How Machine Control Systems for Compact Track Loaders Can Elevate Earthworks
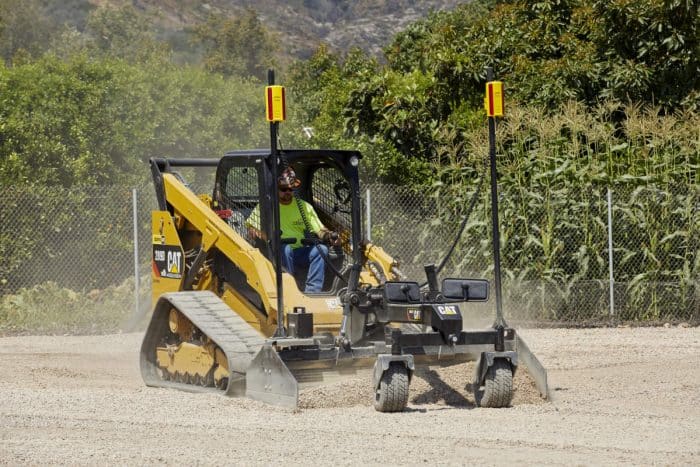
Machine control for grading is among the categories of technology proliferating in the compact equipment world. The good news? Customers are more likely to find the exact right system when there are so many options. The bad news? Choosing the right system is challenging because of the many options available. What to do? Your choice should be driven by many factors, but not by the grade control system itself. Referring to the rudimentary world of hand tools, for example, your goal is not to buy a hammer. Your goal is to complete a job. The hammer that works for framing is not the right hammer for breaking up concrete.
The Customer’s Role in System Selection
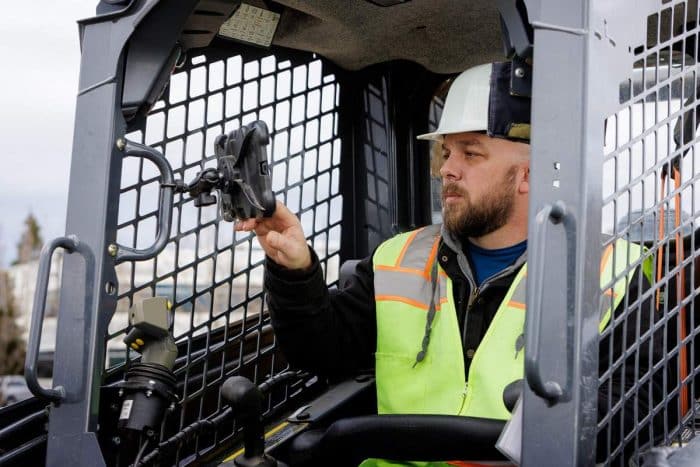
Start by defining your applications. Are you doing single-slope or compound-slope work? Driveways and parking lots are common examples of each. Maybe no slope, such as with slab-on-grade foundations. Maybe heavily contoured surfaces, such as golf courses. What physical size projects are you doing? Driveways? Parking lots? Sports complexes? Maybe you’re not doing contained projects like these but linear projects such as roadways. What accuracy do you need in both horizontal and vertical planes? Accuracies down to 1 mm (0.0397 in.) are available, but there’s a correlation between accuracy and cost, which brings up another point: What’s your budget?
Your budget should include many things, not least of which is your payback period. Machine control improves accuracy, reduces rework and cuts material costs, labor hours and equipment hours. It opens the doors to some jobs for which you had not been qualified; municipal contracts, for example, may require the use of machine control as a quality assurance measure. Because the greater efficiency of machine control reduces everything from material waste to carbon emissions, some customers will offer you jobs because you support their green initiatives. In fact, the “greenness” of machine control can be an effective marketing tool. The payback period can range from one job to one year, due mainly to the diversity of machine control options and the resulting ability to scale the machine control solution to the customer’s jobs.
Compact track loaders are the most popular category of compact equipment in America. Learn why with loads of track loader features right here.
