Grade A: Learn Why Scotty’s Contracting and Stone Capitalizes on Machine Control Systems
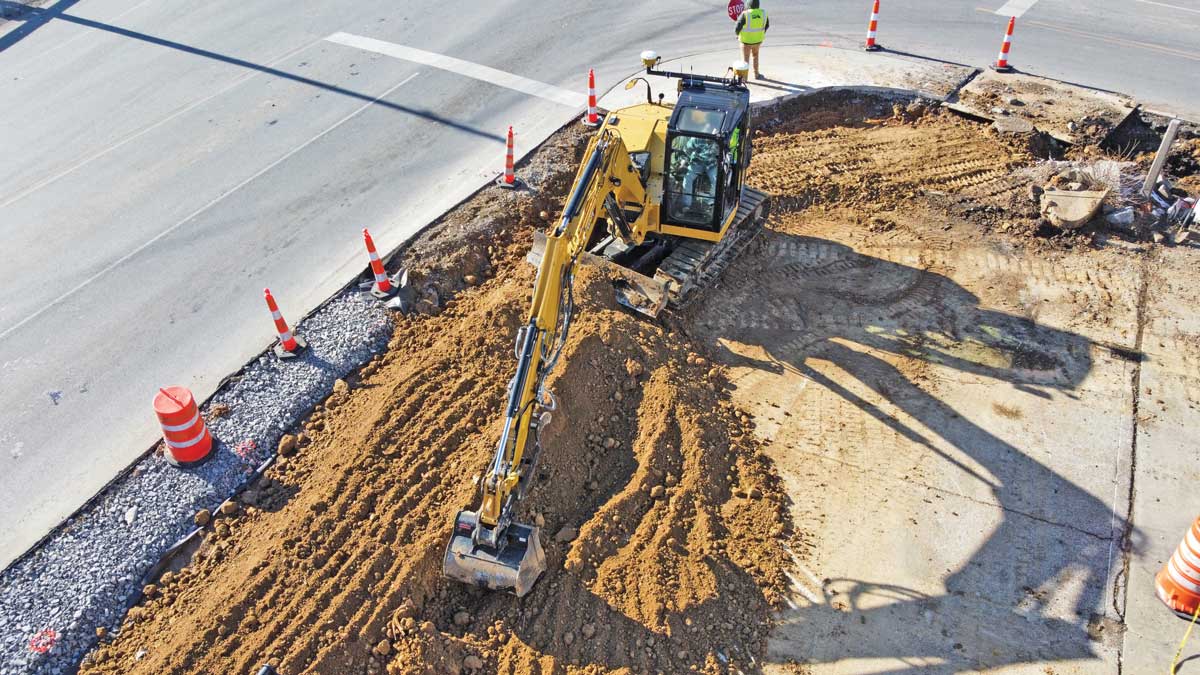
Founded in 1972, Bowling Green, Ky.-based Scotty’s Contracting and Stone LLC has become an industry leader in the state’s civil and heavy highway sector. It is among the largest heavy highway contractors in the region, with specialties in asphalt paving, grade and drain construction, aggregates, driveways and parking lots. The company owns 14 asphalt plants and five quarries, as well as a Technology Center Environmental Laboratory that performs analytical testing services for the asphalt and aggregate industry.
Company leaders say that its more than 50 years of success is due largely to the organization’s overall focus and emphasis on continuous improvement. They believe that the company’s investment in the best tools for its crews is what has helped the organization meet and beat project timelines and deliver exceptional results, reducing cost, time and errors over the past five decades. Currently, the company has over $70 million of equipment deployed throughout Kentucky — but it’s not all about big machines for this industry innovator. In fact, recently, crews embraced smart and small machines to demonstrate big performance on projects.
“We’ve seen a trend away from bigger machinery,” said Chris Higgins, vice president of construction and engineering at Scotty’s. “It used to be that everyone had to have a backhoe on every job — that was the piece everyone wanted. Today, our operators want mini excavators and skid steers because of the ease of use and flexibility.”
