Compact Compaction: Let’s Learn About Vibratory Plate Compactor Attachments for Mini Excavators
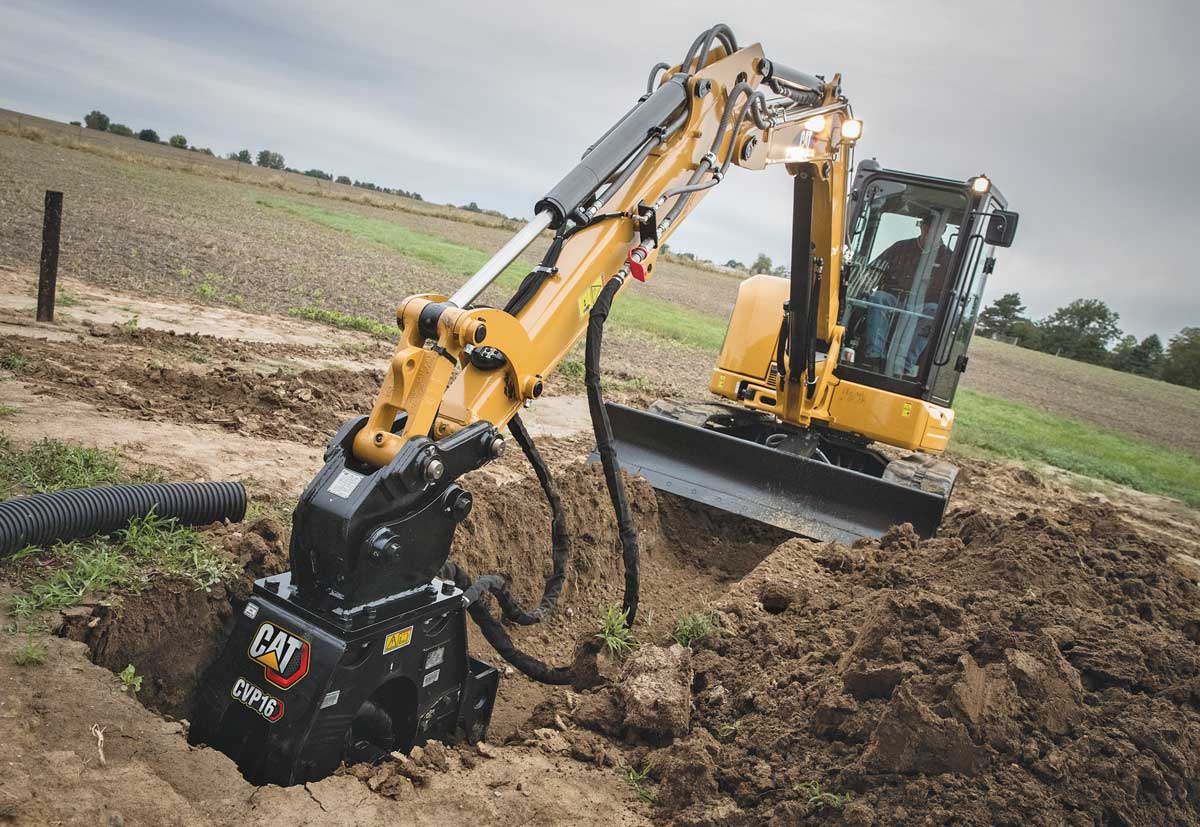
Proper soil compaction is critical for certain construction applications. A pro has a lot of options. Upright rammers. Reversible plate compactors. Forward plate compactors. Those cool trench rollers, some of which are remote controlled. All of those are solid options, but have you ever considered a compaction plate attachment on a compact excavator? It’s great for trench or hill compaction. It’s definitely safer than being in a trench and offers good visibility from above with a nice long reach.
“The vibratory plate compactor is a great alternative to remote controlled or walk-behind compaction equipment,” explains Kristin Stout, senior sales support specialist at Caterpillar. “The machine-operated compactor offers a safer work environment, eliminating the need for the operator to be in or near a trench to complete any work. The plate compactors also allow higher compaction in a shorter work time, increasing productivity.”
Mini excavator plate compactor attachments are designed to effectively compact soil in trenching, ground leveling and embankment construction apps. Good examples are pipeline backfills and road or railway slopes. They’re also good for driving in and pulling out product and tools — posts, sheet piling and other formworks. Mini excavator plate compactors are ideal machines for applications where the task is to compact soil on slopes or in confined places where self-moving plates or rollers cannot operate.
A compact excavator hydraulic plate compactor consists of four main components. The bottom plate is made of wear-resistant steel, with what’s called an “eccentric element” bolted onto it, giving it its vibration force. The eccentric element is rotated by a hydraulic motor that requires pressure and return lines from the carrier and sometimes a case drain line from the motor to the tank, depending on the hydraulic system of the carrier. This vibrating lower part is mounted on a top frame with rubber pad isolators. On top of the frame can be a hydraulic rotation motor or free rotating plate where the adapter plate is mounted, or sometimes it is bolted directly to the frame. Once installed, these units are powerful tools.
“Excavator-mounted plate compactors typically feature higher dynamic force output than handhelds,” adds Rob Reister, product specialist, attachments, Doosan Bobcat North America. “Another advantage they have is being able to compact trench backfill material from outside the trench and compact side slopes from a machine versus using handheld compaction equipment on the slope itself. Excavators are able to be utilized for more than the one task of digging a trench.”
Adding to the numerous safety advantages these attachments offer, Reister says, is the fact that noise and vibration are minimized while operating a vibratory attachment from inside the cab of an excavator — as opposed to outside with a walk-behind or handheld unit. Additionally, when operating from the cab, the operator is safely away from where the compaction is taking place.