Know how many machines you want with machine control. Some components can be shared among several machines simultaneously. Some components can be moved from one machine to another as the job progresses. Some systems are installed permanently on one machine. Some systems require the CTL to have electrohydraulic controls while others can be adapted to machines with pilot controls. The level of control ranges from indicate systems where the operator moves the controls according to a cut-and-fill display on a monitor to 2D (for flat work and single slopes) to 3D (for compound slopes and contours) where the operator handles direction and speed and the machine control system handles the ground-engaging tool (grading blade or box blade).
Depending on the OEM, machine control can be a factory-installed option when spec’ing a new machine. Often, it’s a dealer-installed system, whether on a new machine or one already in the customer’s fleet. Is it conceivable that machine control could be installed by the customer? Possibly. Is it advisable? It depends on the system. As machine control has migrated down from higher-cost machines to compact equipment, the cost has come down and the technology is more accessible. But to be fluent in machine control you’d still need a thorough understanding of all the components and concepts from lasers to RTK GPS (real-time kinematic) to RTS (robotic total stations) to GNSS (see sidebar below) to CORS (continuously operating reference stations) to IMUs (inertial measurement units). Fortunately, machine control system OEMs and dealers are fluent in these areas, and although many options exist, they’ve provided starting points for track loader owners that may well serve the vast majority of customers with minimal or no modification.
It Isn’t just GPS
GPS, or Global Positioning System, is the U.S. system of global positioning and navigation satellites. Virtually all GNSS-based machine control systems in the United States use GPS but many also use the Russian GLONASS satellite network. “GNSS” (Global Navigation Satellite System) identifies systems that use more than one network; “GPS” is used in those rare instances where a system uses only GPS.
Topcon
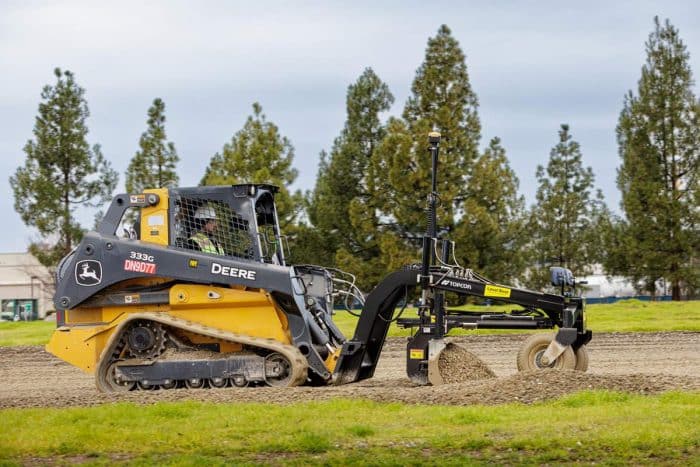
Topcon Positioning Systems has the Compact Solutions product line, which consists of two systems — the laser-based 2D-MC and the MC-Mobile 3D technology. 2D-MC is designed for use with track loaders and skid steers. MC-Mobile adds track loaders and compact excavators to this list and the flexibility to be used with a rod for layout and in-field design tasks. The excavator version can be 3D positioning laser or GNSS. The 2D-MC is attachment-centric and fits on the grading blade or box blade and has a ruggedized Android Bluetooth 7 3/4-in. monitor mounted in the operator’s preferred cab location using RAM mounts. It uses bolt-on poles with laser receivers. It is self-contained and can be moved from one machine to another. MC-Mobile is machine-centric and is a dedicated installation for practical purposes.
Either can be 2D machine control or indicate. Both connect to the machine’s CAN bus network. Because of this, the systems are available only for machines using EH controls, although Topcon is working on solutions for machines with pilot controls. The dealer will work with the customer to ensure the host machine, grading attachment and Topcon system integrate well. Communication is via a J1939 connection so there is no hydraulic valve added to the machine. Customers can go directly with either product initially. If they start with 2D-MC and later want to upgrade to MC-Mobile, some components can be migrated to the new system to reduce cost of conversion.
