Operation Efficiency: Pro Tips for Operating a Compact Track Loader
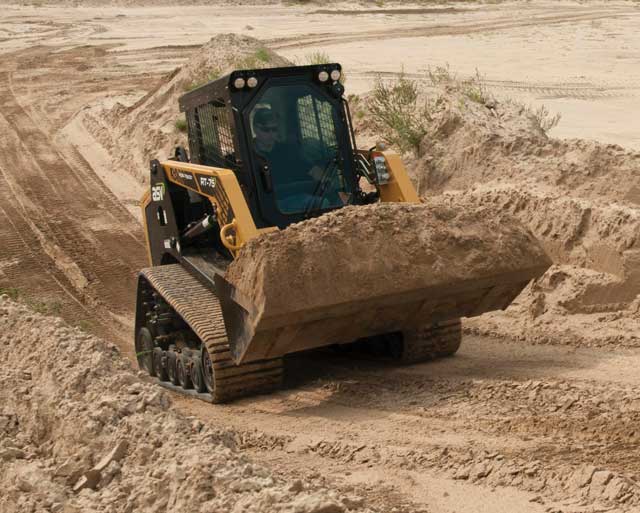
When it comes to units sold in America, compact track loader sales went from 37,000 in 2015 to 45,000 in 2016, outpacing skid steers sales, according to the manufacturers that we surveyed. That’s a jaw-dropping jump.
When an operator seats himself in a compact track loader, he always faces two tasks. The first is to take care of the machine. The second is to move material efficiently and productively or put to work some other multitasking attachment. Note the priority: First the machine and then the job. Operating a track loader carelessly can lead to all kinds of grief and unwanted downtime. Manufacturers of compact machines try to engineer them to withstand operator abuse and normal wear and tear, but there is no substitute for wisdom in the driver’s seat. Hereafter is some wise counsel and perspective for owners and operators of track loaders from those who know the machines best, their makers.
Track Loader vs. Skid Steer
The first piece of advice always given to skid steer operators when they move to a track loader is “do not rip donuts on concrete,” in the words of Bill Wake, director of product development at ASV, the Minnesota compact machinery company. “You can do donuts in a track loader just as you can in a skid steer, but you are leaving rubber behind when you do them, and tracks are more expensive than tires.” Wake recommends a tight three-point turn instead of the damaging swivel turn. While he cannot point to hard data affirming his point, he says the experience of numerous ASV customers is that eliminating donuts “will drastically reduce the amount of wear on your tracks.”
That said, Wake believes the biggest difference in efficient operation of a skid steer and a track loader is not in the turning, but in the loading. “When running on tires, an operator rams the load to get a bucketful. A track loader has so much more traction than a skid steer that its operator can utilize traction, rather than momentum and spinning of tires, to get a full load. Spin is wear.” Learning this loading technique is central to extending the life of tracks.
All rubber tracks are not created alike. The Kubota model SVL95-2s track loader rolls on rubber tracks that are tapered to the outside to help shed debris.
Undercarriage Awareness
“Once everyone has learned the lesson about the difference between skid steers and track loaders,” says Jorge De Hoyos, senior product manager for skid steers and compact track loaders at Kubota Tractor Corp., “then idlers and rollers are the first to wear out on the undercarriage. It depends on how well the operator operates the machine.”
Skid steers ride on tires and axles, but track loaders move on tracks, idlers, rollers and sprockets, and operators should be aware of them all. Improper operation prematurely wears out these undercarriage components. Operating habits that stress these components include running across slopes rather than up and down them. Running crossways, with one side of the track loader higher than the other, places sideways stress on rollers and sprockets, which are primarily engineered for vertical pressures. The same is true of curb-crossing. When a curb is crawled at an angle, the rollers and sprockets are needlessly asked to withstand twisting pressures that ultimately reduce their working life.
