Compact Excavator Terminology Explained: Your Essential Guide to Mini Digger Lingo
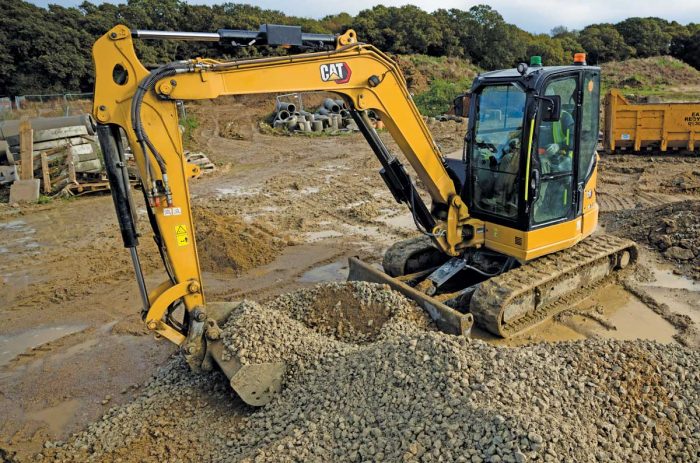
Decoding Key Terms Every Contractor Should Know
Compact excavators have become indispensable on jobsites — from residential landscaping projects to major infrastructure developments. Their versatility, performance and ease of transport have made them a favorite among contractors and equipment rental companies alike. With such widespread use, a specialized vocabulary has evolved to describe everything from undercarriage designs to advanced machine control systems. This article serves as a dictionary of terms used in the compact excavator industry. Whether you’re a seasoned operator or new to the world of mini machines, understanding these terms will help you make more informed decisions when buying, renting or maintaining your equipment.
Compact Excavator/Mini Excavator
A compact or mini excavator (same thing) is a small, maneuverable piece of earthmoving equipment used in off-highway construction and landscaping. These machines generally weigh between 1 and 8 metric tons and are designed to work in confined spaces. Fitted with a dedicated track undercarriage, operator station and a boom equipped with a bucket or attachment at the end, mini excavators are ideal for tasks ranging from trenching to demolition. They are easily transported on trailers or small trucks, making them well-suited for urban and residential areas, and they can be fitted with a wide variety of attachments — from augers to brush cutters — enhancing functionality on the jobsite.
Attachments
Attachments are additional tools that can be fitted to a mini excavator to expand its functionality. The versatility of mini excavators is largely due to their ability to accommodate a wide array of attachments, making them true tool carriers on the jobsite. Common attachments include:
- Buckets: Ranging from ditching and grading to specialized cemetery or skeleton buckets.
- Breakers: For demolishing concrete or other hard surfaces.
- Grapples: Ideal for handling debris and bulk materials.
- Augers: Used for drilling holes or planting trees.
- Brush Cutters, Thumbs and More: Additional attachments that enable tasks ranging from vegetation clearing to precision material handling.
Attachment Couplers
These systems enable quick and secure attachment changes, maximizing machine uptime and operational efficiency. Standard couplers require manual securing of pins during attachment exchange. Quick-couplers allow operators to switch attachments rapidly from within the cab without leaving the seat, enhancing safety and productivity. Tilt couplers and tiltrotators offer additional flexibility by permitting the attachment to tilt or rotate (up to 360 degrees in the case of tiltrotators), which is invaluable for complex grading or utility work. Selector valves allow operators to switch hydraulic flow between multiple attachments, such as a hydraulic thumb and a breaker, without manually changing hoses.
Backfill Blades
Attached to the undercarriage frame, a backfill blade is an important part of the compact excavator’s arsenal. The backfill blade is used primarily for grading, leveling and trench backfilling. It also provides additional stability during digging operations. There are some unique backfill blade options out there. Blades can come in simple push configurations or angle versions. Blades on the smallest micro units will have the ability to fold in with a retractable undercarriage. There are also four-way and six-way angle blades.
Eco Modes and Anti-Idle Systems
These features are designed to reduce fuel consumption and emissions. Eco Mode automatically adjusts engine rpms to conserve fuel when full power is not needed, while anti-idle systems either shut off the engine after a set period or lower rpms to reduce fuel consumption and emissions. With rising fuel costs and environmental concerns, these energy-saving technologies are becoming standard in modern compact excavators.
Compact Excavator Engines
Compact excavators are typically powered by diesel engines, although electric options are emerging. Diesel engines sport power ranges generally between 13 and 70+ hp. In the United States, these diesels comply with EPA’s Tier 4 Final emissions standards. Engines over 25 hp often include emissions systems like diesel particulate filters (DPFs) or selective catalytic reduction (SCR). Battery-powered electric mini excavators provide quieter operation, zero emissions and lower fuel costs. Electric-powered diggers are particularly beneficial in indoor demolition, residential areas and locations with strict noise or emissions regulations.
Grade Control
Grade control systems help operators maintain precise digging depths and slopes. Aftermarket options (e.g., Trimble, Topcon) offer full automation, while manufacturer-integrated systems (e.g., Cat’s Ease of Use, Bobcat’s Depth Check) provide real-time guidance without full automation. Grade control systems help operators dig precisely, measuring the position of the bucket and boom and automatically controlling certain parameters set by the operator (depth, slope and elevation control) or even using a 3D model to dig and sculpt. Applications such as trenching for footings, grading ditches or digging out basements might require a consistent grade, sustained slope or precise design.