Trimble
Trimble Earthworks Go! 2.0 is an entry-level, 2D system designed specifically for compact equipment. It uses lasers and magnet-mount laser receivers and a smartphone app for file management and operation. It is designed for the local contractor doing smaller, simpler jobs such as driveways and sports fields. It can be installed in 20 minutes or less by the user and requires the use of a grading attachment on the machine. The Trimble Siteworks Machine Guidance Module can be used on a pole for survey then moved to the excavator offering a two-for-one package of site survey and data acquisition plus machine guidance.
The base station remains the base solution. It is easy to use and accurate and provides RTK (real-time kinematic) guidance. They are declining in popularity as more state and local governments provide VRS (virtual reference station) services. Total stations are a premium product for larger contractors: heavy and highway, airports, etc. They are the most accurate. The Trimble MT900 prism serves as a machine-mounted target for the system. No lasers or sky access is required.
GNSS system accuracy is a matter of best practices and the tiers of accuracy options built into the correction sources. Another option is the Trimble VRS/IBSS (virtual reality station/internet base station service), which is more affordable but provides lower accuracy.
Systems have better portability now, which is especially beneficial when moving the system from machine to machine is a necessary part of receiving value (unlike in production settings where an excavator or other machine uses the system throughout the workday). The system is hot swappable, configured so that as it’s moved between machines setup time is minimized. These systems are easiest to integrate with EH joystick machines. For those using pilot controls, Trimble has their VM510 valve module that enables use of their systems with pilot control machines. Trimble Sitech dealers are the best source of information and provide excellent insight into best practices in the local market. There are Sitech dealers in all 50 states as well as international locations.
Our thanks to Mark Jones, senior manager of the compact solutions group, and Oscar Cantu, construction content manager, North America, Topcon Positioning Systems, and Jack Young, machine control product manager, Trimble, for their input on this article.
Why Track Loaders?
Grading technology that works on a compact track loader can just as easily be applied to a skid steer, so why isn’t it? Compact track loaders are better than skid steers at grading because they have more tractive effort and greater stability, both essential to effective grading. And yes, a skilled skid steer operator can use the machine to spread material with reasonable accuracy, but that’s not the same as precision grading. For that, you need a track loader; better yet, a track loader with machine control.
Economic Drivers
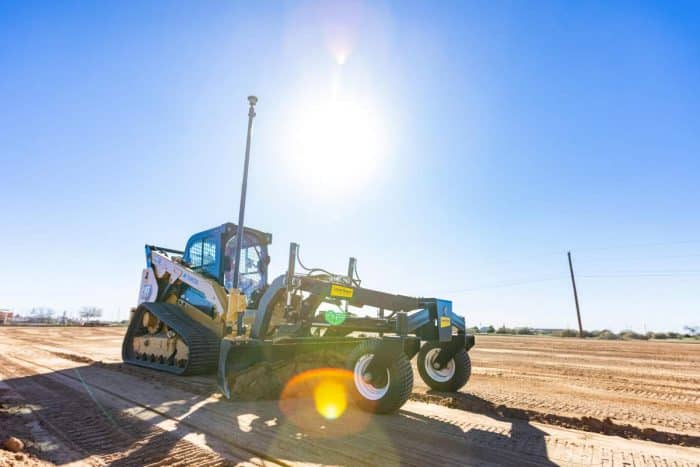
The same economic forces making advanced technology affordable on compact track loaders will bring tech to a wide range of compact machines. Economy of scale and economy of scope are the two main ones. Economy of scale is spreading fixed costs over more units. Economy of scope is spreading fixed costs over a wider range of products. Moore’s Law has long been cited as another economic force. The gist is that computing power doubles every one to two years. (Gordon Moore said one year in 1965 and two years in 1975.) Recent changes have thrown Moore’s Law into question, but the underlying truth remains unchanged: computer technology advances rapidly, relentlessly and reshapes the value proposition of every market it touches … including compact equipment.
Richard Ries is a freelance writer for Compact Equipment.