraction. Many compactors need to be modified prior to use for extraction or the isolators will be destroyed. Here, Atlas Copco’s line comes with an install axle bolt that is helpful for extraction use. In addition, higher efficiency motors require less flow with no loss of performance and reduce fuel and maintenance costs, along with PermanentLube for the eccentric bearings, which are virtually maintenance free and require no greasing.
“Make sure to get the appropriate model that suits the carrier size, not too small or too large,” Elliott says. “Also, look at the plate width to match up with a typical trench size that is most common for the application it is being purchased for.”
Attachments of Drilling
The right concrete dowel pin drills will maximize productivity and safety on road patchwork jobs. And when it comes to dowel pin drilling, Minnich should be your first stop.
“A lot of dowel pin drilling time is spent not on drilling but on alignment,” says Rob Minnich, vice president of marketing at Minnich Mfg.
The side-shift functionality of Minnich excavator-mounted drills allows the operator to drill twice as many holes without moving the carrier and realigning.
The side-shift functionality of Minnich machine-mounted drills allows the operator to drill twice as many holes without moving the carrier and realigning. Another benefit of side-shift capability is it allows for the use of a smaller compressor.
“For example, instead of using a six-gang drill and supplying air to all six drills [600 scfm], a contractor could use a three-gang drill and only need 300 scfm by simply side-shifting to achieve six holes,” Minnich says.
These pneumatically powered units can be mounted to an excavator, backhoe or skid steer loader to form a self-contained, mobile drilling solution for full-depth repair. On the safety side, with enforcement of OSHA’s final respirable crystalline silica standard in the construction industry scheduled to begin Sept. 23, 2017, dust collection is the big topic in dowel pin drilling right now. You’ll want to ask Minnich about its dust collection system — a canister-style unit can be retrofitted to any Minnich machine-mounted, on-grade, on-slab or utility drill model. It can also be adapted to fit other drill makes and models.
“Air consumption and mobility are extremely important in full-depth repair,” Minnich says. “Transporting a huge compressor can be cumbersome. A smaller, more mobile machine-mounted drill needs a smaller compressor and can be attached directly to an excavator, eliminating hitching or trailering.”
Attachments of Coupling
Quality-couplers are key to ensure maximum machine life, as lower grade quick-coupler attachments have a tendency to leak. John Deere’s new hydraulic coupler features a wedge bar locking system that compensates for wear and keeps the coupler joint tight. Operators are no longer required to exit the cab to switch buckets, so site clearing can continue with high productivity and minimal interruptions. The hydraulic coupler is designed for 35G, 50G and 60G excavators and is compatible with the ever-expanding lineup of John Deere Worksite Pro attachments.
Some handy features: Sudden hose-assembly failure is all but eliminated thanks to optimized hose routing and flow rates. This means maximum uptime and durability. Building upon that, the John Deere hydraulic coupler allows operators to switch attachments from their seats, so site clearing can continue with high productivity and minimal interruptions.
“We have over 100 Worksite Pro attachments in our lineup for use on compact equipment,” says Jessica Hill, program manager, global attachments, John Deere. “The majority are compatible with our universal self-cleaning Quik-Tatch system, which allows operators to switch between attachments quickly and easily.”
“We also have a variety of compact excavator buckets with clamping capabilities, which allows for more fill in the bucket when lifting bulky material and heavy loads,” Hill says. “The clamp also aids the operator removing debris at the jobsite by grabbing large and small objects.”
Chris Crowell is a contributing editor of Compact Equipment.
Air Excavator : Check Out the Vermeer VX30 Gen3 Vacuum Excavator at ICUEE
Available in 300, 500 and 800 spoil tank sizes.
The Vermeer VX30 Gen3 vacuum excavator built by McLaughlin brings productivity-boosting features including automotive-style belt tensioners, quick-grip tool storage, quick-drain technology and more. The portable nature of this vacuum excavator makes it the ideal choice for utility contractors’ potholing and fluid management needs. The VX30 Gen3 vacuum excavator is available with a no-hassle hose and strong arm option — an industry exclusive that allows crews to move quickly between jobsites by eliminating the need to disconnect the suction hose. A high-lift version of the patented cam-over hydraulic rear door opens 40 percent higher than previous generations. Powered by a Tier 4 Final compliant 24.8-hp Kubota diesel engine with a common-rail fuel injection system, this four-cylinder, high torque engine requires no regeneration or DEF fluid, allowing for constant productivity without shutdown. For more info, visit mclaughlinunderground.com or ICUEE booth K120.