Understanding this shift requires a bit of a look back at the company’s technology-enabled equipment evolution.
Mini Machine Focused
Scotty’s has a long-time commitment to technology. For instance, the company was one of the first in the region to put 3D laser-guided machine control equipment on the job beginning in 2000. Since then, the company has adopted GNSS, drones and robotic solutions to provide more accurate data and to reduce costs, time and errors. With that adoption came a building of skills such as 3D modeling. Higgins said, “We build a lot of models. We have a great engineering staff and use Trimble Business Center to crank out a model for every project, a skill that helps us optimize project work — whether paving a road or installing drains — to ensure we deliver quality results.”
Over the last decade, the Scotty’s team has seen a need for smaller equipment, specifically a GNSS-enabled mini excavator, to help work in tight spots. They looked to Sitech MidSouth’s technology sales specialist Scott Thomas for ideas.
“We initially teamed up with Scott and his team to customize a smaller excavator with sensors and wiring in our shop,” said Higgins. “It worked pretty well, so we looked for a similar production system from our manufacturer.”
Not long after, Cat introduced its line of next generation mini hydraulic excavators. These machines ranged from 1 to 10 metric tons and offered flexibility and performance. When the Next Generation Cat 308 mini excavator equipped with Trimble Earthworks Grade Control Platform became available, Scotty’s was first in line to purchase it. This was the industry’s first integrated 3D aftermarket grade control system with automation for a mini excavator. The value of the system on the job became so clear that the firm bought a second one a month later — and two more after that.
Mini excavators are making big waves on jobsites all over North America. Click here for the latest news on these machines and the companies that make them.
An Automatic Opportunity
The flexibility of the mini excavator is ideal on projects that have tight spaces or require small cuts and fills with a constant focus on grade, according to operators at Scotty’s.
“One thing that is common in all widening projects is tight spots and existing utilities,” explained Higgins. “Having a machine that can work in these close areas with GNSS-enabled accuracy is a big advantage.”
He added that the availability of the automatics mode has changed processes for all excavator operators, no matter the size of the equipment. The Trimble Earthworks “Autos,” or automatics mode, automates the boom and bucket operation while the operator controls the stick for consistent, high accuracy finished grade in much less time.
“This feature makes the operator’s job so much easier,” said Higgins. “With Autos, the operator can dig to grade without worrying about going below grade. Combine that with grade control and our operators don’t want anything else.”
The other advantage, said Higgins, is the lack of rework and increased speed of the operator. “The excavator has always taken the best operator to run. The coordination that’s required for an indicate-only machine is real. Operators have to manage the boom and bucket, while moving along a grade, all while watching the cutting field and keeping an eye on traffic,” he said.
It’s a challenging job that used to require multiple passes to ensure accuracy. “With Trimble Earthworks, operators can turn on automatics and dig to grade on the first pass. Now, that operator can concentrate on the overall operation of the machine rather than numbers jumping on the screen.”
Operator ease of use has been particularly valuable. “While I’ve always preferred to train new operators without the benefit of automation so they learn grade, the bucket movement, and how to run the machine, that’s not always an option, particularly in today’s tight labor market,” said Higgins. “With GNSS and automatics, we can get someone up to speed much faster. A side benefit is attracting new workers who love technology to our industry.”
The flexibility of the mini excavator was evident in a project along highway 62 in Muhlenberg County. This was an extensive urban widening project with many challenges such as utilities, traffic and very narrow widening width, often 4 ft or less.
“The demand I have on the mini hex machine is incredible,” said Higgins. “I only have two, and all of our operators are wrestling over them. Those are the hottest items in my fleet right now because of flexibility, and there’s more we’re learning about its capabilities. We’re very pleased with the productivity, which on a project with many small cuts and hills, could easily improve production by 50 percent. We’ll add more in the future, no doubt.”
Vicki Speed is a freelance writer covering the construction industry.