Another good operating practice is keeping an eye on the tautness of a track. “Too loose a track can lead to de-tracking problems,” says Michael Shebetka, product manager at Takeuchi US. That is, a loose track will slip its cogs and come off. “When it rolls off, it also will cause the track to stretch beyond its normal threshold, making it harder to keep on thereafter. On the other hand, if the track is too tight, it will cause premature wear on sprockets and idlers.”
Shebetka notes that these habits — angling across curbs, running tracks too slack or too tight — damage tracks but so does rolling over demolition-type debris such as chunks of concrete with rebar. “All of these practices can result in chunking and cuts in the rubber track that expose internal steel cables. This will allow moisture to penetrate and cause the cables to weaken and eventually fail.”
However, all rubber tracks are not created alike. For example, ASV tracks are not vulnerable to rusting because they have no steel in them. Instead, the belts are reinforced with nylon and polyester fabric and molded in one piece to eliminate seam weakness. Warranties for ASV tracks are for two years or 1,500 hours, and Wake says a CONEXPO-CON/AGG customer claimed to have 3,600 hours on his rubber tracks. Over at Kubota, the model SVL95-2s track loader rolls on rubber tracks that are tapered to the outside to help shed debris. The bottom line: An operator should know the characteristics of the tracks he’s riding on.
Keep It Clean
A conscientious operator recognizes the varying impact on a track loader via different work conditions. For instance: Florida sugar sand becomes airborne around a working machine and gets into everything.
Skid steer tires roll over debris. Tracks roll through it, with bits and pieces getting wedged inside the undercarriage and between components. Ground material is a threat to all track loader undercarriages.
De Hoyos says a critical “post-op” procedure to protect tracks and components is simply to clean them thoroughly at the end of each work day. “Clean that undercarriage so the soft stuff doesn’t set up overnight,” he says. “Some operators have a shovel clamped to their unit somewhere. When they are done operating and before they call it quits, they knock out all the dirt and debris they can.” They also routinely check for debris in the morning light with rested eyes.
Kubota undercarriages are “very open” so that a shovel or an arm can reach areas where rocks, roots or clods have collected. ASV also has gone to an open undercarriage design. Buck Storlie, the company’s testing and reliability leader, says the openness “lets debris fall in but also lets it fall right back out. We have good data that shows our self-cleaning design doubles or even triples sprocket life and, in some applications, increases wheel life exponentially.”
Other brands have opted to cover idlers and sprockets to protect them from debris accumulation. In either case, operators should visually inspect and systematically clear out foreign material to lessen wear. This practical habit avoids a working machine becoming a nonworking machine because of a worn sprocket or a damaged idler.
A conscientious operator also recognizes the varying impact on a track loader of different work conditions. Shebetka notes that “Florida sugar sand becomes airborne around a working machine and gets into everything. It fills up the bottom of the chassis, plugs filters and can prematurely wear out an undercarriage if the tracks are not tensioned loosely for this type of ground conditions.” Working in loamy dirt, on the other hand, is a whole other situation. Operator maintenance routines should reflect work conditions.
A track loader is more than an undercarriage, of course. Staying on top of engine and hydraulic fluids and mechanical components is a given. Still, it is overlooked. “We always tell operators and maintenance techs to look at the manual, but nobody does,” says De Hoyos. So Kubota makes it easy: An abbreviated maintenance schedule is affixed to a wall of the engine compartment. “Open up the hood and look to the left, and there it is. Just follow the diagrams. It tells where every grease fitting is. We get positive feedback from customers about that.”
Also Check Out MWE’s Undercarriage Components
MWE offers one of the widest ranges of aftermarket undercarriage components for compact track loaders and compact excavators, including rollers, sprockets and idlers. Manufactured from high-quality materials, MWE undercarriage components are designed to provide long service life and reliability under the most severe operating conditions. Also, MWE stocks one of the widest ranges of components for most major brands of compact equipment. For more info, visit tracksandtires.com.
Giles Lambertson is a freelance writer for Compact Equipment.