Ensure You Are Correctly Complying with OSHA’s New Crystalline Silica Dust Regs
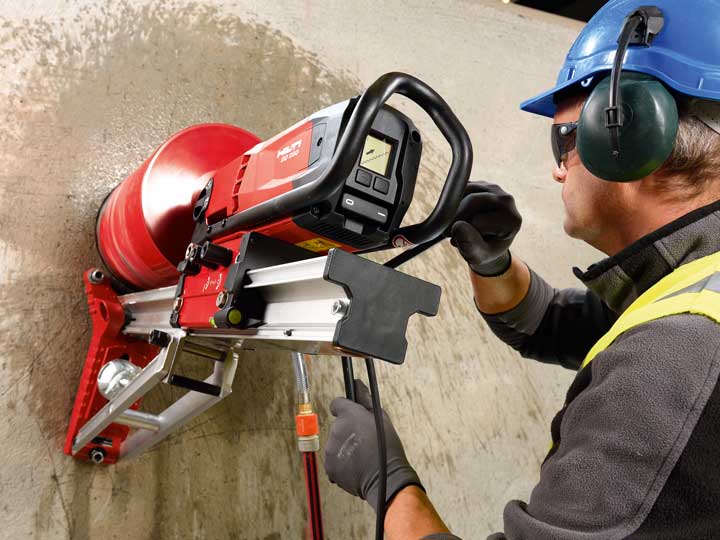
Because the Hilti DD 250 is used for wet coring applications, it is Table 1 compliant with the new OSHA §1926.1153 standard for respirable crystalline silica dust.
On March 25, 2016, the Occupational Safety and Health Administration (OSHA) issued a final rule on respirable crystalline silica dust. The new rule updated regulations that were established more than 40 years ago and introduced requirements for reducing an employee’s exposure to silica dust. The final rule is written as three separate sets of regulations for construction, general industry and maritime. This white paper (which can be downloaded at dust.us.hilti.com) provides a brief overview of the requirements in the new construction standard.
Overview
Under the existing silica rule established in 1971, employers were responsible for testing exposure and finding ways to limit exposure below ~250 μg/m3 averaged over an eight-hour workday. The new standard aligned the permissible exposure limit (PEL) for the construction industry and general industry to the NIOSH recommended limit of 50 μg/m3 averaged over an eight-hour workday (time weighted average, or “TWA”) — a level already adopted by several European countries. According to OSHA, the new PEL is expected to prevent hundreds of silica-related deaths and illnesses each year — including 900 new cases of silicosis.
In an effort to increase the ease of compliance, OSHA included a layer of flexibility for determining the control methods needed to protect employees that was not a part of the 1971 standard. Under the new OSHA construction standard, OSHA offers three methods an employer can choose from to demonstrate compliance and assess employee exposure. An employer can choose from one of the three or any combination of the three to ensure their employees are protected. The options are:
1. Table 1: a table of pre-defined tasks and specified control methods available in the market today.
2. Performance or ‘Objective Data’: assess exposure by providing objective data proving the control method used reduces silica dust exposure below the permissible exposure limit (50 μg/m3).
3. Scheduled Air Monitoring program: assess exposure by implementing a scheduled air monitoring program to ensure employees are not exposed above 50 μg/m3.
Option 1: Table 1
Table 1 lists tasks and equipment-control methods that OSHA has determined will reduce exposure to acceptable levels. The table includes requirements for when a task is performed for different periods of time and in different environments. An employer that fully implements an equipment-control option on Table 1 for a task will not have to perform air monitoring for that task. This will most likely be the most popular option. To see an entire Table 1 entry (not just the clip above), visit dust.us.hilti.com, and it will make more sense.
Option 2: Performance or ‘Objective Data’
OSHA allows employers to use objective data to provide evidence that the control method(s) in place reduces the exposure level below 50 μg/m3 over an eight-hour TWA work period. Objective data can be air monitoring data compiled by the employer or a third party, such as universities, trade associations or manufacturers, which is sufficient to accurately characterize exposure. The data relied on must reflect conditions that are similar or worse than the employers current worksite conditions.
Option 3: Scheduled Air Monitoring
If the employer prefers to generate their own exposure data, the “scheduled monitoring option” can be used. When this option is used, an employer is required to implement an air monitoring program when workers are exposed over the Action Level (AL) of 25 μg/m3 over an eight-hour TWA work period and implement control methods.
In addition to the requirements related to assessing and controlling exposures, all employers covered by the standard must have a written plan that identifies silica-generating tasks, the engineering controls and work practices that will be used for each task, respiratory protection (for exposures above the PEL), housekeeping practices used to limit exposures and procedures that will be followed to restrict access to areas where silica-generating tasks will be performed. The “restrict access” requirement is intended to eliminate exposure of unprotected bystanders. The plan must be implemented by a “competent person.” The competent person must 1) be capable of identifying existing and foreseeable respirable crystalline silica hazards, 2) have the authority to take prompt corrective measures to eliminate or minimize silica hazards and 3) have the knowledge and ability to implement the exposure control plan.
Employers are also required to follow a medical surveillance plan for workers that are required to wear a respirator — under the new standard — for 30 or more days per year. Under the surveillance plan, each worker that meets the requirement for testing must be offered an exam within the first 30 days of the assignment, and every three years after the initial exam if the worker continues to meet the trigger for the exam. A physician or other licensed health care professional (PLHCP) must conduct the exam. Within 30 days of the exam, the employer must ensure: (1) the PLHCP explains the exam results and gives a “medical report” to the employee; and (2) the PLHCP provides the “medical opinion” to the employer. The medical opinion may trigger limitations on respirator use, and to the extent that the employee agrees, limitations on exposure to respirable silica and/or examination by a specialist.
This is only a fraction of the fantastic white paper provided by Hilti, the multinational power tool manufacturer. Read the rest of it (including in depth analysis of each method of compliance) right here: dust.us.hilti.com.