Maintenance Tips for Rubber Tracks on Compact Track Loaders
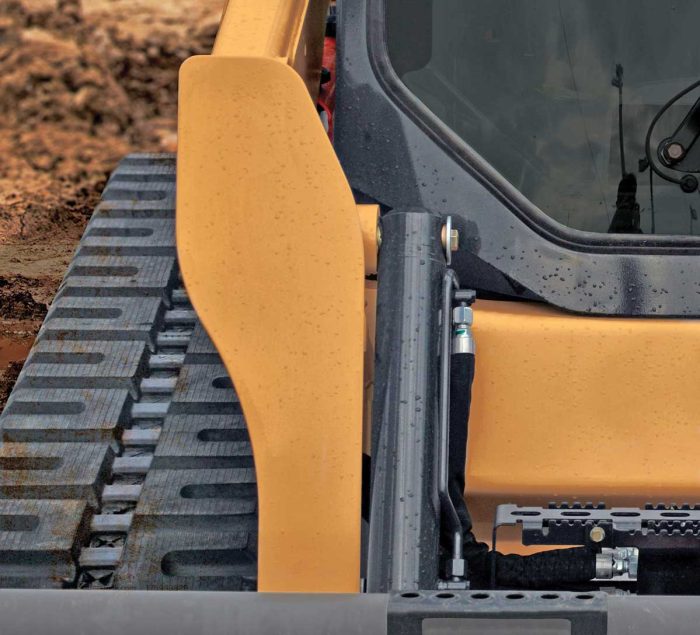
Want to keep your compact track loader’s tracks in good, working condition? Check out the following maintenance pointers.
Daily
Rubber tracks should be inspected daily. One should look for cuts, cracks, exposed wires and movement of the metal imbeds. The track and undercarriage should be rinsed off and any debris removed.
Weekly
Once a week the tracks and undercarriage should have a more in-depth inspection. This should include measuring the tread wear, examining undercarriage components such as the rollers, drive sprocket and idler arm. If there is excessive wear on any of these components, they should be changed out, as they will adversely affect the performance and life of the tracks.
Monthly
There should be a total inspection of the undercarriage and rubber tracks. Along with the normal daily and weekly maintenance, the tension of the tracks should be checked and adjusted according to the machine manufacturers specifications. There should also be a complete cleaning of the undercarriage and tracks. This can most easily be performed with a pressure washer.
Tracking Wear
Tread Depth
The first way to gauge the wear of your tracks is by taking an initial tread depth reading. Going forward, one can take a new reading during their weekly or monthly maintenance. This will allow them to take the percentage of wear compared with the machine hours and come up with an estimated wear life of the track. Although it is extremely rare for CTL rubber tracks to last the total life of the tread, due to the heavy torque of these machines causing breaks, it still gives an idea of the maximum possible life you can get out of the tracks.
Cutting and Chunking
Damage to the tracks in the form of cutting and chunking will significantly affect the life of the tracks. When a cut or rubber chunk reaches the steel cables, it will then allow water to attack the cables in the form of oxidation, which leads to rust. Rust will cause the steel cables to eventually break, causing total failure of the track.
Exposed Cables
The rubber tracks should daily be examined for exposed cables. If exposed cables are seen, it is best to clip them off with wire cutters. Depending on the severity of damage to the cables, this may limit catastrophic damage. If the cables are totally separated due to impact damage or debris cuts, the track will need to be replaced.
Exposed Metal Imbeds
If the metal imbeds are exposed in any area outside of the guide lugs, this is evidence of severe damage to the rubber tracks. This is normally caused by some type of impact damage. Impact damage can happen while running over hard debris during operation or from debris being trapped between the undercarriage of the machine and the rubber track.
Tips for Extending Track Wear
Undercarriage Maintenance
In order to get the best possible life out of the rubber tracks, first you should begin with a high-quality track such as Trelleborg’s CRT-800 rubber track. This, along with several external maintenance activities, should be done regularly, to ensure the best life possible out of the tracks. Undercarriage maintenance is one of the most important operations to be followed because machine undercarriages have many wearable parts that both need to be examined regularly and replaced at the machine manufacturer’s recommended intervals. Worn parts can cause many problems, such as de-tracking, high levels of vibration, excessive wear and premature breaking. Track tensioning is one of the items that can affect the life of a rubber track for the positive or negative. Too loose will cause de-tracking, which will eventually cause damage to the tracks, leading to failure. Too tight will cause the track to crack, loosen metal pieces and lead to eventual failure.
Application Maintenance
Maintaining a clean worksite can not only greatly extend the life of the rubber tracks but will also help with maintaining the machine. Any type of debris, such as scrap wood, cinder blocks, bricks, stones and rebar can cause impact damage and, ultimately, failure of rubber tracks. By walking the worksite and removing these types of debris, the life of the rubber tracks will be extended greatly.
Driver Training
It is also important to make sure that the driver of the machine is properly trained. They should be prepared for all situations they may encounter while operating a CTL. Training will ensure that the operation is safe for the driver, the environment and the machine itself.
Driver Awareness
Driver awareness can be one of the most important factors in extending the life of your rubber tracks. Being aware of the application and not running over debris, rock-filled surfaces and curbs will significantly reduce impact damage. Part of the training that each driver should have should be based upon application awareness.
Mike Giordano is segment manager, rubber tracks, at Yokohama TWS North America Inc.