The Ex Factor
Productivity is the name of the game in the construction industry, and machine downtime costs money. Effective maintenance is very important, especially in today’s economy, when owners are under pressure and looking for ways to increase efficiency and productivity. Compact excavators typically don’t accumulate as many hours as their full-size siblings, but maintenance is still key to a long machine life. Unlike larger excavators, the smaller machines are more likely to be serviced by owners. And, if owners do a thorough job of maintaining their equipment, that means fewer technician calls, which saves money and downtime.
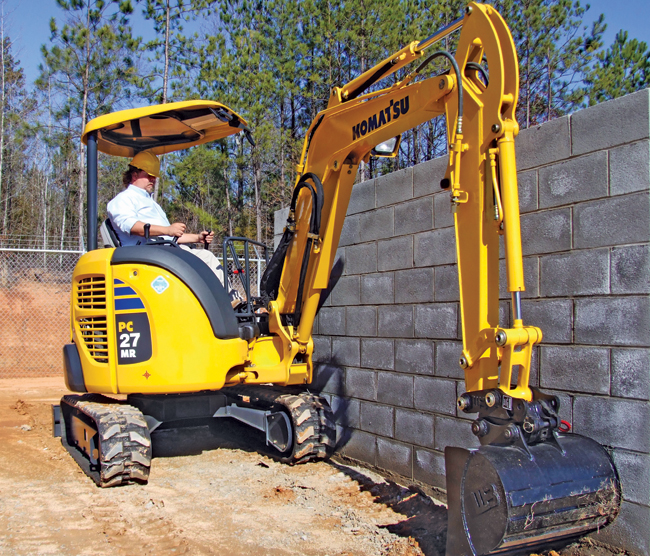
Access, Access, Access
When selecting a compact excavator for purchase or lease, carefully evaluate the ease of completing routine maintenance checks. Because proper and regular maintenance are key to effectively managing your compact excavators, the easier it is to perform those checks, the more likely operators will perform them on a routine basis. Check points that are difficult to access will run the risk of not being inspected.
Compact excavators are typically easier to service than the larger machines, with easy ground level access. Look for machines that have service points grouped in common areas to make good use of an operator or technician’s time. Fluid drain ports can help speed up the maintenance process. Even tight tail swing excavators, which have less room, should be designed with simple access to the service points.
When your compact excavator is hard at work on a large project, routine maintenance can often be missed or overlooked. Don’t let that happen. Maintenance checks (which will be clearly spelled out in the owner’s manual) are imperative to extend the life of your machine. Follow the OEM recommended procedures and use the recommended materials and fluids to keeping your machine properly maintained.
Make Routine Maintenance Part of Your Daily Routine
Starting the day off on the right foot will influence what happens for the rest of the day. All compact excavator operators should begin their workday with a routine daily machine walk-around. An experienced operator’s eyes and ears can be as important as any onboard diagnostics. Simple daily checks will keep you on top of the machine’s condition and can help identify issues before they get bigger. Daily inspections can also help you plan a repair if necessary and reduce downtime.
Each and every walk-around should start with a check to make sure there’s no obvious physical damage. Check under the machine to ensure nothing’s leaking. Engine and hydraulic oil levels should be checked daily. The few minutes it takes to complete these simple checks could save thousands of dollars in repair and replacement costs in the future. Preventative maintenance is the name of the game and simple daily checks keep you appraised of the machine’s condition and can help identify issues before they get bigger.
And just like with larger excavators, neglected maintenance can impact any of the main components of a compact excavator. Be sure that those key components are getting the maintenance they need and they are being looked at regularly. Below is a list of daily checks you should perform on a compact excavator:
- Engine oil level
- Hydraulic oil level
- Air filter dust indicator (engine air cleaner)
- Coolant reservoir level
- Fuel filter (water separator)
- Window washer fluid
- Horn
- AC filters (fresh air & recirculation)
- Working lamp switch
- Electric wiring
- Track shoe bolts, track tension and shoe condition
- Work equipment greasing
- Swing machinery oil
However, it’s very important to remember that the best guide for maintenance is the operator’s manual. Read and follow it carefully for a complete list of maintenance items.
Repair vs. Replace
When deciding where to draw the line between repair and replacement, it really depends on whether a proper repair procedure is available for a particular component. Keep in mind that a proper repair completed the right way the first time can prevent downtime. If a proper repair procedure is available, then it should be evaluated for the cost-to-benefit ratio. However, if a proper repair procedure is not available, the component should be replaced.
The best way to avoid a maintenance emergency or break down is regular maintenance. Once the damage is done, there is no way to add more oil to remedy the situation. The daily walk around inspections give operators the chance to identify issues early, which can be instrumental in minimizing downtime and repair costs.
Whether or not to perform a major overhaul usually comes down to evaluating the alternatives as a business decision. If the machine was properly maintained throughout its life, then there is a good case for rebuilding. Rebuilding the engine and/or transmission on a well-maintained machine makes good business sense if the rest of the machine is in good condition. However, if maintenance was not regularly performed, a component rebuild is not as attractive because other repairs would likely be needed to keep the machine in running condition. Before making a decision about rebuilding, owners should take the condition of the entire machine under consideration.
Fleet Management Tools: An Owner’s Best Friend
One of the easiest ways to maintain your compact excavator is to buy or lease a machine that comes standard with a remote fleet monitoring system. These management systems continue to become more technologically sophisticated and can provide invaluable information about machine health and productivity to ease your maintenance worries. Being able to track the machine’s hours and find its location can be a great benefit to keeping the machine properly maintained because it facilitates proper maintenance scheduling and can help identify potential problems before failure occurs.
A good fleet monitoring system notifies an operator when maintenance is due and will relay basic and critical performance data from the machine to the owner and local distributor. Relaying this information to the distributor, allows the distributor to align manpower, processes and inventories to best support customers’ parts, maintenance and service needs. This accurate and timely information means distributors can improve their response time, which in turn, lowers owners’ costs and downtime by being “at the ready” for service.
For example, if a machine’s “cautions” are transmitted to the owner and an authorized distributor technician, the latter can troubleshoot the machine even before arriving at the jobsite. The upside is that distributors can provide a higher level of support by reducing travel expenses and ensuring a prepared mechanic arrives at the site — ultimately reducing the owner’s expense and unscheduled downtime.
Knowing How Hard Your Machine Works Can Increase Its Value
There are good reasons to idle a machine but knowing how much idle time a machine has can help identify instances when it can be reduced. Reducing idle time obviously saves on fuel costs, but one of the chief hidden costs of excessive idle time is reduced residual value of a machine.
Is your machine idling excessively at the end of the workday without a valid reason? Understanding the idle time of your compact excavator not only tells you how much fuel is being used, but idle time also advances the service meter, putting the machine closer to the next service interval. When unnecessary idle time can be reduced, it not only conserves fuel but also extends the calendar time of service intervals — giving you an advantage.
Knowledge is power and knowing how far from the next maintenance interval a machine is not only helps schedule the maintenance, but can also help owners schedule jobs and make better utilization of their fleet.
Armando Najera is product manager of compact excavators at Komatsu America Corp., based in Rolling Meadows, Ill.