Feel the Heat: Forget the Cold and Keep Work Going with Jobsite Heating Solutions
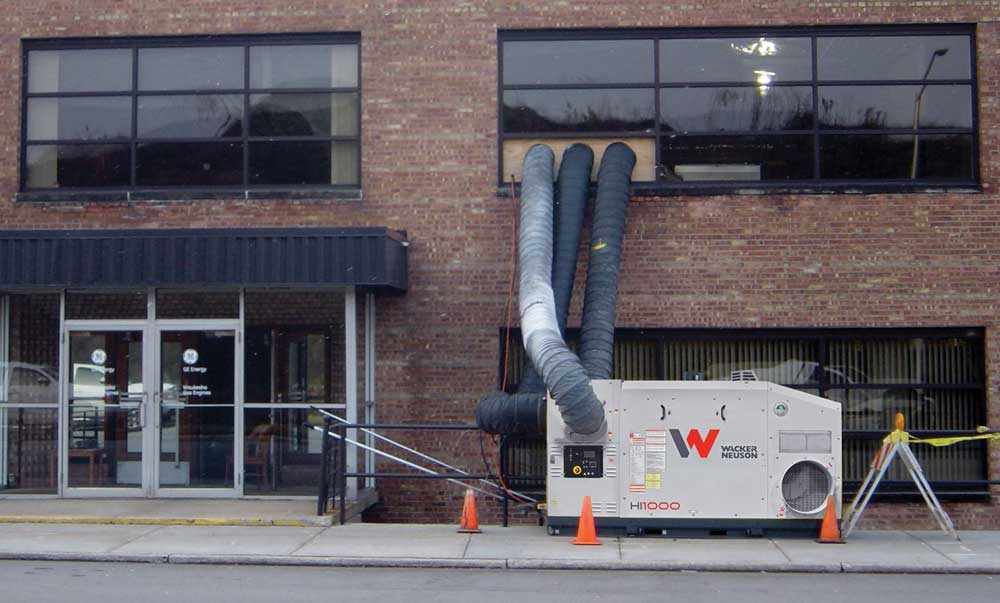
Indirect air-fired heaters, like Wacker Neuson’s HI1000, provide a consistent and safe heat source so contractors can work year-round despite cold weather conditions.
The days are shorter, and there is a chill in the air. This signals the time when contractors in cold weather climates hurry to finish enclosing structures so crews can move inside and continue working during the long, cold winter months. It is also the time when contractors need to consider their heating needs so the trades can continue to work and keep jobs on schedule. There are heating options to keep the indoors dry, warm and healthy and heaters to keep the ground thawed for work to continue year-round.
Surface Heat for Thawing and Concrete Curing
Frozen ground is no longer an issue for winter construction and concrete work. Hydronic surface heaters, also known as ground heaters, can be used for thawing and maintaining soil temperature for cold weather construction from excavation, commercial concrete preparation and curing to emergency utility repair. Using hydronic surface heaters is a cost-effective way to prevent scheduling delays for construction projects and keeping jobs running smoothly even in extreme temperatures.
Hydronic surface heaters circulate a hot glycol/water heat transfer fluid through a flexible hose placed on the ground. Heat radiates through the wall of the hose to thaw frozen moisture in the soil. The process is much more efficient than traditional propane heaters placed inside an enclosure. Hydronic surface heaters are used to thaw ground for excavating, heat the ground prior to pouring concrete and to maintain the ideal concrete curing temperature in cold weather.
The process is relatively simple. Once a site is cleared of excessive snow and ice, hoses are placed over the thaw site area. Plastic sheeting is placed over the hoses which help contain the water vapor to improve thawing, prevent loss of heat, keep soil moist for better heat conduction and help keep the next layer of insulated blankets clean. Finally, insulated blankets are laid over the plastic to further prevent heat loss and direct heat laterally into the ground.
Hydronic surface heaters will thaw approximately 1 in. every two hours, but of course there are many factors to consider. It is not the actual soil that freezes but rather the moisture content within the soil that turns to ice and binds the soil. Gravel and sand hold less moisture compared to clay and silt. Therefore, it will take fewer BTUs and less time to thaw, or actually melt the ice, for gravel and sand than clay and silt.
Depending on the application, the spacing of the hoses will determine the amount of thaw time needed. For general excavation, the hose is laid out with runs typically spaced 18 to 24 in. apart. Frost islands form between the hoses and can be easily excavated. For accelerated thawing, hoses are spaced between 6 to 12 in. allowing for fast thawing without frost islands between hoses. The closer the hoses are placed, the more BTUs per square foot are applied and the faster the thaw is completed. Performance will vary based on the soil type, moisture content and the use of insulation blankets, which can help optimize performance by keeping heat from escaping.
When temperatures drop below 40 degrees F, additional measures have to be taken to properly cure concrete. The colder temperatures will slow the cure rate, not allowing the concrete to gain strength in a desired time period. Hydronic heaters can be used to help cure footings, slabs, walls and elevated decks and are commonly used on bridge decks. Once the area has been thawed and excavated, as previously described, the concrete can be poured. Following the pour, the same system utilized for the thaw can now be used to promote faster curing. Plastic sheeting is placed over the freshly finished concrete, followed by the hydronic hose, spaced at 24 in. and then topped by insulated blankets. The hydronic heater will allow the optimal temperature range of 65 to 75 degrees F to be maintained during the concrete curing period.
Hydronic surface heaters circulate a hot glycol/water heat transfer fluid through a flexible hose placed on the ground.
Heating Inside Structures
Indirect fired air heat creates an ideal environment that allows contractors to work year-round and extend the work season, even in harsh and cold weather conditions. Whether it’s residential or commercial building construction, utility, maintenance or special events, indirect fired air heat provides a consistent and safer heat source.
Direct fired heaters, like torpedo heaters, introduce moisture and carbon monoxide into the air stream. Ventilating the area to remove these emissions reduces the overall efficiency. For improved safety and reduced moisture, indirect fired heaters are an excellent choice for eliminating water vapor, which can cause work delays within the structure. The system also keeps mold and bacteria growth in check. The flame on an indirect fired heater is contained inside a combustion chamber, providing safer, clean and dry heat. A flue for venting emissions away from the work area is included so carbon monoxide and dioxide, nitrogen oxide and moisture do not become problems.
Indirect fired heaters act more like the furnace in your home with a burner, heat exchanger and exhaust that is vented away from the jobsite. The flame that is created by the burner is captured in the heat exchanger, and the heat is distributed and moved with the use of a blower. The combustion by-products are vented outside and away from the workspace. Large units pressurize the inside space quickly, efficiently and evenly throughout the structure. They recirculate the air from inside the space through the heater and, when combined with thermostat controls, can help reduce fuel consumption by up to 50 percent compared to other heating methods.
Indirect fired heaters are sized and classified by the BTUs per hour. Generally, 1 to 3 BTUs are required per cubic foot per hour, depending on the structure’s R value. For example, a Wacker Neuson HI1000 is designed for heat output of 890,000 BTU/hour at an efficiency of 83 percent. Indirect heaters can be configured to operate on natural gas, LP or diesel fuel. Trailer-mounted diesel heaters with an on-board generator provide a self-contained system perfect for remote locations or to supply emergency heat if power is not available.
Benefits of Indirect Fired Heaters:
• Save on fuel due to efficient operation.
• Save time on finishing operations by eliminating moisture in the space.
• Improved quality of finishing to dry walls and other moisture sensitive materials by eliminating potential mold growth.
• Healthier and safer conditions by venting fumes out of the area and eliminating hazardous open flames.
Dave Peters is a product application and training specialist for Wacker Neuson.