Easy Maintenance, High Efficiency
Plate compactors work on the same principles as larger drum rollers, according to Reister. As with those machines, plate compactors produce centrifugal force and frequency, which work together to develop compaction force and transfer it into the soil being worked.
“Centrifugal force is what gives plate compactors power,” Reister adds. “Weights in the eccentric weight housing of the plate compactor rotate to produce the force being transferred through the plate to the material being compacted.”
Frequency refers to the rotation speed of the plate compactor’s eccentric weight, which is measured in vibrations per minute (vpm). “The lower the frequency, the better for compacting medium to thick layers of materials,” Reister says. “While the higher frequency models work better at compacting thin layers.”
Compactors for smaller excavators come in a variety of sizes and are often categorized by vpm, impulse force, weight, auxiliary hydraulic power or carrier size. Caterpillar offers two models of vibratory plate compactors for use with mini hydraulic excavators. The CVP16 features 3,650 lbs (16.2 kN) of impulse force and is designed for use on 2.5- to 6-metric-ton mini hydraulic excavators. It has a base plate length of 24 in. and unit weight of 476 lbs. The recommended hydraulic oil flow rate is 10 to 12 gpm.
Cat’s CVP40 model has 8,928 lbs (40 kN) of impulse force and both models can be used with pin grabber couplers, dedicated hydraulic couplers or pin lock couplers, providing quick and easy exchange of tools. The CVP40 is best suited for the 7- to 10-metric-ton family of Cat mini hydraulic excavators, with a base plate length of 38 in. and an 886-lb unit weight, utilizing 18 to 22 gpm of aux. flow. It also has a recommended hydraulic system pressure from 1,800 to 2,200 psi.
Both models are performance-matched to Cat machines and integrate closely with the Cat hammer line, allowing interchangeable brackets and hydraulic kits. Both models also feature an optional bolt-on blade that can be attached, allowing the operator to level backfill as they are working the compactor. Both plate compactors utilize a single auxiliary hydraulic system, which allows for ease of use without special hydraulics required on the machine.
A plate compactor attachment should be selected according to the carrier size and typical flow capacity of the auxiliary circuit. Contractors should consider the multiple ways this attachment will be used in compaction and extraction. Many compactors need to be modified prior to use for extraction or the isolators will be stretched and destroyed. Some compactors offer an axle bolt that should be installed when using the compactor for extraction. These axle bolts will prevent the isolators from getting damaged. Installation will vary. Some compactor attachments can get up and running quickly with no special installation required on the excavator. Standard adapter plates and attachment brackets can simplify attachment to the compactor.
Like a breaker, maintenance will be important for plate compactors because of their high impact job. Oil is critical. Stout says maintenance on Cat plate compactor attachments is relatively straight-forward thanks to the unit’s oil plug, which it located on the unit’s rear center line.
“This arrangement means oil can be changed with the compactor installed, which Cat recommends doing every six months,” she says. “Other daily maintenance checks include inspecting the unit for any leaks as well as ensuring the rubber isolators show no signs of cracking.”
Before getting to work with a plate compactor, Reister says it is important to inspect the compactor for loose or missing fasteners and check the shock mounts for rips or tears. Rotate the shock mounts 180 degrees if cracks occur at the top outer crease of the shock mount. Additionally, he says, make sure the carrier machine is approved for the attachment and rated for the pressure and flow rating of the attachment before putting it into service. “For longer-term maintenance, we recommend lubricating the bearings after every 40 hours of use,” he adds.According to Reister, Bobcat offers two vibratory plate compactor attachments. The PCF34 sports 3,400 lbs of dynamic force and features 488 in. (squared) of compactor plate surface area. The PCF64 model offers 6,400 lbs of dynamic force and features 804 in. (squared) of compactor plate surface area. Bobcat plate compactors have auxiliary hydraulic flow requirements from 12 to 28 gpm, with optimal flow being around 13 gpm. Typical operating pressure for these attachments is around 2,000 psi with relief set between 2,500 to 3,500 psi.
Also Consider…
A tiltrotator coupler will allow a plate compactor to spin 360 degrees to compact at different angles. A compact excavator’s backfill blades can make the attachment even easier to use. These blades assist with pulling material back into the trench or area that will need to be compacted. They can also be used to level off the path so that work can progress smoothly and protect against any material being thrown up. An integrated flow rate and pressure control valve can help ensure safety because it prevents hydraulic overloading of the compactor. This is an added bonus when it comes to safety and saving time, especially when using the compactor with different carrier machines. Finally, consider larger mini excavator models with offset housings that better distribute force across the plate, which means less stress and wear on the attachment during operation.
Some helpful tips for plate compactor operation include keeping the plate flat and in full contact with the material to obtain uniform compaction, Stout says, adding that operators need to apply appropriate down force on the attachment — several shorter lifts will give higher compaction than thicker lifts.
Water and air are pressed out of the material to be compacted during the compaction action. The degree to which a material can be compacted mainly depends on the following characteristics: form and size; water content; and depth of the layer to be compacted (the compaction result can be increased if the layer height is less). Place the hydraulic compactor on the ground. Make sure that the entire tamper plate makes contact with the ground. Switch on the hydraulic compactor. Exert slight pressure on the hydraulic compactor and move it slowly along a straight line. The ground/soil is compacted by the frequency of the tamper plate. Exerting excessive pressure with the carrier does not improve the working result. Switch off the hydraulic compactor, lift it and put it back on the ground elsewhere to compact the next section.
“The soil moisture content can also impact the quality of work while operating the plate compactor,” Stout adds. “Very dry dirt does not compact well, so it is critical to add moisture for good compaction.”
Just remember: Operators should follow all of the instructions in the safety and operation manual for their specific manufacturer’s compactor.
Jack Roberts is a freelance writer for Compact Equipment.