Hydraulic System
Hydraulics are the lifeblood of excavator operation, powering everything from digging to attachment actuation. Main hydraulics provide the primary power for boom and bucket movement and excavator travel. Load-sensing hydraulics adjust the flow rate based on load demand, ensuring consistent performance regardless of the work being done. Auxiliary hydraulic horsepower refers to additional hydraulic power available specifically for operating attachments. It’s typically measured in gallons per minute (gpm) and pressure (psi).
Long Stick: A mini excavator with a long stick configuration is a compact machine with an extended boom that can dig deeper and reach farther than a standard mini excavator. They are useful for dredging and deeper excavation projects.
Most Popular Mini Excavator Size Class
The 3- to 4-metric-ton mini excavators are the category’s biggest sellers. These machines offer the perfect balance of power and versatility, providing just enough capacity for tougher tasks while still being small enough for tight jobsites and trailering. With more than 20 brands in the market, ranging from Kubota to New Holland Construction, there’s no shortage of options when eyeing the 3- to 4-metric tonners. Contractors love them for their ability to tackle a wide range of projects, from digging trenches to grappling rocks, all while being compact enough to maneuver into backyards and confined spaces. With hydraulic systems capable of handling a variety of attachments, these machines are equally adept at lifting, digging or even clearing brush with tools like grapples and mowers.
Operator Station
The cab (or operator station) is the control center from which an excavator is operated. There are enclosed vs. open-air options, ranging from fully enclosed, climate-controlled cabs to open-air ROPS (roll-over protective structures) that provide basic safety. Most operator stations now feature electro-hydraulic joystick controls, ergonomic layouts and digital interfaces that enhance comfort and efficiency. Many operators now benefit from digital displays and LCD touchscreen panels that provide access to machine diagnostics, maintenance data and attachment controls.
Tail Swing
Tail swing refers to the design characteristic of an excavator’s rear end relative to its tracks when the machine rotates. Conventional tail swing means the rear extends beyond the track width during operation. Reduced tail swing notes the counterweight may protrude only slightly beyond the track limits. Zero tail swing indicates the machine rear never extends past its tracks, allowing for work in very confined spaces. Zero tail swing models are especially popular in urban and residential areas where space is limited, enabling operators to work closer to structures without obstruction.
Telematics
Telematics encompasses the digital systems that monitor an excavator’s operational data and location. Remote diagnostics allow maintenance teams to monitor machine health in real time, often via smartphones, tablets or computers. GPS tracking enhances security by tracking the machine’s location, which is especially useful for rental fleets and large construction operations. Data analytics provides insights into usage patterns, maintenance schedules and even fuel consumption, helping optimize overall performance.
Let’s take a look at the smallest mini excavators on the market.
Tracks for Compact Excavators
Tracks are continuous belts — commonly made of rubber, steel or a hybrid — that enable the excavator to move over various terrains. Rubber tracks offer high flotation and reduced ground disturbance, ideal for lawns and softer surfaces. Steel tracks provide enhanced durability and are used in more aggressive, heavy-duty applications. Hybrid tracks (rare on smaller units) combine features of both rubber and steel, often with detachable pads. Many track pattern choices are available, ranging from a C-pattern tread (balanced for general use) to a zig-zag pattern tread (for mud and snow).
Undercarriage
The undercarriage is the assembly of components that support the machine’s tracks and contribute to its mobility and stability. Sprockets are profiled wheels with teeth that drive the tracks. Idler wheels guide and tension the track, usually located at the front of the track frame. Rollers are mounted at both the top and bottom of the track frame. These support and guide the track’s movement. Some models feature innovative designs such as retractable undercarriages or foldable blades that help the machine pass through tight spaces.
Keith Gribbins is publisher of Compact Equipment.
Key Mini Excavator Specs
Operating Weight: The total weight of the excavator, which impacts transportability, stability and ground pressure. Mini excavators typically range from around 2,000 to 10,000 lbs, while giant compact models (midis) can exceed 22,000 lbs.
Dig Depth and Reach: The maximum depth the bucket can excavate and the horizontal reach of the arm at ground level, determining the machine’s capability for digging and material placement. The Bobcat E10 has a max dig depth of 6 ft and a max horizontal reach of 10 ft, 2 in., while the Bobcat E88 with a long arm has a max dig depth of 15 ft, 2 in. and a max horizontal reach of 23 ft, 5 in.
Bucket Breakout/Digging Force: A measure of the force exerted by the bucket and stick during excavation, determining the excavator’s ability to break through tough materials. The Caterpillar 301.5 mini excavator has a stick digging force of 1,843.4 lbf and a bucket breakout force of 3,169.8 lbf.
Lift Capacity: The max weight an excavator can lift at a specific height and reach, influenced by boom angle, arm extension and counterweight. Mini excavators typically have lift capacities ranging from 900 to 6,000 lbs, while larger compact models can exceed 10,000 lbs.