Evolving Hydraulics
If you’re a compact equipment OEM, you probably already know about the impact of Tier 4 emissions compliance on diesel power plants, but if you’re a contractor you probably don’t. Government-enforced Tier 4 emissions regulations are pushing off-road diesel engine manufacturers to revamp their engine lineups with more eco-friendly power plants. Unfortunately, these new diesel engines are generally bigger, thirstier and come with a suite of after treatment accessories that have to be installed somewhere in the engine envelope — and it’s only going to get worse.
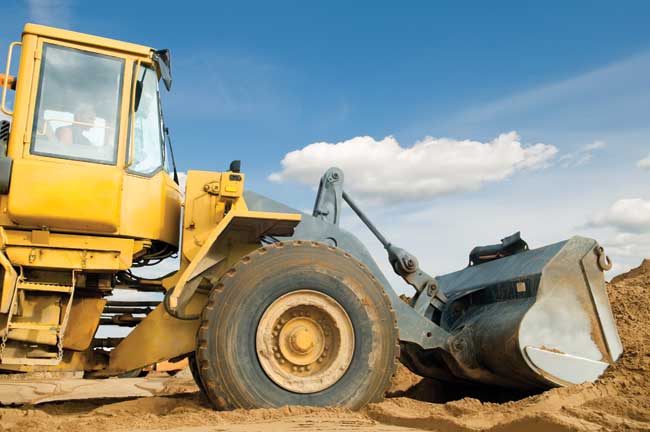
Unless you want to re-design your vehicle, and make it less “compact” in the process, the extra space required for an emissions-compliant diesel power plant is going to have to be found by making something else physically smaller. And, since hydraulics are typically the largest single consumer of energy on a compact machine, the hydraulic system is a natural place to start. The good news is that today’s best hydraulic systems have the capability to produce the same amount of work in a smaller physical envelope than was possible just a few years ago. In other words, part, or maybe all, of the space you lose to emission compliance can be made up by selecting more efficient hydraulic system components to achieve greater power-density.
Those more power-dense hydraulic system components achieve their efficiency largely by operating at higher pressures. Higher operating pressures are more efficient because most hydraulic system losses are directly related to flow volume. Higher pressures require less fluid and, therefore less flow, to do the same amount of work and that makes the whole system more efficient.
Higher pressures have an added benefit because they let physically smaller system components deliver the same performance as larger components operating at lower pressures. So, in theory you could simply dial up the operating pressure of an existing hydraulic system and increase its performance — provided, of course, that the existing components can handle the pressure. There is still no free lunch, however, and they almost certainly can’t. In reality, you probably will have to change most or all of the system components to get the benefits of modern high-pressure operation. Fortunately, it may not be all that difficult because hydraulic suppliers have introduced a lot of upgraded products in the last few years to address this issue.
Eaton’s recently introduced 420 Series open circuit piston-type pumps are a good example of this trend. The 420 pump with hydro-mechanical torque control automatically senses heavy loads and adjusts hydraulic fluid flow accordingly. It is intended for moderate-flow, high-pressure mobile applications such as compact wheel loaders, telehandlers, rough terrain forklifts, telescopic booms, sweepers, backhoe loaders and garbage trucks. To accommodate the new torque control, the pump housing was designed to decrease airborne noise to 76 dBA at 1,800 rpm and 207 bar. A case-to-inlet check valve was added to improve cold weather operation and provide added protection to the seals and rotating group. The new torque control works in parallel with the standard compensator, using a special mechanism to replace the control piston.
In compact and mid-size equipment, torque almost always needs to be controlled; limiting the torque at the pump shaft across a wide range of engine speeds provides operators with the benefits of increased productivity, greater efficiency and fewer engine stalls. The result is lower engine emissions and improved fuel economy.
Productivity, or more specifically cycle times, are enhanced by increasing the speed with which the vehicle function is performed due to flow rate changes made by the torque control system. For example, raising a heavy load with a set of forks on a telehandler places a significant amount of pressure on the hydraulic pump and system. To prevent engine stalls without limiting the telehandler’s lifting capacity, manufacturers not using torque control would be forced to use a smaller displacement pump that significantly slows the operation of the forks. Torque control automatically senses heavy loads and adjusts flow accordingly.
Limiting the flow in high pressure situations limits the torque the pump can apply to the engine and, as a result, avoids the corner horsepower point and prevents the engine from stalling. It also allows for higher flow and quicker operation when the set of forks is empty, which means higher productivity.
It is true that higher operating pressures and smaller, more power-dense hydraulic components can go a long way toward offsetting the space, weight and fuel-efficiency costs of Tier 4 compliance in the compact equipment marketplace. But the real solution to this ongoing challenge isn’t finding ever more innovative ways to perform the same functions with physically smaller components and systems. What’s really needed is a re-thinking of how machines use energy to accomplish their functions in the first place. In a hydraulic excavator, for example, all of the energy used to raise the boom using today’s technology is lost when the boom is lowered. And it is not just lost; it is converted primarily to heat and turbulence in the reservoir that requires additional energy to control.
Why not engineer the system to re-capture most of that energy by changing it into pressure in an accumulator instead? It’s a relatively simple and well-understood process that’s being used elsewhere to cut the fuel consumption of refuse trucks, shuttle busses and utility vehicles. Why not do the same thing with compact equipment? Any time energy is expended to lift or move a load, that energy is available for re-capture when the load is set down or stopped. It’s there for the taking, and it doesn’t have to be re-created by burning more fuel the next time it’s needed.
Hydraulic systems are the ideal tool to use for the transition from energy consumption to energy management. By maximizing the efficiency of energy transformation and marrying with the “intelligence” of electronics, the opportunities for an electro-hydraulic hybrid are significant.
Going back to that excavator, if the operator measures system performance based on the sound of the engine bogging under load it’s almost certain the machine is not operating at maximum efficiency. The truth is that a bogging engine is much more often an indicator of system overload than of maximum productivity. Remember that the engine is supplying power for the whole vehicle — propulsion, boom, bucket, radiator fans, power assists, everything — and the operator cannot possibly monitor all of that. But, with electro-hydraulic power management, an onboard computer interfaced with an electro-hydraulic system can intelligently direct the power to where it is most needed in real time.
The increased efficiencies in that scenario are not incremental, they are exponential. Enough so that the size, weight and fuel consumption penalties of Tier 4, and Tiers 5,6,7 and so on that we all know are coming, may turn out to be minor inconveniences rather than major headaches. It’s just possible that the real impact of Tier 4 compliance may be a new benchmark for the efficiency and productivity of compact diesel-powered equipment. Higher operating pressures are a reality today. So are energy capture and re-cycling and whole-vehicle electro-hydraulic monitoring and control. It’s only a matter of time until someone puts the whole package together and changes the rules of the compact equipment game.
Tony Welter is the construction and mining segment director for Eaton Corp., based in Eden Prairie, Minn.