When Should You Repair, Rebuild or Replace Equipment?
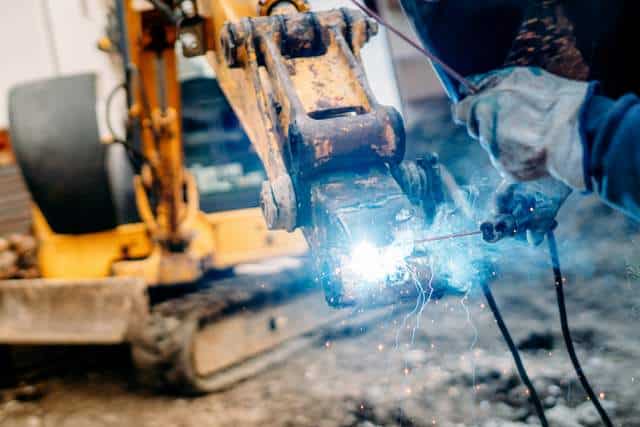
Equipment costs are a significant expense for every construction company. And despite the strength and durability of heavy construction equipment, harsh working conditions will eventually cause even the most robust tools to stop functioning. When equipment fails, owners have options. Often, they can repair, rebuild or replace any piece of equipment. Below, we’ll cover when to use each of these strategies, as well as their pros and cons.
When to Repair
The smaller and more pressing the issue, the more cost-effective simple repairs will be. If a piece of equipment is in excellent condition and isn’t functional or safe to operate because of a single broken component, doing repairs can be a time-effective and money-saving solution. Conducting repairs will typically be the cheapest option available compared to other choices. It’s effective if you are worried about the expenses of more extensive maintenance or equipment replacement.
Combined with a robust maintenance and equipment monitoring program, repairs are typically the best alternative regarding any situation where downtime or cost will be a significant issue.
You should consider, however, that most repairs will be limited in scope. While a rebuild or replacement can improve a machine’s fuel efficiency or performance, repairs will usually just bring it back online.
Sometimes, a repair may only buy you some extra time. Damaged or non-functional equipment will need a rebuild or even a replacement if the problem is serious enough. Depending on how costly downtime will be, a quick repair may be the right decision, but you should be aware this may be a temporary fix. Check the maintenance records and speak with maintenance staff to give yourself an idea of how much longer the machine will work after a repair.
Depending on the machinery’s age, it may also be difficult or impossible to source replacement parts. Manufacturers don’t create replacement parts forever, and you may find essential components aren’t available. If this is the case, a full replacement will likely be the best option.
When to Rebuild
Equipment rebuilds are larger in scope than simple repairs. With a rebuild, a technician will replace all the parts of a specific component in a piece of equipment.
A rebuild will likely be more expensive than a repair. At the same time, however, a rebuild will almost certainly be cheaper than replacing the equipment altogether, even if you plan on reconstructing a significant portion of a machine.
Rebuilds can also drive down the average lifetime cost of equipment by extending its lifespan and reducing the need for maintenance over time. Combined with a good maintenance monitoring program that ensures equipment health, you may find that rebuilds, despite being more expensive than repairs, cost you less when all upkeep expenses are factored in.
Another advantage of rebuilds is that the exact scope will vary from dealer to dealer. Some offer component rebuilds, where technicians will restore components like equipment powertrains or hydraulics, in addition to full machine rebuilds. If you don’t want to commit to fully refurbishing a piece of equipment, the technician can rebuild by replacing the parts most in need of maintenance or an upgrade.
As a result, a rebuild will allow you to take advantage of newer components without investing in a completely new machine.
Like with simple repairs, you can schedule rebuilds based on factors like condition monitoring and fuel consumption. With a plan in place, you can ensure equipment health and increase the lifespan of your machinery by regularly upgrading with the best available parts.
When to Replace Equipment
A full replacement will typically be the last option you consider, due to its cost. But because repairs and rebuilds aren’t always practical, you should always keep it in mind.
There are some situations where it’s almost always a good idea to replace equipment. If the broken machine is outdated, low-quality or no longer supported by its manufacturer, you should consider replacing it. If it needs extensive repairs or full replacement of certain components — like a powertrain — but the dealer no longer offers offer maintenance support, rebuilds or replacement parts, it may be a good idea to consider a replacement.
You should also consider the advantages that new equipment can provide. If old machinery is less efficient than newer models, requires specialized training or puts your company at risk of not meeting regulations and safety standards, a replacement can also be an upgrade. Many newer models of heavy equipment, for example, are more fuel-efficient. You’ll want to consider diesel savings when calculating the cost of a replacement against a repair or rebuild.
A replacement will almost definitely create the greatest capital expense of these three options, as buying new equipment will be more expensive than repair or replacement. You’ll need to pay taxes on the full cost of new machinery, which may not be the case with a repair or rebuild. You’ll also likely need to pay for a new warranty.
Downtime can also be a serious issue. Repair is typically the quickest way to get a piece of equipment back online. If you replace a machine, you’ll need to wait for it to be procured, shipped and delivered before you can get back to full productivity.
While replacement will drive up costs in the short-term, new equipment may lower upkeep in the long-term. A new machine will likely need less maintenance than one kept functional with repairs or rebuilding. You can also take advantage of strategies that decrease the cost of new equipment to make replacement a more economical option.
Best Options for Managing Broken Equipment
When equipment breaks down, you have a few different options. Repairs and rebuilds will allow you to get it up and running without needing to replace it. However, these options can’t fix all problems and may not be possible if a manufacturer has stopped fabricating replacement parts.
Replacing equipment is also a possibility and will typically present an opportunity to upgrade your machinery to more modern or fuel-efficient models. However, a replacement will also be significantly more expensive than a rebuild or repair in most cases — though there are strategies you can use to reduce the expenses.
Megan R. Nichols is a technical writer and blogger who covers industrial and scientific topics. She has four years’ experience covering these industries writing for sites like Thomas, IoT Times, IndustryWeek and Discover Magazine. For more of her work, subscribe to her blog, Schooled By Science.