Let’s Explain Variable Tilt Technology and How It Boosts Productivity on Scissor Lifts
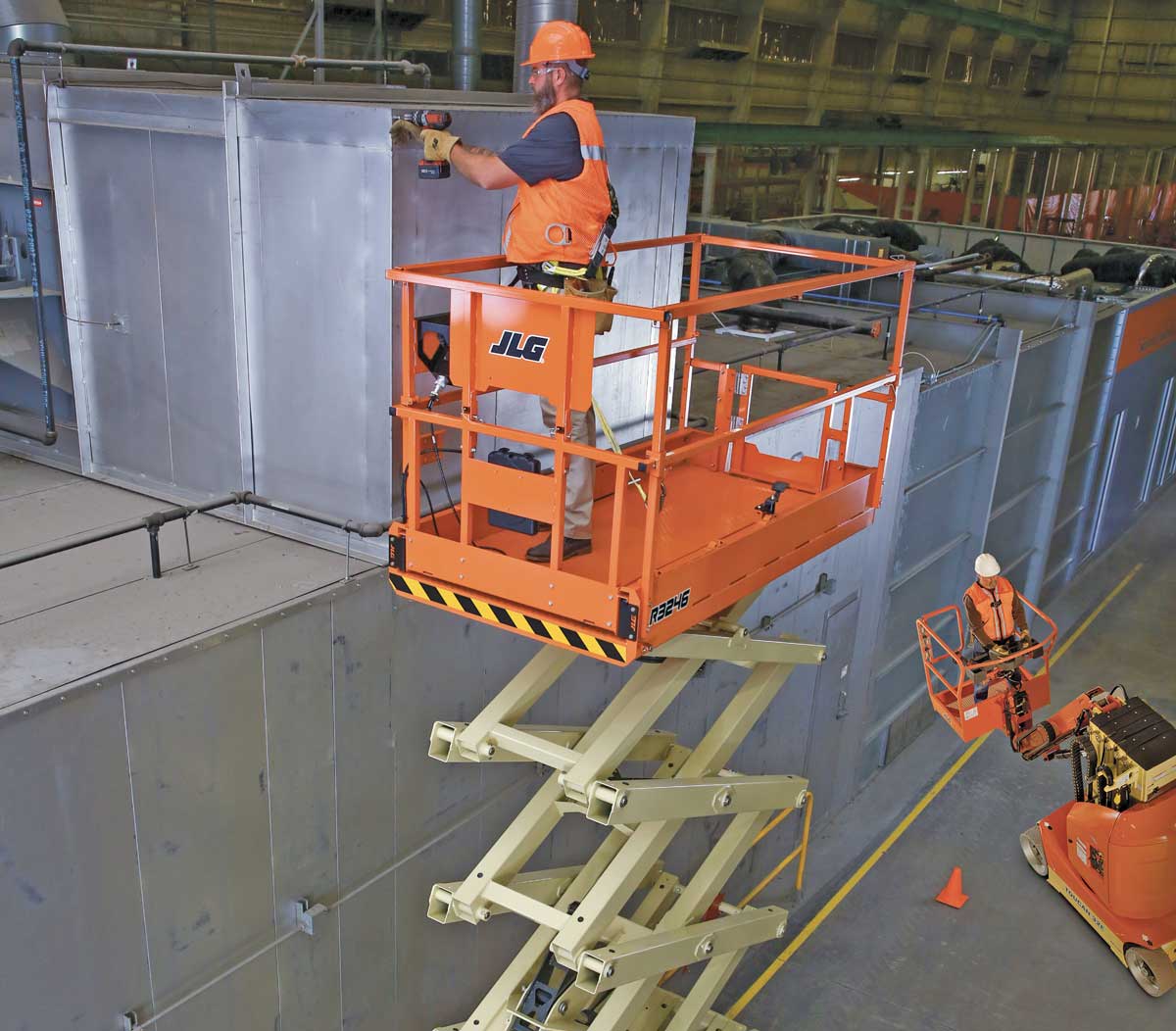
In the past, scissor lifts were primarily designed to fit general specifications. Today, that’s all changing. This new generation of machines looks and operates very differently — their designs giving more attention to the demands of real-world jobsites and the needs of the users operating these machines.
For instance, many applications and working environments can be rather challenging for scissor lifts because these machines are only rated to work on firm, level surfaces, and most jobsites aren’t flat. To solve this common jobsite challenge, scissor lift OEMs like JLG have had to consider what solutions they can offer that address working in varying terrain and make sure that the machine is engineered to handle the capabilities of advancing technologies.
For example, it is important that the machine is able to drive (move) while elevated, that the tires stay in contact with the ground and that the machine’s drive system is capable of offering smooth operation in all conditions. Also, the machine’s control system needs to be able to actively monitor and control the machine’s dynamics during operation, such as platform movement. In addition, the machine must be able to communicate back to the operator what it’s doing, as well as what the limits of the machine’s operations are under the present conditions via the control display panel.
With these considerations in mind, technology like variable tilt for slab scissor lifts was developed to adjust a machine’s capability under certain conditions to the ground or surface being worked on. Let’s take a look at how it works.
What Is Variable Tilt?
Most slab scissor lifts cannot elevate when working on a side slope greater than 1.5 degrees, but variable tilt technology, which is designed to maximize a scissor lift’s height based on the slope on which the machine is positioned, can now elevate on side slopes up to 3 degrees. This gives the operator a greater degree of flexibility, and most importantly keeps machines operating within the approved work envelope.
The first evolution of this technology focused on modifying the machine’s lift height or work envelope based on the tilt of the chassis, assuming the machine is fully loaded. A new, modern version takes this technology a step further — it considers the tilt and actual load of the platform, measured by the load sensing system, to define how high the operator can lift the platform. Equipped with sensors that monitor both the platform’s weight and the machine’s tilt, today’s variable-tilt technology determines the allowable work envelope. The machine then notifies operators on the platform-mounted LCD, before raising the machine, about how high they can elevate.
The display can clearly communicate the machine’s side-to-side tilt, front-to-back tilt, how much weight is on the platform, the current height of the platform, as well as the maximum height the operators can raise the MEWP by taking those factors into account. This means that operators can see if they should take a little bit less material with them or if they need to get to a spot that’s a little bit more level on the jobsite so that they can get the full height. This technology removes the guesswork that often results in operators having to descend and try again.
Because variable tilt technology is still relatively new to the market, fleet owners and operators may not fully understand how it works. Here are two common scenarios where this capability helps scissor lift operators work more efficiently at height.
Scenario #1 – Food Processing Plant
A maintenance technician at a meat packing plant needs to diagnose what’s wrong with an overhead conveyor that carries large cuts of meat from the slaughterhouse to the packing area. The first step is to diagnose where the failure occurred. To help the tech reach the conveyor, which varies in height from 10 to 15 ft above the plant floor, a JLG ES1932 scissor lift is available to assist with the inspection process.
The concrete floor in this area was laid with a 2-degree slope to enable easy wash-down and drainage. As the tech prepares to elevate the scissor lift, the slope gauge on the instrument panel has two of the three lights illuminated, which means that the maximum platform height will be limited.
The operator consults the machine’s operation and safety manual and learns that the maximum deck height will be 14 ft — just enough to comfortably reach and inspect the broken conveyor. The tech connects the fall restraint harness to the machine’s anchor point, elevates the work platform and gets to work, knowing that the variable tilt system will keep the machine operating within its approved work envelope, getting more done with fewer operational interruptions.
Because the floor has a consistent slope, the tech can drive the scissor lift along the conveyor, checking idlers and drive motors as he goes. After several stops, the tech finds the problem.
United Rentals Adds All-Electric Polaris Ranger XP Kinetic UTVs to Fleet
Construction and industrial jobsites are often loud, dirty and diesel- and gas-powered, but United Rentals is paving a new path with the addition of all-electric Polaris Ranger XP Kinetic utility vehicles. United Rentals is expanding its partnership with Polaris Commercial, a division of Polaris, to include more all-electric utility vehicles that will help make jobsites cleaner, more environmentally friendly and quieter, helping customers meet sustainability initiatives and reduce maintenance requirements. With class-leading horsepower and torque, Ranger XP Kinetic offers more power than ever to pull more, haul more and to get more done.
Scenario #2 – Data Center
A contractor is installing network cabling at a new data center, which utilizes a network of raised trays to carry data cables above the floor of the massive facility. The contractor’s job is to lay the cables and connect them so that data can flow smoothly through servers, routers and other high-tech equipment.
Utilizing a JLG ES2632 scissor lift, the contractor maneuvers it next to one of the reinforced concrete walls of the data center and positions it just below and in front of an empty aluminum cable tray. Knowing that the floor in this part of the building was built with approximately 1 degree of slope, the contractor glances at the machine’s LCD slope indicator. It shows that the platform can be fully extended to its maximum height of just over 25 ft.
Carefully positioning the machine and connecting the fall restraint harness to an anchor point, the contractor elevates the scissor lift until it’s alongside the cable tray. Knowing that variable tilt technology allows the machine to work on side-to-side slopes of up to 3 degrees allows the contractor to grab a toolbox and a spool of CAT5 cable from the floor of the work platform and get to work.
Improving Productivity
Another benefit of variable tilt technology is that it provides an uncomplicated user experience. Many people think that more controls and more limits a machine has would mean more machine issues, such as lift restrictions. However, the opposite is true. Productivity can greatly increase with the gain of a larger working envelope with fewer machine restrictions.
For example, by increasing the work envelope on JLG scissor lifts, there are decreasing machine alarms, which means better machine utilization time — and getting the job done faster.
Also, when operators know how much material they can take up with them, more or less than what they already have loaded before raising the machine, it removes the guesswork that often results in operators having to descend and try again.
Scissor lift manufacturers like JLG continue to focus on the areas of operator productivity, safety and cost of ownership, offering a broad range of models that cater to the specific needs of its customers through innovative solutions. Variable tilt technology is just one example of innovation that enhances productivity in the real world by allowing users to expand their work envelope.
ARA’s Quarterly Forecast Reveals Economic Optimism Reflected in Rental Operator Attitudes
The American Rental Association (ARA) recently updated its forecast for the United States equipment rental industry, noting growth will soften but still grow. Last quarter, year-over-year growth was expected to be 4.7 percent in 2023 and 2.1 percent in 2024. The most current projections indicate 7.6 percent growth in 2023 totaling $60.4 billion in construction and general tool rental revenue. As for 2024, a 3.1 percent revenue increase is now expected.
“While the growth has softened, we’re looking at a more optimistic outlook than we were a quarter ago. The recession fears we had have subsided,” said Scott Hazelton, managing director at S&P Global.
“After talking with many manufacturers and operators at CONEXPO-CON/AGG and in the weeks after, it’s clear the headwinds are still there,” said Tom Doyle, ARA vice president of program development. “Inflation is still high, interest rates are still high and they may continue to rise, while issues remain with labor shortages and supply.”
However, investment in the construction industry and construction employment approaches a record high. Also evident is rental companies’ adaptiveness.
“I continue to marvel at the adaptability of our members. They have found ways to overcome these headwinds and provide solutions for their customers,” Doyle said. For more info, visit ararental.org.